D |
elta Industrial Services in Minneapolis has designed
and built machines for the packaging and converting industry since the early 1980s. The foundation of Delta machines is servo motor-based modular technology. Our systems use proven modules that include rotary stations (used for die cutting, laminating, slitting, etc.), flexographic printers, unwind/rewinds and material-handling systems, as well as numerous additional custom and commercially available components to meet the requirements for the specific application."The modular approach allows Delta to build custom systems that handle the rapidly changing needs of medical and pharmaceutical manufacturers, including the flexibility to modify a machine--originally designed for one process--to run a different process as the customers manufacturing needs change," says Wendy Stromberg, sales engineer at Delta.Delta's Modtech Vision system is integrated into its HMI package. It can be configured for gauging, assembly verification and machine-guidance tasks.All of Delta's machines are controlled though a single, user-friendly operator interface that allows the operator to program and monitor a number of specific process modes to control registration, tension, island placement and die-to-die synchronization.The medical and pharmaceutical industries are driven to create devices that are smaller, easier to use and more accurate. These industries also are required to validate and bring these products to market more quickly than ever before. The field of in-vitro diagnostics (IVD), for example, demands constant improvements in accuracy, flexibility and production capability. Manufacturing tolerances once considered acceptable are rapidly becoming unacceptable, as new testing methods require reduced sample sizes and testing time.
"Today we are seeing trends in a variety of markets to push inspection upstream in production runs rather than simply at the final process," says Stromberg. "In addition, our customers want collection of real-time data inline with production runs, and want that inspection data written to file, where they can import it into any number of statistical process software."
One particular Delta machine, built for Multi Web Converting Inc. (www.mwconverting.com), St. Paul, Minn., handles both the printing and die cutting in one process, at a line speed of 95 ft./min. At the final stage of the process, the distance between a printed eye mark and the die cut label must exactly meet the process specification. A Visualized Solution
It eventually became apparent that Delta needed machine vision technology to ensure this level of accuracy and precision. We also needed to bring this data back to the HMI in a fashion that the operators could use.
Why vision? The customer requested data on the distance between printed eye mark and die cut. After product is shipped to the next customer, that same web runs through another machine that inserts the actual label into the product. The machine indexes to an eye mark and arm punch assembly pushes the label to joining part. So, if the eye mark to die cut does not hold very close tolerance, the end product doesn't match.
"We decided to locate cameras along the process line to make several types of visual inspection," says Delta design engineer Joel Oakes. "If these measurements reach one of the control limits, the vision system triggers discrete output to the PLC to increase or decrease the machine registration system offset between features."
Delta first tried using frame-grabber boards with progressive-scan camera systems, but the learning curve and cost of integrating these systems was unacceptable. Frame grabbers have to be installed in computers, so Delta engineers had two options: install them in their host computers, which were being used for HMI, or buy a separate computer to control the vision system. As it turned out, the frame-grabber boards use so much computing resource that the HMI program locked up and communication to the PLCs stopped.
Delta looked for an Ethernet-based vision communication system that wouldn't eat up computer resources. Progressive scan cameras and PCI-slot vision boards were not economic. The company would have to sell a lot vision systems with the machines to pay for the development costs. In addition, the cost of the vision systems and software to develop the system was too much risk.
"When we examined DVT systems, we discovered the advantages of TCP/IP communication and a use-to-use programming software package with free training," says Mike Kult, electrical engineer at Delta. "The cost to develop and purchase a solution was considerably less than the frame-grabbers system we had purchased. We could store parameters in the camera processor and we gained a significant speed advance with the DVT systems. We also found easily configurable integration tools and the need for less support once the system was installed at a customer site."
So, consistent with Delta's modular design philosophy, it used a DVT Model 540 SmartImage sensor to design ModTech Vision, a Windows NT/2000-based software package, which is integrated into Delta's Mod-Tech Rotary Converting System HMI package. It can be configured for most on-line gauging, assembly verification, and machine guidance tasks. Delta Mod-Tech Vision allows users to configure powerful vision applications at various speeds with high accuracy.
The system used was made up of the DVT sensor with a breakout board with eight digital I/O, a 16 mm Tamron lens, and a field of vision of 1.5x2.1 in. at a 640x480 pixel resolution.
At the operating speed of 95 ft./min., the vision system performs inspections of the eye mark-to-label dimension 268 times per min., or about five inspections per second. The distance is logged continuously into a file and graphically plotted during the run at the HMI.The vision system performs inspections of the eye mark-to-label dimension about five times per second. The distance is logged continuously into a file and graphically plotted during the run at the HMI.
The customer saw the process differences they wanted. "There were quantifiable improvements with the vision system," says Dan Gabrielson, president, Multi Web Converting. "Product quality improved and the ability to collect better data from the processes is a reason why. The addition of vision inspection to the ModTech machine also improved our yields by 10%."Critical Part of the Process
When Delta provides vision systems in web converting equipment, its customers can produce with greater accuracies. For example, the tolerance stacking created by multiple gear passes in traditional line shafted equipment is eliminated by direct coupling a die roller to a servomotor. In addition to the elimination of mechanical tolerances, the servo system is closed loop--the motion controller knows the position of the die at all times, permitting it to correct the position of the die or shut down the process if it falls outside programmed levels. The corrections are made by advancing or retarding the die roller in relation to the repeat of the part. This part repeat is measured by using a vision system to sense a mark or edge of the part, thereby registering the position of the part to the die location. The motion controller will either speed up or slow down the die to precisely cut the web in the proper location.
Flexibility is another advantage gained from a well-performing vision system. "Often, our customer's processes needed easy-to-configure setup and run capability from a touchscreen," says Ryan Herman, another member of Delta's electrical engineering team. "By fully integrating ActiveX components, we can customize our HMI software with vision. We have created quick tolerance with pass/fail status, easy camera setup/calibration techniques, and a statistical process package for collecting data. This means our customers can produce multiple parts on the same machine by selecting a new part program--without retooling or other costly changes to the machine."
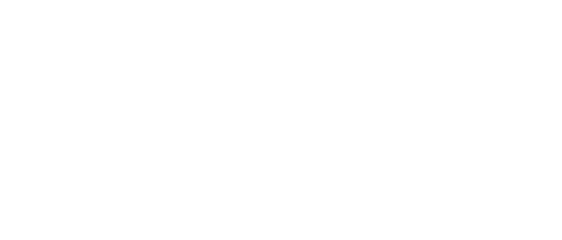
Leaders relevant to this article: