A Reader Writes:
We provide our food processing machinery with operator interface (OI) units that won't withstand washdowns at our customers' plants. The current method of bagging them during washdown won't satisfy the FDA's Hazard Analysis and Critical Control Points (HACCP) requirements. Before we talk with the suppliers about changing the OI, we'd like to know what others are doing to provide operator interfaces in washdown areas that meet HACCP?
--from October/November Control Design
Answers
Go Thin, Stay Cleaner
Washdown for food processing operations is one of the areas where we often see customers going to a thin-client solution. While this means a change in the OI hardware, it is much less expensive to find industrial thin clients that are washdown-capable than to find a PC with the same capability, because many of the industrial thin clients are low voltage (some as low as 5 VDC) and require no external ventilation for cooling. Because thin clients take advantage of Microsoft's Terminal Server operating systems they will run the exact same software that the customer is currently running. But because they are thin clients (Windows "terminals") they can be powered down at any time (if desired) for washdown without even affecting the operation of the program, which would continue to run on the server.
David Hancock, Vice President, Marketing
Automation Control Products, Atlanta
Designed for Nasty Stuff
We manufacture a set of terminals that were originally designed for food processing and other washdown/clean environments and have since found uses in many factory and processing settings. They all have different processing and expandability characteristics to meet a wide range of needs. They all look similar to the photo--silicone NEMA-4 spray-down case, full keyboard, and resistance to common spray-down chemicals such as cleaners containing lye and mild acids. The terminals are mounted into a bulkhead or case (ours or custom-fabricated ones) to protect the electronics, leaving the face exposed for operation of the keyboard and easy viewing of the display. The display faceplate has a molded-in, double-ridged seal for sure sealing in the case/bulkhead.
...The photo is not contrived. It is an old photo from a customer's beef processing plant, as you may be able to tell, taken probably 15 or 20 years ago. We still produce this terminal, which our OEM customers love. The case has been so popular that we used it for the other three models over the years as we added more capabilities and progressed with electronic and computer technologies.
...While your reader asked about solutions that people have found that don't include changing the OI, we specialize in open architecture standards that, in most cases, make the changeover easy and usually there is one or more of the terminals that can be retrofitted into existing applications with little modification to the existing machine.
Paul Liska, Product Manager
Intelligent Instrumentation Inc., Tucson, Ariz.
Get Real
Plastic bags on indicators. Welcome to the world of enclosure ratings that are out of step with today's sanitation practices.
...A review of available indicators in the market will uncover the fact that Type 4x construction (formerly known as NEMA 4x), or IP65/IP66 are the prevailing standards to which most indicators are designed and manufactured. You will find the majority are stainless steel enclosures with gasketing around all openings into the enclosure. Unfortunately, adding a gasket may allow the indicator to be rated 4X/IP65/IP66, but it might not prevent water from entering the enclosure.
...The IP65 standard requires protection against low-pressure jets (30 kilopascals, equivalent to about 4.35 psi) of water. The IP66 standard requires protection against high-pressure jets of water (100 kPa or 14.5 psi). It further defines the distance to be 2.5-3 m and the water temperature to be within 50 C of the enclosure's ambient temperature. As a point of reference, the water pressure entering a typical home in the USA is about 300 kPa.
...Here are the disconnects: The average ambient temperature of an enclosure in a poultry processing plant is somewhere around 50° F when in use and possibly around 70° F when the refrigeration is turned off in preparation for cleaning. The water temperature used for cleaning the enclosure is routinely above 120° F and the water pressure can easily approach or exceed 7,000 kPa [1,000 psi].
...That is why an enclosure can fill with water when cleaned if it minimally meets the 4x standard. The water temperature is far hotter than the enclosure, and the water pressure is far higher than the design standard used for the specified gasketing.
...The solution: Make sure your enclosure is rated IP69k. The IP69k standard provides far superior protection and closely mirrors common equipment cleaning practices employed in meat and poultry processing plants, such as:
* 14-16 l/min. of water
* Sprayed at 8,000-10,000 kPa
* Temperature of ~80° C
* 30 seconds per position from 100-150 mm
...Recently, we too have seen plastic bag-covered terminals, including some of our own. For that reason, we recently switched from designing terminals around IP65 and IP66 standards to using IP69k for terminals intended for use in severe washdown installations.
...As is often the case, the root cause of this problem is misapplication of a product. Unfortunately, there have not been many better terminal choices available on the market. That is slowly changing as manufacturers respond to the requirements of users instead of focusing on traditional enclosure protection standards intended to provide adequate protection in less severe operating environments.
...While plastic bags can provide a temporary solution to water-logged terminals, the ultimate solution is to upgrade them to IP69k rated enclosures.
Frank Cava, Market Manager
Mettler-Toledo, Columbus, Ohio
Here Are the Regs
Bezels on our panels comply with CFR 181.32 for repeated-use food contact and the touchscreen overlay complies with CFR 177.1580 for use in single and repeated-use food contact surfaces. Gaskets are made from ingredients that comply with CFR 177.2600.
Tim Roberts, Operator Interface Product Manager
AutomationDirect, Cumming, Ga.
Design for Harsh Environs
To help customers comply with HACCP requirements, we make a fully sealed control interface guaranteed to stand up to the harsh demands of the food & beverage processing industries. The design of the unit includes a special airtight multisealing procedure to protect the enclosed electronics from chemical cleaning sprays, solvents, water, grease, and other liquids. Yet, the enclosed electronics are exposed to steady air circulation to maintain an optimum, uniform operating temperature to ensure a long life. Built-in heat sinks and redundant, internal forced-air heat-transfer systems are also part of the design.
...We take maximum advantage of the thermal conductivity of stainless steel and ensure that the operating temperature of the internal electronic components are as low as possible. The internal component layout is configured to maximize the internal turbulent airflow so that the convection heat transfer effect is optimized for each component.
Chris McDonald, Director of Marketing
Dolch-Touch Controls, Fallbrook, Calif.
June's Problem:
Configurable or Dedicated OI?
I guess we're way behind the curve here, but we've gotten along with building dedicated operator interfaces for our machines. Lately, the demands of open standards technology are catching up. It looks like we'll be using more configurable Windows-based software, but I'd like to know if any readers have had any buyer's remorse and find that rolling your own, for a panel that just needs a few hard-wired buttons and switches, is still not a terrible idea.
Send us your comments, suggestions, or solutions for these problems. We'll include them in the June 2003 issue. Send visuals, too,a sketch is fine. Have a problem you'd like to pose to the readers? E-mail us at [email protected] or mail to The Answer to Your Problems, CONTROL DESIGN, 555 W. Pierce Rd., Suite 301, Itasca, IL 60143. You can also fax to 630/467-1124. Please include your company, location, and title in the response.
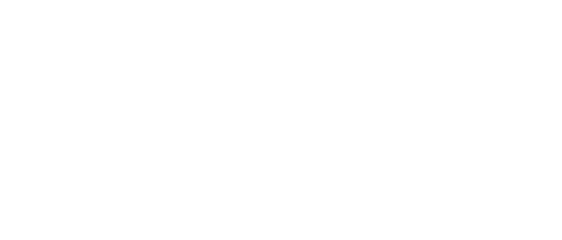
Leaders relevant to this article: