Because of recent improvements to the range and reliability of wireless I/O technology, it may be used as an alternative to hardwired connections.
“Depending on the situation, a wired connection can be difficult to implement physically because of the location,” says Earle Foster, senior vice president of marketing at Sealevel Systems. “Wireless connectivity also can be a perfect solution for mobile applications like monitoring a forklift or communicating with test equipment moving down an assembly line.”
Also in wireless’ favor are lower implementation costs. “Trenching through harsh areas sometimes can come at a cost for permits, special equipment to keep the cable safe and extra approvals to allow the hardware in the hazardous area,” says Justin Shade, product marketing specialist—wireless, I/O and networks for Phoenix Contact USA. “Simply using a wireless solution to transmit through these environments helps avoid those hurdles.”
Maintenance also can be easier with wireless I/O because it lets the technical maintenance staff troubleshoot systems from a nonhazardous safe zone in real time without taking the system offline, says Andrew Barco, product manager—network connectivity, Weidmuller North America.
Also read: Is wireless the right solution?
While wireless I/O can solve some issues, there are other considerations to keep in mind, including the finite bandwidth that all devices share.
“This frequency range of 900 MHz/2.4 GHz/5.8 GHz is shared not only by the industrial wireless products, but also with other mobile devices, printers, tablets, office Wi-Fi and more,” says Barco. “This is when an efficient peer-to-peer solution comes into play for larger installed bases. It only transmits when there is a message to send, effectively putting its radio portion into sleep mode. It ensures that all radios are not talking simultaneously and makes maximum use of the limited bandwidths. A peer-to-peer solution also is easy to expand and grow with systems as needed. They can connect and work seamlessly with very little setup. The automatic mesh topology makes installation a breeze for both in-building and outdoor applications.”
Another challenge to wireless I/O is a noise-prone environment, which may result in a loss of transmission from that noise. Welding is the extreme case of a noisy environment. “Wireless I/O technology as it stands today might be a better fit for less noisy environments such as lab automation,” says Shishir Rege, marketing manager, networking and connectivity, at Balluff.
Also of concern is supplying power to actuate the output or valve. “A wireless sender may be able to convey the data for the outputs to the receiver, but power to activate the valve may still need to go over the power cable,” says Rege. “If the primary purpose of using wireless I/O is to avoid cables for hard-to-reach areas, then an inductive coupling solution that offers transmission of power and data over a small air gap may be a better alternative.”
As with all implementations, wireless I/O requires planning. “Wireless I/O modules have a specified range of operation, typically 100 m or 328 ft,” says Charlie Norz, Wago-I/O-System product manager. “To optimize signal quality and prevent signal absorption by plant equipment, walls or piping, care has to be taken in the planning stages to ensure that the antenna of the wireless I/O is placed in an open/direct area.” As with any technology, the decision to use machine-mount or wireless I/O often comes down to a particular application’s specifics, adds Norz.
Another issue to plan for is latency. “When sending I/O wirelessly, one common misconception is assuming the transmission will be as fast as if you were running a standard wire,” warns Shade. “In a wireless system, whether it is a high-speed WLAN system or a slower 900-MHz system, there is inherent latency added that is not seen when transmitting over a wire. As long as this latency is taken into consideration during the planning stage, there typically is no issue implementing a wireless I/O system.”
While improvements have been made to security, it still is a big concern. “Most wireless I/O uses standard open frequencies,” says Kevin Romer, product manager, Advantech Industrial Automation Group. “Although obviously it’s illegal to knowingly interfere with a wireless system without permission, it is relatively easy to attain equipment.”
Romer suggests implementing wireless I/O in such a way that it eliminates the security issue. “The more practical way is to implement wireless I/O for noncritical information,” he says. “One way is to use the wireless I/O as a tool for an installation contractor to help monitor systems during a startup. For instance, an HVAC contractor is hired to balance a large HVAC system because people are complaining about hot and cold zones. Normally you would install temperature sensors throughout the building to record and monitor those. There is nothing wrong with that except in the case where you didn’t install a temperature sensor. A wireless solution is best in this case because of the ease of installation.”
Romer says that this would not disrupt the day-to-day business inside the building because the HVAC contractor can simply install a battery or ac-powered wireless device to send temperature signals back so he can monitor as he tunes the system.
“The important aspect of this is the HVAC contractor is not relying on these signals for crucial information because they are being checked by other hardwired equipment,” he explains. “Instead this provides the additional information the contractor needs to make his job easier and provide less hassle while at the same time listening to hot/cold zone complaints. If a system is improperly designed to account for the reduced signal in the extreme condition event, communication will be interrupted, resulting in false I/O readings and control. Integrators implementing a wireless solution must account for the specific type of environment to overcome the reduced signal loss, so that when the most significant wireless condition occurs, the minimum receiver signal is maintained.”
Main image courtesy of cuteimage at FreeDigitalPhotos.net
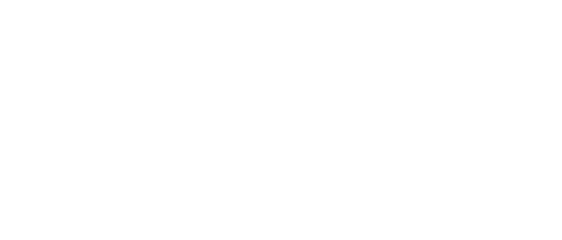
Leaders relevant to this article: