Our machines use a variety of proximity switches to detect presence or absence. These switches have been hardwired to local I/O at our central PLC. We think it might be time to upgrade and move to switches connected to our PLC via a digital network to cut wiring costs and add diagnostics. Our concerns are the complexity of adding a network and, most importantly, real-time performance because we'll be depending on the network for speed of execution and ultimately the safety of our machine. What's been the experience of others in a similar situation to ours—machine builders that have made the upgrade from hardwired to networked proximity switches? Is this a good case for the IO-Link you wrote about?
—From May '11 Control Design
Answers
Make It Simple
The concept of moving your I/O terminal points from the PLC into the field on a digital network can provide many benefits, including lower material cost, enhanced troubleshooting, shorter commissioning time and overall cleaner machine aesthetics. Integrating a bus network between your PLC and discrete I/O can be as simple or as complex as you want.
Networks such as Profibus, DeviceNet and their Ethernet-based counterparts Profinet and EtherNet/IP are quite powerful, and provide many options for device connection in the field, including motor and motion controls. For integrating basic sensors and actuators, such as proximity, photoelectric, solenoids, etc., a simpler network such as AS-Interface could be a great first start.
"Your control panel will slim down without all the terminal points, replaced with one or two bus and power cables running to the field. Your field network will be composed of I/O blocks."
All of these networks and protocols have gateways (backplane cards) that connect to the popular PLCs on the market. These interfaces will look like large I/O cards in your PLC program configuration, and allow you to maintain your current programming software. Therefore, your only learning curve is the hardware and configuration of the bus network. Most of the manufacturers have short, quick-start guides to help ease setup.
Your control panel will slim down without all the terminal points, replaced with one or two bus and power cables running to the field. Your field network will be composed of I/O blocks. These blocks come in a variety of flavors: terminals for cabinets, quick disconnects for easy plug-n-play, IP67-IP69K rated for harsh environments, and so on. Since you can mix and match these on your network, your designs become more flexible.
Once up and running, your PLC program will have full access to your network status, allowing remote troubleshooting down to the I/O block. I/O-Link is a protocol that rides on the back of these bus networks and provides even greater diagnostic capability.
Although specific benefits and ROI depend on the machine function and layout, applications from material handling to parts assembly to bottling have all found great returns in implementing a digital bus network.
Andrew Waugh, Product Engineer,
AutomationDirect, www.automationdirect.com
Distributed I/O Benefits
IO-Link will be most prevalent in sensor devices with analog outputs. At this time, IO-Link is generally not available in discrete position.
Network speed is affected by the length of cable runs and sometimes the number of devices on the network. Using a distributed I/O solution limits the number of nodes and allows the user to maximize the number of inputs per node. A distributed I/O solution gives users more flexibility in selecting a network that better meets their overall needs, and provides the type of diagnostic data they require.
Tony Udelhoven, Director, Sensors Division,
Turck, www.turck.us
Keep It Real
As a manufacturer of I/O devices, I can say that this application is better addressed using a real networking solution instead of an intelligent point-to-point approach.
Going from a hardwired installation to such a network certainly involves learning new things. How much of a learning curve depends on the selected solution. At the sensor level, there is only one real solution (called AS-Interface) that is easy and fast to implement, deterministic, offers millisecond-range update times, and is priced attractively.
AS-Interface is supported by all major PLC manufacturers and—when preferred—directly ties into the most frequently used higher-level networks, including EtherNet/IP. I/O blocks for enclosure and field (up to IP68/69K) are available from a number of providers.
"Going from a hardwired installation to such a network certainly involves learning new things. How much of a learning curve depends on the selected solution."
Although safety was not directly mentioned, it is important to know that AS-Interface is also certified for safety application (Category 4, SIL 3, PLe) without the cost involved in using a safety-rated PLC. The attainable wiring simplification can be as high as a 90% reduction in cable, termination points and labels. Speaking for our company, we have always offered live and/or web-based training sessions to help first-time users get going quickly.
Helge Hornis, manager, Intelligent Systems Group,
Pepperl+Fuchs, www.pepperl-fuchs.us
Reduce Your Wiring
End users have numerous options and flexibilities to reconfigure their machines for cost-saving measures. We offer remote I/O capabilities in both Profibus and Profinet networks. We can migrate the local I/Os to a remote I/O network with benefits to customers from reduced wiring cost and the same reporting and diagnostic capabilities as local I/O.
"We understand your concern with the increased complexity by adding a network, but you can look at adding a network as a way to simplify the machine's overall design."
We understand your concern with the increased complexity by adding a network, but you can look at adding a network as a way to simplify the machine's overall design. Imagine the difficulties facing machine builders to expand their machine designs without adding a network to allow distributed/remote I/O for adding field devices and safety devices such as emergency stops and light curtains. Statistically, there have been more than 35 million Profibus and more than 3 million Profinet nodes installed.
Real-time performance is even more critical for safety network applications to detect, evaluate and respond when a safety event such as the emergency stop is pushed to prevent injuries. Network safety with Profisafe has more than 1 million nodes installed, making Profisafe the unchallenged leader in network safety. Those numbers are from Profibus Trade Organization, www.profibus.com/press/newsletter/profinews-2011/profinews-79. From the statistics provided, they are a clear indication that machine builders like you have made the upgrade from hardwired to networked for both I/O and safety needs.
Kevin Wu, Product Manager for Distributed I/O,
Siemens Industry, www.industry.siemens.com
Use SERCOS
Generally, when it comes to standard PLCs, input/output capability is when PLCs have some means of receiving and interpreting signals from external objects such as switches, sensors, encoders, etc. Some PLCs have a fixed number of I/Os built into the unit; others use individual circuit boards or interface card modules to provide customized I/O capability. In addition to onboard I/O, some PLCs have the ability to connect to remote I/O modules or blocks through I/O networks to increase the number of I/O channels beyond the capacity of the base unit and to decrease wiring to the central PLC.
"Many different digital network standards exist for PLCs to communicate with, from PLC to PLC, and between PLCs and field devices."
Many different digital network standards exist for PLCs to communicate with, from PLC to PLC, and between PLCs and field devices. To achieve true, hard-real-time characteristics, SERCOS III, like SERCOS I and II, uses a form of synchronization that depends on a synchronization mark issued by the master control at exact equidistant time intervals. All nodes in a SERCOS network use this telegram to synchronize all activities in the node. To account for variations in network components, delays are measured in the node-to-node transmissions during initialization of a SERCOS network, and those values are compensated for during normal operation.
The integration of peripheral I/O devices into SERCOS III networks has become even more simplified. It also minimized the interface costs with the feature of being able to support centralized and decentralized control architectures. Rexroth block I/O (both analog and digital) enables the connection of sensors and actuators to the higher-level control system through the uniform SERCOS network. This greatly reduces development, installation and commissioning time, making it possible to implement a consistent, capable, and cost-effective overall automation system.
Abdulilah Alzayyat,
Drives, Motors and HMIs
Bosch Rexroth, www.boschrexroth.com
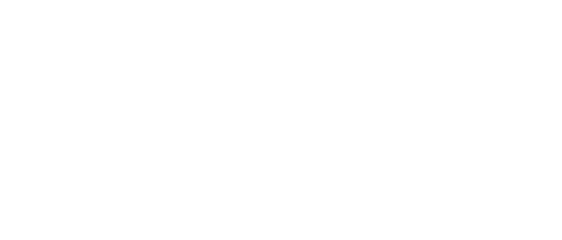
Leaders relevant to this article: