The past decade has seen an ever-increasing adaptation of the PC in manufacturing, as OEMs and manufacturers incorporate what were once standalone machines into an overall plant process,and why not? Exponential advances in performance, software, and networking capabilities have made PCs an attractive choice over the basic PLC and operator panel normally found at the machine level.
More and more engineers, technicians, and machine operators are gaining familiarity and comfort with PC technology, while new generations of manufacturing execution systems (MES) software and industrial communication networks allow businesses to get the most cost-effective use of their equipment. However, the basic PC hardware platform doesn't always stand up to the daily rigors of machine control,the key culprit being excessive heat generated by the rotating media in hardrives.
But with the advent of embedded operating systems such as Microsoft Windows CE and NT Embedded, a new class of equipment is emerging that provides PC-like performance in an industrially hardened operator panel. The multifunctional platform solutions available today combine the ruggedness of dedicated hardware solutions with much of the flexibility of a PC. They define a new, innovative product category, providing a bridge between classic components such as operator panels and PLCs on the one hand and PCs on the other. Machine reliability and performance that didn't seem possible in a PC for years to come.
Protecting the Mold
In more than 27 years of designing and installing custom control systems for various industrial machines, Industrial Control Services Inc. (ICS), has seen the progressive change from highly proprietary, custom-built control products to open architectures based on standardized hardware and software. The company specializes in retrofitting expandable polystyrene (EPS) foam molding (Figure 1), plastics injection molding, and casting equipment with its EXpress Service, and is also an OEM of the Spirit Series foam molding machinery.
Figure 1: PCs Find Lost Foam
ICS began integrating PCs in its lost-foam molding press retrofit systems following the lead of customers that wanted the benefits of a PC.
Industrial Control Services designs controls to speed production, improve process, and protect expensive molds. As any manufacturer in this business will tell you, communication bottlenecks or other disruptions in the sequence of activating interlocking core pulls can result in bushel-baskets-full of scrap aluminum.
The company began integrating PCs in its Lost Foam molding press retrofit systems following the lead of customers that wanted the benefits of a PC. This modular system is applicable to most molding applications that require digital, analog, and motion control, with 64 digital I/O, eight analog I/O points for thermocouples and RTDs, and a 24 V power supply (Figure 2).
A PLC still provides the logic engine in each cabinet, and it remains an attractive choice today because of lower costs and easier maintenance. PCs have been primarily used as operator panels, or human machine interfaces (HMI), for recipe handling and interface with plant-wide Ethernet communications networks.
In order to create a real-time control device, PC manufacturers integrated much faster processors and larger hardrives into their designs. But with the increased performance came more heat, causing the rotating media of hard drives to fail on a regular basis. Heat also makes backlit display screens susceptible to damage. Add vibration and moisture commonly found on a shop floor to the heat factor and you have an environment that makes a PC difficult to sustain.
The best performing hard drive in our experience,and ICS tried them all,lasted only two years. That isn't tolerable. Failures became so frequent that, at one point, ICS had real doubts about the viability of PC-based control.
The Heat's Off
The introduction of dedicated hardware running on an embedded platform opened up a new world for ICS. Windows CE makes systems behave in a deterministic manner, which is a precondition for application safety.
Basically, the Windows CE operating system is an abbreviated, device-specific version of Windows based on a subset of the Microsoft Win32 application programming interface (API). In contrast to Windows 95 or NT loaded on a PC, Windows CE offers instant-on functionality and does not require a hard disk to operate, instead using solid-state flash memory cards. Heat build-up is no longer an issue.
Figure 2: Nicely Integrated
Modular systems are applicable to most molding applications that require digital, analog, and motion control, thermocouples and RTDs, and a 24 V power supply. A PLC still provides the logic engine.
Reduced power consumption, as well as lower hardware costs, produces a considerable cost savings. Features such as ActiveX, Visual Basic, Internet Explorer, Excel, and word packet applications included with Windows CE gave us flexibility and openness.
There was a lot of initial promise, as well as reservation with the first version of a Windows CE-based Multi-Panel (MP) we tried from Siemens E&A (http://www.sea.siemens.com). Function and durability were excellent, but screen update times were slow. When a customer looks at a control display, he wants to see the timer count down or an encoder move at appropriate intervals that are in concert with machine operation.
A subsequent model was equipped with a faster processor and Windows CE 3.0, which provided the necessary real-time control functionality. Processing speed is especially important as more analog values are being controlled.
Programming is accomplished using the same configuration software as all other Siemens operator panels. The MPs communicate with PLCs in the same manner, and when used with Siemens PLCs, they share the same tag database, making programming errors less likely, and changes much simpler. Overall, the CE panels have a common look, feel, and operability to their PC siblings.
The Windows CE operating system allows a multifunction platform to perform numerous additional tasks that put it closer to a PC in its HMI capabilities. MPs can be placed on an Ethernet LAN (wired or wireless) to save PLC data to a shared network drive, or they can save data to removable memory cards. They can also print via TCP/IP to network printers, and can even upload and download recipes over the LAN.
At the most basic level, the MPs can provide much better graphical representations of processes because they have screen capabilities similar to those of PCs; in this case a 12-in., 800x600 SVGA TFT color screen (Figure 3). The MP display was intentionally limited to 256 colors to reduce demands on the CPU. Graphics, photographs and AutoCAD drawings can be imported into panel configurations via object linking & embedding (OLE), just as they can on a PC.
The Future Is Embedded
An even better solution for machine control lies in a dedicated operator panel running on NT Embedded. In our estimation, this should be the next upgrade to the MP family.
NT Embedded provides added security and an expanded Visual Basic (VB) scripting capability--once the domain of the PC. This is significant, in that VB can be used to develop HMI software, allowing users to sidestep packaged HMI products that require licenses each time they're loaded onto a operator panel or PC. Given that individual licenses can range $200-3,000, the savings can be substantial.
VB scripts can be used to offload the PLC from doing tasks not particularly suited for it, such as high-level mathematical and comparative functions. These can now be handled to some degree within the HMI panel, but real VB capability won't be possible until the NT Embedded version becomes available to us.
Figure 3: Good Graphics
The multiplatform units have screen capabilities similar to those of PCs--in this case a 12-in., 800x600 SVGA TFT color screen intentionally limited to 256 colors to reduce demands on the CPU.
Better still will be the introduction of a dedicated panel with an NT Embedded operating system running a software-based controller.
A move from the traditional PC/PLC configuration to a pure PC-based control system will produce major increases in processing speed. Until now, ICS has been limited largely to 19.2 KBaud connections, which is like passing data through a funnel. Much faster speed is possible when laying a controller on the same PC backplane.
Faster speed is a substantial benefit for foam-molding machinery, especially when migrating from hydraulic to all-electric designs. Speed is essential with the higher level of sophistication in motion control as you add more resolvers and encoders for positioning. And as ICS moves PC-based control into injection-molding machines, benefits will result. There are a lot more servo valves for hydraulics, as well as proportional valves, that need to be updated quickly and held at the proper set-points.
Yet, despite the inevitability of PC-based control, and as much as customers want PC functionality in their machines, there is still plenty of concern about pure PC-based control. Concerns lie mainly on reliability and maintenance issues.
For us, Siemens reduced a lot of uncertainties in PC-based control with software. WinAC is a software product that can be programmed and operated with the same package as its own line of PLCs, so you get the same look and feel of a PLC without the added hardware. Programs already developed for an S7 PLC can be transferred directly to WinAC.
ICS anticipates a strong demand for WinAC running on an MP 370, seeing this combination as the future in its machine control initiatives. End users will appreciate the added performance of backplane speed interfaced directly to remote I/O. Machine builders will like the reduced hardware and simplified installation.
These developments will give machine builders and their customers a lot to smile about in the future. Embedded platforms provide a very cost-effective way to increase system performance and reduce complexity. Some very high-end process automation and SCADA systems have been implemented with embedded systems and dedicated hardware, but functional, affordable solutions for machine control are here or will soon be available.
Jeff Birch is president of Industrial Control Services Inc. based in Centralia, Mo. He can reached at [email protected].
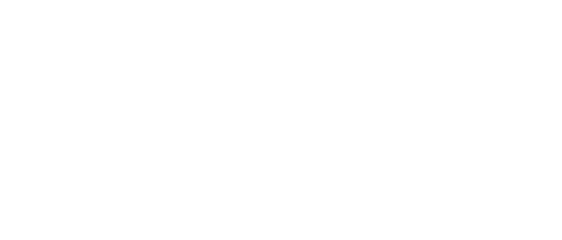
Leaders relevant to this article: