Ian Verhappen is an ISA Fellow, Certified Automation Professional and a recognized authority on industrial communications technologies with 25+ years' experience. You can contact him at [email protected], via his blog at community.controlglobal.com/kanduski, or check out his Google+ profile.
Though a great deal of the conversation on industrial networking of late has been on wireless technologies, copper and fiber are still the workhorses of industrial networks, especially with the rapid growth in deployment of Ethernet-based digital networks.
Because of the high bandwidth of 100 MB/s associated with Ethernet, it's susceptible to noise and, therefore, typically limited to the distances for which Cat 5e or Cat 6 cable can be used. This is in addition to the 100-m limit between nodes for Ethernet in general. Since copper communications systems let many devices share the same cable and communicate with each other, while fiber signal transmissions and reception are point-to-point, there will continue to be a need to mix systems for many years to come. Fiber typically can be installed 2 km to 20 km between nodes and is, therefore, well-suited to connect the various automation nodes throughout a facility — part of the reason for its increasing use in industrial settings.
SEE ALSO: Fiberoptics Extend Ethernet's Empire
Therefore, it's time to have a look at just what to consider when using fiber in the industrial environment.
- EtherCAT's Roots in Fiber
- Fiber Optic Evaluation Tools
Fiber Is Good for the System
Fiberoptics, as the name implies, uses light rather than current or voltage for signalling. As such, the primary reasons to use fiberoptics, other than for the greater distances possible, are:
• Ground Isolation — Since electrical currents do not flow on fiberoptic cables, grounding systems are not needed
• Noise Immunity — Because fiberoptic cables are immune to electromagnetic noise from radio stations, motor turn-on surges, welding discharges, electrostatic discharges and other radio frequency interference (RFI), and since fiberoptic cables do not conduct electricity, they can be placed on the same cable trays as power-carrying cables.
In the accompanying sidebar, you'll find an example of how fiber networks are being used to advantage in an electrically noisy environment in alternative energy projects using EtherCAT technology.
Mind the Details
Although fiberoptic cable is not susceptible to RFI, that does not mean that fiberoptic data communications are error-free. Though the cable itself might not be conductive, an armoured sheath, if used, could be conductive, as will any metallic hardware used in the cabling systems, such as wall-mounted termination boxes, racks and patch panels, which all must be grounded. In addition, the electrical code requires that all premises cables shall be listed and have flammability ratings per NEC 770.50 (2002), now 770.113 (2005). "Listing, Marking and Installation of Optical Fiber Cables" requires all cables within a facility to be labelled with the following exceptions:
Exception 1: Optical fiber cables shall not be required to be listed and marked where the length of the cable within the building, measured from its point of entrance, does not exceed 15 m (50 ft), and the cable enters the building from the outside and is terminated in an enclosure.
Exception 2: Non-conductive optical fiber cables shall not be required to be listed and marked where the cable enters the building from the outside and is run in a raceway (which includes a conduit) installed in compliance with Chapter 3.
Color Codes and Splice Tips
The TIA 568 standard specifies color codes for the individual fiber connectors: orange, black or gray have been multimode, and yellow has been single-mode. However, the advent of metallic connectors, such as the FC and ST, made color-coding difficult, so colored boots were often used. The TIA 568 color code for connector bodies and/or boots is beige for multimode fiber; blue for single-mode fiber; and green for APC (angled) connectors. In addition, color codes for the individual fiber sheaths in a multimode fiber are specified by TIA/EIA 598-A.
TIA/EIA 568 also specifies splice performance of 0.3-dB loss for both multimode and single-mode splices as industry-acceptable limits, and single-mode fusion splices are typically under 0.1 dB. The splicing itself can be a fusion splice that "welds" the two fibers together, usually in an electric arc. Fusion splicers are generally automated to produce splices that have minimal losses. A note of caution for the industrial setting is that, since fusion splicing uses an electric arc, it should not be performed in a dusty or explosive atmosphere, as the electric arc could cause an explosion or fire. The second and more common field splice is a mechanical splice that aligns the two fibers in a ferrule or v-groove, and then uses an index-matching gel or adhesive between the fibers to reduce loss and back reflection.
Plastics in the Mix
Glass fibers are generally not field-serviceable, as they require special skills and tools. However, plastic cable can be cut with scissors and not fracture, and will continue to function if the alignment is "close." This makes it much more field-service-friendly. Manufacturers sell kits to finish plastic fiber, although plastic fiber lengths can be restricted to as little as 50 m if finished this way. Despite the limitations of plastic, Kurt Wadowick, safety and I/O specialist at Beckhoff Automation indicates that the company sells more plastic than glass fiber.
SEE ALSO: Shed Some Fiberoptic Light
Key Factors
A typical fiberoptic cable construction from the inside or core to the outside consists of the following layers: fiber(s), buffer tube, rip cord, strength member, steel armor and outer jacket. Let's look a little closer at the role each of these plays in a successful installation.
Multimode glass fiber typically has a 50-µm or 62.5-µm core with 125-µm cladding outside diameter, while plastic fiber is thicker at 200 µm or 230 µm for hard-clad silica (HCS) and plastic silica (PCS) and 1 mm for all-plastic fiber.
Attenuation in fiberoptic cable is the loss of optical power as the signal travels through the cable. In general, attenuation decreases as wavelength increases, but certain wavelengths are more easily absorbed in plastic and silica fibers than others. One of the reasons for establishing standard operating wavelengths of 850 nm, 1300 nm and 1550 nm in silica fiber and 650 nm for plastic is to avoid the high-attenuation regions. The typical attenuation of a 62.5-µm to 125-µm fiber at 850 nm is 4 dB/km, and the attenuation at 1300 nm is 1.5 dB/km. Plastic fiber is low-bandwidth, high-attenuation (19 dB/m), and due to these higher losses, best suited to short-run applications, such as those found in the manufacturing sector, where there is a high degree of repetitive motion.
When fiberoptic cable becomes kinked, several things can happen. Glass can fracture, resulting in splinter(s) that can't be repaired, while plastic will crinkle like a garden hose. In both cases, the fiber will cease to operate properly. However, the effect in a glass bundle is obviously more catastrophic, and that's why plastic fiber tends to be used in robotics and similar applications.
Because multimode is able to transmit to approximately 2 km, it is what is most commonly used for IT projects. It can therefore be sourced from the same suppliers, and often purchased with prefabricated ends, making it more easily available than single-mode or industrial fiber. As indicated earlier, single-mode fiber can handle 20-km distances before requiring amplification, and is typically installed with one fiber transmitting and the other receiving, so when purchasing a cable bundle, it's recommended to always install it in pairs or an even-numbered set of fibers.
Dispersion affects bandwidth by limiting how close together the individual light pulses are from each other to prevent overlapping. To minimize the chance of dispersion affecting communications, the signal rise-and-fall times generally must be no more than 20% of the width of the shortest period. The amount of time between pulses directly affects overall bandwidth.
Signal gain, expressed in dB, determines distance between light source and receiver. Both the passive and active components of the circuit have to be included in the loss-budget calculation. Passive loss is made up of fiber loss, connector loss and splice loss. Active component specifications of interest are system wavelength, transmitter power, receiver sensitivity and dynamic range — the difference between transmitter power and receiver sensitivity.
There are two types of buffers: tight and loose. A tight buffer is applied directly over the fiber. This protects the fiber, but introduces a potential problem if the temperature drops below freezing. At low temperatures, the buffer material shrinks more than the glass fiber, which puts stress on the fiber and causes the glass to develop "micro-bends" or spots where light escapes from the fiber, thus increasing the attenuation of the fiber.
Loose buffers do not protect the glass fiber as well as tight buffers, but they hold the glass strand in a tube filled with a compound to keep moisture from getting onto the fiber. Because they are loose at low temperatures, the buffer can shrink without the fiber developing micro-bends. As a result, loose-tube cable is primarily used for outside plant installations where low attenuation and high cable-pulling strength are required.
Stay Dry
Until recently, most installations chose a gel-filled cable, but now dry-water-blocked cables are widely available and preferred by many users. Dry-water cables use water-absorbing tape that expands and seals the cable if any water enters it. Installers prefer dry cable, as it does not require the messy, tedious removal of the gel used in many cables and greatly reduces cable preparation for splicing or termination.
The strength member in a cable is either fiberglass or aramid, and the cable should be pulled only by these strength members. Any other method can put stress on the fibers and harm them. Similarly, cables should not be pulled by the jacket unless specifically approved by the cable manufacturer and an approved cable grip is used. In addition, twisting the cable can also stress the fibers.
Remember when installing cable that the typical minimum bend radius for fiberoptic cable is 20 times the outside diameter of the jacketed cable for installation and 15 times this same diameter over the long term. Bearing in mind that installation of an outside plant (OSP) cable could cost 100 times the cost of the cable itself, the recommendation is that you do not bend your fiber to less than 20 times the outside radius of the jacketed cable.
As it is the fiber sheath that provides strain relief and strength for pull-through conduit, more sheath means more rigidity and, therefore, a requirement for increased bend radius. In addition, you should always pull cable down to avoid stress from the weight of cable on the fibers in the core.
Knowing the limitations of the physical layer will help you prepare a better design, and the references at the end of this article and in the sidebar offer sources for additional information about the network layout as well as the specification and execution of the project in the field.
Beckhoff Automation's Wadowick reinforced the importance of terminations, saying, "Technical support calls are almost always about fiber terminations, the connections and ends, or splicing."
Fiberoptics will continue to grow in the industrial setting. Fiberoptic cable is different than copper and requires special skills and tools to install. Terminations continue to play a critical role in the success of an installation. And, yes, the constant remains that the physical layer, which is the underpinning of any industrial network, continues be critical to the success of any project.
Reference: "Guide to Industrial Fiberoptics," from Relcom.
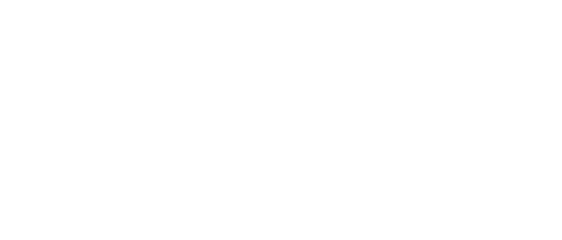
Leaders relevant to this article: