W |
E MAKE PACKAGING EQUIPMENT and use pneumatic linear slides. They've been pretty accurate and we know how to support them. One of our new engineers is all about linear motors and feels we'll have a big improvement in accuracy and reliability, simpler maintenance and increased machine uptime if we re-design. What do you think? -- A CONTROL DESIGN magazine reader
ANSWERS:
Stick With Pneumatics
It's true that a linear motor and especially a linear servo motor would give increased accuracy and might even reduce maintenance downtime. But these benefits will come at significantly increased cost and increased difficulty of troubleshooting when something finally does go wrong. So, do you need the increased accuracy and is the present level of reliability unacceptable?
For simple stop-to-stop motion, it is virtually impossible to beat air-operated linear slides. The only time I would look at electric motor solutions is when there's a need for precise control of speed or endpoint, especially if these parameters need to be changed by software, or where other considerations such as sanitary or cleanroom environment or lack of an air source preclude use of pneumatics.
Kim Ground, Senior Automation Engineer
Surface Finishing Technologies, Clearwater, Fla.
Choose What's Simpler
Linear motors are going to improve your machine's performance in areas or accuracy, speed and flexibility. As far as reliability and simpler maintenance are concerned, there's more to it than a simple component replacement.
If done properly, the linear motor solution will provide simpler maintenance and greater reliability because of the significantly more advanced diagnostic features associated with servo drives. In the event of a problem, the faults generated should pinpoint exactly what happened, and what the corrective action is. With a pneumatic slide, all you know is that it didn't get there in time.
If the application is not done properly, the more complex servo system will baffle the typical maintenance electrician, and the machine might sit idle until you, not your customer, ends up fixing it. There's not a lot involved,from a technical standpoint,to a pneumatic slide, and that helps the untrained technician. Overall, you need to ask yourself which one presents a bigger problem for you: the machine not performing its function, or an external force preventing your machine from performing its function.
Lastly, be careful not to open a Pandora's Box by making the upgrade. You'll need to look at the mechanics of your machine before attempting such an upgrade. Linear motors have the potential to introduce a significantly higher amount of stress and strain to your machine due to the higher velocities and acceleration/deceleration rates. Cable tracks and other wire-management devices will need to be examined for higher velocities and higher fill ratios. Safety systems, panel layouts, etc., will also need to be revisited.
I agree with a move to linear motors from a performance point of view. However, if it is not something that your company can execute or support properly, it might not make sense.
Jason Christopher, Controls Designer
Liberty Precision Industries, Rochester, N.Y.
Do Your Homework
When faced with the decision of choosing between linear motors or pneumatic slides, the first step should be to identify the specific application where the actuator is to be used. Then consider requirements for speed, accuracy, and flexibility. Finally, evaluate performance vs. cost. Select the technology that best fits the application and budget at hand.
Traditionally, linear motors are very accurate with a premium price tag, while pneumatic rodless actuators are affordable with limited flexibility and accuracy. Additionally, linear motors provide higher speeds, which translates to more cycles per minute, and can accelerate heavier loads than pneumatics.
Kjell Lyngstad, Market Segment Manager
Bosch Rexroth Pneumatics, Lexington, Ky.
Linear Is a Viable Replacement
Linear motors and linear stages can accelerate rapidly,as much as 10 g with speeds to 200 in./sec. Linears provide repeatability ranging 1-25 ?m and accuracy of 10 ?m. What performance is needed and what improvements are you trying to attain?
The initial cost of linear motors will be higher compared to pneumatic slides. However, reliability and maintenance should be better. When evaluating applications and costs, be sure to consider a pneumatic slide's long-term costs and take account of air and maintenance costs, replacement parts for worn air hoses, compressors, leaky hoses, and,very important,downtime associated with maintenance. How much of an issue is reliability and maintenance now, and do you wish to improve on this?
Linear motors can provide a big improvement in the application's performance, accuracy and reliability.
John Mazurkiewicz, Motion Control Product Manager
Baldor Electric, Fort Smith, Ark.
Air Is a Variable
The terms "accuracy" and "repeatability" too often are interchanged. The repeatability of a system is important if you are speaking of velocity or position. The position of a pneumatic linear slide system can be repeatable, but typically, its velocity is not. Pneumatic linear slide accuracy typically is not good due to the difficulties of closing the loop around air. Delays, variance in pressure, and the compressibility of air cause issues.
The repeatability of direct-drive brushless linear servo motors is excellent and surpasses that of pneumatic linear slides. The velocity and acceleration of a servo-driven mechanism is a programmed repeatable value. The system will follow the profile time and again.
Velocity and acceleration variances in pneumatic linear slide systems might cause inordinate amounts of wear if extra care isn't taken. This wear can be of the mechanism that is being controlled as well as the pneumatic linear slide itself. The use of valves in the system also requires oil. Usually there are atomizers involved in maintaining an oiled air environment for the valve. With too much oil, the pneumatic slides will have their lubricant washed out causing failure. With too little oil, the valves fail. The oiler is a maintenance issue that is not required for the direct drive brushless linear servo system. With direct-drive brushless linear servo motors, the system reliability is dictated by the bearing life. Direct-drive brushless linear servo motors, like all direct-drive servo motors are zero-maintenance solutions.
In addition, direct-drive brushless linear servo motors can provide higher operating speeds that offer increased machine throughput and reduced audible noise for a quieter work environment.
Lee Stephens, Systems Engineer
Chris Radley, Senior Product Line Manager
Danaher Motion,
Pneumatics Might Be Simpler
When a linear motor is compared to a pneumatic power slide, several issues should be highlighted. A pneumatic slide is designed to carry and support a load and has a built-in drive mechanism in the form of an actuator. A linear motor is purely a drive mechanism and requires additional hardware to support the load. A pneumatic slide requires one or two air valves, a position sensor and a controller to move the slide proportionally between the maximum limits of travel, a system less expensive than a linear motor, load support and controller by as much as one-half to one-third the cost. A linear motor also requires a controller to control the position between the maximum limits of travel. A pneumatic controller is less complicated than the linear motor controller and at comparably lower cost.
Other decision factors include:
Application: If end-to-end travel or proportional motion is required both systems are capable, however, a linear motor may be excessive for an end-to-end application.
Resolution and Accuracy: A linear motor provides higher resolution and accuracy. Does the pneumatic system achieve these goals while remaining cost effective?
Cost of Ownership: The cost of typical maintenance over an equivalent period of time is virtually the same.
System Requirements: Is clean, dry factory air available at the installation? Generally electricity is and sometimes air is.
Vince McCarroll, Chief Engineer
Enfield Technologies, Trumbull, Conn.
Send it along and we'll present it in an upcoming issue of CONTROL DESIGN magazine and on our website. Send visuals, too, or a sketch is fine. E-mail us at[email protected]or mail to The Answer to Your Problems, CONTROL DESIGN, 555 W. Pierce Rd., Suite 301, Itasca, IL 60143. You can also fax to 630-467-1124. Please include your title, company and location in the response.
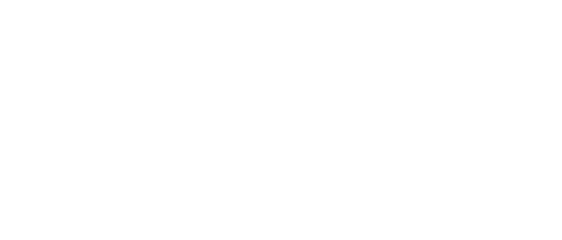
Leaders relevant to this article: