Most machine builders think about performance, cost, and support issues when they design new-generation equipment and systems. Some of them think about modularity and flexibility, since they have customers that need to rapidly reconfigure the assembly, both mechanically and electronically, for a variety of product requirements.
But few have to think about designing a modular assembly of equipment and controls that may have to be disassembled, moved miles away, and reassembled in about 36 hours.
One industrial OEM that manufactures turnkey automated systems to produce hot-mix asphalt does precisely that.
Paved With More Than Just Good Intentions
An ambitious state and federal program to repave interstate roads in Arkansas is keeping a recently built, modular, movable asphalt hot-mix plant (Figure 1) operating 24/7 over two shifts to serve paving crews in a roughly 100-mile radius.
As the demand for road repair continues to stretch beyond the horizon and allowable project-completion time shrinks, the speed and ease of installation of a site's hot-mix plant becomes essential. Modular, turnkey, ready-to-go systems, some of which are designed to be taken down, moved, and re-assembled are a big part of the answer.
Figure 1: Bolt It Together and Plug It In
Modular, turnkey, and ready-to-go, these asphalt systems are designed to be taken down, moved miles away, and reassembled in two or three days. (Source: Astec)
A subsidiary of Ashland Inc., the Arkhola Div. of APAC-Arkansas Inc. in Ft. Smith, Ark., is part of a highway construction and materials-supply organization that operates in 14 southern states, serving communities from Virginia to Kansas and from Florida to Texas. Explosive population growth in the region over the past decade created a need to maintain existing roads and build new ones to keep up with development and to attract industry.
The portable, skid-mounted asphalt plant manufactured by Astec Industries (www.astecinc.com), Chattanooga, Tenn., and operated by Arkhola is a modular system, designed for quick installation and wiring, with minimal site preparation for components ranging from mixing drums to storage silos and fuel tanks to a baghouse. The modularity of the system makes it easy to install a plant in a relatively short period of time and at a lower expense.
First of Its Kind
A completely integrated asphalt plant, the Arkhola facility sits just south of Fort Smith in the Ozarks, hugging the Oklahoma border. There, feeder bins contain the raw aggregate--mainly sandstone--brought in from an on-site quarry. A conveyor deposits various aggregate material (depending on the recipe) where it is superheated and then sent to the mixing drum with liquid asphalt at 340º F. Liquid asphalt is a mixture of below-diesel-grade petroleum and polymers.
The Arkhola plant was the first opportunity for Astec to use its new TC-2000 PC-based control system, designed around a flexible hardware architecture that could not only control an entire facility, but minimize wiring and other complexities for easy set-up or dismantling.
Operating on a Windows NT platform, the TC-2000 controls and monitors all plant functions from a standard PC. This includes blending operations, plant motors, motor currents, mix and plant temperatures, material inventory, silo levels, energy usage, and alarm status. Distributed I/O over an industrial communications network vastly reduces wiring, making the system easy to install or disassemble.
Rethink the Controls
Astec began to rethink its control strategy in the mid-1990s as major automation vendors began introducing software derivatives of programmable logic controller (PLC) functionality. The company had built its own custom embedded systems based on relay ladder logic programming since the 1970s and realized it was time to decide what the future generation of asphalt control systems would look and feel like.
Astec management decided it made sense to look for a solution from one of the major control vendors, considering the additional system capabilities demanded by customers coupled with strains on its own development resources.
"It takes a lot of engineering staff resources to design custom products such as CPUs and I/O boards," says engineering manager Mark Harned. "Plus the customer wanted more than blending control. It wanted centralized control for all the functionality of a hot-mix facility--heating up the aggregate, taking moisture off, recipe management, conveying, silo storage, and point of sale systems."
While contemplating an off-the-shelf answer, Harned and his team considered what type of product Astec could--and should--offer. Was it good to go a "stereo-component" approach and offer different pieces at different times? Or should they offer a control package for the entire process that would include all of the sequences?
Figure 2: Center of the Hot-Mix Universe
The key day-to-day metrics--mixing temperatures, asphalt content, amount of aggregate in the bins, motor performance, and individual recipes--are monitored and controlled from the prefabricated main control house.
Since processing power in PCs had advanced to the point where major deficiencies in scan time were disappearing, and a number of companies were beginning to offer total control packages at competitive prices, the company decided to look for a PC-based solution.
These developments made the direction of Astec's development program more clear. "We looked for the company that would give us the most bang for the buck and had the best configuration and programming tools," said Harned. "Siemens E&A was the only supplier we found that was willing to stand behind its product." The TC-2000 system is built on Siemens' Simatic WinAC controller software.
The Pre-Fab Nerve Center
Nearly all manufacturing at the Arkhola facility is handled automatically. The only exception occurs once a mixture is purged, then the operator decides when to start a new batch. APAC-Arkansas initially used the system's interlocks, but experience showed things ran more smoothly when an operator intervened at the start of a new batch.
The TC-2000 system is essentially a continuous batch control system that allows operators to monitor and control the entire plant from the prefabricated main control house (Figure 2). The key day-to-day metrics are mixing temperatures, asphalt content, amount of aggregate in the bins, motor performance, and individual recipes.
Astec's control house is the nerve center for the entire asphalt plant. All controls are factory installed and fully tested prior to delivery. Below the main operator deck at APAC Arkhola are the motor control centers, all integrated into the TC-2000 through Siemens SimoCode software, which allows the operator to see the numbers of starts, trips, trip current, hours of operation, and other diagnostic functions. It controls a separate PLC that can run with or without a supervisory controller.
Wiring has been minimized through extensive use of Profibus-enabled devices and compatible instrumentation in a distributed I/O topology (Figure 3). Individual wires that would connect each device have been replaced by a single cable.
The idea behind the TC-2000 was to give users an integrated distributed control system that would minimize the wiring and provide better troubleshooting and diagnostics. Astec also believed it was important to build a product that would protect the customer's investment. "We didn't want to leave ourselves short and have to develop the project again after a year or two," says Harned. "The products we now offer are based on relatively open standards for greater flexibility."
Astec says PCs and Windows have brought performance to a level of nearly deterministic operation suitable for a number of control applications, since processor speed is now in the gigahertz range; only a few years ago, it topped out at a tenth of that. There is also far more memory at a user's disposal, notes Harned.
For the Arkhola project, Astec used a standard Dell PC with dual 1.2 GHz processors in one enclosure. The processors are configured to mirror one another, providing a backup. If the master has a problem, there is no hot-swap function, but the other PC can become the master in a few minutes. "It's a pretty cheap way to get backup, as opposed to getting two PLCs online in a hot-backup mode," says Harned.
Each processor can perform scan cycles in about 40 msec, far faster than the custom electronics of Astec's older system. Scan cycles in a process loop--with changes and updates--happen in one or two seconds, which is more than adequate in a hot-mix application.
PCs Flex Muscles
To Astec's thinking, adherence to Microsoft standards also makes gathering data simple. The controller's human machine interface (HMI) includes an Active X interface acting as an online data collection platform. The HMI in this case is a Simatic WinCC software package. APAC can instantly transfer data to an Excel spreadsheet from the WinAC engine without any intermediate CPUs.
As for development tools, Harned says Siemens was ahead of other vendors, having tools that included the key IEC 61131-3 programming languages: ladder, function block diagram, graph, and S7-SCL (the last being Siemens' version of structured text). The IEC standard helped Astec structure programs to increase reusability, reduce errors, and increase programming and user efficiency.
"Certain programming languages have their individual strengths," says Harned. "Ladder is great for interlocking motors and other equipment. Graph is great for sequencing and staring up or shutting down equipment, and the pascal-like SCL is good for doing flow calculations and totalizing numbers in the PLC."
The individual programs are all assembled into one automation project with the Step 7 configuration toolkit of WinAC.
Harned believes the 2000 has accomplished Astec's overall goals in developing a cost-effective, integrated control architecture for current and future customers needing the flexibility required when building roads.
"We don't have it down to a science yet, but we're making the system more configurable and more generic from the operator's perspective, without having to do additional programming," he says. "We found that we had jumped from being in a cave to having a leading-edge control system in one fell swoop."
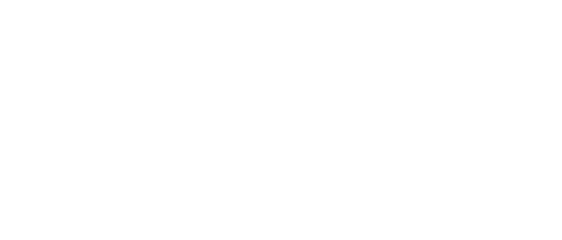
Leaders relevant to this article: