Although most 3D printing systems use little in the way of conventional motion control technologies such as found on most machines on the factory floor, builders of 3D printers and large motion control suppliers alike agree that advances and improvements to additive techniques are changing the face of industrial automation and how companies manufacture things.
It's probably helpful to note that the term "additive manufacturing" (AM) is replacing "3D printing" in industry because technologies such as fused deposition modeling (FDM), electron beam melting (EBM) and stereolithography (SLA), among several others, also build up three-dimensional parts layer by layer. Techniques might involve an extrusion head working its way around a part, an electron beam moving across a bed of metal powder, a UV laser traveling across a vat or any of several other approaches.
Figure 1: 3D printed fuel nozzles replace complex assemblies that traditionally took 20 parts that were machined, cast, brazed and welded with a single part instead.
According to Tim Caffrey, senior consultant at 3D printing consultancy Wohlers Associates, AM, which has been building prototypes of designs, tools like jigs and fixtures, and custom medical implants for years, is moving into making end parts in relatively high-production settings.
For example, improvements in EBM now let medical device manufacturers build standard-sized orthopedic implants in large lots instead of making custom implants derived from each patient's CT or MRI data, as in the past. "To date, more than 80,000 standard acetabular implants have been manufactured using EBM machines from Arcam in Sweden," Caffrey continues. "Hospitals stock the parts as inventory, and use them as-needed for hip replacements."
In addition to medical equipment manufacturing, AM plays a part in the aerospace and, to a lesser degree, in the automotive sectors, Caffrey says. "Production volumes in automotive hit millions—much higher than aerospace—so automotive OEMs tend towards traditional methods such as CNC machining or injection molding because the processes are fast, accurate and repeatable."
The bang for the buck an aerospace OEM gets from AM is what's called the "lightweighting" of parts, Caffrey says. This practice combines the many parts that would typically go in an assembly into a single component.
Aviation Leaps Into Additive
For example, GE Aviation uses EBM machines from Arcam and other AM technology to build its next-generation jet engine, the LEAP. According to Greg Morris, leader additive technologies, GE Aviation, the company 3D prints its fuel nozzles because it allows making complex assemblies that traditionally took 20 parts, which were machined, cast, brazed and welded, and makes them as a single part instead (Figure 1).
"As far as networking, our additive machines are centrally hooked to the network, but only as a means to send part files to each machine," Morris says. "We're working on mechanisms to save data from the machines to optimize future builds."
Figure 2: The images show Arcam’s special EBM technology. The component to be manufactured is created in a 3D CAD design that is transferred to the machine´s control computer. The work chamber is loaded with metal powder and a vacuum is established. The system´s electron beam melts the metal powder with high energy, and the part is gradually constructed according to the design by a thin layer of powder being added to the part and melted. The process is repeated layer by layer until the entire part has been built.
Magnus Rene, Arcam president and CEO, says, "EBM machines have only one axis, which moves the bed up and down using a stepper motor, and a powder rake that rakes the powder out, so the machines don't use too much in the way of traditional motion control (Figure 2). The engine is controlled by electronics, but it's really not motion control—it's more deflection electronics."
FDM machine builder Stratasys, Eden Prairie, Minnesota, targets aerospace companies, including Northrop Grumman, GE Aviation and Lockheed. The machines build up end-use parts in standard, engineering-grade and high-performance thermoplastics. One example comes from non-flight-critical, lightly loaded, aircraft ducting and bracketry made from the company's proprietary thermoplastic, which meets aerospace standards for non-toxicity and self-extinguishing capabilities. "There are lots of costs associated with machining, so we've sometimes provided positive ROIs in replacing machined aluminum with FDM," says Chris Holshouser, senior manager for global manufacturing solution development at Stratasys' aero, auto, defense business unit.
Holshouser adds the FDM process is custom-made, and current platforms use controllers built in-house to keep costs down.
"Belt-driven FDM systems work well in balancing cost and throughput, but when we started making machines with larger build envelopes, we used a ball screw to support scalability," Holshouser says. "As systems evolve and manufacturing demands increase, moving to a more capable control technology such as linear motors is something that should be considered. Opportunities certainly exist to leverage expertise from current leaders in the controls industry that have been down this road longer than us."
Automation Speaks Out
According to Travis Schneider, product manager—linear mechanics, Parker Hannifin, for about 10 years, Parker has been supporting AM machine builders of mid- to high-precision machines that are used in aerospace and automotive industries. "We see a trend toward higher-precision systems as well as higher-speed systems," he says. "As part features become finer and machine speeds increase to meet demand, AM builders' needs have shifted. Parker can support AM builders' motion and control needs with fully engineered standard components such as high-precision linear actuators, servomotors, drives and controls, or a clean-sheet design of a full motion solution. We also can help machine builders address issues ranging from reducing velocity ripple to improving machine throughput."
One division of Parker even provides 3D printing services. Paul Gray, manager, advanced manufacturing technologies, c in the U.K., says the facility houses three selective laser sintering (SLS) machines and a Stratasys system, which can build parts as large as 355 mm x 254 mm x 254 mm. "We were an early adopter of this technology, making prototypes and working parts for our in-house manufacturing process for more than 14 years," he says. "We also provide services to other Parker Divisions and external technology users such as Lotus F1 [Formula 1], Red Bull F1, Mercedes F1 and Airbus Industries. We have long thought that AM can be used to manufacture as well as to prototype, so we have lots of experience in exotic materials and process control."
"Considerations that might arise with metals in the aircraft industry include how manufacturers should qualify the powder they use and quantify the entire process," Gray says. "In the U.K., lots of research is being undertaken within industry and universities on resolving this issue, because once process control is nailed, manufacturers will feel more confident about 3D printing metal-based parts that could be used safely in life-critical situations."
Jerry Sorrells, control and HMI product manager, Parker Hannifin Automation Group, points out that for additive processes to grow more into mainstream manufacturing, system throughput must increase. "When you try to speed up certain deposition methods, control and optimization problems arise, such as overshoot, settling time and mechanical stiffness among others, which can negatively affect quality," Sorrells says. "To increase throughput for mainstream manufacturing, we likely will see pipelining techniques and collaborative robots employed, where different printing systems will work together to produce an assembly made up of parts from highly dissimilar materials."
Roger Hart, head of R&D for Siemens Motion Control, agrees that some additive technology isn't too challenging from a traditional motion standpoint. "For instance, metal deposition and FDM are being controlled with traditional CNCs with little or no additional feature enhancements. In addition, some AM techniques have lots in common with the synchronous, path-based, on-and-off control of conventional laser-cutting machines. However, there are interesting things going on with closed-loop machining, where damaged parts are digitized with 3D cameras and then compared to the original design. Hybrid machines then can be used to simultaneously add to and subtract from the part until it is ready for the next stage. However, state-of-the art technology for this is currently barely automated."
Additive With Lots of Motion
Figure 3: The MX3D printer combines an industrial robot with an advanced welding machine to 3D print metal in any axis and on a large scale.
An additive process with a lot of motion comes from the Joris Laarman Lab in Amsterdam, the Netherlands, although the process is not ready for high-production prime time. Autodesk is working with the lab to help develop control software for the lab's MX3D printer, which combines an industrial robot with an advanced welding machine to 3D print with metals such as steel, stainless steel, aluminum, bronze or copper (Figure 3). The robot moves a torch, which deposits a few drops of molten metal, waits for the metal to cool down, and then moves slightly and deposits more metal. This fully free-form printing approach needs no support material and allows printing in any axis.
"The machine pushes the envelope of high-deposition FDM," says Maurice Conti, director at Autodesk and a member of its CTO's team. "Typically, in industrial automation, a company sets up a robotic work cell, which then does the same operation a million times over. So if it takes a month or six months to program the work cell, that's okay because it might be performing that operation anywhere from one to 10 years.
In contrast, the MX3D asks the robot to do something once, and only do it for a short time. "So if it takes longer than a few seconds to program the movement, it's probably easier to do it non-robotically, which defeats the whole purpose, Conti says. "Eventually, we hope to adapt the printer for real-world manufacturing, especially to quickly print things on a larger scale—anything from the size of a breadbox to an object as large as the room that holds the robot. Because the builds are pretty rough, we're working on including a subtractive process that would machine the metal as it is being deposited for a smoother surface."
The biggest challenge has been creating software that can talk to the robots easily, Conti says. "For industrial software, the technology stack goes from the actual instructions the robot is receiving from its controller, such as the servo being told to move, all the way up to the design software. In some cases, we bypass the robot software and talk directly to the controller in engine code, or we bypass the controller and talk directly to the servos. The traditional robot stack is incompatible with what we're trying to do."
Imagine a future in which every part that goes down the line could be different, and each line would adapt in real time. "The control software would have to understand what's coming down the line and, depending on the blank, it would make a specific part using a particular set of robotic instructions. Also, the electromechanical systems, the robots themselves, would need to be flexible in the operations they can perform, so the line can be dynamic in that way."
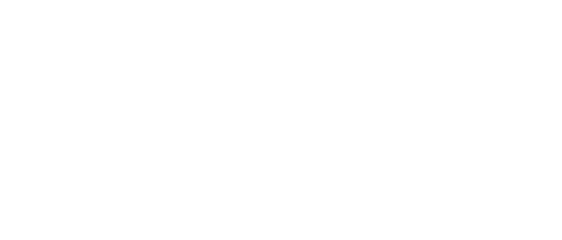
Leaders relevant to this article: