Park Industries of St. Cloud, Minn., designs and builds cutting, shaping and polishing machinery for its stone fabrication customers. There came a point when this 50-yr.-old company recognized that it needed to provide a machine control scheme that could be modified at the front end to suit the special setup, programming, operational, service, and training needs of its stoneworking customers.
Park Industries' customers cut natural stone, engineered stone (an amalgam of natural stone and a synthetic binder), and synthetic solid-surface material into various finished products. Park operates an architectural division to serve the structural, landscape, curbing, monument and related industries, while its interiors division markets machines to companies that produce kitchen and bath countertops, fireplace surrounds and mantels, stone furniture, decorative edging and other similar dimensional products.
Because Park Industries' Customers were new
to CNC-equipped machinery such as this servo-controlled,
PC-based Infinity saw, the company needed to develop
special interfaces geared toward how people in the
industry actually work.
The machines that Park Industries builds range from hydraulic stone-splitting equipment and diamond sawing tables, to edge shaping/polishing machinery and computerized gantry systems for cutting, milling and dual-saw blade orientations that produce three-dimensional architectural shapes.
The company designs, engineers and builds its machines at its St. Cloud complex, where it also operates full metalworking, welding, heat treating, and finishing departments. Park Industries also does its own electrical engineering, electrical assembly and machine sofware development in-house.
The Call of the Future
"Our Destiny CNC stonecenter, Infinity CNC stone-profiling machine and Odyssey II CNC countertop-fabrication system needed a CNC with an open-architecture orientation, so we could build-in customized user interfaces," says Bob Penas, a Park Industries electrical engineer. "For the new Destiny, we wanted to develop what we call Stonecam, a complete shop floor programming system." The system displays information and processes in the specific language of Park Industries' stoneworking customers. "That's very important," adds Penas. "Stoneworkers have traditional ways of processing material and simply using a straight metalworking control interface would be too confusing."
The engineers at Park Industries knew where they wanted to end up with regard to the new machine's functionality. They decided CNC was the only way to go. "Our experience with CNC controls was limited and we wanted to avoid the pitfalls other builders must have encountered," says Jim Eckberg, Park Industries' marketing manager. "We decided we needed to develop a partnership with a control vendor that had the engineering versatility and complete product line depth we needed to achieve the kind of machine we were dreaming about."
The company had been accustomed to assembling control systems using solutions from many vendors. "For our new CNCs, we elected to see if we could source as much as possible from one vendor," says Penas. "We wanted an integrated tested solution. We also knew our customers were so new to CNC equipment that we needed to develop special interfaces geared toward how people in our industry do their work. At the same time, we wanted to work with a supplier that could understand and make adjustments for our industry's unique demands." Choosing a vendor that offered an open-architecture system became a high priority for them.
After Careful Review
After completing an extensive examination of available CNC solutions, Park Industries settled on the Sinumerik 840Di from Siemens Machine Tool (www.siemenscnc.com) with a Visual Basic front-end and a Profibus digital-drive interface. "In the case of the Destiny CNC Stonecenter, the machine and its Visual Basic software interface were designed specifically around the 840Di's control capabilities," says Penas. "With our Visual Basic programming enhancements to Siemens' HMI, the Infinity control is up and running out of the box. Penas adds that it's faster to learn, easier to use for stoneworkers than traditional G-code programming, and allows the machine to display movements and programming routines specific to customer needs."
The Infinity has three CNC-controlled axes. The cross travel X-axis covers 13.5 ft., the Gantry Y-axis spans16.5 ft., and the raise/lower Z-axis has a 32-in. travel. The A-axis for mitering has a servo-controlled programmable position of 0 to 90 degrees, and a B1-axis for swivel is servo-controlled and programmable for 0 and 90 degree positioning.
A 30-hp variable-speed arbor drive spindle operates at 300--6,000 RPM to power either a 40-in. diameter blade or ISO-40 tool holders for shaping tools, milling bits and flush-mounted blade.
"The control is built on a standard Windows NT platform and an industrial PC with a Pentium processor," says Karl Kleppek, the Siemens Machine Tool representative to Park Industries. "It's supported by a Simodrive 611U drive and Posmo decentralized drive technology." Kleppek argues that a simplified, streamlined approach increases productivity in a broad range of motion control applications for machine tools, including milling, turning, grinding, robotics, material handling, welding operations, presses, laser cutting and more. "PC-integrated control is ideal for applications where PCs are the prevalent choice or where there is a preference for the distributed configuration of the drives and I/Os," adds Kleppek.
With this approach, the NC processor unit required on conventional controls--usually located in the main electrical cabinet,is no longer necessary. The PC processor drives CNC operations, as well as all HMI functions.
Flexibility Achieved
Park Industries believes this PC-based solution has great versatility with the broad range of integration options offered by the Sinumeric product line. In addition, operator functions and machine data are transportable between the various controls, providing an open, plant-wide platform for automation and control.
As an example, using a physical template of a job-site application is the typical way to create finished product in the countertop industry. This template information is transferred into the control, using either a DFX file exchange to the machine or by indicating points on the template using a laser indicator. On the Park Odyssey II and Destiny machines, an operator has the ability to move the machine over the template (full-sized vellum, cardboard or paper, typically) with the MDI to enter locations indicated by a laser cross-hair. As each point is entered along a path, the operator tells the control whether the point is on an arc or a line. Tooling routines, feeds, speeds and entry/exit points are also applied at the control.
More to Come
As a result of the success achieved integrating the new CNC into their premier machines, Park Industries has recently applied similar control solutions on their Jaguar II gantry bridge saw and Yukon automatic diamond saw. Park modified the operator interface to include stoneworking-specific work routines and language by using Siemens' PLC development software.
With some VB enhancements to its new HMI,
Park Industries says it has a control system
that's faster to learn, and easier for stoneworkers
than traditional G-code programming
Siemens trained Park Industries' personnel at its Chicago facility, as well as at the Siemens OEM/HMI Group in Stuttgart, Germany. The training included applications support of the control integration and startup; custom OEM HMI, controller and and drives training for Park Industries' engineering, installation and service support groups; as well as training on Siemens-Weiss custom spindles.
"In fact, adds Penas, "the same application engineers, including those involved in the installation and startup are still available to us today for any problems or questions. All of this support made Park Industries' transition to Siemens a great success."
Park Industries strongly believes they've done the right thing. "The lesson we learned is one we already knew, concludes Penas. "Stay focused on what your customers are really looking for in their machine. Don't assume any design limitations based on what you think can or can't be done right now. Today's control systems are really remarkable in how they can be adapted to fit the job."
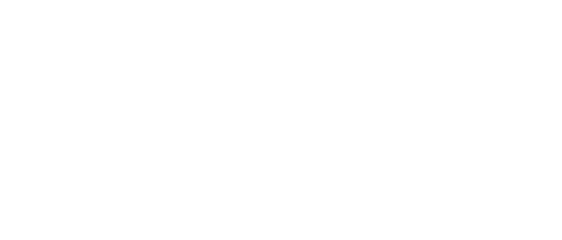
Leaders relevant to this article: