Linear motor technology has been touted as the next killer app for some years now. Industrial machine builders that require precise, reliable linear motion have heard the promise of vast performance improvement over more traditional translated linear motion.
Touted as...? Promise of...? Is that still all there is? As we take another look at the technology, the question is simple: Has linear motor technology broken through to wider acceptance?
Regrettably, the answer remains decidedly mixed. In this article, we detail some of those promising examples of linear motor application, as well as some present-day realities of cost and understanding that have hindered and may continue to hinder widespread use.
Two Years of Experience
It's been two years since a major confectionery customer approached custom machinery manufacturer Tritech Industries (www.tritech-industries.com) with a challenge. The food processor wanted to cut a product at very high speed using ultrasonic cutting technology, but also needed a high-quality cut.
Figure 1: Precise Cuts
This Tritech ultrasonic cutting machine has identical cutting heads controlled by linear motors to engage and retract the cutting heads at precision high speeds.
Rather than using cam or screw-driven motors, Tritech engineers used linear servo motors and off-the-shelf ultrasonic blades and peripherals to design a cutter (Figure 1) that tracks the product at the speed of the conveyor on the x-axis while making a perpendicular slice through the product on the y-axis. The Tritech machine controls acceleration and deceleration in both axes and avoids the elliptical cutting motion of other types of cutters (Figure 2). More importantly, the linear motor machine beats standard system throughput rates (about 150-200 cuts per minute) by a significant margin, according to Tritech.
"We focused on the customer's business drivers," says Rick Tkaczyk, vice president of sales for Elk Grove Village, Ill.-based Tritech. "We were able to provide higher speeds, and [the customer] got higher production rates. With linear servos, they potentially also could have lower maintenance costs because there are fewer moving parts. And by using the linear servo technology, we could change the motion profile in our software package, so the customer could cut variable lengths of product on the fly by changing the recipe."
In the notoriously conservative food industry, linear motor technology is relatively new. The industry as a whole is not known to be an early adopter of new technology, and its low profit margins make companies hesitate to invest in technology with a higher capital cost than "tried-and-true" solutions. But Tkaczyk is seeing growing interest in linear servo-driven ultrasonic cutters throughout the food industry, as well as in the pharmaceutical, electronics, and automotive industries.
"It's not for every cutting application," Tkaczyk concedes. "It's meant for applications where speed, quality, maintenance reduction and higher yield are critical to the operation."
Cutting-Edge Machine Speed
Industrial machine builders who have switched to linear motors on cutting tools, medical devices, packaging pick-and-place machines, and similar high-speed equipment have realized dramatic increases in tool positioning speed and acceleration.
Figure 2: Shift On the Fly
Since the cutting head consists of independent linear motor axes run with a preprogrammed motion controller, the Tritech ultrasonic cutter can switch on the fly among many different product recipes at many different belt speeds.
"Companies that use linear motors are producing machines that are extremely fast," says Paul Webster, servo product manager for GE Fanuc Automation (www.gefanuc.com). "They have switched because rotary motors cannot provide the acceleration and top speed of a linear motor. These are typically light part weight or very small machines. The speed and acceleration can only be realized by keeping the weight down, substantially lower than traditional machines. Also, a linear motor does not require the space of a traditional motor, so the machine can be made smaller."
Speed was a critical factor for a machine builder that used linear motors in its latest laser metal-cutting tools. Alabama Laser Systems (www.alspi.com) and GE Fanuc collaborated on the design and engineering of CO2 laser CNC cutting systems that are used to make high-speed cuts in sheet metal up to one-inch thick (Figure 3).
"We wanted to take high-speed cutting technology into the future and build machines that exceed the current state of the art," notes Sai Mudiam, vice president of engineering for Alabama Laser Technologies, parent company of ALS in Munford, Ala. "We decided linear motors are the technology of the future for the machining industry. With these motors, our machines are able to move faster with higher acceleration rates."
Using 1,500-W and 3,000-W lasers, the ALS systems are capable of cutting 233 holes per minute, with contouring speeds of 1,000 in./min. using linear motor coils and brake and brakeless servomotors. The motors are mounted on both sides of a lightweight gantry arm and can withstand three Gs of acceleration force with no backlash.
Slow Growth for Faster Motors
If you believe the vendors, linear motors are finding slow, steady growth in specialized applications where rapid axis acceleration, repeatability, low maintenance downtime, and accurate programmable motion control top the wish lists of industrial OEMs.
"Industrial equipment manufacturers some time ago made the leap from mechanical or hydraulic control to servos," notes John Mazurkiewicz, product/marketing manager for Baldor Electric Co. (www.baldor.com). "As the needs of industrial equipment builders are being pushed to higher cycle times and better accuracy, the willingness to incorporate new technology is increasing. Thus, this allows linear motors to be accepted more readily."
But several factors continue to limit the technology's widespread acceptance in the marketplace. Greater capital cost to the machine builder (and customer) is perhaps the main factor hindering sales, while design complexity, heat dissipation, and payload limitations also limit expansion of market share.
"The use of linear motors on machine tools seems to increase from year to year," says John Meyer, marketing and communications manager with Siemens Machine Tool Business Unit. "However, I would be cautious to call the growth significant. The OEMS are trying to keep the manufacturing costs down, and the relatively high price of a linear motor solution may be a factor in the slow spread of this technology."
Mike Pitka, product marketing manager with Rockwell Automation's Anorad Corp. (www.anorad.com), sees opportunity for market expansion as linear motor costs drop with time. "The cost of these motors has decreased considerably over the past several years with new materials and manufacturing methods," he says.
But Pitka cautions that the greater level of hardware and software customization required to design machine tools that incorporate linear motors still will limit linear motor sales in some market sectors. "Linear motors are basically a kit," he explains. "You have a magnetic track and motor, but need the right bearings and encoders to make them perform properly. This requires an added skill set that is not necessary with rotary motors."
Start at the Beginning
In many cases, a machine tool needs to be designed from the ground up with linear technology in mind, and not all OEMs can justify the time and expense needed for such major design overhauls. "Chilling a linear motor is much more challenging than blowing air on a regular servo motor," Meyer says. "Developing a machine that is fit to accommodate linear axes requires expertise, and that can be costly."
Figure 3: Fast and Furious Contouring
Using 1,500-W and 3,000-W lasers, ALS systems are capable of cutting 233 holes per minute. At contouring speeds of 1,000 in./min., linear motors and brake and brakeless servomotors control the motion.
A soft machine tool market also has hindered the expansion of the technology. "Linear motors are still having a difficult time breaking into the OEM market," says Phil Hollingsworth, director of engineering with California Linear Devices (www.calinear.com). "It seems to me that right as people were getting interested, the economy went south." With the economy picking up recently, Hollingsworth senses renewed interest from OEM customers.
Hollingsworth agrees that cost may be slowing the adoption of linear motors, but he cautions that their higher sticker prices may mask potential savings in total system costs. "Cost is definitely an issue. However, when a customer compares total system cost, linear servos can actually cost less than other technologies," he says. "When the benefits of the improved performance on throughput and downtime are factored in, linear motor technology can save the end user quite a bit of money."
Positive Market Perceptions
W.A. Whitney Co. (www.wawhitney.com), Rockford, Ill., switched its bridge-style laser cutting machinery to linear motors in 1999 in part to meet a growing market demand for linear technology. The company's construction, agricultural, forming, and fabricating customers have tight accuracy requirements for laser cutting machinery, and they drove the decision to replace ball screws and rotary motors with linear motors from Siemens.
"Customers see an advantage in premium machinery having linear motors," says Jimmy Gay, Whitney project engineer. "There is a perception that if you want a high-quality machine, you want a linear machine." Gay adds that Whitney's customers also are enjoying improved machine longevity and lowered maintenance costs as a result of the transition to linear motors.
Siemens' Meyer notes that linear technology gave the Whitney laser cutting tools higher acceleration and cutting speed, but concedes that holding the line on costs was a major challenge. "The longer the axis travel, the more secondary sections, i.e., magnets, were needed," he says. "The cost of those magnets then becomes a factor."
Tool builders must emphasize the counter-argument, that the additional capital cost of linear motors is more than offset by reduced maintenance costs over the life of the system. In a linear motor, only the linear guides and motor coil are moving wear parts, and maintenance generally is less of an issue for end users.
"Let's say the customer currently is using a ball screw system," explains Fred Zahradnik, linear mechatronics engineering manager for Yaskawa Electric America (www.yaskawa.com), the linear motor supplier to Tritech. "What the customer often sees is the ball screw costs $5,000 and the linear motor costs $5,500. But if you don't have to worry about maintenance as much, the linear motor does pull ahead."
Engineering issues currently give the edge to rotary motors in many applications. Rotary and ball screw motors, with proper maintenance and sizing, can provide long service life with strong performance characteristics that suit the majority of applications just fine.
"Until the limits of rotary motors are reached, the demand for linear motors will not grow quickly," suggests GE Fanuc's Webster. "The technology is widely accepted, just not needed in most cases. Advances in mechanical designs, like cover design, carriage/bed weight, machine stiffness, and tooling must get to a point that demands linear motors before we see the industry converting to this technology in vast numbers. Until that time, synchronous AC servomotors will be the performance standard in motion control."
So, in many segments of industry, the linear motor remains a solution in search of a problem.
Jeff Hoch is a freelance journalist specializing in science, environment, and technology issues. He can be reached at [email protected].
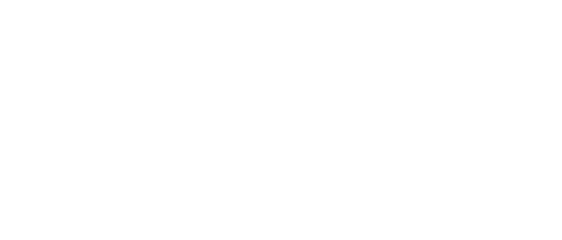
Leaders relevant to this article: