In an effort to improve on these traditional construction methods, many plants are turning to turnkey, automated, skid-mounted systems and modules. Skid-mounted systems offer a host of advantages compared to systems built on-site, and many of these advantages may be germane to your next project.
Keeping Secrets
One of the main reasons a customer may buy a skid-mounted system is to take advantage of a vendor's proprietary and/or patented technology. Many "skid builders" have spent tens, even hundreds, of man-years developing their processes, and they only make these innovations available with their skids.
Mobile Process Technology (MPT,
www.mobileprocess.com) is one of them. MPT's advanced separation technologies (Figure 1) provide waste-stream elimination, resource recovery, and remediation to the chemical, petrochemical, polymer, pharmaceutical, and general manufacturing industries.Figure 1: Delivery & Pick-Up
Mobile Process Technology's separation technologies provide waste-stream elimination, resource recovery, and remediation to many industries. Skid-mounted delivery means MPT can offer advanced, proprietary systems to customers on a leased basis.
"Our clients are often faced with challenges that can only be solved by advanced separation technology," comments Sean Kelly, MPT project manager. "Our systems can save them significant operating expense dollars, improve product quality, improve operations, and improve environmental compliance."
Off-Site Construction Is a Plus
There are numerous advantages for customers if they can have a system constructed off-site. Safety is a huge issue for plant management, and an ideal way to reduce the number of OSHA-recordable incidents is to reduce on-site construction hours.
Skid-mounted systems are one of the best ways to shift construction hours off site. Off-site construction in the controlled environment of a skid-builder facility should be safer than similar work performed at an operating plant.
Labor efficiency is another reason for off-site construction. Operating plants introduce a host of inefficiencies including security gate check-in, compliance with union work rules, work-permit procurement, and coordination with plant operations and other crafts. A craftsman working an eight-hour day at an operating industrial plant would typically spend no more than six hours of productive time at the actual work site.
Not only can off-site craftsman devote more hours to actual work, they are often more efficient because they work on the same types of systems every day. "Skid-builder personnel are extremely efficient because they are always building similar equipment," says Flemming Larsen, automation project manager for Novo Nordisk Engineering (NNE) in Copenhagen. "Skid builders often use an assembly-line approach to manufacturing, which is much faster and less expensive than on-site custom and one-off construction."
NNE designs and builds pharmaceutical plants, and the company uses pre-built skids and modules whenever possible (Figure 2). When skids are used in new construction projects, overall construction time can be greatly reduced. "Buildings and utilities can be constructed while skids are being built instead of waiting until the building is ready for occupancy and then starting construction," adds Larsen. "On a recent project this trimmed the schedule from 32-36 months to 18 months."
Figure 2: Parallel Processing
Novo Nordisk Engineering designs skids and modules in pharmaceutical plant construction whenever possible. A recent project schedule was trimmed from 36 months to 18 months because module-building was done in parallel with the building it would reside in.
Reliance on skid builders also removes on-site interference among different processes and systems. "When construction takes place on-site, it is often necessary to construct separate systems in a more sequential fashion as compared to off-site skidded systems, which can all be built at the same time," adds Larsen.
When processes must be added to existing plants, skid-mounted systems are often the only good answer. Hutchison-Hayes (www.hutch-hayes.com) centrifuge skids (Figure 3) are often purchased for installation on operating oil-production platforms. "The very nature of this business environment dictates that the equipment have an efficient skid-mounted modular design in order to be integrated into the drilling system with as little effort as possible," observes Gary Hensley, executive vice president of Hutchison-Hayes.
One chief disadvantage of off-site construction is coordination among different vendors to ensure commonality of components, methods of construction, and control systems. While it is possible to mandate that all skid builders follow strict and unwavering standards, in practice this can increase costs and lengthen schedules.
According to Larsen, up-front planning with all skid builders is essential to ensure that necessary standards are met while allowing each skid builder to maintain internal efficiency. Inevitably, trade-offs must be made when standards collide with costs and schedule.
One Throat to Choke
Some call it single-source responsibility, others refer to it as having one throat to choke. In any case, clients always know where to turn if a skid doesn't work as designed. This is usually not the case when a company decides to construct a system on-site, unless the construction is awarded to a firm on a complete, engineer-procure-construct design-build basis.
Figure 3: Efficient Deployment Required
Hutchison-Hayes makes skid-mounted centrifuges for deployment in hostile environments, which mandates an efficient modular design in order to be integrated into the drilling rig system with as little effort as possible.
"Skid-mounted systems provide the customer with a single source of responsibility that includes all mechanical and electrical components for the system," says Shawn Harris, engineering manager for Metron (
www.metroninc.com). Metron provides packaged pumping systems to municipal water districts, power plants, and city park departments. "Most customers prefer packaged systems to eliminate many of the integration problems that arise from purchasing components from multiple vendors and attempting to stick-build at the job site," adds Harris.Metron officials say one potential customer elected to take the stick-build approach and later regretted the resulting headaches and finger-pointing among the suppliers.
Plug-and-Play Installation
A skid-mounted system typically arrives at the job site fully tested and ready for operation. On-site installation work is minimized, often to an extreme degree.
Enterprise Automation (
www.enterpriseautomation.biz) is a control system integration firm that works extensively with skid builders. Pacific Consolidated Industries (PCI) (www.pci-intl.com) builds skids that produce industrial gases and is one of Enterprise's main customers."PCI's nitrogen skid is completely self-contained and does not even require utility hookups," says Dave Panish, president of Enterprise Automation. "It generates its own power, electricity, compressed air, and instrument air. Just hook up a high-pressure discharge hose for nitrogen output, perform a three-step start sequence, and you're done. Load demand is simply determined from the client's nitrogen back-pressure and flow."
Other PCI skids require somewhat more in the way of on-site connections, but the principle is the same. Nothing plugs and plays in an industrial environment like a skid-mounted system. "Skid-mounted systems can be installed and commissioned in much less time than a similar system built on-site," adds Panish. "This allows the customer to be up and running much faster and with less of an impact on its facility and production schedule."
Most skid-mounted systems require interface connections to existing plant control and instrumentation systems. Hard-wired connections require precise definition of all upstream and downstream analog and discrete interfaces. Any changes to these hard-wired interfaces can result in significant modifications to standard skid-mounted system interfaces.
Another problem with hard-wired interfaces is the sheer number of wires that often must be run from a skid to an existing plant control system. Digital interfaces alleviate these problems by allowing large amounts of data to be transferred over a single communications cable. These digital interfaces are very flexible and can easily accommodate changes in interface connections.
The PCI skid-mounted systems use PLC-based controls, which allow for many types of integration with existing plant control systems, from simple digital I/O handshakes to more complex communication drivers.
Basic interface methods are digital inputs and outputs such as 120 VAC or 24 VDC, as well as analog I/O signals such as 0-10 VDC and 4-20 mA. More advanced interface methods incorporate digital communication interfaces. "The PCI nitrogen skid uses a PLC controller and can support many different communication protocols including Modbus, DeviceNet, Profibus, DirectNet, and general ASCII serial communications," says Panish. "The PCI control system also has a supervisory PC-based HMI that supports DDE and OPC connections via Ethernet."
PCI also has plans for multiple skid installations that will all be networked via Ethernet for PLC, HMI, and OIT connectivity.
Hutchison-Hayes supplies its centrifuge systems to operating oil rigs, and these systems must be plug-and-play so as not to interfere with existing operations. "The complete system needs only two power drops," reports Hensley. "Communications can be as simple as discrete alarm contacts and local paging. However, the control panels can be equipped with a complete Ethernet-based embedded web server that provides remote control and troubleshooting capabilities."
Eascan Industrial Controls & Automation (
www.eascan.com) recently designed a collator control system with plug-and-play capabilities. "No on-site wiring is needed, only the connecting of the devices with quick connectors that have been prewired and tested, and most of which are molded factory cables," says Phil Bernardin, Eascan control system programmer/designer. "To a large extent, interconnection of the solenoid banks with DeviceNet made this possible."Eascan's customer for the collator system project was Premier Agendas/Peak Automation of Bellingham, Wash. (
www.premieragendas.com), a manufacturer of student day planners. Kyle Treichel is a machine design technician with Premier/Peak Automation and he appreciates the modular design of the collator. "The main control panel can be easily disconnected because all of the interconnecting cables running into the panel have quick-disconnect fittings," says Treichel. "All 11 sections of the machine are also individually interconnected using quick-disconnect fittings."The collator has one main trunk line that runs the length of the machine. All machine sections can be quickly disconnected from the main control panel and also disconnected between each section. "The quick disconnects make for an extremely easy move operation, and reassembly errors are minimized because everything is labeled," adds Treichel.
Skid-Mounted Systems Speed Commissioning
One of the main attractions of skid-mounted systems is expedited control system commissioning and start-up. The very nature of modular construction forces skid-builders to perform many commissioning and start-up tasks prior to machine delivery.
"Determining system operation, I/O requirements, and motion requirements must be done ahead of time," observes Treichel. "This decreases omissions and errors, and allows for complete off-site testing, which ultimately reduces costs and downtime."
There is a definite alignment of interest between skid builders and their clients on off-site skid testing. It is much cheaper for a skid builder to perform testing off-site and to minimize on-site commissioning and start-up efforts. This dovetails with client desires to have delivered systems up and running as soon as possible.
Figure 4: Drop-In Validation
Millipore offers membrane filtration and chromatography systems for purification and separation of pharmaceuticals. In addition to providing compliant control software, Millipore fully tests each system prior to delivery. Each system includes a complete documentation and validation support package.
Despite this convergence of interests, clients know some issues cannot be addressed until a system is running at full production in their facility. "Skid-mounted systems have been a clear advantage for our company and we look forward to using them in the future," says Treichel. "But it is sometimes difficult to find a problem unless the entire system is up and running with operational power and load."
Skid builders are very familiar with their own processes and control systems, and this allows them to commission and start-up systems very quickly and efficiently. My old employer could completely check out a multi-million dollar system in the shop in less than a week. On-site start up also took less than a week.
Regulated Complications
Commissioning and start-up can be especially problematic in regulated industries where control system validation is required. In these cases, it can be especially beneficial to purchase skid-mounted systems with control systems that can be quickly validated on-site.
Millipore Corp. (
www.millipore.com) offers a range of membrane filtration and chromatography systems used for the purification and separation of pharmaceutical drug products (Figure 4). "Our Common Control Platform (CCP) software is used to control our large-scale automated systems," says Tom Dennen, technology manager of automated separation systems for Millipore. "CCP software has been audited by an independent third party and complies with FDA guidelines for 21 CFR Part 11."In addition to providing compliant control software, Millipore fully tests each system prior to delivery. Each system includes a complete documentation and validation support package including Installation Qualification/Operation Qualification test protocols. All documentation complies with the guidelines published by the GAMP Forum, a joint interest group promoting the use of computer and control systems within healthcare industries, and its JETT consortium of pharmaceutical manufacturers, equipment suppliers, and consultants involved with the validation requirements of the pharmaceutical industry.
Digital Networks Turbocharge Startup
Digital networks not only facilitate installation interconnections among skids and between skids and existing plant control systems, they also simplify commissioning. "On a recent project, we used Foundation fieldbus for analog instruments and Profibus-DP for discrete components," reports NNE's Larsen. "We found these networks expedited calibration and set-up of instruments, both at the skid builder's facility and on-site."
Digital networks also make it easy to add devices to a system, and this feature also can expedite commissioning. "On a conveying system project, we were able to easily add inputs and connect them to a nearby module instead of trying to run power and control wiring from the sensor to the main control panel," says Steve Benvenut, senior process engineer with Performance Automation.
Sidebar:
Will It Fit on the Truck?
When it comes to skid-mounted systems, the make/buy decision is often complex for your customers. One issue that could make the decision for them (and you) is whether it's even possible to ship the system to their plant.
Skids that must be transported via truck are limited to a width of 8 1/2 ft. with no permit, 12 ft. with a permit. Shipments wider than 12 ft. require an escorted permit.
As skid widths increase, trucking time and costs also increase. But there is virtually no limit to the size of skids and modules if barges are used for transport. Removal of size limitations can make skids and modules a viable alternative for even very large-scale plant construction projects.
Despite the attractiveness of skids and modules, there are certain types of equipment that should be shipped loose for installation at the site. Often weight is a consideration.
"Very large and heavy items like tanks and heat exchangers are often not practical for skids because the skid steel frame can add 20% or more to the total weight," says Mike Fujita, director of engineering with Wahlco (
www.wahlco.com) in Santa Ana, Calif. Wahlco specializes in the design and manufacturing of flue gas conditioning, NOx control, and ammonia handling equipment.A Baker's Dozen Reasons To Buy a Skid-Mounted System Instead of Assembling On-Site
1 It may be the only way to purchase vendors' proprietary technology.
2 Reduces installation time.
3 Reduces start up time.
4 Skid can be built before the facility is ready for occupancy.
5 Skid can be moved from one location to another.
6 Off-site construction reduces on-site construction hours and on-site OSHA recordable incidents.
7 Multiple units can be built simultaneously with no interference from other unit construction.
8 Off-site labor can put in a full day, on-site labor is hampered by ongoing operations.
9 Off-site "assembly line" operations are cheaper and faster than on-site custom installation.
10 Skids are often more compact than similar systems built on-site.
11 FDA validation often can be done quicker with skid-mounted systems.
12 Skids make equipment rentals viable.
13 The skid builder guarantees system operation.
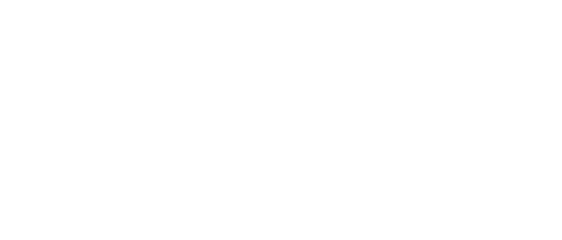
Leaders relevant to this article: