A Reader Writes:
Solutions:
It's the Ratings
www.ul.com/hazlocOne Method for Div. 1
www.microwavedata.comFebruary's Problem
Can We Use IDC Connectors?
Our I/O and terminal block vendor is pushing insulation displacement connection (IDC) technology. It looks slick but we're not sure how it will hold up in the plant. Does anybody have experience with IDC terminations in chemical plant environments? Is there any place they should be avoided? What IDC characteristics should we be looking for?
[email protected].Please send us your comments, suggestions, or solutions to this problem. Solutions will be published in our February issue, but we need your responses by January 6 to meet our editorial production deadlines. If you have a solution to this problem, or a problem of your own that you would like to pose to other colleagues, mail, fax, or e-mail it to CONTROL Problem Solving Ideas, 555 W. Pierce Rd., Suite 301, Itasca, IL 60143; Fax 630/467-1124; e-mail
To install wireless transmitters in a hazardous area, you will need to purchase a wireless transmitter that is certified for a hazardous area. For a complete solution, the wiring and electrical connections for power, radio transmission and transmitters must also be approved for a hazardous location.
...To date the only wireless transmitter that is Class 1, Div. 1 (Group C and D) certified is manufactured by zed.i solutions. zed.i's product, the Smart-Alek System, is specific to gas volume measurement (for more information, see www.smart-alek.com). The device measures static pressure, differential pressure, and temperature as gas flows through an orifice plate. The field data is processed on-board, then transmitted over public telecommunication networks (satellite or cell phone) to a secure central data repository where it can be accessed via the Internet.
...In the process of approval for Class I, Div. 1 locations, zed.i had to submit both the components and the complete installation. In addition, the zed.i system architecture is easily customized to work with most existing automated measurement systems to create a seamless, integrated solution.
Toku Ito, P.Eng., Chief Technology Officer
zed.i solutions, www.zedisolutions.com
Power Is Key
There is a major obstacle to installing a wireless, level-measuring sensor in a hazardous environment. While there are numerous level instruments that are either explosion-proof or intrinsically safe, they require either 24 VDC or 120 VAC to operate. The selection of a sensor is important, but the transmitter (either radio or cellular) must also meet hazardous approvals and the sensor and transmitter need to be battery-powered.
...The first system that we designed used a solar panel and storage batteries mounted in explosion-proof housings with the appropriate barrier. This system powered a 7100 Series magnetostrictive level sensor with an intrinsically safe Class I, Div. 1 approval. While the system worked, it was expensive and had various maintenance problems that related to the solar panel and RF transmitter.
...We decided that this was not a practical solution, and designed a sensor that could be powered by conventional batteries. Once we had the level sensor available, we contacted a variety of companies that were developing 900 MHz broad-spectrum transmitters to establish an alliance. The need was for a transmitter that could provide power for both the radio and level sensor using a conventional battery.
...Our first products were developed for Xsilogy and Signet Scientific, but the system did not have hazardous approvals. Since then, we have developed level sensors for Innovative Sensor Solutions, World Telemetry (subsidiary of LPG Central), and SupplyNet (division of Alert Technology).
...The development of wireless instruments has been limited by the power requirements of the level sensors that are currently available. Obviously, battery life became an issue, and this meant that not only the power consumption of the radio and level sensor were involved, but update frequency had to be considered. For this reason, most wireless applications focus on inventory monitoring that does not need continual updates. With updates every 5 min., new lithium ion batteries will last between two and three years before they need to be replaced.
...While radar and ultrasonic instruments are very popular, their power requirements make it impractical to use them with standard-size batteries for distances greater than 6 ft. In addition, the filtering software used by these technologies to eliminate false signals is not suitable for the low power budget available in a wireless application, unless a solar panel is used. For that reason, the ultrasonic unit available has a recommended range of 6 ft. and the TDR radar is only about twice that.
...In large tanks, either pressure sensors or magnetostrictive probes must be used. When the application requires high accuracy for either distribution or inventory management, magnetostrictive probes offer accuracies of 0.1% of full scale, without calibration.
...There are a few companies that offer wireless level instrumentation with hazardous approvals. Barton has a TDR guided radar sensor and RobertShaw offers both a pressure transducer and ultrasonic unit that meet some type of hazardous approval. The Barton TDR and RobertShaw ultrasonic have limited ranges, while pressure sensors can be used in larger tanks. The accuracy and dependability of these sensors is also limited.
...Ametek's 7240 Series Digital Stik magnetostrictive probe has been used with Innovative Sensor Solutions' and World Telemetry's RF transmitters. Innovative Sensor Solutions offers a complete system, including a SCADA package for tanks up to 50 ft. in depth. It provides excellent accuracy, requires no calibration, and has a Class I, Div. 1, Group C and D approvals. The Data Stik system has been patented and is currently available.
...World Telemetry offers the only wireless level sensor that can be used in underground tanks. This system is also rated for Class I, Div. 1, Group C and D environments. The other companies involved in this market are Simmons and SupplyNet. Both of these companies rely heavily on pressure sensors for their level measurements.
Mike Geis, Director of Business Development
Ametek Sensor Technology, www.ametek.com
Apply Standards
To install electrical equipment in hazardous areas, it must be approved by a recognized certification agency and bear that agency's authorized certification mark. In North America, it must meet the requirements of the applicable CSA or ANSI/UL standards. For hazardous locations, the product must meet the general location standards plus the requirements of the applicable hazardous locations standards.
...The applicable method(s) of protection and hazardous location standard(s) depend on the area classification where the equipment is to be installed (see table). Specifically, for wireless transmitters used in hazardous locations, there are two main concerns: ignition of the hazardous atmosphere via electrical ignition, and ignition of the hazardous atmosphere related to the transmit/receive power of the wireless radiation. Assessment of the electrical ignition hazards would be as follows.
...In Class I, Div. 1, intrinsically safe devices are evaluated to ensure that, even under fault conditions, the equipment does not contain enough energy (thermal or electric) to produce an ignition-capable arc, spark, or heated surface. In most cases, this requires the transmitter to be specifically designed as intrinsically safe. For explosion-proof, the device is placed in an approved explosion-proof enclosure. If an antenna is required and is mounted through the explosion-proof enclosure, it must both maintain the integrity of the explosion-proof enclosure and be evaluated as intrinsically safe. One of the advantages of this method is, except for the antenna, the device does not specifically have to be designed for hazardous locations. The antenna may be addressed with an off-the-shelf safety barrier or by being designed intrinsically safe.
...In Class I, Div. 2, for non-incendive, the entire device is evaluated to ensure that, under normal operating conditions, the equipment does not contain enough energy (thermal or electric) to produce an ignition-capable arc, spark, or heated surface. For "no arcing, sparking, or heated surfaces," the components and assemblies of the device are evaluated to ensure that, under normal operating conditions, they will not produce an arc, spark, or heated surface. Most equipment for use in Class I, Div. 2 would be a mixture of the two methods above, and in most cases, would not require the device to be specifically designed for use in hazardous locations.
...Assessing the transmit/receive power ignition hazards is more difficult. If the power from the antenna is high (how high is not specified in CSA standards) and its proximity to ground or a metal object is close (how close is not specified in CSA standards), arcing can occur, resulting in the ignition of the hazardous atmosphere or harm to personnel.
...Requirements for transmitter power levels and restrictions can be found in some European and IEC standards. These requirements may be used as a guideline for manufacturers and end-users, as well as by certification agencies, to determine the suitability of a device for a particular application.
Dave Adams, Certification Engineer, Hazardous Locations Products
CSA Intl., www.csa-international.org
Intrinsically Safe for Class I, Div. 1
Five years ago, we undertook the challenge of developing a battery-powered, wireless high-level alarm system for petroleum storage tanks. Several states (most notably Florida and Pennsylvania) were beginning to require storage tank operators to install redundant overfill protection systems on their storage tanks. In many instances, the tanks didn't have usable electrical conduit and wiring. In almost every case, it was found that the electrical work required to provide the overfill protection far exceeded the cost of the sensors and alarms. We decided that using non-IS approved devices (located outside the hazardous area) connected to sensors through an IS barrier was not practical or cost-effective.
...We began searching for an agency-approved IS wireless telemetry system; however, none existed. We therefore decided (perhaps somewhat naively) to undertake the development of an intrinsically safe (IS) battery-powered wireless telemetry system. The requirements for this system were:
1. Agency-approved IS for Class I, Div. 1.
2. Field-mounted transmitters must operate on batteries for at least two years.
3. Real operating range of at least 1-2 km.
4. Operating temperature ,40-60 C.
5. High immunity to obstructions, RF interference, and atmospherics.
6. Failsafe and fully supervised operation (alarms for inactive transmitter or low battery).
...Our resulting FillCheck system (U.S. Patent No. 6,229,448) was developed after considerable time and expense and is now in wide usage for virtually any application where discrete inputs (i.e., switches) are required. This includes, of course, level switches, but has also found many other uses wherever the transmission of discrete inputs is required.
...As the FillCheck system gained industry acceptance and our customers gained confidence in its reliability, they began to urge us to increase its I/O capability. We decided early in our corporate evolution that wireless technologies were exploding and to be successful, we needed to stay focused on our core applications; namely, hazardous areas. Consequently, all of our wireless products are IS and battery-powered to permit fast, easy and cost-effective application in hazardous areas.
...The challenge now was to increase the I/O capability without sacrificing long life battery operation. Fortunately, some highly efficient microcontrollers (which were developed specifically for battery-powered devices such as PDAs and video games) were becoming commercially available, and with the help of some ex-TI engineers we were able to integrate one of these with our transmitter.
...Last year, we introduced our DataCheck line of wireless transmitters (U.S. Patent No. 6,369,715). Three models are offered: Model S allows communication with virtually any serial device, Model P allows pulse input, and Model A provides 2 separate ADC channels which can be configured for either 0-20 mA or 0-5 VDC input. All three models also provide several discrete inputs as well. One additional feature of DataCheck is an intrinsically-safe 6 VDC output that can be programmed to power external IS devices with the proper IS entity parameters. The frequency and duration of this output can be configured to switch on external sensors connected to the transmitter, collect the data for transmission, and then switch off the power.
...We are now using the versatile DataCheck platform to develop a line of IS, battery-powered, wireless sensors. To accomplish this, we are partnering with other sensor manufacturers who have sensors with power requirements that can be handled by DataCheck's external powering port. In our first venture, we worked with Ametek Sensor Technology to develop DataStik, the first IS, battery-powered, wireless automatic tank gauging system. We are currently working with other sensor manufacturers to develop additional DataCheck-integrated self-contained IS battery-powered wireless sensors.
...I would be quite derelict if I failed to mention that without the advancements in lithium ion battery technology, none of these new IS battery-powered wireless products would be possible. With an operating temperature range from ,55-85 C and 10-year shelf life, they have opened sensor and telemetry possibilities that were truly unthinkable in the not-too-distant past.
J.L. "Larry" Taylor, III, President
Innovative Sensor Solutions, www.innovative-sensor.com
Use Industrial Equipment
Wireless connectivity offers many benefits, and the ability to operate in hazardous locations is one of them. A product that has been tested for specific risks such as fire or shock will perform most safely in a hazardous location. One of the most common approvals for electrical equipment comes from Underwriters Laboratories (UL), whose standards are widely accepted around the world.
...There are several UL classifications that can certify an electronic device, such as radio, for use in hazardous locations. A wireless solution that is not certified to these standards can pose a serious risk if operating in a hazardous location, such as a blasting site or gas installation. When a device makes or breaks an electrical connection there is potential for a spark, which could lead to fire or explosion. For example, a spark could result from a power connector being accidentally pulled out with power applied. Utilizing a wireless solution with a locking power connector or a screw-lock connection eliminates this risk and should be part of any installation in a hazardous location.
...UL is widely accepted around the world as a recognized safety standard, however, there are other standards-based organizations in most countries whose additional approval may be required in order for a wireless device to be marketed or used.
...While the ability of your wireless device to operate safely in a hazardous location is important, another advantage to deploying a wireless solution in a hazardous environment is the ability to keep site visits to a minimum, thereby limiting the risk involved for technicians and field crews. An industrial wireless solution tested to extreme temperatures and able to withstand rugged, dirty RF conditions may out perform a wired solution in a hazardous environment.
...A perfect example of this is a recent encounter of the MDS iNET 900 with Hurricane Lili in October. Routine upgrades were being made remotely to the MDS iNET, which happened to be directly in the hurricane's path. The ability of the radio to withstand a natural disaster and continue functioning as if it were in an ideal environment illustrates the importance of using an industrial solution.
Deanna DeFisher, Marketing Writer
Microwave Data Systems,
Before implementing wireless transmitters in hazardous areas, it is necessary to define the area. Instrumentation commonly used in factory automation and the process industries typically requires adherence to UL Class I, Div. 1 or 2. For areas where ignitable substances such as gases, vapors, or liquids are likely to exist only under abnormal conditions, as classified under Class I, Div. 2, instrumentation rated for the area should not require an explosion-proof housing.
...For areas where these substances can exist under normal conditions, as classified under Class I, Div. 1, instrumentation must be either contained within a suitable explosion-proof housing, contained within a suitable purged housing, or rated as intrinsically safe.
...Wireless products are available with Class I, Div. 2, Groups A, B, C, and D ratings that can be incorporated into this type of hazardous location without the need for expensive explosion-proof housings, for example, our new OS2400-485 spread-spectrum wireless radios and 9xxMB Modbus I/O Products. However, if the area is classified as Class I, Div. 1 and the radio is not rated as intrinsically safe, then a special housing will need to be considered as
referred to above.
Rob Frewald, Process Products Sales Engineer
Acromag, [email protected]
All in One Box
In the U.S., the National Electrical Code (NEC) covers the requirements for electrical and electronic equipment and wiring for all hazardous locations. Different approval agencies have different standards to evaluate equipment installed in hazardous locations. For example, ANSI/UL 913 is the Underwriters Laboratories (UL) and American National Standard (ANSI) standard covering intrinsically safe apparatus and associated apparatus for use in Class I, II, and III, Div. 1 hazardous locations.
...In general, in a Class I environment, you can use explosion-proof, purged and pressurized, intrinsically safe, or non-incendive techniques to install equipment in hazardous locations. Due to the nature of the performance and power requirements of radios, it is very difficult to get an intrinsically safe Class I, Div. 1 radio. However, if you install a radio in an explosion-proof enclosure, it is very difficult to get the RF signal to the antenna in a Class I, Div. 1 environment.
...We have extensive experience installing equipment in hazardous locations. By using special techniques in integrating a spread-spectrum radio and a smart multivariable transducer, our AutoGraph wireless transmitter can be installed in a Class I, Div. 1 environment. A single box will contain the flow computer and communications equipment as well as power components. Directly mounting the flow computer on the meter run with all necessary components in one box eliminates the cost of additional housings, as well as associated cabling and barriers.
King Poon, Vice President of Engineering
Thermo Electron, www.thermo.com
In a Word, Plastic
Our products have been certified for use in Class I, Div. 2 areas in North America. If your application is in a Class I, Div. 1 area (or in other countries), you can wire out of the Div. 1 area to a Div. 2 area, or use a "flame-proof" or a pressurized/purged enclosure inside the Div. 1 area.
...Non-metallic pressurized enclosures are ideal for wireless applications, using a small whip antenna inside the enclosure. The non-metallic box decreases radio range, but not significantly.
...With flame-proof enclosures, an external antenna is required. The antenna is connected to the wireless unit by a length of coaxial cable. An antenna is a passive element like a wire, and requires protection against mechanical abuse like a wire. Mounting the antenna inside a heavy-duty PVC pipe is a common way of achieving this requirement. The PVC pipe reduces radio range, but again, not significantly.
Graham Moss, President
Elpro Technologies, www.elprotech.com
Mesh Means Robust
Hazardous areas are increasingly being targeted for wireless communications as wire-based communications solutions can be sub-optimal due to the difficulty of getting to these areas and the costs associated with the installation. But many of these industrial environments prove difficult for RF-based solutions due to interference from motors, steel tanks in the environment, or other wireless communications such as radios.
...Recently vendors have begun to embed wireless networking solutions within their sensing and control devices, making it easier to deploy wireless transmitting/receiving devices in difficult environments. The sensing and control devices, such as temperature sensors integrated with wireless communications, are simply deployed and the wireless device identifies its location in the network and puts itself into operation.
...The most currently available, optimal wireless solutions operate in the license-free spectrum ISM band of 915 MHz and employ mesh networking algorithms for a highly robust and reliable communications network in difficult environments. With each node serving as a router and repeater, mesh networks have the ability to intelligently route data around interference and challenging RF conditions to ensure the data reaches its destination, eliminating the problems associated with point-to-multipoint "star" topologies and single-point-of-failure issues.
...In addition, these solutions need to automatically recognize new nodes in the network and self-organize without node-by-node configuration, to minimize human exposure or intervention in such hazardous environments. Our EmberNet products are one such solution.
...With embedded wireless networking products, the sensing and control manufacturer will have gone through the proper certification channels to ensure the products achieve the requisite certifications for the intended environments. For Class I, Div. 1 certifications, there are a number of standards including BS EN 50020 and UL 913. BS EN 50020 is British and more stringent than the American UL 913. UL 913 is expected to shift to become more similar to BS EN 50020.
Olivia Hecht, Director of Product Management and Marketing
Ember, www.ember.com
Eliminate Explosion-Proof Conduit
New technology is enabling greater use of spread-spectrum radio for monitoring and control in industrial environments. Today, spread-spectrum can securely move small amounts of sensor and control information from a transmitter measuring flow, level, pressure, temperature, etc., even transmitting mission-critical information through heavy interference. The most efficient interference-tolerating technology for such applications is frequency hopping (part of spread-spectrum).
...The maximum allowable transmit power according to the FCC is 1 W for a frequency-hopping spread-spectrum device. The devices can be connected directly to a transmitter located in a Class I, Div. 2 hazardous location and can send the signal 600-1,000 ft. in-plant in harsh industrial conditions, eliminating the need for wire, conduit, trenching, and all associated labor. No setup, configuration, or software is required. Simply plug in, power, wire the transmitter or signals to it, and get it out on the other end.
...However, the 1 W maximum transmit power and the circuitry around it is used to achieve the distances and tolerate interference levels, but is high enough to pose a problem with applications in a Class I, Div. 1 area. In those areas, the device can be mounted in a supplied explosion-proof housing with a clear window. The propagated radio signal can penetrate through the clear window to a receiver in the safe area. This method eliminates the need for additional explosion-proof conduit systems, seals, glands, and associated labor.
Davis Mathews, Instrumentation Product Manager
Phoenix Contact, www.phoenixcon.com
Now Testing a Trick Antenna
We have run into this problem frequently and decided to tackle the problem by developing an antenna that would be able to pass the rigorous certification tests.
...For a starting point we chose the 2.4 GHz Mobile Mark body-mount antenna because of its rugged construction for vehicular applications. This antenna can be manufactured with a solid two-piece aluminum mounting base and Radome containing the radiating element.
...The RM3-2400 antenna was redesigned to allow a coaxial cable to be routed through the mounting base and internally sealed using fibrous packing and approved conduit-sealing compound. The bottom side of the base has a plug that further seals and secures the coaxial cable. This is an accepted method of preventing gases from leaking inside the housing through the antenna-mounting base.
...A Radome containing the radiating element of the 2.4 GHz or 900 MHz antenna is threaded and securely screwed onto to the aluminum base section with a proprietary sealant cement securing the two pieces. The base of the antenna has a 3/4 in. NPT fitting, containing the feedthrough, for assembly into a hub on the top of the housing. The figure shows the prototype Model RM3-2400 explosion-proof antenna attached to an Adalet XIHL explosion-proof enclosure.
...Although our antenna is still in the final design stages and has not been certified at the time of publication, I hope that readers find it helpful.
Ed Rasmussen, President
Tekcomm, www.analynk.com
Look for the UL Label
In addition to the UL ordinary locations/general purpose standards that may apply, and the installation requirements per the local Authority Having Jurisdiction (such as ANSI/NFPA 70, "National Electrical Code" Article 500), the node(s) should be evaluated in accordance with the following UL hazardous locations standards and their protection method philosophies briefly described below. Readers may wish to refer to www.ul.com/hazloc first to familiarize themselves with the different protection methods, standards and area classifications noted in this article.
...It may be difficult to place the node, antenna and all, inside an explosion-proof enclosure and have it perform as desired with other nodes. But it could be possible to evaluate the node's enclosure as explosion-proof, or obtain an appropriate UL-certified explosion-proof enclosure suitable for the location, so the node could be placed inside. This enclosure would most likely be evaluated to ANSI/UL 1203, "Explosion-Proof and Dust Ignition-Proof Electrical Equipment for Use in Hazardous (Classified) Locations." In this scenario, any atmospheric ignition caused by the node would be contained within the enclosure and not propagate into the surroundings. (The same argument would apply to Class I, Zone 1 Flameproof protection in accordance with ANSI/UL 2279, "Electrical Equipment for Use in Class I, Zone 0, 1 and 2 Hazardous (Classified) Locations.")
...A more viable choice for Class I, Div. 1 hazardous locations may be to have the node evaluated as intrinsically safe per standard ANSI/UL 913, "Intrinsically Safe Apparatus and Associated Apparatus for Use in Class I, II, and III, Div. 1 Hazardous (Classified) Locations." The intrinsically safe method achieves its protection by evaluating, and more importantly limiting, the potential energy of the node under electrical fault conditions so that the specific atmosphere or group of atmospheres the node is located in is not capable of being ignited by a possible spark from the node. An evaluation per UL 913 would also allow the node to sit openly and transmit without the interference of being in a thick-walled enclosure. (The same argument would apply to the consideration of using the Class I, Zone 0 or 1 Intrinsically Safe protection methods in accordance with ANSI/UL 2279, "Electrical Equipment for Use in Class I, Zone 0, 1 and 2 Hazardous (Classified) Locations.")
...In addition, the possibility of the node being used only in Class I, Div. 2 hazardous locations should be addressed. In this case, the protection method used for evaluating the node would be Non-Incendive per UL 1604, "Electrical Equipment for Use in Class I and II, Div. 2, and Class III Hazardous (Classified) Locations." Though this method of evaluation would also evaluate the potential energy in the node as in the above intrinsically safe method, it does not limit the energy nor does it consider the potential energy under the electrical faults introduced during the intrinsically safe evaluation. Instead, this method evaluates the normally sparking parts as well as the possibility of shorting or grounding exposed electrical circuits (such as the antenna), and their ability to keep the ignitable atmosphere out of the electrical contact area, or by the parts not having enough energy under normal conditions of use to ignite the hazardous atmosphere. This type of evaluation would most likely also require an evaluation of the combination of the node and the device it is installed with, not just the node itself. (The same argument would apply to the consideration of using the Class I, Zone 2 Non-Incendive protection method in accordance with ANSI/UL 2279, "Electrical Equipment for Use in Class I, Zone 0, 1 and 2 Hazardous (Classified) Locations.")
...There are currently many radio/modem devices that are UL-certified under the intrinsically safe and non-incendive protection methods. Many of these devices involve process control applications located near pipelines, furnaces, etc., gathering temperature and pressure information and relaying it back to a central computer via antennas.
Jason Frieders, UL HazLoc Project Engineer
Underwriters Laboratories,
We would like to use wireless communications to add points, but many locations are in hazardous areas. Does anyone have experience doing this? Does it have to be explosion-proof? Are there any standards we can reference?
-From October 2002 CONTROL
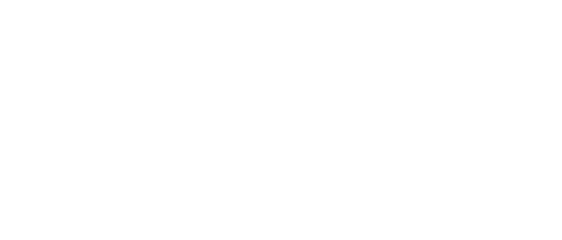
Leaders relevant to this article: