Glasstech Inc. (www.glasstech.com), Perrysburg, Ohio, makes glass-bending and tempering equipment for the automotive and architectural markets. Steve Connell, manager of systems engineering, says hardware obsolescence and lack of support are risks, and clearly are reasons to upgrade."As spare parts become more difficult to purchase, prices can skyrocket and the resulting downtime while waiting for components increases," he explains. "In addition, those older DC motors require more maintenance."The lack of diagnostics in old control systems and the availability of advanced diagnostics with new systems are additional reasons he lists for upgrading controls. "The lower level of diagnostics available in old systems makes it nearly impossible to predict the next failure," laments Connell. "With improved diagnostics, our machines can be more efficient."Glasstech had been using a Mikul bus and 6809 embedded control system, which they had developed themselves some years before. Connell says the rewards resident in Glasstech's now-standard Rockwell Automation ControlLogix platform with integrated motion control are better machine performance and improved diagnostics, plus the controls are easier to operate. "On nearly all our glass machines, higher production rates are the result of the new controls," he adds. "It was a very big decision to go from an internally developed system, where all spare parts and repairs came from Glasstech, to off-the-shelf spares."It often boils down to a short list of reasons why we upgrade. "There typically are two reasons our customers have for upgrading legacy control systems," says Ed Diehl, owner and principal engineer of Concept Systems (www.conceptsystemsinc.com), a system integrator in Albany, Ore. "First, the legacy system has become a maintenance issue or a potential maintenance issue because customers can't purchase replacement parts or support the software anymore." His second reason is that customers can improve their bottom line via productivity, quality or both with a modern control system. "Usually, the first item is why they look to upgrade, and then the clincher, in many cases, is when they can see other bottom line benefits to the upgrade," adds Diehl.Doesn't Have to Be HardOne of the easiest upgrades is to add a modern HMI/SCADA system to an existing machine control system. This might be suitable if the controls are working well and all you really need are some modern communications and Windows-based functions.Virtually every HMI/SCADA software package on the market today has one or more interfaces to legacy PLCs, machine controls and CNCs. If you can find a package that fits your specific control hardware, then you can plug your legacy controller into the 21st Century. For less than $1,000 (much less when you get an OEM agreement), this will get you a web server, Ethernet connections, advanced HMI capabilities, data logging and data acquisition and all the advantages of a modern Windows architecture, including OPC, .Net, and database connectivity. You will be able to phone in from your home office to the customer site and perform remote diagnostics.If you can't find a plug-in package that works out of the box, maybe a little hardware will help. Joel Young, vice president of engineering at Digi International (www.digi.com), says adding connectivity to legacy systems is a big part of Digi's business. "We make it possible to extend the life of existing systems with only an incremental investment," claims Young. "We provide a path by which connectivity can still be used as other components get replaced."Young offers a processing environment example that has relevance in many discrete industry applications. "Chevron needed to integrate 200 of its Square D SyNet PLCs with Wonderware software via Ethernet," he says. "The existing PLCs used a proprietary system that required a specialized PC board. To further complicate the issue, the PLCs were no longer in production and were not Ethernet compatible."What to do? Replacing 200 PLCs would be extremely costly. Besides, the PLCs were performing their control tasks admirably. They just couldn't talk to the new HMI.Digi connected the legacy PLCs to the HMI PC with its off-the-shelf RealPort communications module, so operations could continue with no changes.Schneider Electric (www.schneiderelectric.com) has an interesting way of upgrading an old network. "Install a Telemechanique Momentum PLC that can translate other vendor network protocols," advises Joe Eiden, segment manager at Schneider. Once the Telemechanique PLC gains access to the legacy network, you can take advantage of its built-in web server, XML programming and other languages to integrate to higher-level systems.If you already have a "modern" HMI/SCADA system that's more than a few years old, it's probably running on old PC hardware and Windows software, and just needs to be updated. Older systems can't gain access to web servers or modern Windows-based architectures such as .Net and OPC. Virtually every HMI/SCADA package has an update path for its own software, and some software can update other packages.When upgrading a Windows-based software package, however, it is best to start from scratch with a new PC and new Windows operating system. Trying to upgrade an old PC or an old Windows operating system is difficult, frustrating and fraught with problems. Better you should spend $395 on a white box and get a whole new system. Otherwise, you may spend 10 times that much in labor trying to update an old PC.It is much the same with old HMI hardware. Throw it out and install new (Figure 1). For example, thousands of Allen-Bradley PanelView HMI terminals exist in the machine control world, and some of them are getting long in the tooth. Rockwell Automation offers an upgrade path that replaces the hardware with new PanelView Plus software and terminals.
Figure 1: Just Add Software |
All those old A-B PanelMate and PanelView HMI terminals can be upgraded to modern PC hardware and software with a software package that reads in the old HMI screen configuration data and displays it on a PC, panel PC, or PDA. Source: InduSoft |
Upgrade the Hardware
The day will come when controllers, motion control processors and other equipment must be replaced or upgraded. See Table 1 for a little guidance.Updating control processors to a newer generation is a good way to upgrade a system for more computing power or increased reliability. Ken Wild of Crisp Automation (www.crispauto.com) says he can upgrade any Crisp control system from an old DEC PDP-11 or VAX platform to the newer DEC Alpha platform, and soon will be able to upgrade those systems to the new Itanium platform running Open VMS.Wild says R.J. Reynolds Tobacco, Tobaccoville, N.C., installed Crisp Systems in the 1980s. At that time they were using dozens of redundant DEC 11/44s to control many manufacturing machines. In the 1990s, RJR upgraded its systems to run on a handful of large DEC VAX systems.Finally, in 2001, Crisp Automation migrated the RJR control software to run on the DEC Alpha 64-bit platform. "This added many more useful years of service to control systems that R.J. Reynolds had invested more than $100 million in," says Wild.He claims he can do this for non-Crisp systems as well. "We can migrate any type of DEC VAX system running Open VMS to run on a DEC Alpha or Intel server, without any application changes," he claims. "We are currently developing a generic OPC server/client product for all VMS users."Wild also claims he has access to enough replacement DEC computer hardware and I/O boards to support all the Crisp systems that are still running.PLCs may be one of the easier controllers to upgrade. Schneider Electric, for example, offers a Validatable PLC service that allows its customers running older Modicon PLCs to upgrade to new Modicon platforms. The service allows I/O cards installed 30 years ago to be connected to new PLCs.If you haven't looked at the new breed of PLCs lately, you may be surprised. "Schneider Electric has spent more than $400 million in the past five years, completely redesigning its PLCs, drives, motor starters and other products," says Eiden. "This includes software for PLCs and motor controls. These new products have more capabilities, are simpler to install, and are easier to integrate with legacy systems."AutomationDirect says its PLCs and programming software are compatible with several legacy PLCs, some going back to 1983. "By upgrading to DirectLogic PLCs, machine builders can continue to provide replacement systems, spare parts and compatible software to their customers," says Paul Ruland, PLC and I/O product manager. "Newer models also provide multiple serial ports, Modbus connectivity, PID loops and Ethernet capabilty."What Ruland says may be very important to your upgrade; that is, you want to upgrade the machine control system that is going out the door in new systems; but you also want to be able to upgrade your customers' old systems. If you pick the right upgrade path, when you finally run out of parts for those vintage PLCs, you can repair an old system by dropping in a brand new PLC that is compatible.Upgrade as a Marketing StrategyAll the major machine control system vendors offer migration paths to their current technology. In many cases, it's because of an old marketing axiom: It's easier to keep existing customers than to find new ones. Therefore, if you use one of their old control systems, you can be reasonably sure they will support it for a while. They don't want to lose you.The same marketing axiom applies to you: existing customers are your best source of new business. If you can keep them happy by supporting your old machines, they will think favorably of you when they are looking to buy new. Offering them a cost-effective migration to better technology (that improves productivity) via incremental control system upgrades, therefore, becomes an excellent marketing tool.Rockwell Automation makes it easy for its customers to upgrade entire drive control systems. "We can upgrade the entire system or only the architecture, while leaving in place drives and I/O," says John MacDonald, manager of commercial marketing for Rockwell's Global Drive Systems group. "One of our customers decided to keep its A-B/Stromberg drives, motors and I/O, while upgrading the control system and HMI. The upgrade protected the original capital investment, allowing them to build an integrated system without the expense and investment of an entirely new system."There's more to this strategy. "We've invested more than $2 million in developing bridge solutions--products specifically designed to make it easy for customers to migrate from legacy systems to newer systems," adds MacDonald. "For example, we have a DriveModule solution that upgrades legacy Reliance AC and DC drives to the latest PowerFlex 700S control while integrating them into a ControlLogix-based architecture." That's how big companies get big, and how the smart ones stay big.The Right Upgrade Choices
Concept Systems' Diehl does many control system upgrades. "We typically replace obsolete or highly customized control systems with modern, industry-standard, off-the-shelf hardware and software," he explains.For example, Concept Systems upgraded the controls for Andrew Corp., Denton, Texas, a manufacturer of spin lathes used to make satellite dishes (Figure 2). Concept Systems replaced the old custom control system with an off-the-shelf A-B PLC, Delta motion control system, Rockwell RS-View HMI hardware and software, and an Ethernet network to link it all together.Figure 2: Spin-Off New Controls
The custom controls on this spin lathe were upgraded to off-the-shelf PLCs, motion controllers, HMI hardware and software, and Ethernet. Source: Concept Systems"We often perform machine retrofits for customers," says Lenson Wong, director of marketing at Berkeley Process Control (www.berkeleyprocess.com). For example, Bishop-Wisecarver (www.bwc.com), Pittsburgh, Calif., installed a Berkeley controller on its track drill machines (Figure 3) 17 years ago. Bishop-Wisecarver wanted to upgrade from the existing brushless servo motors with amplifiers, because the amps required too much manual tuning. "From time to time it was necessary to re-tune and balance the individual axis amplifiers with manual trial-and-error potentiometer adjustments," reports Brian Burke, manufacturing engineer for Bishop-Wisecarver. The new controller was selected for features such as motor autotuning. Berkeley provided full electrical schematics, program updates, and an overall assessment of machine condition, according to Burke. Because the new software is backward compatible to the old, they were able to preserve the machine application software and operator interface displays. "System upgrades, installation and testing took fewer than eight days," he said.Figure 3: Teenage Controls
The software controlling the servo motors on this four-axis track drilling machine was 17 years old, but upgrading it to new autotuning software was easy. The new software was backward compatible to the old system, so the machine control and OI displays could be preserved. Source: Bishop-WisecarverConnell says Glasstech often upgrades its customers' systems, and it's not a major problem. "On our systems, the controls are a small part of the overall cost of a machine," he states. "Our systems were built to last for decades, long after the electronics and software had changed. Also, the time required to upgrade the controls is a fraction of the time required to install an entirely new system. Unless the customer has not taken care of their system for 10-15 years, it is generally not necessary to bulldoze the current system."Sometimes it is necessary. "We manufacture specialty food packaging machinery systems with both PLC and embedded controls," says Peter Brennen, electrical engineer at Sealed Air (www.sealedair.com), Danbury, Conn., "and we upgrade systems fairly often in the field."Brennen says the company designs and programs its own systems, so it usually can upgrade them easily. But one was a mess. "We had to bulldoze one old system," he says. "The prints were not up to date, the wiring looked like a plate of spaghetti, and the technology was old. The safety devices had to be updated as well. On top of all that, our original service rep for the system changed jobs and the new one did not know how to troubleshoot the system. So we put in a whole new control system that combined our updated technology and AutomationDirect PLCs."Table 1Should You Upgrade?Top 10 reasons for upgrading your legacy machine control system:10. Increasing failures in the field are stretching your service department to its limits9. Fewer parts are available to support and maintain systems8. The cost of upgrading is less than the cost of repair7. The old system can no longer perform its control task6. The old system cannot be expanded to perform new tasks5. The original vendor no longer supports the controller4. Customers want machine data the system cannot provide3. New control schemes would provide economic benefits, but the old system can't perform the functions2. No one remembers how to configure or change the controlsAnd the number one reason:1. You're spending too much time on eBay looking for spare parts
By bringing this customer into the 21st Century with a new PLC, Sealed Air simplified all future upgrades. "I find that upgrading PLCs is easy and quick," says Brennen, "because you can just add or remove cards."
Plan First, Then Upgrade
Once you've determined that you must upgrade the controls, plan ahead. "We start by understanding what the system does," says Diehl. "We want to make sure we clearly understand the process we are controlling and the machinery behind it. We develop a functional description of the process, and use it as the baseline to develop the control architecture, including hardware and software for the new system."
You might want consider two things says Digi International's Young: "What new functionality do I need today and what do I need to provide in the future?" Then, says Young, beginning with the current system, "How do I get there? At some point along the way, an add-on system becomes too complex to manage. It's a big mistake to make decisions in the present without projecting future needs. This leads to trouble."
Operators and customers have certain expectations that play a part in planning. "The first problem is trying to include all the new features/improvements while keeping previous features and customizations, which can be mutually exclusive," says Connell. "The second problem is operator acceptance. The systems have a different look and feel about them, although the same basics apply. Many new and improved features require good training to explain how they function and to get the new feature accepted by the operators."
What about international considerations? "Our systems are sold throughout the world and we already have performed upgrades on a number of these systems," says Connell. "We have found that when you provide a control system that can be supported anywhere in the world, and where spare components can be purchased locally, then international customers are very open to such retrofits."
Dave Hart, commercial programs manager at Rockwell Automation, says such an upgrade project is like an iceberg. That is, there is more to it than just the hardware costs. "There are a number of factors below the surface that need to be considered," he explains, "including installation cost, employee training, machine downtime and spare parts inventory costs. The bottom line is that, when all is said and done, new equipment decisions are about measuring and weighing the whole iceberg and calculating its ROI."
Maybe you don't want to update your legacy system at all. "Despite the overwhelming line of new products continually marching into the marketplace, sometimes it makes sense to keep what you have," says Hart. "If your current equipment is reliable and meets productivity goals, there may not be any compelling reason to switch."
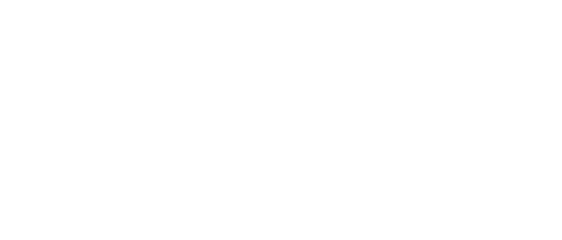
Leaders relevant to this article: