We do a lot of controls upgrades including panels with a lot of old mechanical relays. Our first response is to simply replace them all via PLCs. Some of the non-variable functions, though, are ideal for relays, and many of the installations are in high-EMI areas where relays do better than PLCs. Customer reaction is mixed. Some want every possible relay eliminated. Others who have had them a long time don't see the need to ban them entirely. Anyone dealt with something similar?
—From June '11 Control Design
Answers
A Balanced Response
A control system design is a balance between costs and reliability. Application considerations include: How many I/O points are there? What are the voltage and current requirements for the devices being controlled or supplying input (field I/O)? How reactive are the field devices (inductive/capacitive properties)? How often are the field I/Os changing state? Is maintenance a concern?
For a cost-effective PLC design, high-density digital I/O is desirable to achieve the smallest rack size and the best price per point. Digital I/O is normally low-voltage dc, for example 24 V, and current outputs are typically 500 mA. For those I/Os that do not fit the requirement of the voltage/current specifications for the high-density I/O PLC card, then you can add separate PLC cards to fit those specifications, or a relay can be used by the high-density I/O to either convert the voltage or to amplify the current.
For a reliable system, the designer must understand the properties of the field I/O. Both PLCs and electromechanical relays are concerned with reactive loads in regards to the reliability of the system. A highly inductive field device such as a 24 Vdc solenoid can produce a high-voltage spike that can damage the PLC output or weld the contacts of an electromechanical relay. A common design choice is to use relays in between the PLC and the reactive field device for isolation (interposing relays). This is a way to protect the more expensive PLC card and sacrifice the low-cost plug-in relay over time. Another example of a reliability concern would be field devices that have to change state very quickly and very often. An electromechanical relay has moving internal components, so it can cycle only so fast and will cycle only so many times. A solid-state device such as a PLC digital output has no moving parts and can theoretically cycle an infinite number of times at a very high frequency.
Maintaining the system is always a concern. A PLC has better diagnostics, and when the problem is found, the failed I/O card can be replaced. Relays have no intelligence, so troubleshooting can become an issue depending on the complexity of the relay scheme. If troubleshooting the wired logic is not an issue, then there is no debate on the cost of a PLC card vs. the cost of a plug-in relay.
The bottom line is that there could be a good reason to use electromechanical relays in an old design. It's also quite possible that a PLC upgrade makes perfect sense. Quite often, the combination of a PLC and electromechanical relay system results in the most reliable and cost-effective design possible.
Mike Garrick, product marketing manager—power solutions,
Phoenix Contact, www.phoenixcontact.com
Not Too Shabby
This question brings up refreshing ideas. We're probably the world's largest manufacturer of solid-state relays, so it's sometimes easy to forget that there might be some applications out there for which a mechanical relay might be better. In the scenario described, leaving banks of relays in place and just changing out the control hardware might not be such a bad idea.
A mechanical relay doesn't care whether it switches ac or dc, whereas with SSRs, it might be necessary to change the relay if the nature of the signal changes. Also, SSRs have both a minimum and a maximum amount of current they can switch. Too little, and there is not enough power to switch on the SSR, and too much can destroy the SSR by creating too much heat. None of this negates the many advantages of the solid-state relay, but I wanted to illustrate how it might not always be a no-brainer when deciding to replace mechanical relays.
The most interesting twist comes when you swap out all the old logic with a PAC, then use the PAC's high-density digital I/O (low-power capability) while leaving the existing mechanicals in place for their higher current-carrying capability. Other advantages of trying it this way would be the added communications abilities and the state-of the-art logic that comes built-in with the PAC. Plus, there are the savings of not having to replace and rewire the existing system.
Tom Edwards, Senior Technical Advisor,
Opto 22, www.opto22.com
Strengths and Weaknesses
In most control systems, PLCs and relays are not mutually exclusive. They both have their strengths and weaknesses, depending on the level and types of functions needed in each control system.
Relays are traditionally easy-to-install, economical solutions for simple logic and standard control functions. In these types of applications, relays provide cost savings because of their relative low price and ease of installation and setup compared to PLCs. Wiring a relay for simple, non-variable logic functions is a standard job for an electrical technician, whereas PLCs often require specific programming skills that add cost and time for installation and commissioning. This situation is reversed, however, when logic functions vary, such as in a flexible production environment where the PLC could have different schemes or processes stored in memory and can be implemented instantly by an operator.
While mechanical relays can be sensitive to pickup of EMI on both the control voltage and the output, solid-state relays using opto or pulse transformer technologies provide excellent solutions for high-EMI applications through the use of integral protection on their control and the output circuits. In fact, PLCs in many control systems depend on relays for isolation and protection against EMI on their inputs and outputs, especially in applications where inductive loads are driven. In these cases, solid-state relays can protect the PLC from high-voltage transient feedback when switching off the load.
Finally, solid-state relays also can be used for signal conditioning. PLCs typically need 24 Vdc status inputs, but machinery and equipment often use lower or higher voltages for signaling and control. In these cases, relays are used to convert voltages at the input side of the PLC.
Susanne M. Walker, Product Manager—Advanced Connectivity
Weidmuller North America, www.weidmuller.com
Easily Overcome Drawbacks
The three largest drawbacks to a traditional relay logic system are reliability, flexibility and diagnostics. However, control panels can be updated to overcome these issues without abandoning relays for PLCs.
Reliability is the simplest issue to address. Just replacing the original relays with more modern, compact versions will increase the lifetime of the panel. If there is a desire to take this even further, electromechanical relays can be replaced with solid-state versions. Although the cost is higher, solid-state relays ensure that the panel will not suffer from mechanical relay failures.
Flexibility is probably the strongest argument for PLCs. However, making the correct product selection can allow for future flexibility. Product features that allow for changes to the function of the panel without changes to the product and wiring include standardized sockets that can accept different relay/timer types, wide input voltage ranges, multiple poles for future expansion, and multi-function, multi-range timing relays.
Also, making these changes requires nothing more than a screwdriver, while changes to a PLC require a PC and programmer.
Finally, diagnostics can be achieved by the features available on the relay. Often available as standard, LEDs allow the user to see the electrical status of the coil of the relay. In addition, a mechanical flag will indicate the status of the contacts. These two pieces of information on each relay quickly can help identify the cause of an issue in the panel. This also can be done simply by looking inside the panel, instead of looking into the code.
Although PLC applications and the market for them will continue to grow, there will always be situations in which it is more cost-effective, simple or efficient to use relays.
Jacob Feutz, Product Manager,
Eaton, www.eaton.com
Understand the App
This is a fairly common challenge when updating existing industrial control panels. Understanding the final installation and application of the panel is most critical to provide clear insight into what product should be selected. By taking a customer-first approach, and understanding who they are and what they need, it becomes easier to demonstrate the features and benefits of programmable devices and electromechanical relays when compared to each other.
PLCs can provide great benefits over electromechanical relay logic; however, they can also be significantly more complex than needed when replacing electromechanical relays. A good solution could be a programmable relay or a micro PLC because these devices can provide the programmable functionality with built-in functions (e.g. timers, time switches, counters, etc.) that eliminate the electromechanical relay logic. They typically are programmed with ladder logic, which is easy to learn and visualize, giving the interactive feel that is found with electromechanical relays. Programmable relays and micro PLCs are cost-effective, allowing customers to get exactly what they need at a price they are willing to pay.
Electromagnetic compatibility (EMC) is critical where electromagnetic interference (EMI) is present. However, many PLCs and programmable relays are tested per EMC standards and have some level of compatibility. It is important to know the application when identifying EMC requirements.
Both programmable devices and electromechanical relays have features and benefits that allow the products to thrive in a given application. Understanding that application and the customer's needs allow for proper selection of products and implementation of the proposed upgrade.
Peter Damesimo, Manager, Engineering and Quality,
c3controls, www.c3controls.com
Mixed Message
Control panel upgrades often result in a mix of PLCs and relays depending on the application. PLCs are a good solution where electrical loads are small—typically 2 A or less. Examples include relay coils, small contactors, tower lights and annunciators. Larger loads typically require relays with a switching capacity rating of 5 A or more. Examples include solenoid valves or devices with small motors such as valve positioners, or linear actuators characterized as inductive loads with surge, peak or inrush current.
Another consideration for using PLCs or relays is ease of replacement at end of life or in the event of an unforeseen maintenance issue. General-purpose relays offer the convenience of plug-in replacement compared with a PLC that might need an entire output module replaced.
Randy Pohl, Project Manager, P.E., PMP
Rockwell Automation, www.rockwellautomation.com
Arguments for PLCs
There are four key areas that favor choosing PLCs over relay panels for a modern control system.
The cost of PLCs has come way down over the past 20 years, while the cost of relays has gone up. In terms of hardware alone, a 10-relay circuit could easily cost $400 for relays and sockets today, while a PLC capable of the same basic functionality is often less than $400. The costs for installation, hardwiring all the relay connections and verification of correct wiring is substantially higher than a comparable PLC-based control system due to more hours of licensed electrician labor.
Traditional relays are capable of simple Boolean logic control, but lack the capacity for simple diagnostics (other than LED indicators on the relays) and are generally dedicated to a very limited-scope task. To obtain counting capability, a separate counter is needed; for timing capability, a separate timing relay is needed. PLCs offer built-in diagnostic capabilities, counting, timing and general programming flexibility for use in changing applications. PLCs make it easy to add simple HMI workstations to display errors, counts and other pertinent information.
Before maintenance departments had access to laptops with software, anything programmable was typically serviced by the "engineering department," often delaying recovery from a fault and increasing the labor cost. Today, laptops are standard tools for maintenance personnel, making PLCs a much more mainstream choice for a control system. With built-in diagnostic tools, the PLC quickly identifies the location of a fault to shorten downtime. When it comes to documenting program or component changes, relay panel systems require modification of schematics and bills of material. Using a PLC, documenting program changes and their ladder logic connections can be printed out in a fraction of the time.
For example, in the automotive industry, which was the driving force behind the creation of the PLC, production lines typically are retooled every one to three years. This required rewiring relay logic, adding relays, removing others, etc. With the advent of PLCs, the automotive industry was able to dramatically reduce the model changeover time, keep track of additional parameters and data for the automobiles, and generally produce a higher-quality product at a reduced automation cost.
Relay panel control systems make it challenging to share production data with upstream and downstream machines. Production floor data (regardless of the end product) and the ability to collect data, analyze data and, ultimately, supply a report is only capable via connectivity of the control device or control system, and usually requires a PLC exchanging data with a host computer. Connectivity to SCADA software makes all this possible and supports changes in manufacturing and associated, critical data. Even in the event of system failure, the ability to take a snapshot of the system to determine fault is most critical to a wide range of automation applications. With increased connectivity, the ability to share/use system data becomes possible, even remotely.
Rich Gamboa, Vertical Market Manager
Security and Detention/Water Wastewater,
Omron Industrial Automation, www.omron.com
Solid Maintenance
Besides the obvious cost implications (both hardware and installation), what shouldn't be overlooked are the maintenance advantages offered by solid-state electronics. Not only will solid state allow for greater reliability, but automated diagnostics, which can be accessed through open networks (such as EtherNet/IP) means faster up time when a failure does occur.
Robb Dussault, Offer Marketing Manager, Industry Business
Schneider Electric, www.schneider-electric.com
ALSO READ: Mini-PLCs—more than just a smart relay
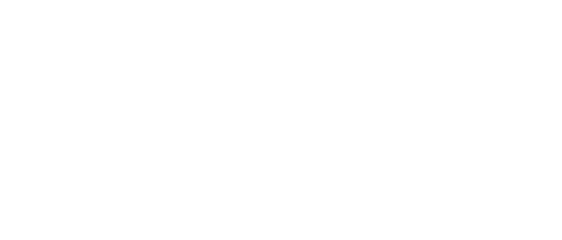
Leaders relevant to this article: