Hillshire Brands operators improve visibility into production data with alarm management to cut waste
• Company-wide, Hillshire standardized on the Logix control platform for scalable control.
• EtherNet/IP network provides seamless, real-time communications structure and single design environment with consistent tools.
• FactoryTalk VantagePoint software aggregates, correlates and presents production information to operations, so variances are easily identified and corrected in real-time.
• FactoryTalk Historian software automatically identifies, gathers and stores production data.
• Grantek Systems Integration, a Rockwell Automation PartnerNetwork program Solution Partner for control, process and information, led system design, configuration and implementation.
• Annualized yield improvement of 0.10%, or more than 100,000 lb of sausage, translates into a significant return in cost of goods sold.
• System ROI will be achieved in less than a year
Americans consumed almost 450 million lb of breakfast sausage and ham in 2012, equating to nearly $1.5 billion in sales for sausage producers. While it might be true that most people don’t want to see the production process behind this hearty centerpiece of breakfast, this growing consumer base wants to know there are keen-eyed, well-informed operators on the plant floor ensuring the integrity and quality of the product.
The Jimmy Dean brand, part of the Hillshire Brands portfolio, sells more refrigerated breakfast sausage than the next top four producers combined (Figure 1). Hillshire Brands is a wholly owned subsidiary of Tyson Foods. To maintain such a leading position, we must not only offer a consistently high-quality and uniform product, but must do everything possible to keep costs low and throughput high, maintaining a competitive price point among competition eager to cut into our market share.
Too much chub
The Hillshire Brands facility in Newbern, Tennessee, produces more than 150 million lb of sausage annually. The Jimmy Dean 1-lb fresh sausage rolls, affectionately called “chubs,” account for more than two-thirds of this production total. The facility dedicates 11 machines to grinding, seasoning, filling and packing chubs of more than 300 different SKUs. Plastic-wrapped sausage chubs are sold by the pound, so getting just the right amount of sausage in each roll is crucial. At the end of each line, a check weigher assesses and removes chubs outside the acceptable weight variance. Off-weight chubs are manually sliced open and repackaged at the appropriate weight, a costly process as a portion of meat is not recoverable once repacking is initiated.
Because the product is priced per package, any amount of meat included beyond the required weight results in lost revenue. At the same time, if a chub is underweight, customer satisfaction is at risk, as customers are not getting what they pay for. Additionally, the Federal Meat Inspection Act requires that packages of meat products bear an accurate statement of the quantity of their contents in terms of weight, measure or numerical count. Every state in the country has similar or additional regulations. If a weights-and-measures inspection finds packages mislabeled, the food cannot be sold and fines can be incurred, all of which is damaging both to a company’s reputation and the bottom line.
Also read: Get in touch with HMIs and machines
Figure 1: Armed with new levels of information, Tyson engineers saw a yield improvement of 0.10% within six weeks of rolling out the new system. This translates into savings of 105,000 chubs per year and hundreds of thousands of dollars in cost of goods sold.
In October 2012, it was identified that operators at the Newbern plant were experiencing unacceptable variances in chub weight, giving away and throwing out too much product. Unfortunately, at the time, operators did not have access to enough control-system data to understand the actual amount or cause of giveaway. By April 2013, a full solution was implemented.
Waste reduction
Plant engineers at Newbern saw an opportunity to reduce weight variance if they could better understand the cause of the problem, so they brought their problem to corporate engineering for help. I had already led the implementation of a manufacturing intelligence strategy and information system at plants in Florence, Alabama, and Kansas City, Kansas. After listening to concerns from my engineers in Tennessee, I brought in a team from Grantek Systems Integration to implement a manufacturing intelligence strategy in Newbern.
Grantek worked with the Hillshire Brands control, quality and maintenance engineers to understand the behavior the team wanted to drive with a manufacturing intelligence strategy. For the plant team, a better understanding of finished product weight was the top priority. However, additional data points throughout the process line were also necessary to understand how weight fluctuations were occurring.
Grantek worked with us to implement a manufacturing intelligence solution based on the FactoryTalk software suite. The software integrates directly with the Logix control platform from Rockwell Automation to access real-time production data. Hillshire Brands had previously standardized on the Logix control platform across all of its facilities, which simplified integration of the information software to the plant-floor control system.
The check weight unit is able to reject products with a weight variance above and below our targets. The FactoryTalk VantagePoint system from Rockwell Automation provides a reporting structure to identify how many of the underweight and overweight products are produced (Figure 2). It also provides statistics such as standard deviation to tell the operators how their equipment is running versus its capabilities. The operators are able to see these reports and statistics throughout the workday.
Figure 2: With the software in place, operators can see weight fluctuations along the line, the exact giveaways on finished chubs, machine downtime, OEE and even meat temperature.
Additionally, the Newbern plant was already running on a single industrial network, EtherNet/IP, which greatly simplified data collection. The team connected the 11 chub-line machines to two new on-site servers running FactoryTalk Historian software via EtherNet/IP. This allowed the team to collect data over longer-term periods for trend viewing and compare performance across machines. During a shift, if one machine is producing chubs of greater variance, the operators can look at past data and see just when the issue began. If all other machines are functioning properly and under capacity, perhaps production will move until the issue is resolved.
We have our PLCs talk with a server that collects data into the FactoryTalk Historian system. We also use SQL to do some database calculations to combine information. We then provide reports and dashboards through FactoryTalk VantagePoint software based on the information contained in the historian software and SQL. The operators get their alarms through an HMI.
Grantek then installed FactoryTalk VantagePoint software to aggregate information from multiple data sources—the controller, historian and SQL server. Gathering data into one centralized dashboard provides easy access to real-time data and key performance indicators via any Internet browser. The FactoryTalk VantagePoint server is located in the Newbern plant. But, as a Web-based reporting platform, it is accessible to both corporate and Newbern personnel.
Before the implementation, the main operator interface on the equipment were HMI units from Rockwell Automation with Rockwell Software RSView Machine Edition software. The operators still interact with these to run the equipment, but the information we are providing comes through on TV-style monitors. The operators do not interact with the dashboards. They see a rotation of three dashboards that automatically update.
The Newbern plant engineers, those interacting with the data on a daily basis, worked with Grantek to design the system dashboards. The Newbern team had full control over what they wanted to see on the FactoryTalk VantagePoint dashboards. I’ve worked with this software enough to understand that there are almost infinite possibilities of what it can show visually. It’s very flexible, but the local team has to like it or they won’t use it.
Worth the weight
Before we implemented this system, operators could only see how many bad apples were produced. Now operators can see weight fluctuations along the line, the exact giveaways on finished chubs, machine downtime, OEE and even meat temperature. The alarms provided to the operators come on the HMI. We do record the types of alarms that occur so that maintenance can go back through a daily report to see where the big issues are on a piece of equipment.
Armed with this information, Newbern engineers saw a yield improvement of around 0.10% within six weeks of rolling out the new system. This translates into savings of 105,000 chubs per year and hundreds of thousands of dollars in cost of goods sold.
The control engineering team is certainly much happier. Now that they can see the weight of each chub as it goes through the line, they were able to track some variance to a specific filler and make a fix to reduce some of our giveaway right off the bat. We have incorporated FactoryTalk Metrics software to provide alarm reporting flow through to the KPIs and dashboards. But our quality assurance folks might be even happier. They were the ones that were doing all the weight checks. Instead of extrapolating giveaways based on hand samples taken several times a day, they now have constant, real-time insight into the weight of each chub, each batch and each shipment.
Though the yield improvement was all the company needed to justify ROI on the project, Hillshire Brands expects its new information solution to reduce giveaway another several tenths of a percent, increasing yield by up to 0.50%, or more than half a million pounds of sausage.
Beyond meeting and potentially exceeding our project goals, it’s important to our company that this solution is flexible enough to grow not only with production changes, but with our engineers’ changing perspective. The FactoryTalk system provides the data our operators need to understand what to pay attention to and where problems are occurring. Once they start to see the high-level patterns that were previously impossible to collect or see manually, they can determine exact causality and what changes we can make to improve the system. Weight adjustments are made by the operator choosing manually to increase or decrease the weight. After a few months, they start to ask for more tags, dashboards and reports. We are currently considering adding energy-use metrics to the system at several plants. The information is empowering, and they want more.
The operators make the weight adjustments using a manual process. We are working to move to an automated process for adjustments, which requires some information coming from upstream of the sausage-filling machines. The filling machines operate on a timed clipping procedure. We pump meat in and every x seconds the machine clips the package to get the right size and weight. Due to the fluctuations in fat percentage of the meat as it flows, the density of the meat changes, and we need to know the incoming density to automate the changes.
Latest from Alarms
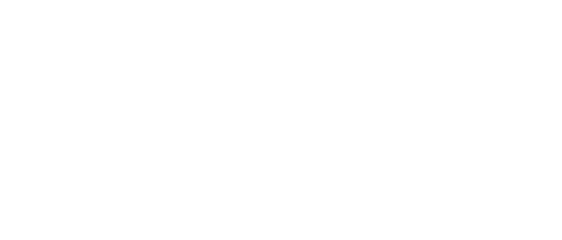
Leaders relevant to this article: