Many months ago, as yachting teams began to prepare for the prestigious America's Cup competitions, an unusual alliance of sailors and engineers began sharing carefully guarded design secrets with trusted manufacturing partners such as Southern Spars Group.
Southern produces booms and masts, often referred to as spars, for some of the world's fastest yachts, including several syndicates that vied to challenge Team New Zealand for possession of the coveted America's Cup this month.
Based on the collective talents of this mast maker, a system integrator, and a machine builder, a new, specially designed autoclave emerged to build masts that would stand up to the performance requirements and stresses of racing at the highest level of competition.
The Carbon Composite Advantage
Carbon composite spars are stronger and lighter than their alloy predecessors. In yacht racing, the stronger and lighter the spar, the faster and more competitive the yacht. Wooden or metal masts would work, but they would be much heavier and larger in section. The new composite masts are lighter and stiffer and so, pound for pound, stronger.
In the case of the America's Cup Class, there are rules that limit the weight of the mast, but in general terms the stiffest, smallest, and lightest would be the best.
Figure 1: Tall Manufacturing Task
Mast and boom strength is important. There is a compression force of about 120,000 lbs. at the bottom of an America's Cup boat mast.
The length of the spars, which can measure more than 150 ft., is only part of the production challenge. Masts have tapered shapes and are manufactured from two long shells joined to make one piece. To maximize strength, the manufacturer must ensure absolute uniformity from the wider and thicker base to the narrower and thinner tip.
Strength is important. There is a compression force of about 120,000 lbs. at the bottom of an America's Cup mast (Figure 1). "When we go to schools and talk to students about it, we compare it to about 25 Chevy Suburbans sitting on the top of the mast," said Scott Vogel, a designer/engineer for Southern Spars.
Custom-designed autoclaves are critical to the manufacturing of the masts, and the Southern Spars Group was the first to have extra long autoclaves built for its use to improve uniformity in carbon fiber spars.
Gilbert Engineering, a general engineering/machining business that specializes in pressure vessel handling equipment, in Auckland, New Zealand, partnered with Southern Spars to build a custom autoclave.
The autoclave is 160 ft. long and 5 ft. in diameter (Figure 2). It is internally lagged with a mechanical load in/load out system that is electronically heated.
Figure 2: It's Long. Any Questions?
Southern Spar GM Claude Cognian and his company's 150 ft. autoclave.
Although Gilbert Engineering usually builds turnkey systems, this autoclave was specifically built in New Zealand for Southern Spars. "The autoclave we designed was a three-stage system that required varied interior temperatures over an extended period of time," says Ron Gilbert, managing director of Gilbert Engineering. "Because the shape of the mast is not uniform, one section might require a higher heat than another."
Racing strategy begins with equipment design, so the ability to control the composite material cure process gives a competitive edge that Southern Spars can pass on to the racing teams.
The Cure Is Never Easy
It takes both extensive knowledge of composites and a high skill level to produce quality carbon fiber spars. Carbon fiber spars are manufactured from multiple layers of carbon fiber and resin placed in a mold. The orientation of these layers combined with the type of fibers and resin system used produces rigs of varying shapes, stiffness, and strengths.
"The curing process can be difficult to control," explains Vogel, "in part because of the variety of resin chemistries used and the substantial variations in thickness required to generate optimum performance in any given spar."
Quality relies heavily on the fabricator's ability to prevent air pockets from forming in the laminate and to remove any pockets that do form before the resin is cured. This prevents weak spots. Two processes are used to remove these air pockets: vacuum bag molding and autoclave molding. Having previously considered competing technologies, Southern Spars this time saw an opportunity to improve quality by applying both methods.
In vacuum bag molding, the laminate is covered with a thin polymer release film, a porous bleeder fabric, and a polymer membrane bag. The bag is sealed to the mold around the edges of the part, and a vacuum is applied between the bag and the lay-up.
The vacuum can greatly reduce trapped gas, but does not necessarily eliminate it all. So, at Southern, operators use autoclaves to further process the vacuumed-bagged spars.
With the heat and pressure capabilities of a tightly controlled autoclave, the company applies its expertise in composites to create an environment capable of removing any remaining gas pockets while curing the resin. As the autoclave heats, the resin alters to a liquid state, allowing any remaining voids to be eliminated by pressure condensation and/or molecular diffusion into the liquid resin. This produces a tightly compacted, void-free laminate.
Defining the Cure
To develop the techniques that now set the industry standard for autoclave-cured masts, Southern Spars and Gilbert Engineering needed another partner onboard. "Instead of choosing one curing technique over the other, we recognized that we could set a new standard of quality by using both vacuum bagging and autoclave molding," says Vogel. "At the same time, we wanted to make it easier to achieve the level of perfection we need."
The search for an automation partner that could develop a straightforward system capable of the needed accuracy and precision turned up Applied Industrial Controls (AIC) of Reno, Nev. The combination of Southern, Gilbert Engineering, and AIC provided all the tools needed for a successful design and manufacturing plan.
Southern engineers worked with Gilbert and AIC to design a system sophisticated enough to control all essential process parameters, yet simple enough to keep the process running through the night when only operators are on duty. And, with the America's Cup approaching, they needed the new system working for them quickly.
In addition to the expected requirements for precise temperature and pressure control, Southern needed the ability to stop and hold a setpoint program segment during an exothermic reaction. "The ability to detect and control an exotherm in a locally thick section prevents excessive temperature peaks," explains AIC sales engineer Mike Howard. "This is critical because the peaks can damage the composite or result in variations in the finished parts."
Curing Complexity With Control
Howard worked with Gilbert and AIC Application Engineer Jake Derner to develop specifications and design for the new autoclaves and the system controls. Derner says they chose a Honeywell UMC800 Universal Multiloop Controller because it offers a number of advantages over traditional control systems.
"First, it has the level of sophistication needed to maintain uniformity despite the sometimes troubling properties of resin," says Derner. "But it still presents operators with a straightforward interface that minimizes training and troubleshooting."
Gilbert was initially hesitant about using the controller. "Since we were building it in New Zealand," says Gilbert, "I thought that we could find a comparable system here that would not be as expensive, given the rate of currency exchange between the United States and New Zealand."
Figure 3: Integrated Software Aids Control
The controller (above and below) made commissioning much faster by offering the automation team a single software package for process control, logic control, and operator functions.
Gilbert didn't hesitate for very long. "I saw that the UMC800 was able to record up to 18 different points within the mast as well as the overall temperature in the autoclave," he says. "And it could also monitor and record pressure and temperature across a range of 120° C. I was impressed. That was pretty unusual." The controller is comprised of a CPU with I/O, operator interface, and programming software all bundled together.
"We knew the controller would meet the process control and information needs," says Howard. "But we had our own concerns about getting the system up and running fast enough for Southern Spars to start applying the technology in time for the America's Cup designs."
By offering the automation team a single software package for process control, logic control, and operator functions, the Honeywell controller made commissioning much faster (Figure 3).
"It's a system that's really easy to use," says Derner. "Since we didn't have several different, unfamiliar software packages to learn, we cut the time it normally takes to implement a complete system almost in half."
The final design lets operators monitor and adjust all the diagnostic alarms linked to analog process values as well as safety switches inside the autoclaves. "Everything operators need to know and do can be learned and accomplished from a single interface panel on the machine," says Derner.
The design team was pleased, and more importantly, the customer was impressed. "I was especially impressed with the flexibility of the control system," says Kurt Andress, Southern's composite material and process engineer. "It allowed us to create all the logic necessary to achieve the required process control, have the system diagnose itself, and report all problems to the operator.
"The system can automatically respond to a variety of equipment failures, such as a thermocouple, and safely continue without loss of process control," says Andress. "In the past, we might find ourselves committed to a cure that was going to result in waste. The new system gives us visibility over the entire process, and we can easily access the program to adjust pressure and temperature as needed."
Today, Southern is doing many things that could not be done as readily or reliably without this equipment and its level of control sophistication. "Operation is largely just responding to system alarms, if and when they occur,"
The result is smoother sailing for Southern Spars operators. "There are cost and time savings to be sure," concludes Vogel, "but what's most exciting for us is that when we take the lead with innovative technology, we get to see our quality improvements giving teams an edge in the most prestigious and exciting yacht races in the world."
Claude Cognian is general manager for Southern Spar's facility in Minden, Nev.
Sidebar:
Autoclave Curing System
Process:
Pressure and heat cure of advanced composite materials.
System Description:
* Pressure vessel fill, vent, and dump valves
* Three electric heater banks
* Two gas-circulation fans
* Vacuum pump with isolation and shutoff valves
* Pneumatic control valves throughout
Size:
5 ft. diameter x 158 ft. length
Controller:
Honeywell UMC800 Universal Multiloop Controller
I/O points:
* 22 analog inputs monitor process temperature, pressure, and vacuum. Capacity to simultaneously monitor two separate mold/part temperature profiles for guaranteed temperature achievement and over-temperature control. Automatically detects pressure and vacuum system leaks.
* 22 digital inputs monitor system component status and safety interlocks. Automatically detect all system component malfunctions.
* 1 analog output enables fine temperature control.
* 18 digital outputs handle remaining system controls.
Sidebar:
About the America's Cup
The 2003 America's Cup is a best-of-nine (first to win five) match between the Defender, Team New Zealand, and the Challenger, Team Alinghi from Switzerland. Racing was to begin Feb. 15.
The Challenger was determined in a four-month elimination series known as the Louis Vuitton Cup, which began Oct. 1, 2002. Challengers included nine teams from France, Switzerland, Italy, Great Britain, Sweden, and the U.S.
The Vuitton Cup final concluded late in January, with Team Alinghi defeating U.S. Team Oracle BMW.
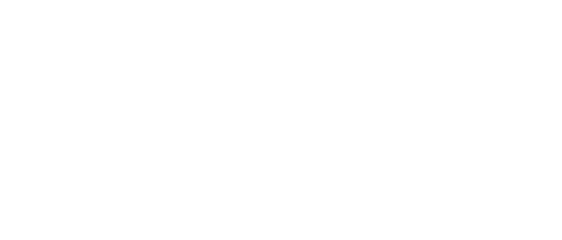
Leaders relevant to this article: