S |
afety system developers, especially those that supply the automotive industry, continually evaluate available new technologies in hopes of staying ahead of the evolving safety regulations curve. Sterner Automation, a Toronto-based engineering firm that specializes in custom testing machinery and end-of-line test calibration equipment, is one company that is fully aware its safety testing equipment can save lives. Because its products play such a critical role, Sterner believes that simply meeting its customers expectations is just not good enough. The company also believes that a switch to the right control platformat the right timecan make a good solution better.
Sterner recently went hunting for an alternative to the PLCs and motion-controllers it uses to automate a machine that calibrates and tests in-vehicle safety sensors for automotive industry applications.
What it found was a PC-based solution that met its expectations in both machine performance and enhanced customer support capability.
Test Time
The Sterner machines test process begins by conveying a car seat (traveling on a pallet) into a testing station. A scanner reads its barcode for identification and a factory information system (FIS) uses that information to determine the right recipe for the proper testing and calibration for each type of seat.
After the seat and its pallet are lifted and locked into position, the test and calibration operator passes through a system-disabling light curtain to connect a harness to the seat. The operator then steps back through the light curtain, returns to his station and resumes the procedure. During the calibration test, the control system communicates to the seats electronic control unit (ECU) using a vehicle communication protocol interface unit manufactured by Sterner.
The sensors the machine tests and calibrates determine the weight of, and the acceleration force on the vehicles passengers and drivers.
The "butt formthe element of the Sterner machine that's lowered onto the seatapplies varying degrees of weight. This tests the sensors to make sure the safety system will differentiate between the weight of an adult and that of a child. This is important because the force of an inflating airbag can injure a child if it is designed solely to have enough force to prevent an adult from striking the dashboard.
When the calibration process is complete, all tooling and test equipment is retracted, the operator disconnects the test harness and steps clear of the light curtain, and the conveyor is signaled to move the seat out of the testing station.
NO BUTTS ABOUT IT
The "butt form" applies varying degrees of weight to the seat. This tests the sensors to make sure the safety system can differentiate between an adult and a child by weight.
Sterners engineers realized they needed a refined control solution that would allow remote monitoring of machine performance, while reducing the training and maintenance costs incurred by its customers. Sterner also sought to decrease assembly time and simplify the hard wiring and connections required in the machines."At the time, we were applying a typical PLC architecture along with either an industrial PC running an operator interface package or a simple touchscreen display, says Victor Hilario, manager of the Electrical and Control Systems Group at Sterner. We were determined to take the next technology steps and design a system that would ultimately be more flexible and allow for a more seamless design evolution. We felt a PC-based system would allow us to enhance the remote diagnostic and troubleshooting capabilities of the product, while staying within industry-accepted standards for programming.The PLC-based system also had relatively limited memory for historical equipment data. Sterner wanted to design a system that would provide its engineers and technicians with months of test data including detailed machine diagnostics information. This information is extremely valuable because Sterner can use it to provide customers with superior preventive maintenance and service support by improving the ability to troubleshoot faults based on past events, as well as conduct more thorough fault and failure analyses with better operational data. Sterner considered the possibility of developing its own proprietary PC-based solution. Ultimately, we realized we didn't want to offer an overly proprietary solution that would limit our ability to program effectively, says Hilario.Just What We Needed
As the hunt for a new control solution continued, Hilario attended a Beckhoff Automation technology seminar. He was drawn to Beckhoffs open IEC61131 programming package, which defines five different languages for programming logic control systems. Many people are comfortable with Ladder Logic, but Ladder doesn't lend itself to some of the functions we have on our machine," states Hilario. "The IEC61131 approach allowed us to apply the appropriate language to the algorithms we were writing and create code that is cleaner and easier to maintain. Sterner engineers designed a system around a Beckhoff industrial PC with Profibus and SERCOS network cards, TwinCAT NC point-to-point software, SERCOS servo drives and Profibus I/O. For sensor connection, they chose bus-terminal I/O and rugged IP67 fieldbus module I/O. (See Figure 1) "Fortunately, says Hilario, the engineers on my team had previous experience working with IEC61131. This gave us a running start on the project."
THE PC SOLUTION
An industrial PC and fieldbus technology centralized all controls, eliminated the PLC and tied into customers plant networks.
According to Hilario, Sterner selected Profibus because of its integration capabilities. "We were able to use an SMC Profibus valve bank and an HMB load cell amplifier, as well as bus-terminal I/O and fieldbus boxes to create one integrated, high-speed I/O network, he adds.The network connection technology also lends itself to making the machine more modular. We reduced the overall component count and were able to maximize our hardware panel space rather than wasting that space on additional terminal blocks for intermediate connections, claims Hilario.Having saved 80â100 terminations, Hilario says Sterner achieved a 30% reduction in I/O wiring due to terminating signals directly to field I/O stations (distributed I/O). This also made our electrical drawings less complex because sensors and actuators were terminated directly to the cards, requiring fewer cables and terminal strips, he adds.Smooth Ride Ahead
With this PC-based control solution, Sterner is now able to provide its customers with a wealth of test and calibration data. Using some of our standard Visual Basic modules, we were able to build our own HMI front-end complete with a data-logging system, says Hilario. A buffer of files stored on the PC allows us to provide several months of detailed historical machine and process data. We also can provide a good read on the current health of our machines and assist our customers with preventive maintenance. In addition, alarms or faults, including the sequence of events that lead to them, can be examined easily from halfway around the world. If customers encounter an issue, Sterner technicians can dial into the PC to extract and analyze the testers log files to provide an accurate, timely root-cause analysis. Weve been able to quickly diagnose and resolve any system issues and ensure that our customers continue to meet their just-in-time production commitments, states Hilario. This allows us to provide our customers with unparalleled service and support while saving the expense and time of flying technicians all around the world for on-site support. This is a key service for our customers, because we can now resolve issues much faster.
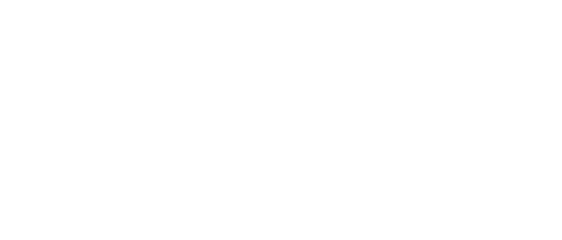
Leaders relevant to this article: