PNEUMATIC AND HYDRAULIC TECHNOLOGY AS PRIMARY disciplines have been part of the machine builder landscape for a very long time. There still are vast armadas of these machines performing admirably in factories all over the world. Now, to many automation gurus, this might seem to be an increasingly old-fashioned approach in a world of electronic servo motors and digital controls, but those solutions are not nearly as antiquated as some might think.
With modern position sensors and closed-loop control methods, servo-pneumatics fulfill more than traditional bang-bang stroke applications, while servo-hydraulic systems can position heavy weights with accuracy and precision. They both have a few drawbacks, but for well-chosen applications the benefits will outweigh the problems.
Heavy-Lifting Hydraulics
Hydraulic-power solutions are great for heavy lifting or where extreme applied pressure is required, such as for powdered-metal press operations. Typically, powdered metal is dropped into a mold, called a die. An upper cylinder pushes a "punch" into the die area and compresses the powder. "Pressures depend on the machine's size, but can range up to 750 tons," says Scott Green, president of Alpha Lehigh Tool and Machine Co. (www.alphalehigh.com), Phillipsburg, N.J. The compact powder particle mass that holds the shape of the die is pushed out of the die and then baked in an oven similar to a ceramics kiln. The metal particles bond at the grain and molecular level,a microscopic welding process known as sintering.
"We refurbish presses to modern standards and use a closed-loop control system to operate proportional valves that control the amount of oil to the upper and lower ram cylinders," says Green. "Magnetic transducers on the upper and lower ram cylinders supply position feedback to the computer. The computer system provides greater flexibility with upper and lower ram movements, and greater flexibility and synchronization with the feeder system,the system that moves the powder into the mold or die."
With these servo-hydraulics, says Delta Computers CEO, Steve Nylund, the system can position down to the resolution of the transducer,in the micron range,and do it accurately and repeatedly. "You can apply huge amounts of force, and do it more safely than with pneumatics," he says. "Hydraulic actuators are smaller than their electrical servo cousins, and are a real benefit when a machine builder has a limited amount of space, but needs to apply large forces accurately."
There are transducers that are well-suited to hydraulic applications. For example, magnetostrictive transducers can be inserted into a hydraulic cylinder,the combination making an excellent actuator-feedback system. But industry professionals say there are special control considerations for hydraulic systems. Hydraulic cylinders typically are built as single-end devices. The forces on the rod side and its opposite end are unequal, so gains in the controller have to be scaled to work with hydraulic systems.
Servo-Pneumatics: A Control Challenge
Hydraulics are usually recognized as a good solution when it comes to those heavy applications, but some machine builders are moving away from it. Bill Schap of Schap Specialty Machine, Spring Lake, Mich., says servo-pneumatics makes more sense for the seating test equipment systems his company builds for the automotive industry and major furniture manufacturers. "We've been doing servo loops for 15 years or more, and we're making a concerted effort to get away from hydraulics," says Schap. "They're noisy, they leak, and they're expensive. Where they do work well, however, is where there's a need for a large static load. But for the most part, low-end hydraulic applications easily can be replaced by pneumatics and servo-pneumatic systems."
According to Schap, he's been working with Enfield Techologies since its proportional pneumatic valve came out a decade ago. When it was first available, he says, it was intended for holding position on pneumatic cylinders with position feedback. "For our applications, we closed the loop with a load cell instead of a position sensor. We've done more than a hundred systems like that over the past 10 years. Many of those systems used up to 16 cylinders,all closed loop, all running independently to a single PC,with good results."
Enfield's LS Series servo-pneumatic control system runs open or closed loop, includes a dedicated device controller and features a five-port, three-position closed-center directional valve. Company president Ed Howe notes that the convergent controller circuitry provides real-time command and feedback signal monitoring with a less than 100 ?sec response time. While the system was designed for proportional pneumatic control, it can also be used in speed applications with a total cycle time of 5 ms for a complete open and close of one port.
As with hydraulic cylinders, pneumatic cylinders can be teamed with various position sensors to provide feedback to a controller. Potentiometers generally are low-cost devices, about a third the cost of other sensors. Since they require physical contact with the actuator, lifetimes are shorter than non-contact devices. Magnetostrictive sensors provide absolute position information and non-contact service, but can range in price from $300 to more than a $1,000, depending on length and application. While inductive sensors cost less than magnetostrictive sensors and don't have to contact moving parts, they are not as accurate as magnetostrictive devices.
The challenge, according to Nylund, is the controller itself. Most pneumatic systems today still use dumb controllers. "We see an opportunity for smarter pneumatic controllers, but they have to deal with the non-linear aspects of the varying compressibility of the medium," he states. "Controllers will need to have a variety of sensor inputs to monitor and control not just position, but force and pressure as well."
Bang-Bang Apps
Has pneumatic technology had its day? For stroke applications, one can use a servo motor and ballscrew instead of pneumatic cylinders. Schap says some of his customers have built fatigue testers with repetitive back and forth motion using a servo motor/ballscrew combination. They've been happy with the system's life expectancy. So, could how about linear motors? "We've watched them," says Schap. "They're still pretty pricey, and they don't put out a lot of power. What they have going for them is that they're really fast and lack moving parts to wear out. But they just don't put out enough brute force in our application."
Linear motors seem an ideal choice in positioning applications. They work in coil-winders, semiconductor wafer-transport systems, PC board pick-and-place machines, and in pharmaceutical liquid-handling systems for automated lab-testing applications. Where speed and accuracy are important to the application, linear motors are available in open-loop step motor formats, and in closed-loop designs.
Is it cost-effective to go the servo route, as in Schap's application? With a servo-pneumatic solution, there is a displacement transducer, servo valve, and a load cell,worth a few thousand dollars for the parts. With the servo motor solution, there are the servo motor and electrical cylinders. Schap thinks the cost differential between the two technologies is close, but suggests that throw-away pneumatic cylinders can be used in packaging machines to keep costs really low and perform well for two to three years. Typically, with high-stroke applications, the ballscrew doesn't last any longer than cheap pneumatics and is usually more expensive to replace.
Digital Makes Control Easier
Whether your application is hydraulic, pneumatic or electromechanical, what really makes the difference today for machine builders and their customers is digital control. Maybe it's the ease of programming or the flexibility of the electronic controls. Chief electronics engineer for Chicago-based Triangle Package Machinery (www.trianglepackage.com) Steve Bergholt says, "The flexible architecture allows us to reuse the design and simplify engineering tasks. We can forecast and pre-build, allocating our resources to get a machine to market in three months instead of six, saving thousands of dollars in engineering costs."
Digital systems provide faster update times, they're more robust, and they have no temperature sensitivity problems notes Erik Nieves, senior manager for technology advancement at robot builder Motoman Inc. (www.motoman.com), West Carrollton, Ohio.
Machine builders are not the only beneficiary of digital control. "Customers want to be able to do file transfers over an Ethernet network," adds Nieves. "They also want to be able to do I/O communication over digital networks."
Alpha's Green says customers also like the ability to store and recall quality control records. "We can archive the final position and pressure for each part," says Green. "Internet connectivity is another plus because troubleshooting can be performed without an expensive on-site service call." It's easier to train on a system like this, too, and customers like the ability to tie into their enterprise systems to monitor the manufacturing process.
And software takes the complexity away from customers that just want to get a job done, rather than twiddle with knobs, switches and dials. "Whatever weird load profiles you want: go to 20 lbs. and hold for ten minutes, go out to 30 lbs. and hold for ten minutes, then 400 lbs. and hold for ten minutes,we can do it," exclaims Schap's unit manager, Brian Sayranian. "It's just software. Any extraneous loading seen by the part can be compensated in the software."
Do the Homework, Then Decide
Before you make a buying decision, consider your application carefully. Don't discount any particular option until you've weighed the cost-benefits thoroughly. Though Sayranian doesn't have much good to say about hydraulics, he'll tell you that for his company's seatbelt pull testing system, "where you need to pull on the seatbelt loading points until the belts destruct--there just isn't any other choice that can deliver the stroke and the force. If you used pneumatics, you'd need cylinders that are 8.5 in. in diameter and 25 in. long."
Wayne Labs is an industrial automation veteran with more than 15 years engineering experience and 20 years in senior editorial positions. You can reach him at www.waynelabs.com.Additional Considerations for Machine DesignersAction requiredWith modern position sensors and closed-loop control methods, servo-pneumatics fulfill more than traditional bang-bang stroke applications, while servo-hydraulic systems can position heavy weights with accuracy and precision. They both have a few drawbacks, but for well-chosen applications the benefits will outweigh the problems.
Heavy-Lifting Hydraulics
Hydraulic-power solutions are great for heavy lifting or where extreme applied pressure is required, such as for powdered-metal press operations. Typically, powdered metal is dropped into a mold, called a die. An upper cylinder pushes a "punch" into the die area and compresses the powder. "Pressures depend on the machine's size, but can range up to 750 tons," says Scott Green, president of Alpha Lehigh Tool and Machine Co. (www.alphalehigh.com), Phillipsburg, N.J. The compact powder particle mass that holds the shape of the die is pushed out of the die and then baked in an oven similar to a ceramics kiln. The metal particles bond at the grain and molecular level,a microscopic welding process known as sintering.
"We refurbish presses to modern standards and use a closed-loop control system to operate proportional valves that control the amount of oil to the upper and lower ram cylinders," says Green. "Magnetic transducers on the upper and lower ram cylinders supply position feedback to the computer. The computer system provides greater flexibility with upper and lower ram movements, and greater flexibility and synchronization with the feeder system,the system that moves the powder into the mold or die."
With these servo-hydraulics, says Delta Computers CEO, Steve Nylund, the system can position down to the resolution of the transducer,in the micron range,and do it accurately and repeatedly. "You can apply huge amounts of force, and do it more safely than with pneumatics," he says. "Hydraulic actuators are smaller than their electrical servo cousins, and are a real benefit when a machine builder has a limited amount of space, but needs to apply large forces accurately."
There are transducers that are well-suited to hydraulic applications. For example, magnetostrictive transducers can be inserted into a hydraulic cylinder,the combination making an excellent actuator-feedback system. But industry professionals say there are special control considerations for hydraulic systems. Hydraulic cylinders typically are built as single-end devices. The forces on the rod side and its opposite end are unequal, so gains in the controller have to be scaled to work with hydraulic systems.
Servo-Pneumatics: A Control Challenge
Hydraulics are usually recognized as a good solution when it comes to those heavy applications, but some machine builders are moving away from it. Bill Schap of Schap Specialty Machine, Spring Lake, Mich., says servo-pneumatics makes more sense for the seating test equipment systems his company builds for the automotive industry and major furniture manufacturers. "We've been doing servo loops for 15 years or more, and we're making a concerted effort to get away from hydraulics," says Schap. "They're noisy, they leak, and they're expensive. Where they do work well, however, is where there's a need for a large static load. But for the most part, low-end hydraulic applications easily can be replaced by pneumatics and servo-pneumatic systems."
According to Schap, he's been working with Enfield Techologies since its proportional pneumatic valve came out a decade ago. When it was first available, he says, it was intended for holding position on pneumatic cylinders with position feedback. "For our applications, we closed the loop with a load cell instead of a position sensor. We've done more than a hundred systems like that over the past 10 years. Many of those systems used up to 16 cylinders,all closed loop, all running independently to a single PC,with good results."
Enfield's LS Series servo-pneumatic control system runs open or closed loop, includes a dedicated device controller and features a five-port, three-position closed-center directional valve. Company president Ed Howe notes that the convergent controller circuitry provides real-time command and feedback signal monitoring with a less than 100 ?sec response time. While the system was designed for proportional pneumatic control, it can also be used in speed applications with a total cycle time of 5 ms for a complete open and close of one port.
As with hydraulic cylinders, pneumatic cylinders can be teamed with various position sensors to provide feedback to a controller. Potentiometers generally are low-cost devices, about a third the cost of other sensors. Since they require physical contact with the actuator, lifetimes are shorter than non-contact devices. Magnetostrictive sensors provide absolute position information and non-contact service, but can range in price from $300 to more than a $1,000, depending on length and application. While inductive sensors cost less than magnetostrictive sensors and don't have to contact moving parts, they are not as accurate as magnetostrictive devices.
The challenge, according to Nylund, is the controller itself. Most pneumatic systems today still use dumb controllers. "We see an opportunity for smarter pneumatic controllers, but they have to deal with the non-linear aspects of the varying compressibility of the medium," he states. "Controllers will need to have a variety of sensor inputs to monitor and control not just position, but force and pressure as well."
Bang-Bang Apps
Has pneumatic technology had its day? For stroke applications, one can use a servo motor and ballscrew instead of pneumatic cylinders. Schap says some of his customers have built fatigue testers with repetitive back and forth motion using a servo motor/ballscrew combination. They've been happy with the system's life expectancy. So, could how about linear motors? "We've watched them," says Schap. "They're still pretty pricey, and they don't put out a lot of power. What they have going for them is that they're really fast and lack moving parts to wear out. But they just don't put out enough brute force in our application."
Linear motors seem an ideal choice in positioning applications. They work in coil-winders, semiconductor wafer-transport systems, PC board pick-and-place machines, and in pharmaceutical liquid-handling systems for automated lab-testing applications. Where speed and accuracy are important to the application, linear motors are available in open-loop step motor formats, and in closed-loop designs.
Is it cost-effective to go the servo route, as in Schap's application? With a servo-pneumatic solution, there is a displacement transducer, servo valve, and a load cell,worth a few thousand dollars for the parts. With the servo motor solution, there are the servo motor and electrical cylinders. Schap thinks the cost differential between the two technologies is close, but suggests that throw-away pneumatic cylinders can be used in packaging machines to keep costs really low and perform well for two to three years. Typically, with high-stroke applications, the ballscrew doesn't last any longer than cheap pneumatics and is usually more expensive to replace.
Digital Makes Control Easier
Whether your application is hydraulic, pneumatic or electromechanical, what really makes the difference today for machine builders and their customers is digital control. Maybe it's the ease of programming or the flexibility of the electronic controls. Chief electronics engineer for Chicago-based Triangle Package Machinery (www.trianglepackage.com) Steve Bergholt says, "The flexible architecture allows us to reuse the design and simplify engineering tasks. We can forecast and pre-build, allocating our resources to get a machine to market in three months instead of six, saving thousands of dollars in engineering costs."
Digital systems provide faster update times, they're more robust, and they have no temperature sensitivity problems notes Erik Nieves, senior manager for technology advancement at robot builder Motoman Inc. (www.motoman.com), West Carrollton, Ohio.
Machine builders are not the only beneficiary of digital control. "Customers want to be able to do file transfers over an Ethernet network," adds Nieves. "They also want to be able to do I/O communication over digital networks."
Alpha's Green says customers also like the ability to store and recall quality control records. "We can archive the final position and pressure for each part," says Green. "Internet connectivity is another plus because troubleshooting can be performed without an expensive on-site service call." It's easier to train on a system like this, too, and customers like the ability to tie into their enterprise systems to monitor the manufacturing process.
And software takes the complexity away from customers that just want to get a job done, rather than twiddle with knobs, switches and dials. "Whatever weird load profiles you want: go to 20 lbs. and hold for ten minutes, go out to 30 lbs. and hold for ten minutes, then 400 lbs. and hold for ten minutes,we can do it," exclaims Schap's unit manager, Brian Sayranian. "It's just software. Any extraneous loading seen by the part can be compensated in the software."
Do the Homework, Then Decide
Before you make a buying decision, consider your application carefully. Don't discount any particular option until you've weighed the cost-benefits thoroughly. Though Sayranian doesn't have much good to say about hydraulics, he'll tell you that for his company's seatbelt pull testing system, "where you need to pull on the seatbelt loading points until the belts destruct--there just isn't any other choice that can deliver the stroke and the force. If you used pneumatics, you'd need cylinders that are 8.5 in. in diameter and 25 in. long."
Is the machine moving a load linearly or rotating it? It could be handled by hydraulics, pneumatics or electromechanical Are you controlling force that's being applied to an object? That's typically best suited for servo/proportional hydraulics or pneumatics.
Force required to Move a Load/Object
While electromechanical actuation has reached the ability to move large loads, it still can't match hydraulics. Loads of approximately 2000-2,500 lbs and under are handled easily by either electromechanical or servo-pneumatics. Above that you get into the realm of electro-mechanical (limit for electromechanical is about 8,000-10,000 lbs) and servo/proportional hydraulics.
Degree of motion
Electromechanical actuators are best suited for pure linear applications. They have gotten better at offering range/degree of motion such as swinging or rotation, but hydraulic and pneumatic actuators still are better for this-they actually are designed for it. Additionally, hydraulic and pneumatic actuators can handle column strength and side-load issues much better than electromechanical actuators since you can put oversized rods in the cylinders.
Accuracy
The nature of electromechanical actuator's lead/ballscrews is accuracy in the 10-thousandths range. However, most applications don't require this.
Environment
Machine or plant environment is more often an important design issue for machine builders. Electromechanical actuators offer the cleanest motion control followed by servo-pneumatics and lastly hydraulics. Many engineers and users have the impression that hydraulics is a very dirty power source. But hydraulic systems have come along way since their inception after World War II. Sealing technology has gotten better and has in most cases eliminated leaks, especially since the inception of SAE and/or O-ring sealed fittings. Additionally, water hydraulics have changed the landscape as well. Engineers can design machinery to use tap water to power motion control systems, which eliminates the potential hazards of petroleum-based oils.
Noise
Most people are accustomed to the noise generated by pneumatics and hydraulics. However, OHSA is mandating less noise. This is another reason why electromechanical actuation has become popular. But servo-pneumatics has eliminated the clacking of cylinders hence eliminating noise. Noise is still an issue for hydraulics.
Cost
Today, cost is a big issue for all machine builders and designers. Typically, the least expensive of all three systems is servo-pneumatics. It typically runs 50 to 75% less than electromechanical and servo/proportional hydraulics. This, of course, assumes the plant is all ready using compressed air.
Jeff Klingberg, Fluid Power Technologies Int'l
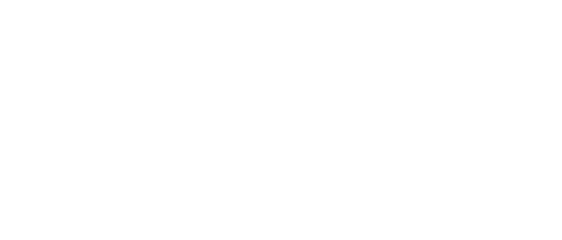
Leaders relevant to this article: