By Tim Schurr, Senior Controls Engineer, Stock America
S |
tock America Inc. is an original equipment manufacturer that builds custom batch sterilizers -- known as retorts, as well as associated equipment for food and pharmaceutical processors. Based in Grafton, Wis., the company works directly with users to design, install and validate in-container sterilization technology that helps ensure products and packaging are contamination free. Stock America serves processors of both retail and institutional products, so its retort designs are standardized, yet flexible enough to meet the varied needs of that diverse customer base.
Stock America develops approximately 30-50 retort units annually, each taking four to six months to build. The units are uniquely designed to support highly sensitive products and containers (See Figure 1). This is a niche market, but it's a growing market.
FIGURE 1: IT'S NOT EASY BEING CLEAN
With 21 CFR Part 11 regulatory requirements, it was increasingly difficult for Stock America to keep up with the rapid technology advances for the custom programming, controllers and other hardware devices required for the operation of the custom batch sterillizers it builds.
We had been using proprietary data acquisition and transfer technology for our retorts, developed based on custom Microsoft Visual Basic scripts. Data was captured from the retorts using controllers set up for viewing on an operator interface and transferred to a database. Stock America developed and maintained the software internally, updating the technology based on customer requests or as needed for new functions.
Because the proprietary software was integrated closely with Microsoft programming standards and Allen-Bradley control technologies, changes in those products also prompted regular changes to the software.
Although proprietary software offered most of the functionality Stock America customers needed, new federal regulations for consumer safety and security were introduced to the market, impacting Stock America's large base of food and pharmaceutical customers. The Food and Drug Administration (FDA) began to demand more stringent safety regulations through 21 CFR Part 11--requiring detailed records on how products are designed, manufactured, packaged and sold. As part of a customer's total manufacturing process, data-producing hardware and software components of Stock America retorts would also need to provide compliance records.
Change Is Good
With these new regulatory requirements, it was increasingly difficult for Stock America to keep up with the rapid technology advances of Microsoft for the custom programming, and Rockwell Automation for the controllers and other hardware devices. The company no longer had the time to continually modify the software scripts to stay current, and the staff didn't want the internal development process to slow down time-to-market. In addition, the company's product managers and design engineers wanted to continue to incorporate new functionality and improved security features, but didn't have the time or the resources to do it effectively.
Company engineers decided that it was time to look at replacing its custom Visual Basic scripts with a commercial HMI software package that would provide data acquisition and transfer, with integrated 21 CFR Part 11 compliance capabilities.
"We wanted to find a commercial HMI software package that would let us offer maximum HMI functionality, and reduce the amount of time we were spending in development," says David Polvino, vice president of Stock America. "We felt that being able to off-load development tasks would help us focus on adding new capabilities to the retorts, rather than spend our time just keeping up with the technology."
The Ultimate Solution
The Stock America Sterilization System Division in Cary, N.C., is responsible for engineering and sales support for all Stock America retort systems. The sterilization division evaluated a number of commercial HMI packages and selected Rockwell Software RSView Supervisory Edition HMI package, running on Allen-Bradley VersaView industrial computers (See Figure 2). The decision to go with Rockwell Automation was due to the company's previous experience, familiarity with Rockwell's products, and,critical for Stock America,its support for 21 CFR Part 11 compliance.
A new HMI package offered all the data acquisition functions that Stock America was looking for, adding improved security and reporting, using it primarily to record process temperature and pressure for compliance with governmental regulating agencies.
This version of RSView Supervisory was ideal for Stock America and OEMs like it because the distributed HMI architecture allows processing information to be available at both the local and enterprise levels. Each retort can have a client for local control, while the server makes crucial processing information available to supervisors at the enterprise level.
"Rockwell Automation brought programming staff from its Global Manufacturing Solutions group to help us with the migration from our proprietary Visual Basic application to RSView," says Polvino. "Together, we were able to migrate our scripts to RSView and decrease the need to redevelop HMI screens." Stock America also installed Rockwell Software's RSSql transaction manager software, a technology that provides efficient data transfer between the controllers and a Microsoft SQL Server database.
"As a small OEM, its tough to stay on top of all the new government regulations impacting automation," says Polvino. "But Rockwell Automation is closely involved with 21 CFR Part 11 development activities and the Parenteral Drug Association Task Force, so they constantly build these latest requirements into their products. This allows us to offer the most up-to-date features to customers without having to be experts ourselves."
According to Polvino, to be 21 CFR Part 11 compliant, customers must be able to authenticate the user of the retort and its control system, manage audit trails of actions taken at the machines and archive electronic records. Specifically, Stock America customers must prove--on a per-batch basis--that all products are sterilized appropriately and that systems in place are working as expected. The FDA monitors the filing and validation of the process and has the right to review records at any time to ensure each batch was correctly sterilized.
To authenticate users, Stock America's system uses Windows security, electronic signatures and authorization. Customers can set up and grant user rights based on roles. Operators logging in are prompted to enter an electronic signature and obtain verification. Via RSSql, all operator actions are logged in an external SQL Server database with the user name to create an audit trail of actions taken on the machine.
All control system data also must be logged in an audit trail, so changes to the controller or other devices are gathered and logged in the database. This makes it easy for customers to collect and maintain a comprehensive record of process settings and changes made to the retort system.
"The larger built-in security and auditing functions helped us see the integrity of the data acquisition and reporting," explains Polvino. "We knew the tools used in our modular portion of production would integrate well with an enterprise solution."
Stock America provides specific 21 CFR Part 11 reports to customers, but customers can also run their own reports on the database if needed.
The choice of HMI hardware was also important to Stock America. "We have customers with very clean, dry-processing environments and others with wet or rugged environments. VersaView was the best choice and we believed it would be durable enough to handle any type of customer environment," says Polvino. "Having a single-source supplier for hardware and software was also a big selling point. We now have one support contact for all aspects of our development and implementation."
"The ability to reuse code helps cut down the time to create new HMI programs, and functions it previously would have had to build itself are now included."
|
"In our former Visual Basic environment, we couldn't create a tagged database and export to an Excel spreadsheet like we can now. It saves a lot of time," adds Polvino.
Stock America also has been able to provide support for 21 CFR Part 11 to customers who need it, without custom development. The system automatically runs reports at the end of each shift that document the authentication and audit data required to meet the FDA's 21 CFR Part 11 compliance regulations.
And, Stock America's customers understand the advantages of the new system as part of a migration toward a more information-based system. "Looking forward, we feel our customers will want to better leverage information to track maintenance and performance issues, and having the architecture to support those functions now, will help customers in the future."
While Rockwell Automation is virtually transparent to Stock America's customers, when the company delivers a RSView HMI software package, users can contact Rockwell Automation directly for technical support. "Our goal is to provide to best systems we can to our customers--systems that offer solutions for the needs they have today, and the needs they anticipate tomorrow," concludes Polvino. "Being able to find technology that offers the latest features, grows with the customer, and still allows us to customize is a valuable asset for our company."
Tim Schurr is senior controls engineer, Stock America. Learn more about the company at http://www.stockamerica.com/.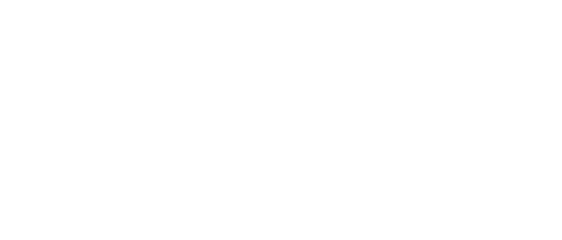
Leaders relevant to this article: