N |
o matter where their machines land in the global manufacturing landscape, industrial robot and production system designers all stand on common design and specification ground when it comes to cabling. To many, cabling may seem pretty mundane. But it’s a big deal when machine reliability and production throughput are all inexorably “connected” to the cabling that transfers network data, control and sensor signals and power to points across a production machine or robotic system.
System designers agree that poorly specified/low-quality cabling can be a chronic cause of machine failure and line downtime. You’ll also learn from them that cabling quality and reliability have come a long way. Ten to fifteen years ago, cable problems caused as much as 30–40% of downtime events in high-flex operations. Today, cables that would likely last about two years of duty are now lasting nearly the life of the machine. This article takes a look at how far the technology come.
It’s a Hard-Knock Life
It starts with system cabling’s ability to function in myriad environmental conditions from hot to cold, wet to dry, while being immune to flying sparks, potent chemicals, washdowns and other harsh conditions.
Robotic systems are being tasked to do increasingly more complex tasks in challenging industrial environments. That means the demands on the cabling that delivers power, data signals and networks are greater than ever. With advances in materials and design, cables are now tough enough to handle it.
Then one has to consider a cable’s ability to handle the dynamic torsional and linear stresses at work as they twist, bend, stretch and flex through millions of cycles. Automotive manufacturers in particular have embraced robotic production systems to automate manufacturing and assembly procedures. Suppliers such as ABB and Fanuc Robotics have developed machines that employ a complex range of motions to accomplish critical tasks in the production setting (Figure 1). For these kinds of systems, design engineers have much to consider when specifying cabling for their designs.
Experience counts and Bob Frease, staff engineer for Fanuc Robotics has several decades of it, providing vehicle and other manufacturers with reliable robotic production systems. “We first determine what the machine has to do. From that point we look backward and start taking into account a number of factors,” he says.
Frease points out that in robotic applications, cables engage applications from power cables to motors and drives, to communications with separate encoder and feedback links. “Some cables have to be intrinsically safe (IS), then there’s grounding, as well as high-voltage power service to other processes such as end efectors on welders to consider.”
Frease says Fanuc engineers analyze the environment and the machine’s intended duty carefully as well. “Then we look at national standards such as NEC and other relevant application and safety standards,” he adds. “What it boils down to is the cables have to be able to defend against the environment and stand up to the types of motion they will encounter as it functions.”
He also identifies the usual plant environmental issues, i.e., those that can affect the jacketing on the cables he specifies. “Robots, especially in automotive applications are doing much more,” he says. “They’re operating in places where oils, paint solvents, inks and flash can attack jackets , while other units must operate in ‘exotic’ environments with high levels of UV and other radiation, extreme cold and even vacuum.”
Clean to the Extreme
Another production dynamic is the environmental condition required to manufacture in extremely clean environments. While cabling in clean or sanitary environments (chip fabrication, food processing, electronics) isn’t likely to be subjected to severe conditions such as sparks or chemicals that can damage or degrade materials, it can’t shed particulate that can contaminate the working area.
To provide a solution to one of its customers, a Korean distributor sought a certified clean room cable that also was suitable for a high-flex cable track application. According to cable supplier Kabel Wächter Gmbh, there was no such product on the market—until the company’s engineering department designed special cabling to fill this need. “We use a polyurethane that is highly resistant to abrasion and features a sharply minimized fraying rate (the loosening of particles as a result of pressure and abrasion),” says Michael Andris, product manager for Kabel Wächter. “The production takes place under very clean conditions and there are no airborne particles such as talc, releasing agents or lacquer wetting inhibitors to be found in this cable.”
According to Andris the cable is especially valuable to users looking for properties such as resistance to oil grease, coolants and other lubricants,. It’s halogen-free, flame-retardant and can be employed in demanding motion applications.
The ability of cabling to withstand conditions served up by a given industrial environment is only part of the story. It’s what’s inside that counts, and according to Frease, cable suppliers have learned a lot about the internal dynamics of cables under motion and stress.
“Everything has to work together,” Frease points out, “especially in long-track, high-motion applications where cables have to slide and release repeatedly to relieve built-up tension themselves.” He describes an action known as “knurling” that can occur when multiple cables with different surface friction characteristics ride up and pull at each other, stretching and bunching until something has to give. “In a way, it’s like arthritis—cables pull, bunch and stiffen up until something fails.”
Suppliers employ a number of tactics that ensure individual cables can slide and move together over thousands of cycles and not bind or build up friction and heat—conditions that lead to premature failure. Depending on the duty and application, talc is used and mylar and cellophane wraps are popular. But compromises always have to be made. “Teflon is a good internal lubricant when heat is an issue, but mechanically it’s not as good as some other choices,” says Frease, offering an example of the trade-offs robotic system designers consider when specifying cable. Some cable designs may also include fillers, and for some specific applications, may include an inner jacket and some type of shielding.
Ethernet for Example
Communications and control network cables must be shielded from a variety of ambient electrical noise to ensure trouble-free transmission of data and signals. Mike Coalardo, vice president of operations for robot builder ABB Robotics North America sees much more reliance on fieldbus and DeviceNet-enabled control networks on the robotic manufacturing lines of his customers. “Most are fieldbus, and with our spot-welding equipment there’s a lot of high-current power passing close by. There’s much more than just I/O to worry about now.”
Ethernet is fast becoming a preferred industrial control medium, but in the real world what is fine for the office has proved woefully inadequate for plant-floor application. “Commercial-off-the-shelf (COTS) Cat 5e unshielded twisted pair (UTP) Ethernet cable is quite fragile,” says Brian Shuman, senior product development engineer for Belden CDT Electronics Div., which manufactures industrial cabling of all types, including an extensive line of ruggedized industrial Ethernet cables.
“Beyond the obvious physical hazards to the cable are the more insidious hazards of electromagnetic interference (EMI) and radio frequency interference (RFI).” Shuman says the best strategy is routing cables away from sources of interference such as arc welders and AC drives. But for many contemporary robotic and motion-intensive production systems, that is simply not an option.
“One option,” says Shuman, “is to use fiberoptic cable, which is absolutely immune to the effects of EMI and RFI. However, if you are concerned about cost, complexity and the reliability of fiber, consider a shielded Cat 5e copper cable solution. Even a simple aluminum foil shield, when properly grounded, provides significant immunity to EMI and RFI.”
And proper grounding is the key to effective cable shielding says Shuman. Missing or inadequate grounding can degrade the shield effectiveness. “Ideally, the shield should be grounded at only one point,” he explains.
Physical issues can affect the signal quality of Ethernet cable as well says Shuman. “Pulling commercial-grade UTP with excessive force will stretch the cable,” he explains. “You may start with 100 feet of cable and end up with 100 feet, two inches. This elongation causes excessive signal loss or attenuation, and signal delay—effects that can limit the distance cable can be run.”
But Wait, There’s More
Many control system designers now push control electronics and other embedded systems closer to points of operation. For designers at Adept Technology, a robotic production systems maker that specializes in fine-motion technologies, the trend exerts a great deal of influence on cabling choices.
According to Keith Bailey, Adept’s director of product marketing, the need for cabling that handles higher and higher data rates has lead them to explore new cabling technologies. “We constantly look for cabling that allows higher data rates while supplying better noise immunity and other electrical characteristics,” says Bailey. He explains that since Adept’s designers are taking a distributed approach to control on their machines, crosstalk and capacitance characteristics are all very critical. Does that mean industrial Ethernet? “No,” says Bailey, “we use FireWire. It’s very robust and has the noise immunity and electrical characteristics we need.”
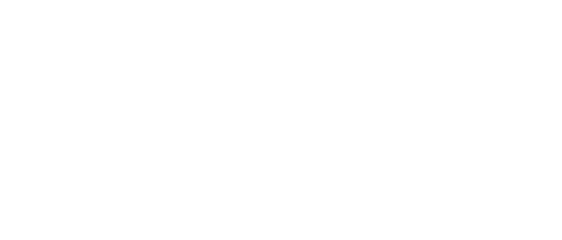
Leaders relevant to this article: