As specialists in part-handling and mold-prep technologies related to die-casting metal, Rimrock Corp. (www.rimrockcorp.com) makes machines that help manufacturers around the world make parts for a broad range of consumer and industrial products. From handling molten metal, extracting cast parts, and cleaning and preparing the die so it's ready to cast a new part, Rimrock is a well-known supplier for many of the essential production-line elements manufacturers need for their die-casting process.
Rimrock, located in Columbus, Ohio, manufactures variety of specialized machines including reciprocators, which is the industry's term for machines that spray air, water, or casting release lubricants onto each die just before it receives a "shot" of molten metal,usually either zinc, aluminum, or magnesium,to make the cast part.
Figure 1: Ethernet Enabled Ladlers
Ready to be shipped to a customer in China, Rimrock's 405 Servo-Drive ladlers manage the pour of molten metal into the die. With new Ethernet-enabled controls these machines can be monitored and controlled remotely. |
The company offers ladlers, one-armed machines that smoothly manage a dipper that ladles molten metal from the furnace, transfers it to the die, and pours it into the mold (Figure 1). Rimrock also manufactures a line of parts extractors, which do exactly that,extract freshly-cast parts from the die and place them for further handling.
Rimrock's customers expect their die-casting equipment to have a productive life of 20 years or more. However, the productivity mantra drives these manufacturers to constantly find ways to leverage their existing equipment to achieve faster casting rates, greater parts precision, higher parts yields, and less waste. The continuing quest production efficiency presents die-cast parts producers with a tough operational challenge: how to improve production performance without scrapping their huge investment in installed legacy equipment.
Challenge Accepted
That's a challenge Rimrock has gladly accepted. Rimrock has a long history in the business and it became increasingly obvious that to remain a leader they would have to provide their customers new ways to achieve incremental production improvements on their installed base of systems and a better overall return on their equipment investment.
A multi-faceted solution presented itself in the form of a compact, innovative Ethernet-based programmable logic controller (PLC). The versatile new control system (now standard equipment on all new Rimrock offerings) can be easily retrofitted to Rimrock machines in the field.
According to Rimrock, retrofitting costs significantly less than purchasing a new piece of equipment, yet delivers all of the new controller's functionality and associated production-related improvements to the machines in the field. Because most companies have cut new capital equipment budgets to the bone, Rimrock believes funds for retrofitting new controls onto existing equipment are more likely to be found and more easily allocated from the company's maintenance budget.
Ethernet's True Value Revealed
The new control platform is well-suited for controlling the dedicated reciprocator, extraction, and ladling equipment that handle the repetitive, single or two-axis motion routines of most die-casting operations,and that also make up roughly 80% of the world's motion control applications. But the real value of the new control began emerged when Rimrock and its customers began to understand how the controllers Ethernet capabilities can help trim overall equipment expenses, boost productivity, reduce machine and line downtime, while speeding and simplifying programming, maintenance, and troubleshooting.
So That's Why I Need It
While Ethernet on the factory floor is still, in Rimrock's view, in the early adoption phase, company management has no regrets about incorporating it into its control architecture. "I talk to customers and they say, 'Why do I need that? I'm not going to network my equipment unless the big boss says to do it.' I tell them we're providing the capability whether you need it now or not," explains Dave Woods, Rimrock's product development manager.
Woods admits that at first he was reluctant to incorporate Ethernet into the new control system. "I was a fieldbus snob, but the more I learned, the more it made sense," he confesses. "Every plant has Ethernet now and people are rapidly moving toward implementing it for factory-floor applications. If you're going to design something new, you'd better do it on Ethernet."
The control system is built around a Schneider Electric (www.schneiderautomation.com) Momentum M1E controller, which has an embedded web server, built-in web pages for diagnostics, integral Ethernet port, and the ability to handle information transmitted by every major sensor bus.
Immediate Cost Savings
He points to the immediate cost savings that can be achieved with Ethernet. "Two control systems networked on Ethernet can share an HMI in a small enclosure, for example, and we can locate both of the control systems on a back wall," he says. "This gives the customer great flexibility in positioning the operator station. It's also easy to debug the program from a laptop, which can become a temporary HMI if equipment gets damaged. Some customers even opt not to stock HMIs in their storeroom because of the backup capabilities the laptop can now provide."
To provide a more robust management tool for its customers, Rimrock also created an optional new operating system called ROSCO (Rimrock Operation System Console) that builds on the benefits of Ethernet (figure 2). "You can transfer jobs from machine to machine, store job specifications in the PLC, monitor settings, alarm looks, cycle counts, and cycle times," says Woods. "It provides a wealth of information that you can use for comparative analysis and troubleshooting, as well as instant disaster recovery if a PLC or HMI goes down,without engineers having to go from machine to machine to check things out. Basically it does the same thing as a SCADA system at a fraction of the cost."
Figure 2: Allows Online Access
Rimrock's ROSCO OS builds on the benefits Ethernet and allows operators to monitor settings online, transfer jobs from machine to machine, and store job specifications in the PLC. |
According to Woods the reliability of the new technology is what attracted Rimrock to the control system. "We interviewed vendor after vendor, and the Momentum PLC was the only one that could meet our cost, size, and performance criteria." The control's compact size also allowed Rimrock to reduce the enclosure nearly 50%. "Real estate is very precious in the die-casting industry, so reducing the size of the enclosure by roughly half was a major achievement," concludes Woods.
Great Market Acceptance
Rimrock has retrofit approximately 200 machines among its installed base and shipped out more than 100 new machines with the new control platform to customers such as Briggs and Stratton, Mercury Marine, Metaldyne, and Magnesium Products of America, as well as die casters M&M, Elkton, Inland, and Northern.
The company says response to the Ethernet-enabled design has been overwhelmingly positive and continues to be trouble-free. "It's outstripped my expectations," says Woods. "With anything new I would have expected problems, but customers tell me they just don't have to worry about it. They set it up and forget it."
Life has become a little easier for Rimrock lately as well. "It just works, and the phone rings a lot less for troubleshooting issues," says Darrell Swartz, product development electrical engineer. "When something does go wrong, one of the real beauties and cost savings of Ethernet is that it simplifies things. You just put an RAS server in a closet instead of installing a modem on each PLC. Eliminating a dedicated phone line can save $30/month right there. You can even go wireless."
Woods seconds the thought. "It's often one little piece of information that can instantly tell you what to fix," he adds. "With Ethernet and a web server in the PLC, you can use a number of interfaces to troubleshoot remotely and see everything you need to see without the customer having to run back and forth to the machine to check out the system. The benefits from increased uptime are enormous."
Record Keeping Simplified
Keeping a record of process changes in the PLC is another advantage. "If you're ISO-certified, you're supposed to be able to maintain process records," adds Woods. "You don't want to clutter your HMI with this stuff. Now you can gather the data and store it in the control system, tracking all process changes so that you can display them through the PLC's web server or the ROSCO operating system."
Rosy Future
Woods expects Ethernet to make a significant contribution to the operating efficiency of manufacturing plants as more and more customers adopt it for factory-floor applications. "Five years ago, no one had e-mail," he recalls. "Now even the maintenance guy has an e-mail address. You just can't live without it. We'll see the same thing happen with Ethernet on the factory floor."
Process consistency is critical for the die casting industry. "Everything has to stay the same from shot to shot--that is, constant temperature, same amount of material, same cycle time, etc.," says Woods. "The greater the number of acceptable parts made, the lower the production costs (Figure 3). So the precision of the equipment's control system is absolutely essential for improving quality and reducing costs."
Figure 3: Precision Required
Consistency is essential to lower production costs in the die casting industry. To deliver the proper amount of air, water, or casting release lubricants time after time, Rimrock's reciprocator technology (its spray manifold shown here) requires precision control. With its new Ethernet-enabled control system, operators and Rimrcok can monitor and troubleshoot the system online to maintain the needed accuracy. |
Woods estimates that several thousand older Rimrock machines now in the field are candidates for retrofit. "This equipment works in a tough environment, surrounded by extreme heat, oil, and metal fines. These factors can cause components to degrade and fail over time. While the mechanical systems can be serviced or rebuilt very cost-effectively on a routine basis, in the past it's not been as cost-effective to rebuild the electrical controls," explains Woods. "Consequently, degradation can lead to downtime issues. With our new system we can do a retrofit of the controls on site. Basically we just drop it in, with some minor wiring modifications. It's that easy."
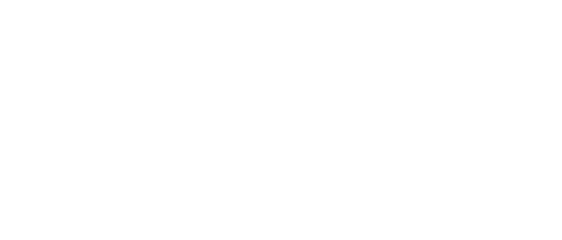
Leaders relevant to this article: