After working as a semiconductor process engineer, Hank Hogan hung up his cleanroom suit and now writes about process control and other technologies from Austin.
Also Read: Three Top Tips When Designing Motion Controllers, Part 1
Empire Magnetics provides solutions for some demanding environments, including space, underwater or in hazardous areas. Stepper motors can be the right answer for motion in such situations. A case in point is in a satellite, for which only a 24-V supply might be available. Any motor has to fit into a tiny space, and the time to complete a given motion may be unconstrained. In this setting, a small stepper motor may be the right answer.
Special circumstances also might dictate motor selection, according to Halstead. "In a nuclear reactor, for instance, the need is to have as few wires as possible penetrate the shielding," he says. "Then a stepper is preferable, as it requires far fewer connections than a closed-loop, servomotor system. Besides being simpler in terms of wiring, a stepper also can be inherently safer, as it cannot go into a runaway situation due to feedback control failure."
If wiring is an important issue, then stepper motors could be the best choice. Steppers only require a handful of wires. "OEMs typically can expect to connect four wires and a ground," says Paul Coughlin, team lead technical support at motor maker Kollmorgen.
A servomotor, in contrast, can have as many as six to 17 additional wires, with all of these due to the feedback mechanism. The relative simplicity in the wiring brings an added bonus. Incorrectly wired stepper motors could rotate in the opposite direction if the phase is reversed or simply not move, according to Coughlin. On the other hand, a servomotor wired in error could take off unexpectedly at high speed because the feedback control is missing or incorrect. Another aspect of ease-of-setup is that steppers require no tuning, something not true for the alternative.
Stepper motors also are simpler to deal with during the design phase of a project. Typically, they are sized for peak torque plus a safety factor of 50 to 100%, Coughlin indicates. Other motor technologies might involve more complicated calculations during design, with acceleration, deceleration, slew rate, RMS torque, dwell time and other factors that require consideration.
That simplicity translates into a lower initial cost as well. Stepper motors run about half the expense of a servomotor and its associated control mechanism. For an application appropriate for an open-loop system, such as bottles being directed one way or another by a lane diverter, a stepper motor can be the right choice.
Microstepping technology has made the decision to go with a stepper motor easier in circumstances where smooth motion is desired. The standard for steppers used to be movement of 1.8° or 200 steps per revolution. That approach resulted in a jerky start and stop because early steppers went from no movement to an immediate 60 rpm or vice versa.
With microstepping, the standard 1.8° is further subdivided by a factor of as much as 250. The result is smoother motion and better ability to move through and in the low-end-resonance speed region.
An application that could benefit from a stepper motor is a dosing machine, says Dave Beckstoffer, project manager at Portescap. "If what's desired is the dispensing of, say, 5 ml, then a stepper motor could be a good fit," he says. "The speed is slow enough, and the torque is low enough for the technology to handle. The mechanical nature of the stepper motor ensures that the amount of liquid dispensed is precise."
That precision is achieved without the use of encoders and feedback mechanisms. Employing these devices and techniques can add to the burden of a CPU responsible for machine control, and could potentially require a more powerful processor.
When it comes to designing an application solution, vendors offer software that can make the job easier. Portescap, for instance, has MotionCompass, which guides users through motor selection in a three-step process. The final decision, though, should take into account the duty cycle of the application, Beckstoffer notes, as that can impact the size of the motor needed.
"It will potentially allow a smaller motor solution to be used. If you're turning on for a few seconds and then going to be off for a minute, you might want to overdrive the motor and let it cool down, and you'll have no adverse effects from that," he says.
So for torques in the fractional horsepower range and for speeds of a few hundred rpm, a stepper motor could be the best choice. Steppers cost less than the alternative, are less expensive to wire and place fewer demands on the rest of the system. Under the right circumstances, they also bring the benefit of precision, potentially leading to a quick decision as to which motor technology to use.
As Beckstoffer says, "If I just need speed, I'm choosing dc or brushless. But if I need precision, my first thought is that I want a stepper because that's what it is designed to do."
Steppers cost less than the alternative, are less expensive to wire and place fewer demands on the rest of the system. Under the right circumstances, they also bring the benefit of precision, potentially leading to a quick decision as to which motor technology to use.
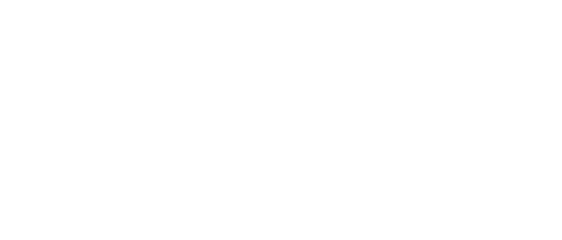
Leaders relevant to this article: