IN A NEVER-ENDING quest to remain competitive, machine builders exercise a variety of tactics to execute cost-efficient design strategies. For example, engineering and building new machinery on a modular theme with standardized control components now is commonplace. This permits builders to configure and reconfigure their designs to meet myriad customer requirements without having to re-invent the wheel each time with a dedicated, application-specific solution.
With control software increasingly based on open, more flexible platforms, it only makes sense to pursue machine programming and implement HMI software in a similar way. Why create expensive dedicated HMI software when todays standardized software platforms deliver cost efficiencies and design flexibility that provide customers with a more reliable, better-performing machine?
Its a Package Deal
Charlotte, N.C.-based machine builder Roberts PolyPro works with consumer products companies to design, construct and commission equipment that installs/assembles plastic fixtures such as handles, spouts and plastic seals on consumer packaged goods. The company also builds paperboard finishing equipment for package converters and contract packagers (See Figure 1).
Figure 1: Simplicity and More Speed Required
Roberts PolyPro built two similar paperboard assembly machines, but its engineers were still looking for ways to decrease time and boost machine performance.
A Better Machine
The Roberts PolyPro machine uses Kraft board and recycled pressed board to manufacture a stronger, lighter carrier in less time and at a significant cost savings when compared to traditional one-piece carriers.
The beverage carrier machine starts with two pieces of cardboard. A plain piece of cardboard goes on the inside of the carrier and creates a web for the beverages to fit in. The other piece of cardboard has a printed graphic on it that acts as the outside of the carrier. The machine takes the two cardboard pieces, and through an automated sequence of precise folding and gluing, produces beverage carriers of speeds of up to 500 per minute (See Figure 2 below).
Roberts Polypro says speed is the real benefit here. It is relatively easy to do this process slowly, but once you start increasing the speed it becomes more challenging. According to the OEM, this is where the motion control decisions made during designfor both hardware and software--really come apparent.
The company built its first beverage carrier assembly machine in 1999 using Allen Bradley SLC 5/04s for control. To help reduce engineering time for the second machine it produced, the machine builder relied on the Rockwells ControlLogix technology for machine control functions.
Reduce Programming Time With VBA
In designing the third beverage carrier, a critical goal for Roberts PolyPro engineers was to further reduce programming time. While fundamentally satisfied with the Wonderware HMI package used on its previous two machines, they were looking for improvements and wanted to explore other options.
While attending a customer event held by their local distributor, Neel watched a demonstration of Rockwell Softwares component-based RSView32 HMI software package.
Among its features, RSView32 can integrate ActiveX controls and use Microsoft Visual Basic for Applications (VBA) as a built-in programming language.
Its very empowering because it allows me to do a lot more with it, says Neel. I already was familiar with VBA so I didnt have to learn anything new, I could just walk in and write code. Neel says if he needed anything special, he could just go to the Internet and find it. It provides a huge reservoir of code snippets and application information that I can find on the Internet, he explains. Its an easier way of doing things because I can just cut and paste code and move on to the next task.
Tags a Drag
According to Neel, there was nothing intrinsically wrong with the Wonderware package used on the previous machinesit just couldnt be integrated as tightly with the Rockwell Automation components. Furthermore, programming in it became very time-consuming. Using the previous software, I would have to go through a long, exhaustive process where I had to create all tags in Wonderware, explains Neel. Then, I would have take the tags written in my computer or notebook and create those same names in my HMI software so that I could relate the two. He says RSView32 eliminated this hassle. Its tight integration allowed him to explore the tags in the processor directly from the RSView32 software.
The other thing that comes to mind, recalls Neel, is that if I wanted to do something with Wonderware with more complexity in the background, I had to use its scripting programming language. Neel says this method worked OK, but it was not standard. Because it is proprietary, it wasnt something that I could easily go out to find snippets of somewhere else, he adds. If I needed help with something or if I had problems, I would have to start from scratch.
As a Result
Using RSView32 to program the beverage carrier assembly machine, Roberts PolyPro cut its engineering time by 30 to 40% compared to similar applications using the previous software. Neel credits this to the familiar and easy-to-use programming environment and VBA code, but points out the ActiveX capabilities also contributed a great deal to the programming development time savings Roberts PolyPro experienced.
ActiveX objects basically are modules that you can roll into whatever software they are compliant with, says Neel. This means anything Microsoft-based, you can roll an ActiveX object into it. So if somebodys written a module for a special feature, I can go and find it and roll it into RSView32 to make it part of the program.
For example, Roberts PolyPro needed to include large numeric keypads on the operator screens of the carrier assembly machine. To add this feature, Neel simply conducted a web search for ActiveX numeric keypads, found an appropriate keypad, and it was instantly part of the application.
In addition to the ActiveX savings, the ability to browse directly from RSView32 into the processor for tag names was another way we saved time, says Neel. This browsing capability is much easier than writing down the tag names and transposing them into a third-party package.
Custom a Standard for Customers
ActiveX helped Neel satisfy a customer requirement for a large keypad display on the HMI without too much bother. What about other such requests? How important is it to have the flexibility to customize the HMI for specific customer demands or specifications?
Being able to customize is very important, says Neel. One customer wanted the visibility to see what was happening on the machine in real time. They wanted a customized report that provided information on the machines uptime, throughput and production problems. That way, a manager would be able to push a button and see a chart that shows how the machine performed for that shift.
Figure 3: See the Problem, Fix the Problem
The HMI allows the operators to make real-time changes while the machine is running. If a downstream worker sees that product isnt folded correctly, he can adjust the settings through the HMI without turning the machine off.
After the Fact
But the value of integrating such a flexible HMI platform doesnt stop once the system is handed over. Its important, Neel says, to be able to make tweaks when necessary. Customers themselves cannot make changes because they dont have the development license for RSView32. If modifications need to be made, Neel points out, it is easy for him to do it remotely or on site.
Cuttin the Debug
After the beverage carrier was built, Roberts PolyPro saved additional time during the equipment debugging stage. Using the ControlLogix controller and RSLogix 5000 programming platform, Roberts PolyPro was able to cut its debugging time by an estimated 50%.
The controller enabled Neel to integrate motion control and machine control into a single, multitasking controller platform, resulting in higher system performance, faster application development, easier maintenance and lower system costs. During the debug stage, the integrated control architecture enabled the machine builder to simply monitor servo status and faults and use the built-in troubleshooting of RSLogix to resolve issues.
While we were debugging the machine, I used the trend charting function to plot actual position versus commanded position of a given servo motor, says Neel. This allowed me to see if it was doing what it was supposed to do. The software capabilities, combined with the plethora of information at my fingertips, cut my debug time in half.
Like most businesses, Neels main goal is to provide the most reliable, efficient products available to customers. With each beverage carrier assembly machine we have built, weve implemented more and more products from a single, reliable vendor with proven technology, concludes Neel. In doing so, we continue to improve our processes, and most importantly, provide a better product to our customer.
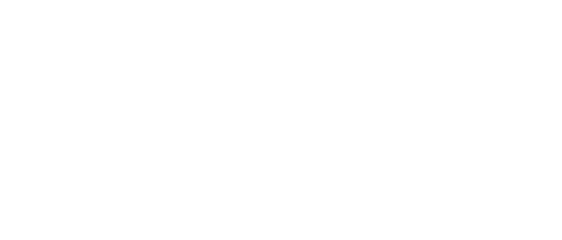
Leaders relevant to this article: