By Rich Merritt, Senior Technical Editor
For several years, the cost of machine vision systems tumbled faster than the stock market. Prices dropped from hundreds of thousands of dollars per system to tens of thousands per system to near-$1,000 prices. Today, you can buy vision systems as a commercial off-the-shelf (COTS) product. Vision systems are rapidly becoming commodities, much like programmable controllers, limit switches and computers.
The big question is whether COTS systems are suitable for machine vision applications. Can a COTS system perform with the needed speed and performance required by fast-moving production lines? Or do machine builders still need special systems designed for speed, performance and reliability?
For our purposes, let’s define a COTS vision system as something that is available, more or less, on an off-the-shelf basis. That is, you call a vendor, you order a system, and it ships in a few days.
Make vs. Buy
Concept Systems, a system integrator in Albany, Ore., decided custom engineering vision systems into every application no longer made sense. “We evaluated all the major vision providers, plumbed the depth of our capabilities, and determined that rolling our own vision system really didn’t make sense from a financial standpoint, as well as an inventory and support standpoint,” says Doug Taylor, principal engineer at Concept Systems.
That sentiment is echoed by an Atlanta-based builder of specialized aircraft assembly and manufacturing systems for Lockheed Martin’s new jet fighter, the F/A-22 Raptor. “When we first thought about this application,” says Roger Richardson, president, Delta Sigma Corp. (DSC), “we assumed we would have to work from the CCD on back. But when we found we could buy, ready-to-go, a no-compromise vision system that fit our accuracy and package requirements for $5,000--instead of creating something that would likely take us $100,000 and three months to develop--there was no reason not to go with it.”
For many it’s a relief that COTS vision is a viable alternative because early systems were tough to build and program, says Roberto Griguoli, vision project manager at Simac Masic, Veldhoven, Netherlands, an engineering firm that specializes in design and development of machine vision, motion control and data acquisition solutions "In the early days, computer programmers were an essential part of machine vision projects for OEMs,” he says. “The only way to get the job done was by programming in C or C++,” explains Masic. “These computer programmers were forced to learn the details of imaging, lighting, optics and image processing.” You had to pay big bucks and follow a steep learning curve for those highly specialized individuals.”
George Blackwell, director of product marketing for Cognex, agrees that in-house development of vision systems went out with bellbottom pants. “Very few equipment builders design their own vision boards today,” he says. “Most buy off-the-shelf hardware--frame grabbers, cameras and lighting--then integrate these components into a system.”
Concept Systems eventually standardized on Cognex board-level vision products and cameras. “We use boards with a 1024x768 camera for normal projects, and a board with a 1280x1024 camera for projects that require a greater field of view as well as high resolution,” explains Taylor.
For its 96 servo axes, 16-camera VisionPin non-contact wing and fuselage alignment and mating system for the F/A-22, Delta Sigma specified DVT Corp.’s Series 600 high-speed smart cameras with 640x480 pixel resolution and separate, modular light sources. The cameras are fixed to critical mating lugs on tools that represent the wings while the main part of the system supports and manipulates the forward, mid, and aft fuselage sections. According to Brett Haisty, vice president of engineering at DSC, “position measurement accuracy is 0.0002 in. in-plane and the distance measurement is accurate to 0.0005 in. with this camera.”
The cameras provide a visual “pin” for the lugs to align to and deliver precise position feedback to control the X, Y, Z, roll, pitch, and yaw motion of the tools moving the fuselage subassemblies into position. The system ensures alignment accuracy of 0.004 in. across the aircraft’s 22-ft.-long wing joint.
Doug Wilson, president of PVI Systems, an engineering firm in East Lyme, Conn., also puts machine vision systems in the custom machines his company builds for customers. “We mostly use machine vision for parts inspection applications, but we also employ vision in a true control mode, where the vision system is used to collect feedback,” says Wilson.
Like Concept Systems, PVI has years of experience with vision applications and it, too, chose a COTS solution. “We use products from National Instruments,” says Wilson. “It lets us use the same LabView and IMAQ Vision software, with which we have more than eight years of experience.”
One of the best features of a COTS system is its reliance on standards, says Kyle Voosen, product marketing manager at National Instruments. “All of NI’s products leverage industry-standard PC technologies,” he says. “A perfect example is our CVS, a tiny, embedded machine vision system based on an Intel chipset, IEEE-1394 for camera and hard drive connectivity, and a reconfigurable Xilinx FPGA for custom digital control and I/O. This architecture allows machine builders to choose the best vision components for their application and even use their own custom vision algorithms.”
Applications Galore
We’ve heard pretty compelling testimony so far. But can a PC-based COTS system handle tough, industrial, high-speed applications in nasty environments? It seems so.
Averna Technologies in Ottawa, Ontario, builds test, evaluation and parts inspection systems for high-speed automation applications. One application required detecting 100 µm-size cracks on both sides of a fast-moving cast aluminum slab with a surface temperature of 400° C, and then marking the defective slabs in real time.
“One challenge we had to consider was the 400° C slab temperature,” says Shahzad Sarwar, director of industrial and real-time solutions. “The delicate vision inspection system needed to operate in a harsh casting process line environment, so we housed all cameras and illumination components in NEMA enclosures with forced cooling. We enclosed the light sources and computing hardware in a cooled cabinet and operated the system through an industrial touchscreen front panel.”
The other problem was line speed. “We used two line-scan cameras with 8,000 pixels each and a line acquisition rate of 5 KHz on either side of the slab,” says Sarwar. “We used spatially randomized light lines to illuminate the slabs with high-intensity white light. A speed-encoder wheel and a pair of limit switches generated the TTL trigger envelope that was routed to the camera through an NI PCI-1422 frame grabber. The images were analyzed by dual, 2.8-GHz Xeon workstations running optimized software built with LabView and its image-processing library. If a surface defect was detected, the PC actuated a rejection system to mark the slab on the side.”
Sarvar says the software supplied with the vision system simplified development and saved money. “From conception to deployment, we developed the system in a short period of five months, and saved more than $200,000,” he says.
Not only are today’s vision systems easier to set up than ever before--DSC’s proof-of-concept setup of the VisionPin lug alignment system took about two hours--they can do jobs that mere humans find very difficult or labor-intensive.
Soliton Automation built a pencil-sorting system that examines 2 million pencils per day, and sorts them by word type, textures, and lead color. It also checks for defects such as missing lead, lead offset, misalignment of slats, wood pieces chipping off, and holes.
“Prior to our vision solution, more than 120 people manually removed these defects, but even though a large number of people were involved, the quality of segregation was far from good,” says Soliton engineer Anand Chinnaswamy. The customer decided to go with an automated system. “The system we created consists of two high-resolution, high-speed monochrome line scan cameras focused at opposite sides of the pencil,” explains Chinnaswamy. “Motorized filter wheels enable an automatic filter change depending on the pencil lead’s color. These cameras are connected to two separate digital frame grabber cards. We positioned the cameras so the pencil axis was in line with the camera axis as they travel on the conveyer.” The system, says Chinnaswamy, will pay for itself in less than a year.
A vision system can check, inspect and measure much faster than humans. At the Lander Automotive factory in Woodgate, U.K., a Cognex vision system inspects cross car beams for the Ford Transit. The camera is mounted on a robot arm, and it inspects 49 points on the beam, looking for the presence and location of welded brackets, screw clips, etc.
According to DSC’s Richardson, before Lockheed automated the aircraft fuselage assembly operations, the procedure was all manual. Engineers were moving aircraft fuselage assemblies with hand jacks and checking alignment with feeler gauges. “This process could take nearly a shift to complete with several technicians climbing around the plane checking, adjusting and checking, over and over until all the aircraft’s subassemblies were aligned perfectly,” he says.
Now, at the push of a button, the cameras take a single measurement at all points and this data is sent via Ethernet to the control computer, which computes and outputs a new position value for seven motors per subassembly [controlling the jacks] telling them 'there is your new position.’ Those motors move to the new positions, then stop. What once took hours now can be accomplished in seconds.”
Software Sells
Taylor says the vision system software helps sell customers. “The rapid-development environment provides a virtual cornucopia of highly advanced and standard tools to very quickly mock up a system for proof of concept,” he explains. “This is invaluable in freeing up dollars from skeptical customers that have very unique needs. In addition, it also saves huge resources and reputation when the proof of concept proves that the application actually is not possible.”
Grignoli, from Simac Masic, adds that end users also benefit from modern software. “The graphical nature of the modern programming software supplied with some COTS systems allows end users to expand, tune, and optimize the vision system long after the system integrator or machine builder has deployed the equipment,” he says. For a machine builder, that may mean fewer trips to the user to fine-tune or update the system.
Closed-Loop Control
Some vision systems don’t inspect anything. Instead, they are used for closed-loop control. PVI Systems built a closed-loop vision system that controls a manufacturing process. “We built a system to dynamically control the position of up to 14 strength members as they are being fabricated for use in towed array sensors,” says Wilson. “The vision system measures position marks printed on the strands and the position-error data from the images are used to control electronic brakes on the 14 supply reels and other brakes in the system to maintain a constant length among all the strands.”
A closed-loop system doesn’t actually have to control the process. It can simply shut a line down when it discovers a critical problem. Concept Systems built a vision system for an airplane manufacturer in Washington. “The riveting machine rivets the skin to the spars of the aircraft, installing a rivet every six seconds,” says Taylor. “Right after rivets are injected into the machine’s fingers, we take a snapshot and look to make sure it's the correct rivet and that it is positioned properly in the fingers. Our system tells the operator whether it's okay to put into the wing. If it's not okay, the system will stop and tell an operator to come and maintain it.”
The system uses Cognex and JAI cameras. “If the vision system wasn't there, the wrong rivet could be injected or it could be inserted crooked or even miss the hole,” adds Taylor. “This has caused damage in the past, which is very expensive to correct after the fact. The cost can be in the hundreds of thousands of dollars, primarily because the damage has to be corrected in a way that maintains the integrity of the wing/body.”
Standalone vs. Components
The major reason COTS systems are easier to use is because they are smarter than ever. Some “smart” cameras contain the image-processing hardware inside the camera itself, which means they can stand alone. All a vision engineer has to do is configure the system and teach it the task at hand. So what’s best for a machine builder? Smart standalone cameras or a component system?
“In the past, smart cameras did not have much horsepower, so they represented a smaller part of the overall machine vision market,” says Joe Rogers, VP marketing at PPT Vision. “With improving power, speed, and image-processing software, some smart cameras now have all the capabilities of full-scale vision systems.”
This can be beneficial to machine builders. “The good part is low cost, they are easy to set up and they do not require a highly trained individual to operate, so the end user is saving money all the way around,” says Reno Suffi, sensor and vision marketing manager at Omron Electronics. “On the factory floor, simple is always better. In addition, the machine builder can get dedicated systems up and running with much shorter development time.”
Once taught, a standalone system becomes just another I/O peripheral. “While most of our vision products use a camera with a separate processor, our LightPix system is a standalone vision sensor,” says Niki Hoffman, marketing manager at Aromat/Matsushita. “Once the camera is taught what to look for, the controller can be removed and all outputs come directly from the camera.”
Catherine Overbury, marketing manager at Matrox Imaging, says its Matrox Iris product integrates everything but the lighting. “A major benefit of a smart camera is that its components are integrated by a single vendor, so compatibility is ensured,” she says. “Another benefit is that the camera's compact form factor ensures that it fits into physical spaces too small to accommodate a traditional PC-based vision system.”
Overbury cautions that a smart camera can’t do everything. “The lighting component of a vision system is extremely application-specific,” she explains. “It is dependent upon the environment as well as the object that must be illuminated. It is an oversimplification to believe that the one-size-fits-all lighting solution offered by a COTs system works well for all vision applications.”
They can be a godsend, too, says Taylor. “Products that seamlessly integrate with a PLC as remote I/O offer a siren call to integrators that are responsible for the whole PLC system installation,” he notes.
Smart cameras definitely have gotten smarter, but are not universally accepted to be as smart as the board-level and PC-based systems. “A smart camera always will be limited in its processing capabilities,” cautions Overbury. “It never will offer the power of a traditional PC-based vision system because it cannot dissipate the amount of heat that would be generated by such processing power.”
Voosen of NI agrees. “Because of their limited processing power and specialized nature, most smart cameras do not offer support for more sophisticated, high-level algorithms like pattern matching, geometric matching, or part classification,” he says.
Voosen, of course, recommends NI’s embedded CVS, while PPT Vision suggests adding a PC to a smart system. “What we have observed is that most often, smart cameras are used in conjunction with a PC so that the eventual end-user can have some visibility into the machine vision results,” says Rogers.
Blackwell of Cognex retorts that smart cameras are plenty smart. “The new generation models have the processing power to run robust vision tools such as geometric pattern-matching technology for feature location,” he says. “More robust tools mean that users don’t have to intervene as much during operation.”
Vision Is the Easy Part
Machine builders--and the system integrators who help them with critical domain experience--also have to sell the system to their customers. “The biggest hurdle to machine builders is no longer technical, but purely a creative issue,” says Taylor. “With the astounding number of vision options available, plus the vast amount of lensing, lighting, filtering and light coloring, it has become very difficult to find personnel--with 'out of the box’ creativity plus integration skills--who can put together a solution that separates their proposal from the competition. It’s one thing to have a solution that will work. It’s another thing to have a much simpler, faster, more robust and more cost-effective approach than the competition.”
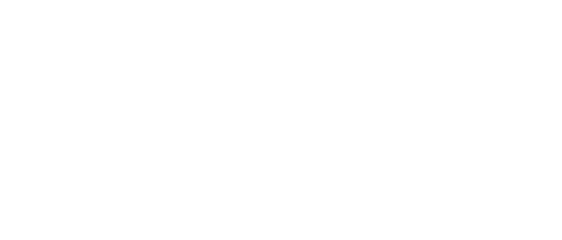
Leaders relevant to this article: