As in real estate, it's all about location, location, location when it comes to basic specifications for industrial PCs. Other important requirement drivers involve things that all automation solutions have to deal with: failure and the future. A final set of basic PC selection criteria arises because computers are general-purpose tools that interact with other machines and people.
With regard to location, one of the most important factors to consider when choosing a PC for a factory floor is the factory floor itself. Is it a non-hazardous area? Or is it a Class I, Division 2 area where there's a risk of a fire or explosion in abnormal conditions? The answers impact PC choices profoundly.
SEE ALSO: Survivor: IPC
"Once you start going into a hazardous area, the list of all the wonderful options that everybody makes gets narrowed down very quickly," says Louis Szabo, business development manager at Pepperl+Fuchs North America.
He adds that what's important is the certification for both front and back of a PC. The front might be rated Class I, Div 2. This means it has been judged to be safe when hazardous gases could be present but normally are not. If the rear hasn't been rated as meeting this standard, then some sort of enclosure purge will be needed to keep the concentration of flammable or explosive vapors at an acceptable level. Putting in a purge system could limit location and drive up costs of the total solution compared to a non-purged system, Szabo says.
He adds that there are no industrial PCs rated for Class I, Div 1, which covers locations where flammable gases routinely exist in ignitable concentrations. There are touchscreens that are certified safe in such conditions, however.
The other aspect of location is the overall environment. A factory floormight be hot, cold, dusty, prone to vibration, occasionally drenched in water, or all of the above. An industrial PC might have to operate in these conditions, which means it should have the necessary NEMA or IP ratings to keep out moisture or dust.
In general, the best system has the fewest moving parts because they increase system reliability and uptime. Thus, a fanless PC is preferred. A rule of thumb, Szabo says, is that the failure of its cooling fan leads to overall PC failure within 20 minutes or so.
The second general category of specs arises because failure of an industrial PC can be expensive. It's not the components or the labor needed for troubleshooting and installation that is a big ticket item, though. Instead, it's the downtime, with lost revenue possibly running into millions of dollars an hour.
For that reason, systems should have easily replaceable power supplies, hard drives, motherboards, screens, firmware and other parts. The resulting ease of maintenance minimizes downtime, and the modular approach helps to future-proof the system against technology advances — if the right approach is taken initially.
"When you're looking for that industrial computer, you want to think ahead," says Connie Chick, product manager for control systems at GE Intelligent Platforms. "I need it right now for this purpose, but in looking around, what else can it be used for?"
A hidden assumption in both maintenance and modernization strategies is that replacement and upgrade components can be obtained now and will be available in the future. For a standard office PC, that is a dicey proposition once a few years have passed. Clearly, one basic spec for an industrial PC should be a design that eliminates such issues and an accompanying vendor commitment to ensure a supply of parts.
You have to consider what a system might be called on to do in four or five years, says Eric Reichert, product marketing specialist for industrial PCs and HMIs at Phoenix Contact USA. Systems might start out handling just the control function, but graduate to more complex tasks such as advanced visualization of data.
This reality is reflected in a basic system requirement. "People want a lot of options when it comes to processors. They want myriad choices," Reichert says.
Multicore systems are good examples of that. Such setups can run a deterministic, real-time control system on one core, while another handles advanced visualization, interfaces with the network, interacts with operators, or does some combination of these tasks. The advantage is that the all-important control function can continue even if the operating system running on another core freezes up.
However, setting up this type of arrangement after installation demands that the system have the appropriate processor and storage, or that these be modular and upgradable to the necessary level. If not, then the system might not have enough computing power to handle demanding tasks or new software. Consequently, another basic requirement is that enough computing resources be present or be installable in an industrial PC for the full range of possible applications.
Along with a capable processor, it's important the system have the right amount and type of memory. It should have a display of the appropriate resolution. Today, displays increasingly have a 16:9 aspect ratio and more offer multi-touch input. The ongoing shift from a 4:3 aspect ratio display and single touch is an example of why future proofing is so important in industrial PCs.
A technology advance such as segmenting functions into different cores is relatively new. It has blurred distinctions, and made the performance of an industrial PC comparable to that of a PLC. But, says Sidney McLaurin, PC-based automation product marketing manager at Siemens Industry, a PLC generally can't readily handle visualization or other advanced tasks. It's also generally not as open as a PC.
Finally, just as no man is an island, no industrial PC is totally isolated. There are network connections to the factory floor, which means that one of the basic specifications is that the system either have the necessary communication protocols built in or that it accept a plug-in card with those protocols. At a minimum, an industrial PC should offer Ethernet connectivity, but even here care must be taken. Ethernet undergoes periodic transitions to a higher data rate, so systems must provide this capability or permit a field upgrade to a faster link.
These types of requirements could push end users away from a less-expensive option toward a more costly one. In the end, though, spending more up front could save a tremendous amount of money and headaches later.
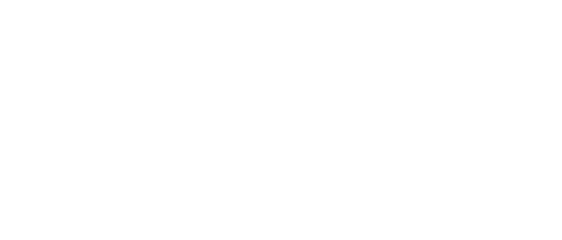
Leaders relevant to this article: