Manufacturers are producing plug-in data acquisition (DAQ) boards, data recorders, and software capable of handling data rates in excess of 10,000 readings per second. This data is becoming accessible over the web. Who needs this type of speed? Well, your customers do, for starters. And in ever-increasing numbers, machine builders do, too.
Machine builders are embedding the means to capture performance data in order to support the move toward after-sales service and support contracts. As end users turn to machine builders for service and maintenance support, OEMs need to gather this information to find faults, perform preventive maintenance, keep customers' machines running, and make a profit on their service contracts.
End users have high-speed DAQ for quality control, asset management, testing, maintenance, and other purposes. In some cases, it's necessary to acquire a great deal of data to capture information for testing and research (Figure 1), inspect material that is moving quickly on a web or through a continuous process, spot "blips" in processes, or find transient faults in process equipment.
Figure 1: DAQ Attack
High-speed data acquisition is critical for many closed-loop control systems, especially when high-frequency vibration control is involved. Exemplar Manufacturing (http://www.exemplarmfg.com) cycles and vibration cycles wire harnesses, battery cables, and bond straps as they come off the manufacturing line, and then adjusts the manufacturing system in real time as necessary. [Source: National Instruments]
Historically, end users did all this themselves. But, as end users lose their in-house engineering support, they'll begin to expect OEMs to build in the capability for them.
And the Survey Says...
The need for speed is reflected in data compiled by Keithley Instruments (http://www.keithley.com), which conducts a measurement trends survey every year. According to Keithley vice president David Patricy, engineers have asked for faster measurement speeds (more than than 10,000 readings/sec.) and higher resolution (19+ bits) every year since 1998. "High speed and high-resolution measurements are critical," he says. This year, 19% of survey respondents say they want at least 10,000 readings/sec., up from 12% in 2000.
Engineers also want more accuracy. For the past three years, Keithley's studies show a steady increase in accuracy requirements. The latest survey says 30% of engineers require readings with 0.10% FS accuracy.
"The consistent yearly increase in accuracy mirrors what we see from our customers in both development labs and on the production floor," says Patricy. "As devices miniaturize and manufacturing indices continue to be pressured, our customers increasingly incorporate high-precision instrumentation into their test systems."
Keithley's 2001 survey showed customers seem to be happy with Ethernet connections, since it had the highest score in user satisfaction out of 12 communications protocols listed; and the 2002 survey says 29% of the respondents use Ethernet. Serial port and GPIB use dropped.
In a white paper, "Instrument-Grade DAQ via Ethernet," Keithley points out that Ethernet systems are much less expensive than any other interface, are easy to connect to PCs, are fast enough for high-speed DAQ, and work over long distances. The white paper compares Ethernet performance favorably to other high-speed industrial networking systems such as Universal Serial Bus (USB) and FireWire (IEEE-1394).
Keithley feels confident that its customers are now ready for the next step: web-based DAQ. It recently announced a new DAQ system, which combines 22-bit resolution, 10/100BaseTX Fast Ethernet, and a web server. The system can scan data at 500 channels/sec., transmit over Ethernet, make data compatible with Excel spreadsheets, and let users view data and diagnostics over a web browser.
Bently Nevada also has a high-speed DAQ system in the works that will transmit data via Ethernet and the web. Such devices should interest machine builders because of the increasing need for remote monitoring of equipment under service contracts.
More Machinery Monitoring
Builders of packaged process equipment, turbomachinery, power generating equipment, and similar systems need these data-collection capabilities, whether they supply it to customers for internal use or embed it for themselves, to facilitate after-sales troubleshooting. High-speed data acquisition (Figure 2) finds all kinds of process problems early on, before they can grow into big problems.
"Recently, we've started to emphasize collecting not just machinery data, but also the surrounding process data so it can be correlated with changes in a machine's mechanical behavior," says Steve Sabin, marketing manager at Bently Nevada (http://www.bently.com).
A good example of that would be a blip in a process that would cause a compressor surge, leading to characteristic vibration and other after-effects. "The ability to capture machine and process parameters at high speeds can often yield important insights into cause-and-effect relationships," Sabin explains. "Did the machine behave badly because of a mechanical malfunction, causing process problems? Or did process anomalies cause the machine to malfunction?"
Figure 2: Process Applications
Data acquisition equipment and PC software can perform vibration analysis on mechanical systems such as turbines, compressors, and pumps. [Source: Bently Nevada]
Knowing the difference is very important and is a big part of being able to manage the asset properly. "Typically, the ability to really manage a machinery asset requires an online DAQ system," he says.
Any industrial OEM or system integrator who builds for the power industry knows the unexpected loss of a generating unit can cost a great deal, so online machinery monitoring helps prevent unnecessary trips. American Electric Power (AEP), St. Albans, W.Va., has a Bently Nevada system to monitor vibration and process data. The utility suffered a turbine trip that was not easily explained until officials examined the process data.
"We found that the steam seal system's desuperheater valve was malfunctioning due to a problem with an air solenoid valve," says Ken Davis, senior engineer at AEP. "Without the data, we would not have been able to identify the problem so quickly and accurately."
Davis says the cost of a single turbine trip lasting four hours approaches $300,000. "The application of diagnostic and predictive maintenance at our plants is instrumental in avoiding unplanned shutdowns," he says.
High-Speed DAQ in Process Equipment Control
Obviously, you don't need high-speed data acquisition to measure variables such as flow, temperature, pressure, and level. Those parameters usually change slowly, except in the case of a trip or fault. Even so, a few readings per second are usually enough.
To spot transient glitches or blips, however, high-speed DAQ is needed. David Potter, measurements platform manager at National Instruments (http://www.ni.com), says in addition to vibration monitoring, high-speed DAQ can be used to monitor combustion, turbine pressures, power quality, webs, and similar applications.
"In web-inspection applications, a customer may use an array of sensors to determine the thickness of material such as film," he says. "The material may be passing by the sensors at rates of several feet per second, so they need a high-speed system to obtain data."
Maarten Meinders, senior research engineer at E.I. DuPont's textile plant in Camden, S.C., collects data on fiber-spinning machines with 64 sensors that measure viscosity, pressure, temperature, flow, fiber tension, and power levels on drive rolls and heaters. "The problem is that you can easily get data overload," says Meinders. "For example, if you capture a seven-second snapshot at 1 KHz, you get 7,000 data points per sensor. So, we use some tricks."
Meinders uses a LabWindows CVI system from National Instruments. He wrote a program that checks data until an event occurs, then starts taking snapshots. As soon as the system senses that a channel has exceeded predefined limits, it creates a high-speed snapshot of data and writes it to the disk. Snapshots usually are four to eight seconds long, but can be longer and contain more than a million data points.
"When an event occurs, LabWindows gives us an overview of 64 miniplots on one screen to look for sensor anomalies," he says. "We can click on plots to examine in greater detail, select regions and perform instant statistical comparisons, or see if there is a correlation among all 64 sensors."
Monitoring large internal-combustion engines at gas pipeline pumping stations presents similar problems. "We installed 23 fiberoptic pressure sensors on the power cylinders of three 25,000 hp engines," reports Alden Cramer, field engineer at Advanced Engine Technologies (
http://www.aetco.com), a company that specializes in engine control system design. "Pressure data from each cylinder must be continuously acquired at a rate of 2 KHz, phase-referenced to top dead center, and then reduced to extract key pressure values. Results are transmitted to the engine's process controller via Modbus, and made available at the engine catwalk for real-time analysis and diagnostics."The system uses a 32-channel data acquisition system and LabView software, both from National Instruments, and a ruggedized PC running under Windows 95. Cramer, too, doesn't try to process all the data all the time. "We use the 'Wait for Occurrence' function to free up the CPU for data reduction and transmission," says Cramer. In other words, between events, the computer spends its time continuously acquiring, reducing, and transmitting data and preparing outputs for operators.
"While many applications focus on acquiring data for diagnostics and analysis, we see other applications using high-speed data in the control loop," says Potter. "The web inspection application, for example, uses sensor array data to adjust web tension."
In recognition of the need for real-time control, high-speed DAQ vendors are beginning to release faster versions of hardware and software. As PCs gain speed and memory, and are better able to process vast amounts of information, the DAQ vendors are matching their need for speed.
Changing Attitudes
Historically, machine builders have barely tolerated vibration analysis. End users were the driving force, because the information let them identify problems early on and schedule maintenance accordingly. This cut their maintenance and repair bills.
"It was not in the machinery OEM's best interest to advocate such systems," says Sabin, "because it could reduce the end user's need for spare parts, emergency service, and other high-margin aftermarket products and services provided by the OEM. Fewer breakdowns and less need for service and parts were not consistent with the industrial OEM business models at that time."
That may have been the case years ago, but times have changed. End users don't have as much in-house engineering and maintenance capability these days, so they turn to their machine builders for after-sales support. It is now clearly in the OEM's best interest to find faults early.
"Today, we are seeing virtually every major machinery manufacturer offering long-term contractual service agreements," says Sabin.
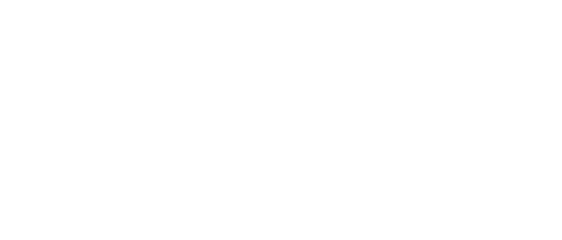
Leaders relevant to this article: