When we configure and wire our control panel housings, we follow all the regulations to the letter. However, because our panels house a constantly increasing array of devices, we're faced with design uncertainties about issues, such as how much expansion space (mostly for I/O) to leave in the panel; the most efficient designs to minimize wiring; how to leave only the minimum device spacing and deal with device density and potential overheating; and how to avoid additional cooling requirements. Simply asked, who has some best practices they've learned and would share?
—from January'14 Control Design
Answers
A Lot to Consider
This is a complex question with no easy answer. When asked to design for future expansion, you need to understand the process being controlled, and if the process has no room or plans for expansion, then maybe no future space is required. The question of budget is also paramount when determining how much extra space and equipment can be included in the panel. A commonly specified spare space requirement is 20%, but most engineered drawings and panel layouts do not show this. Is it the panel builder's responsibility to correct this at bid time and possibly not capture the work against a panel builder who quoted to the drawings which do not show this spare space and equipment?
Make certain the wire duct is sized for some (about 25%) extra capacity, some of which may be used in the field for the base design I/O.
My rules of thumb are:
- Leave room near the power distribution sections for one additional power supply and several (20%) control fuses or circuit breakers with terminal blocks;
- Design cooling for 20 to 30% extra capacity, some of which is absorbed at the base design level due to dirty filters that often do not get attention;
- Side panels in some cases can be added to the interior left and right walls of the enclosure, and if you plan for this when designing the enclosure, it can often be a great benefit later. This requires the enclosure be deeper than specified, but if explained to the customer, it is easy to sell. A deeper enclosure also helps when future additions of HMIs or pushbuttons are done, thus reducing the risk of these devices bumping into back panel components;
If the panel I/O terminal block arrangement is not defined well, then careful planning can save considerable space. Some engineers want every channel fused for DI, DO, AI and AO, which can add up very fast. Perhaps group-fusing, dual-level or compact fuse/terminal blocks can be used.
—Ken Schultze, Engineering manager, Easter-Owens, www.easter-owens.com
Manage the Wires
Putting too much in one control panel can be costly if you introduce EMI noise, thermal problems or poor network connectivity. Up to half of the control panel space is consumed for wire management that is often inefficient. Optimize how DIN-rail modules and terminal blocks are deployed with wiring duct to reduce space required and provide design flexibility for device spacing and future expansion. A rapidly growing area that consumes significant panel real estate is Ethernet switch deployment. A new way to deploy Ethernet switches is to install separate, pre-wired, integrated zone enclosures with optimized spacing for these critical network connections. Panduit and Pentair Hoffman collaborated on a new website, www.hoffman-panduit.com, to share control panel best practices and learnings on topics including space optimization, noise mitigation, environmental protection (including thermal), security and safety.
—Dan McGrath, Industrial automation solutions manager, Panduit, www.panduit.com
Machine Mount Alternative
When configuring control panels to accommodate ever-changing I/O points, consider the worst case. But this might result in an oversized control panel, which is not cost-effective and could leave the customer asking why such a large cabinet. Our solution is to not put the I/O points in the control cabinet, but to use an on-machine solution, such as Allen-Bradley's 1738 ArmorPoint I/O. It can be mounted on the machine without a cabinet and close to the sensors and actuators. With connectivity support for DeviceNet, ControlNet, EtherNet/IP and Profibus, it can be used with a wide variety of PLCs.
—Joe Allard, Controls engineering, Pearson Packaging Systems, Software Aids
You should take a look at 3D virtual validation. By using some very simple but effective tools you can easily create, edit and visualize your complete enclosure in 3D before you decide to manufacture that enclosure.
Our Pro Panel, for example, will allow you to link all your components in your enclosure with the schematic design, eliminating errors in missing components or using the wrong components, thereby adding cost by delays in delivery and increased manufacturing times.
Through the wire list provided to you by the schematics, the software can route these wires in 3D and give you an accurate length calculation. A function to minimize wiring is also available based on the current position of your devices in the panel. This can be a big money-saving feature since you'll be using less wire.
Once the wires have been optimized and length has been calculated, the software exports all the wiring data to wire-cutting machines for automatic labeling, stripping, adding ferrules and cutting the wires for assembly.
By capturing power dissipation values on the components, Pro Panel in conjunction with RiTherm from Rittal can also can give you recommendations on what size of cooling requirements are needed for that enclosure.
Finally, you can capture minimum spacing requirements and visualize these in 3D, giving the user visual validation that the components are correctly positioned and spaced in the enclosure.
—Sean-Patrick Mulherrin, Product manager, Eplan Electric P8, Eplan
[Here's a response we received as a result of posting the problem to LinkedIn's Panel Building and System Integration Group.]
Out of the Box
Have you considered distributed I/O systems like AS-i? This makes expansion and redundancy really easy, as well as reducing the size requirements of your panels. With a well-designed, distributed system you can reduce your main panel considerably, making considerable savings on installation in the process.
—Ian Salter, electrical and controls design engineer, Dematic
[Here's part of a thread about the problem from LinkedIn's Industrial Automation Group.]
Check List
First, if you (and your customer) agreed to install an additional peripheral cabinet in case there's a future need for expansion, be sure that you will have physical space to do that. Simple mistakes, big troubles.
Second, do a thermal calculation to design the necessary cooling for the main control panel, and take into account site temperatures and altitude. In any case, I recommend adding the most possible main panel additional capacity (installed or not) and at least a 15% cooling capacity reserve. It's not very nice when the customer adds more and more elements to change the power requirements, and you must change the cooling system.
Third, leave some signal I/O in spare. Maybe this is an extra cost, but for the long term, customers always need something at the last minute. No more than 2 to 5%. And don't tell the customer, or they will take this as available space and find something to put in there.
Fourth, leave some power left in your power supplies. I prefer 20% minimum, just in case you find on-site more inductive charges or changes in the engineering design.
Nowadays, customers want to have simple and small cabinets, so put communication-capable devices into the main cabinet (protections, contactors, peripheral I/O) with terminal connections directly to the process.
—Cristian Oyaneder, Owner, General Manager, SA Asinpro
A Size Bigger
Here's a general tip: Avoid sizing a control panel to the depth of the tallest component. Go up to the next larger size. For example, if your tallest component is 7.8 in., go with a 10-in. deep enclosure instead of an 8-in.deep enclosure. You might find it helps you avoid issues in design expansion plus other future areas.
—Patrick Dowden, President, Automation Southwest
Think Tens
The basic rule of thumb from experience is basically the 10-10-10 rule. This is a 10% installed spare per I/O type in the panel. The next is to allow for 10% expansion of I/O and termination in existing I/O racks. Third, allow for another 10% real estate spare in a panel to allow for future remote racks with I/O modules and their terminations. Anything more than that, and the expansion should be deemed as a major one, and a new RTU can be placed within that process area. One thing to remember in this rule is to allow for power consumption at the maximum installed-equipment level. This should include the maximum space that would be required for distribution of ac and dc circuitry. I also agree with Patrick Dowden regarding the sizing of panels. Size is a small price to pay for the flexibility you gain.
—Uwe Kurfurst, Director, Moore Process Controls LLC
[This is from a thread on LinkedIn's Industrial Automation and Process Controls Network Group.]
Outside the Box After a Point
I usually use 20 to 25% spare space in panels, with 25% if I know expansions will happen eventually. If the requirement is to keep things as small as possible, then I will stick to 20% spare, but then make recommendations to use IP67 I/O for expansions, and most times as a part of the initial design.
—Christopher First, equipment and controls planning engineer, Altran North America
[This response is from LinkedIn's Automation Engineers group.]
Six Steps
Based on my experience of almost 30 years in design of control panels using relays and now with PLCs, I can share with you the following:
- Provide a minimum of 25% I/O expansion space;
- Place switched-mode power supply on top, below a roof-mounted exhaust fan. Reserve the first top row for the power supply and for circuit breakers with minimum 30% spare space, so that future additions can be made, as well as offer better cooling due to extra space;
- Leave clear space of 300 mm between floor and start of terminal block (TB) rail. This space is required for dressing the bottom entry cables from field;
- TBs connected to a particular I/O card should be grouped and identified by group marker. Leave 30% extra free TB rail for housing TBs in future. This should be evenly distributed;
- Leave minimum 30% space free in cable raceways to accommodate additional I/O wiring; and
- Ferruling should be I/O hardware-based with slot/location reference. User can easily locate grouped TBs for each I/O.
Besides that, wiring drawings should be detailed and easy to follow. This will ensure peace of mind for the system integrator and panel builder!
—Santhiraj Sathanna, Consultant director, Futura Electronics Pvt.,Ltd.
Add Access
Years ago, we were presented with limited floor space for control panels. When the control panel/operator console is larger than the machine, you have a space crunch! So to pack things as efficiently as possible, the control enclosure was a spilt front/rear enclosure with swing-out panels. It made for a very tight package with a Modicon 984, rack-mounted PC, five power supplies and DIN-rail-mounted contactors, signal isolators, etc.
Today with remote I/O being more prolific, you can probably anticipate expansion using this technology. Also, consolidating functions into one device, such as an industrial PC, will reduce the component count, reduce labor assembly cost and reduce wiring mistakes.
—Simon Gibson, Controls engineer, Mathews Co., www.mathewscompany.com
[And from LinkedIn's Business Industrial Network Group.]
The Possible Outcomes
As you said, there are design uncertainties that are an unknown and hard to design into a panel when it's a future requirement. If you're designing a panel so full that component spacing and thermal qualities need to be engineered, then your designs are only to the absolute minimum standard, and that's not a best practice but rather just an acceptable practice.
To the question of how much expansion to design in, I always designed for three possible conditions:
First, to easily contain the components needed to do the job as per requested functions;
Second, to adequately contain the components needed to do the job, plus any of the most probable additional functions; and
Third, to be capable of being modified in order to contain the components needed to do the job, plus any possible additional functions.
I would then design the panels to be capable of the second condition, build the panel to be capable of the first condition, and have a backup plan for the third condition. As an example, you can build a panel that is perfect for the first condition and is a bit tight if changed to the second condition, and you have a backup plan of having to add a fan due to thermal concerns if you have to go to the third condition.
Another example would be a panel intended for 10 motor starters with the likelihood of two more starters and the possibility of yet two more starters. Consequently, you would design a panel for 12 starters and build it with 10 starters and two open spaces for the two additional starters later. You would also design in the possibility of moving all the existing starters closer together to accommodate the last two starters, provided doing so does not compromise any engineering standards and only runs them to a tighter limit.
—David Schumacher, MMP, controls/automation technician
Smaller Wire Ways Possible
At the companies where I have been employed, the rule of thumb was 80%. That is, when you buy a PLC, don't use more than 80% of the I/O to leave room for modifications. Components such as power supplies, drivers, etc., have space requirements for heat dissipation. One should always follow the manufacturer's specs. After all, they did the investments in testing. Why not take advantage of their money? You're paying for it anyway when you buy their product. And should it fail under warranty, the first thing they're going to ask about is installation and how much room was left for air circulation.
One more thing to look at is wire size. In recent years, devices have become more efficient, so amps are down. A good example of this is 24-Vdc power supplies. Anyway, the size of the wires can be decreased, leading to smaller wire ways. This can increase the space around the drivers and such.
More and more, companies want smaller electrical cabinets, so all these things should be considered when engineering and constructing electrical cabinets. Good luck
—Chris Leber, electrical assembler, GL&V
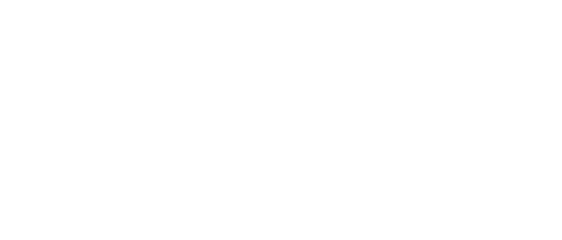
Leaders relevant to this article: