Factories have a variety of industrial machinery operated and maintained by end users and sometimes by the machine builders themselves. In the past, control and maintenance were usually performed right at the machine. Remote control was non-existent, and remote monitoring consisted of little more than a general trouble alarm contact. End users and machine builders are now moving toward a better way of managing industrial machinery, and these efforts are greatly aided by advances in communications hardware and software.
It is now possible to control, monitor, and troubleshoot most plant machinery from a remote location. The remote location may be a centralized control room, it may be a computer on a company intranet, or it may be a fixed or mobile communications device connected to the Internet. Remote machine management is saving end users money by optimizing machine operation, reducing downtime, and facilitating preventive maintenance.
Monitor That Operations Data
Merit Ink & Coating (http://www.merit-ink.com) manufactures automatic ink-dispensing machines (Figure 1). Packaging manufacturers and other users of finished ink products use the machines to mix their own ink formulations on a custom job-by-job basis. Merit worked with system integrator and application service provider Inteworx (http://www.inteworx.net) to implement a sophisticated Internet-based remote machine management solution.
Figure 1: A View From Afar
Ink-dispensing machines equipped with an Internet-based remote machine management system let users monitor production, costs, and materials from multiple locations. (Source: Merit Ink)
Machines equipped with the Inteworx system can automatically dial out via a phone line to a server farm operated and maintained by Inteworx. Alternately, a machine with an Inteworx system, an Ethernet interface, and an I/P address can connect to the server farm on a real-time basis through the Internet. In either case, clients can use a local ISP to access the Inteworx server via the Internet, thus saving long distance or Internet access charges.
The Inteworx server captures information from the machine and posts this data to a web site in the form of reports. OEMs or their customers are able to securely access the machine data from their company intranet or via the Internet from any web browser. The amount and type of data sent from the machine to the Inteworx servers is limited only by the needs and the imagination of the user.
Merit Ink's customers use the remote machine management system to monitor production, costs, ink usage, and inventory. Those customers' ink suppliers use the remote machine management system to monitor ink inventory levels and generate automatic invoices to prevent out-of stock conditions and execute just-in-time ordering.
The system will even keep track of the operators, too. Some of Merit's clients use the biometric scanner option for employee monitoring. "Our machines can be supplied with an optional fingerprint sign-in clock to record employee hours," explains Jack Tanksley, Merit's vice president of sales and marketing. "The fingerprint feature allows employee time to be tracked remotely and prevents clocking-in abuse sometimes associated with a simple time-clock punch system."
Merit's ink dispensing machine is controlled by an AutomationDirect (http://www.automationdirect.com) PLC with Ethernet I/O. The operator interface for the machine is a Windows NT-based PC running Think & Do control and monitoring software. The PC also runs and executes the Inteworx remote machine management software program.
More Satisfied Customers
EcoVend (http://www.ecovend.com), a manufacturer of machines that automatically dispense cleaning chemicals and supplies, also uses Inteworx remote machine management software. Most EcoVend machines are equipped with the biometric fingerprint scanner, and EcoVend clients use the scanner as a time clock and audit trail for product-dispensing requests.
EcoVend clients use the remote machine monitoring system to perform many other functions. "The EcoVend monitors the quantities of cleaning supplies used, provides operational status of the machine, sends automatic notification of maintenance needs, and orders supplies automatically," says Kirk Hegwood, president of Hegwood Electric (http://www.hegwoodelectric.com), the designer and manufacturer of the EcoVend.
The machine is controlled by an AutomationDirect PLC with Modbus I/O. Operator interface is via a Windows CE-embedded touchscreen computer running a custom software program written by Inteworx. The CE computer also runs and executes the Inteworx remote machine management software program.
DHAS Automation Services (http://www.dhasautomation.com) is an OEM and a system integrator that also uses the Inteworx remote machine management solution. Their PLC-controlled skid-mounted pressure-test system conducts either air or hydro tests at pressures to 3,000 psi and is used with products requiring pressure verification such as industrial hoses, pressure vessels, and tanks.
The operator enters the test parameters via a touchscreen and the system automatically fills, pressurizes, and monitors pressure decay. Upon test completion, results are saved to a data table in the PLC. The data collection software on the customer server polls the PLC via an Ethernet link, retrieves the test data, and stores this data on the server in an ASCII format.
An optional system upgrade provides an on-line Internet connection. "The Ethernet module is used for direct connection to the Internet," says Frank Smith, vice president of DHAS. "Data is continuously sent from the PLC to a server-based program that stores the information into an ASCII text file or an ODBC database. Our customers can then use the program of their choice to run reports, analyze test results, and store test data."
Pressure testing is an integral step in the production of metal hoses at American Boa in Cumming, Ga. American Boa uses the DHAS pressure tester to hydro-test metal hoses and hose assemblies and to transfer this test data to the company intranet. "The best feature of the remote data collection system is universal access for all relevant company personnel," says Steve Goley, manufacturing engineer with the hose division of American Boa. "This data is used for viewing, analysis, and record-keeping."
Remote Access in Remote Locations
One of the main advantages of remote machine management is the elimination of costly and time-consuming trips to the machine itself. "Some of our pumps and motors are located 15 miles from the plant site, so it is much more cost-effective to monitor remotely rather than locally," says Adel McNamara, technical working foreman for Sierra Pacific Power (
http://www.sierrapacific.com).Sierra Pacific uses Bently Nevada (http://www.bently.com) hardware and software for remote monitoring. The system monitors vibration and other operating data generated by circulating and well pump motors. Before the remote monitoring system was installed, many of the pump motors were inspected infrequently. "With remote monitoring the system polls the remote sites about once a minute for data," adds McNamara. "Our monitoring schedule before this was a once a month trip to each site." More frequent monitoring yields better operating data, which can be used to more effectively manage machinery.
Another significant advantage of remote monitoring is access to and analysis of data by off-site experts. Tri-State G&T, Craig, Colo., uses a Bently system to monitor speed, radial vibration, thrust, differential expansion, and shell expansion on a 411 MW GE turbine. "We have used remote diagnostics twice on vibration problems," says Gary Crisp, senior mechanical engineer with Tri-State. "It saves time and money because the field rep does not have to be on-site. It also allows several Bently personnel to review the problem at the same time, and this gets us better responses back sooner."
Figure 2: Pickin' Up Bad Vibrations
A stress-wave analysis system digitally detects ultrasonic signal signatures in rotating machinery, and sends them to modem-connected locations for analysis. (Source: Swantech)
It is impractical to equip every machine in the factory with sophisticated preventive maintenance software, but remote machine management allows multiple machines to be monitored by one central maintenance system. "All machine data is monitored continuously by the control room operators, and is also monitored in more detail approximately once per week by our predictive maintenance group," adds Crisp.
One hurdle that must be overcome with any remote machine management system is reliable communications. "The original critical-equipment remote-monitoring loop was based entirely on a serial data cable that was physically connected from the central computer and daisy-chained to each equipment line [train]," says Barry Myers, rotating equipment reliability engineer with Valero Energy (http://www.valero.com). Myers is stationed at Valero's refinery in Paulsboro, N.J., and the critical equipment trains at this facility are up to a half-mile away from the remote monitoring system PC.
Valero uses a Bently Nevada system to collect and analyze data from rotating machinery. Because the refiner's communication system was daisy-chained from one equipment train to the next, trouble in one area caused the entire loop to be lost. Valero also found the system was susceptible to lightning strikes. "As each train's equipment is upgraded to current standards, the remote monitoring system is removed from the serial loop and connected back to the central computer via fiberoptics," explains Myers. "This has proved to be a very reliable solution."
Remote machine management can allow machine operating parameters to be monitored more effectively. Once the remote monitoring system is in place, it can also be used to add other functions including supply chain management, job costing, and inventory control.
Air Products and Chemicals (http://www.apci.com) is headquartered in Pennsylvania but has plants and facilities all over the world. Many of these are unmanned, so remote machine monitoring is a necessity for reliable plant operation. Air Products uses a SWANview Stress Wave Analysis system from Swantech (http://www.swantech.com) to remotely monitor blowers at these unmanned locations. Stress-wave analysis is a digital means of detecting and analyzing ultrasonic sound that travels in a rotating machine structure.
Conventional vibration monitoring technologies were not feasible for this application due to operating conditions. "These blowers are subject to a lot of shaking forces caused by gas pulsations," says Fred Flemming, engineering associate-machinery with Air Products in Allentown, Pa. "Conventional casing-mounted accelerometers could not discriminate between vibration related to the internal health of the blower and the noise."
Data from the stress-wave analysis system is housed in a local PC at each site (Figure 2). Flemming accesses this data every month via a modem and PCAnywhere software. A recent check at a remote site showed a significant change in the stress wave signature for a blower. Flemming analyzed the data and worked with a local technician dispatched to the site. They determined that the wrong oil had been added to the blower during a recent service. The oil was changed, the stress-wave signature returned to normal, and the blower bearings were saved from premature failure.
Sidebar:
RMM Makes LTSAs Profitable For Industrial OEMs
Many machine builders see remote machine management (RMM) as an integral part of the long-term service agreements (LTSAs) offered to their clients. Most of these agreements are structured so that the machine owner pays a flat fee for a fixed number of years. The OEM is responsible for all repairs, spare parts, and maintenance. Most OEMs also guarantee reliability, availability, and efficiency levels.
OEMs see these long-term service agreements as a profit center, but in most cases these profits can only be realized with remote machine management. RMM can greatly reduce the cost of machine maintenance for an OEM by eliminating site visits, allowing maintenance to be performed on a predictive, as-needed basis, and reducing downtime.
OEM customers like them because the agreements closely align their goals with those of the OEM. "When the OEM executes a long-term service agreement with a client, it's in his best interest to have the machine operate reliably and efficiently," says Steve Sabin, the marketing communications manager at Bently Nevada. "The OEMs begin to make decisions just like a machine owner because now repair, maintenance, and downtime costs come out of the OEM's pocket."
The proliferation of long-term service agreements is driving OEMs to provide remote machine management with their products. "Not surprisingly, OEMs have taken a sudden interest in remote condition monitoring so they can better manage their costs of fulfilling their long term service agreements," adds Sabin.
One point of contention between OEMs and machine owners concerns access to the data gathered by remote machine monitoring systems. Some OEMs consider this data to be their proprietary property. They see it as a key tool for not only reducing service costs, but also for improving machine design. Not surprisingly, many customers want access to remote machine management data because they feel that this data can help them to operate and maintain their machinery more efficiently.
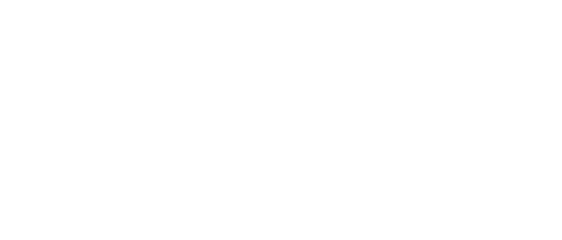
Leaders relevant to this article: