After working as a semiconductor process engineer, Hank Hogan hung up his cleanroom suit and now writes about process control and other technologies from Austin.
Getting from point A to B at the right time and in the right way is the essence of motion control. Sometimes it's easier to do this correctly under pressure. That's when pneumatics are used, with the movement of gas-powered cylinders forcing the needed motion. Those cylinders are often controlled by electronics, through the action of valves and with sensors providing feedback on position and pressure.
But before cylinders start pushing things around, there are some decisions to be made. The first is whether or not pneumatics should be used at all.
SEE ALSO: Is Pneumatics Still a Good Solution?
The alternatives include electromechanical motors and drives. These offer higher speeds than pneumatics. They also allow more complex — as in not simple linear — motion for lower energy costs, but do so at a higher component cost. A Bosch Rexroth study indicated that the total cost of ownership is lower for pneumatic than electromechanical solutions in applications with low to medium force requirements that undergo less than 1 million total cycles per year. Thomas Dwyer, senior automation engineer with Bosch Rexroth, adds that often the choice between pneumatic and electromechanical solutions might be dictated by the operating conditions, such as a contaminated, explosive, wet or corrosive environment. "For those four conditions, compressed air is an excellent medium," he says.
Another fundamental consideration is infrastructure, specifically the presence of a pressurized gas. Typically, this is compressed air. If a compressed gas is unavailable, then implementing a pneumatic solution would involve installing compressors, tubing and valves. The cost of this can swamp any savings achieved by this motion control method.
What's more, the compressed air has to be at a high enough pressure to do the job. Pressures might be only guaranteed to be 60 psi. That value is important, since the force generated scales directly with the pressure. Another pressure-related constraint involves the location of a valve in relation to the cylinder that will be doing the work.
"Air has a sponginess to it, so if your air line is really long, you lose precision because of the compressibility of air," says Don Harris, product marketing manager for Bimba Manufacturing.
He adds that tubing runs between control valves and cylinders should be less than 10 feet. If the distance is greater, then the ability to position a load as needed could be compromised.
Once the decision has been made to go with pneumatics, engineers should look at the mass to be moved, its velocity and acceleration. From that information, the necessary combination of actuators, cylinders and tubing can be calculated
"The determining factor, which way they want to go, starts with the work they're trying to do, such as the mass they're trying to move and how they're trying to move it," says Marchelle Forish, Bosch Rexroth's senior product specialist in pneumatics.
The next steps in the decision tree involve the components. Henry Menke, marketing manager for position, sensing and measurement at sensor maker Balluff, notes that any pneumatic solution has a prime mover, typically an air cylinder. Beyond that, there must be a controller that takes inputs and creates outputs such as the control signal for the valve that drives the cylinder that creates desired motion. The inputs are position and pressure, with the latter measured on both sides of the actuator.
Balluff uses magnetostrictive technology to capture position information. Menke notes that, in motion control, the repeatability of and resolution provided by a position sensor is critically important. Generally, for motion systems, more sensor resolution is better.
"Velocity is a mathematical derivative of position," Menke says. "So the coarser your position value is, the more unstable your mathematical derivative — velocity — becomes. You're really looking for more position resolution, so you can get resolution of your velocity."
Other important characteristics are sensor linearity and update rate, with a 1- to 2-ms update rate sufficient for most applications. Form factor, cost and interface with the control mechanism round out the list.
While often coming toward the end of the selection process, the form factor of pneumatics can be a deciding attribute, says Roger Altendorf, director of technical solutions at valve maker Enfield Technologies. It could be necessary, for instance, to fit a cylinder underneath a machine. In another case, pneumatics might need to move an inspection system across the entire span of a 10-ft conveyor. In the first situation, a guided rod cylinder could be appropriate, while in the second, a rodless approach might be best, as that eliminates the possibility of a 10-ft rod sticking out from the conveyor.
In all of this, valves are a vital component, with proportional air valves often used. Here precision is impacted by response time, as that determines how quickly motion can be stopped or started. Some valves from Enfield Technologies, Altendorf claims, react to commands in less than 2.5 ms. "That allows these highly precise applications to work," he adds.
Another component consideration is that the pressure drop of long pneumatic tubing runs leads to wasted energy, an increasingly important consideration. Sean O'Grady, product manager for valve terminals and electronics at automation supplier Festo, notes that pneumatic valves originally were bolted to machines at a convenient spot near the associated actuator. Over time, those valves migrated into manifolds due to a desire to centralize things. But, since this approach can put the valves further from cylinders, it might be better and more energy-efficient to go with smaller manifolds and shorter runs.
While this is happening, another change underway currently is an explosion of sensors and associated data, O'Grady says. Sensors now are found throughout a machine, and could be connected to or integrated into a pneumatic manifold. Doing so can pay dividends in two different broad applications involving motion and process control.
"In a lot of cases, the PLC program has some functionality to check if there is pressure before it attempts to use that pressure for motion," O'Grady says of the first usage scenario. As for the second, he adds that often it's possible to determine something about the process from the pressure being applied to the actuator.
Finally, an important point to keep in mind in any motion solution is the nature of the legacy setup, if there is one. What was done before will influence any retrofit or upgrade. After all, it's difficult to completely ignore what was used previously.
"If it was pneumatics before, sometimes you could want to stay with that," says Mario Mitchell, product manager at Parker Hannifin.
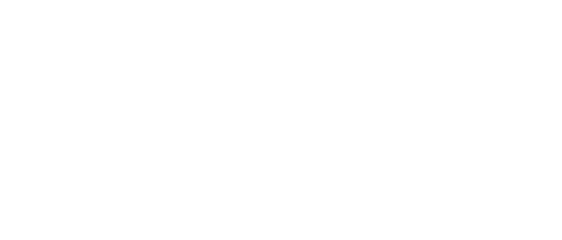
Leaders relevant to this article: