Magnum Hunter Resources Inc. (www.magnumhunter.com), headquartered in Irving, Texas, is an independent oil and natural gas exploration and development company that manages oil and natural gas producing properties for its interest owners. At its Walnut Bend oil field located near Gainesville, Texas, Magnum Hunter subsidiary Gruy Petroleum Management Co. installed a new wireless radio network to overcome interference problems and more reliably control and monitor its wells located in an environmentally sensitive area of the state.
For similar reasons the CO2 Group of Kinder Morgan (www.kindermorgan.com), a leading producer of the gas to U.S. businesses, recently deployed its own wireless radio network. The company’s goal: speed up transmission rates so it could more efficiently manage its SCADA system and tighten control response of the company’s CO2 injection equipment sited in an oil field located in a region known as the Permian Basin near Snyder, Texas.
Both Gas and Liquid
Monitoring and controlling injection operations across 120 square miles of oil field from its facilities control room (See Figure 1) is a daunting task. In the ‘90s, Kinder Morgan relied on employees traveling in trucks to monitor sites, and fielded a large radio network of 200 9,600-baud serial radios. The company also used a very-small-aperture terminal (VSAT) network using satellite technology to monitor and control the wells and CO2 injection equipment.
Out With the Old
As time has passed, the serial radio-based network’s slow communication rate and the weather-dependent, temperamental nature of VSAT prompted the CO2 Group to rethink its wireless control strategy and start looking for ways to improve the performance and reliability of this critical system.
John Ory, the group’s senior facility engineer and Jerry Martin, on-site instrument and electrical supervisor, began working with local integrator Cain Electrical Supply Corp. to migrate the old system to a new wireless SCADA system configured with Schneider Electric Modicon PLCs and a network of solar-powered Locus industrial radios (See Figure 2).
“The Locus radios are field configurable and can act either as a master, repeater or remote radio,” says Martin, who appreciates that he can program that functionality himself in just a few minutes. If one of the repeaters goes down, the units roam automatically to maintain network integrity.
All data collected from the field is transmitted to the master where it is brought into an HMI software package. Martin created all the control screens and technicians can log on to the network from any location to check network health status and other system condition indications.
Walnut Bend Oil Field
The Walnut Bend oil field located north of Dallas was discovered in the late 1930s and produces oil and gas from numerous wells ranging in depth from 2,000 to more than 7,000 ft. Today, Walnut Bend produces approximately 750 barrels of oil per day from 104 wells.
In the 1990s, Gruy Petroleum Management Co. relied on a licensed, 150-MHz frequency radio network to monitor the wells in the field. Over time, the company began experiencing interference and other signal quality problems that were wreaking havoc with its network.
Regional specialist Jeff Walters of Automation Alternatives in Weatherford, Texas, was called in to analyze and diagnose the problem. Using a spectrum analyzer, Walters found the existing radios were operating in elevated noise zones and experiencing power-grid interference, which was causing the system to overload and spontaneously shut down. The radios were unable to differentiate between their own network traffic and the interfering radio signals around it.
An Effective Blend
An interesting and effective blend of technology was used to replace the existing system. Because the oil field’s control and monitoring system is SCADA based, the network had to be free of the interference and noise plaguing the previous low frequency radio network and interrupting operations and. With its advanced frequency hopping and digital signal processing, the 2.4 GHz Locus OS2400-485radios were selected.
Because the Locus units are designed to accommodate multiple protocols, Gruy Petroleum Management Co.’s legacy Schneider Electric and Allen-Bradley PLCs (Modbus and DF1 protocols, respectively) are able to communicate simultaneously across the network. That feature spared the company the expense of creating separate networks and the necessity to purchase more radios to accommodate the separate protocols.
“The new network also eliminates the need for us to pay to maintain our 150-MHz license,” says Gruy Petroleum Management Co.’s district manager Chuck Cheney. The new system transmits both analog and discrete data from all points in the network to the company’s SCADA system (See Figure 3). “All or parts of the field can be shut down by the SCADA system automatically, depending on the nature of an alarm condition, reducing the impact of a process upset,” he adds.
To comply with a number of EPA mandates, the field must be monitored 24 hours a day, says Cheney. “With the new system 24/7 well monitoring is automated and reliable,” he says. “No longer do we have to pay someone overtime to drive to each well and monitor and report its condition.”
Because of the terrain, the radios are configured in both point-to-point and point-to-multipoint repeater configuration (See Figure 4). In this configuration, says Walters, “If a unit goes down, the radios roam to find the next unit. Meanwhile, because the host has lost communication with that particular device, after a set period the exception triggers a countdown timer. When it reaches zero after 30 minutes, it dials out to an attending technician so the failure can be looked into.”
The radio network incorporates 22 Locus radios in a point-to-point, point-to-multipoint configuration. Wells and field equipment are polled every five minutes to check differential pressure and tank levels, injection pressure and flow rates on transfer lines, as well as a variety of discrete alarms. Again, latency is not an issue, nor is network security. Because the oil field is in an environmentally sensitive area, chloride sensors monitor groundwater to alert operators to possible spills.
Environmental Sensitivities
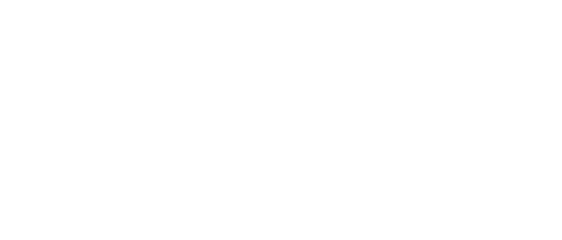
Leaders relevant to this article: