Author
Rich MerrittThe survey results clearly show that you overwhelmingly prefer PLCs and PCs to hybrid controls, custom controllers, and "other solutions," which include CNCs, FPGAs and relays. Over the past few years, you have slowed the development of your own custom control systems. It’s likely that the 20% of you who report using custom control systems are simply getting the last few miles out of old systems developed years ago.The numbers add up to more than 100%, because many machine builders use both PLCs and PCs, depending on the machine or application. "We've always used PLCs and PCs," says David Schoenly, control engineer at VAI. "The PLC is used to control the equipment and the PC is used as an HMI."VAI builds metal processing machines. "The machines are large, about 1,000 feet in length," says Schoenly. "They are used to process metal in strip form. The processes include uncoiling, welding, shearing, cleaning, annealing, application of zinc coating, rolling, application of dry lube, side trimming and recoiling. These processes can be combined or supplied on an individual basis."Nick Merriwether, a control engineer at Integrity Machinery, also specifys both PLCs and PCs for his comany’s packaging and food processing machines. "We use a variety of PLCs and some PCs," he says. "Most of the packaging is PLC. Some of the processing is PC-based, mostly the high-speed color sorters."Some respondents just use PLCs, some just use PCs, and some use both, but almost nobody uses hybrid controllers, which are supposed to be a blend of PLC and PC capabilities. Some market researchers call these "programmable automation controllers" (PACs) and some vendors call them hybrids, but you don't seem to call them anything at all. Only 8% of our respondents claim to use them as a control platform. Some of you tried hybrids, and went back to PLCs.Decisions, Decisions
It appears that machine builders don't make decisions about their control systems lightly. But when they do, they stick to it. A whopping two-thirds of respondents have been using the same control platform for more than five years. Only 5% made a change in the past year. System integrators and custom machine builders are part of that 5%, because they build all kinds of machines, can tailor a control system to a particular application, and can use the latest and greatest equipment. "New technologies allow better control in a smaller package," says Greg Kempfer, controls engineer at M.C. Dean CIM Associates. Kempfer has built just about every kind of machine control system there is, starting with relays."I work for a rather large integrator, which has exposed me to a greater variety of machinery as we meet the control demands of our clients. It also allows flexibility as demands change. For example, modern controllers let us make changes to a machine to enhance its capabilities with minimal changes to the hardware."A machine builder who has a product line of robots, material handing equipment, sheet-metal processing machines, packaging equipment or machine tools, has to be more selective.This kind of machine builder must amortize its investment in a particular control system over several years. The builder must choose a control system that is flexible enough to support several different products, be able to upgrade the controls when necessary, and support the control system in the field. Small wonder that machine builders try to standardize on a single platform.Packaging machine OEM Rovema traditionally supported three different control systems, each from a different supplier. According to Travis Holley, director of engineering at Rovema, this posed a real challenge. "With multiple control systems, we were sometimes unable to make changes in a timely manner and could not provide full support for our machines with internal resources," he explains. "When a customer requested maintenance or upgrades, we often had to wait for the supplier to respond."When Rovema wanted to expand its product line, it realized it needed to standardize on one control platform across all its products. In 2000, it launched a new packaging product based on a hybrid controller; in 2002 it standardized on the hybrid controller; and it has since put the controller on eight product lines. "If we continued to try to support multiple control systems, there's no way we could have expanded our product line with the same staff," Holley says. Price not a Driver
It appears that machine builders don't select a control platform on the basis of cost. Of the choices offered in the question "Why did you change?" the cost of hardware and software licenses were deemed least important. "Price always is a factor in purchase decisions," says Mike Miclot, Logix marketing manager, Rockwell Automation. However, many customers are beginning to look at total cost of ownership data, and making purchase decisions based more on productivity and consistency gains, and less on bill-of-material costs. The machine builder can save tremendously in areas such as reduced design time, reduced implementation time, and reduced support time and incident frequency."Most important to machine builders were "ease of use" and "more capabilities," followed by "customer demands." There was a notable exception however with one reader responding: "We are in the textile business, so cost is everything these days."For some, customer requests and the competition dictated change. "Market pressures demanded that we use controls with better graphics on the operator interface," says Reggie Doddy, control engineer at Milacron. Doddy is responsible for controls on extruders. "Our previous control interfaces were black-and-white screens with text and pixel graphics. In addition, the control hardware was being phased out." Milacron changed over to a combination of PLCs and PCs. It went to PLCs more than five years ago, and to PCs three years ago.Regarding Hybrid Controllers
Whenever we do a control platform article like this one, it simplifies the discussion to outline what we think a hybrid controller is. On the process control side, the answer is easy: It's a PLC that has all the functions needed for batch and process control, so it can perform both logic-type machine control and analog-type continuous control functions. But the answer for a machine builder is not quite that simple.Defining a hybrid controller as a PLC with PC functions, or one that combines logic with motion control, is not enough, because almost all modern PLCs have such capability. Perhaps “hybrid” controller is just another marketing term that machine builders tend to ignore; if so, that might account for its low scores. In other words, to some machine builders, all PLCs are PLCs, including those designated as hybrids.Rockwell Automation's Mike Miclot says the company’s hybrid system bridges the gap between machine controls and the business world. "There is a shift toward multidisciplinary control," he says. "such as solving sequential, motion, process, drives and safety applications, all from a single platform. And, as manufacturers add and augment PC-like attributes to control systems, it will increasingly be viewed as a data epicenter that allows for greater collaboration with business systems."Tri-Way Manufacturing builds machine tools for automotive suppliers and manufacturers. It got a job from General Motors to build an eight-station dial table machine used to produce left and right aluminum rocker covers (Figure 1). As often happens with GM, the automaker dictated the equipment to be used, including the controls. The spec included Allen-Bradley’s ControlLogix hybrid controller. "Although we've been a Rockwell Automation customer for 25 years, we didn't have any experience with ControlLogix," says Ray Weldon, controls engineering manager at Tri-Way. "We were apprehensive about the amount of time it would take to get the system up and running—it can take more than a month to implement a new control system and we weren't thrilled about dedicating that amount of time."Miclot says hybrid controllers are a result of organizations moving from traditional “home-grown” control systems—including PC-based—to adopting off-the-shelf solutions. "One of the benefits they gain is that they no longer have to play system integrator," he says. Tri-Way got the system up and running in two weeks. "The ease of integration and flexible connectivity of the platform allowed us to use four different communication networks in one machine, a task we'd never attempted before," says Weldon. The machine supports Ethernet, SERCOS, ControlNet and Remote I/O. It also uses two processors, one for motion and one to control the loading and unloading robots.PLCs Forever
Machine builders have been using PLCs seemingly since the beginning of time, and that trend shows no signs of letting up. PLCs are like Ethernet—they've been around forever, under attack by various competitive technologies since Day One, and continue to evolve faster than cockroaches.And, like Ethernet, no matter what momentary advantages the competition comes up with, a PLC will develop the necessary capability sooner or later. For example, PCs and hybrids claim they combine motion control, vision, and networking in one platform. PLCs do that too. PCs and hybrids claim web capability, a technology that is spreading like wildfire through the control community, and PLCs have that capability as well.Like a hybrid controller, the Modicon PLC (Figure 2) also supports vision, servo drives, Modbus-based devices, and other equipment—thus reducing the need for systems engineering. "This connectivity expands beyond the PLC to give us access to the HMI and the servo drives as well as other vendors' Ethernet-enabled devices, such as vision systems," says Francois Broche, chief controls engineer of Southern Engineering and Automation. "We can monitor the machine in live mode via an Internet-enabled webcam, and all these features also are available on the customer's intranet for maintenance and production tracking.” The machine monitors the processes and can send e-mails to warn of a deviation. Broche says the e-mail-delivered alarm often happens even before the operator notices something is wrong."Schneider Electric's Transparent Ready web-and Ethernet-enabled architecture gives an OEM or system integrator the capability to see into the PLC via the Internet or an intranet," adds Valerie Tur, senior field engineer for Schneider Electric. "I have seen situations where the OEM determined that a safety door was opened on the machine and that was what caused the machine to stop. The cost and time of a field trip for service to another part of the country was thus avoided.""Thanks to the embedded web server, we can connect the machine via the TCP/IP Ethernet system that’s usually available in a plant," Broche explains. "The customer grants us access via its firewall and allows us to monitor and/or modify the machine's programs in a very efficient manner." All this adds up to a competitive advantage, says Broche. "This web and Ethernet capability has become a major sales advantage because we can offer customers a quicker response time for solving problems when and if they occur."It's not just modern technology that makes PLCs so useful. The amazing flexibility of a PLC and a library of hardware interfaces dating all the way back to teletype machines from the 1960s makes PLCs just about the most universal controller ever developed. They help one machine builder keep old machines alive. "Programmable logic controllers provide so much flexibility in enabling control solutions that it makes it possible to profitably rebuild obsolete machinery to economically solve manufacturing problems for our customers," says Phillip Knobel, president of Knobel Electronics, Exeter, Pa. "We control various types of bakery machinery including mixers, packaging machines and ovens. These are mostly obsolete machines from companies that no longer exist. With the programmable controller we are able to reconfigure as needed to ensure functionality of the finished product."PCs Proliferate Profusely
Across the industrial world, PLCs outsell PC-based systems by a factor of 14:1 ($7.5 billion vs. $537 million, according to the ARC Advisory Group (www.arcweb.com)). This does not appear to be true in machine control, where our survey says PCs trail PLCs by a much smaller margin. Our survey found 68% use PLCs and 50% use PCs."There is a very clear trend in the increasing use of PCs and PC-based controllers," says Greg Gardner, global director of VAR/OEM sales at Wonderware. He acknowledges that PLCs are still number one, but says reasons for the migration to PCs include "the benefits of data collection, connectivity, the ability to not be tied to one solution provider and to choose from a large pool of solutions."Software suppliers seem to have learned their lesson about machine builders and software licenses, because few of our respondents said the cost of licenses is a problem. "Because they manufacture in volume, machine builders typically look for aggressive volume pricing and favorable contract terms," Gardner says.In some cases, the cost of software is considered part of the cost of doing business. "If the machine and its functions are self-contained as an ‘island of automation’ then typically the software is considered to part of the solution," he says. "We see a trend where recent regulations, especially in the food industry, require that accurate information be available quickly." In such a case, the application may require advanced software, which may drive a machine builder to a PC-based solution.Machine builders are using PCs for control quite successfully. Kuka Robots, one of the largest robot manufacturers in the world, has used PCs for more than five years. John Patchin, applications specialist at Kuka Development Labs, says their PC handles the HMI, programming environment, motion control, I/O and emergency/safety functions, plus connectivity with the plant network."We use the controller for our entire line of industrial robots, from 3 to 500-kg payloads," says Patchin. "Most are six degrees of freedom (DOF) PUMA-type configuration robots, except for our 5 DOF palletizing robot. The robots are used in applications that include welding, palletizing, automotive seat testing and cancer treatment (Figure 3)."Patchin offers a laundry list of benefits. "We can run the entire controller on a single CPU, so we can stock fewer pieces of hardware,” he says. “This increases reliability, because we have less hardware to break down. The size of the controller has been reduced substantially, and our stackable controllers weigh less and run cooler."Although many criticize Windows, Patchin likes it. "For HMIs, we took advantage of the powerful graphics interface in Windows. It is very easy to program and customize, and a large pool of programmers is available. Windows provides readily available networking capabilities, and supports a large selection of hardware."We thought respondents who use only PCs for control would fit into a nice, definable group, such as "machines that need a lot of computing power," but no such luck. PC controls named by our respondents were all over the place, including die and wire bonders, assembly equipment for the semiconductor industry, pick-and-place robots, woodworking machines, automatic flowmeter calibration rigs, test equipment and plastic injection molding equipment."We started out with PC hardware, and never used anything else for our wet-end paper machine,” says Stein Wilfried, control engineer at Ciba Specialty Chemicals.Lessons Learned
We learned quite a bit from this exercise. In addition to revealing your preference for PLCs and PCs to the exclusion of almost every other platform, we learned that you use PLCs and PCs almost interchangeably. Although hybrid controllers seem to offer the best of both worlds, you are not using them. Or, if you are, you still prefer to call them PLCs. In any case, machine builders are using PLCs, PCs and hybrids quite successfully, and no technology seems to have an advantage over the other.An old adage says the three most important product specs to an industrial machine builder are cost, cost and cost. We found that isn't the case any more. Instead, you take great care in selecting your control platforms, and cost is only part of the equation. And when you do select a control platform, you tend to stick with it for a long time. Any vendor trying to dislodge you from your current platform has a tough nut to crack. But when you do come around to a particular viewpoint, you stay there for years. That makes you a valuable customer to a control platform vendors.
Reader Survey results
What hardware and software platform do you use for your machine controls?
PLC -- 68%
Hybrid -- 8%
PC-based -- 50%
Custom -- 18%
Other -- 5%
How long have you been using your chosen platform?
Less than 1 year -- 5%
1-3 years -- 15%
3-5 years -- 15%
More than 5 years -- 68%
What did you use before you changed?
PLC -- 26%
Hybrid -- 12%
PC -- 17%
Custom -- 38%
Other -- 10%
Why did you change platforms?
Cost of Hardware -- 21%
Cost of software license -- 23%
Ease of Use -- 67%
More capabilities -- 70%
Customer demands -- 26%
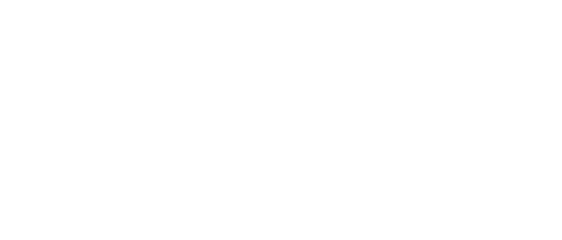
Leaders relevant to this article: