A Tier One automotive supplier decided to research and purchase a new fabrication machine that could guarantee higher throughput and reduce product scrap. The supplier brought its “wish list” to Eagle Manufacturing Corp., Shelby Township, Mich., a recognized presence in the design and fabrication of punching, sawing and notching systems for the Automotive industry and other industry segments including aerospace, plastic, rubber, aluminum extrusion and roll forming.
The customer challenged Eagle Manufacturing to develop an innovative inline notch-and-cut-to-length fabrication system that the profile fabrication industry was urgently in need of.
The Time Was Right
In its previous machine control schemes, Eagle incorporated a mix of technologies from different automation manufacturers. With a design that now relied too much on manual changeover, Eagle realized that the time was right to design an improved solution—a solution that would have to incorporate 22 servo axes in one system. Eagle broke new ground with this design--it had never used that many axes on a single machine before.
“We had a labor-intensive design that required a fork lift and operator to move one of four independent punch tools in and out of the machine,” says Eagle Manufacturing president Brent Short. “With our customer demanding faster changeovers and more flexiblity, we had to find a better way.”
Eagle has migrated over the past 40+ years from pneumatic power and controls, to hydraulic systems, and finally, during the past seven or eight years, to servo drives and motors. “We actually have a good hydraulics-based system,” says Short, “but we couldn’t guarantee the level of positioning control required.” He also says that the jump to servos was the catalyst to better machine performance. But this next step was still a whopper.
“We had a labor-intensive design that required a fork lift and operator to move one of four independent punch tools in and out of the machine. With our customer demanding faster changeovers and more flexiblity, we had to find a better way."
|
Let’s Talk About It
Integrator Majority Controls, Port Huron, Mich., initially briefed Eagle Manufacturing on its partnership with automation supplier B&R Automation and showed Eagle how it could meet several specific design requirements, including the need to precisely link every motion axis to a high-resolution encoder.
Eagle’s Tier One customer initially requested a Rockwell Automation controller and HMI. However, the servo system was open. Working with a tight space requirement, the complete controls solution, including drives, had to fit a two-door 72-in. enclosure. The job already had been quoted and approved, so the budget was tight and fixed.
The parties then took the next step. They introduced Eagle’s customer to the proposed solution for its new “Eaglematic” machine. Eagle’s customer wanted to review the system design in detail and inspect the proposed new hardware.
Short says that once they saw the equipment and realized the capabilities and integration level of the proposed system, the customer reconsidered its requirements and ultimately removed its brand-preference restrictions, agreeing to complete use of the B&R controls that Eagle recommended. The control solution used Ethernet Powerlink for communications between the main controller, a 10.4-in. panel PC and 22 ACOPOS servo drives.
No Gain, No Gain
“I put everything on the line with this new design,” says Short. “B&R never had been involved in a machine design with more than 15 axes control, and this job would one of the biggest they’d been part of in North America. He says the design was solid, and let him say with confidence to his customer, “Let me run with it. We’ll take all the responsibility.”
Short sees the trend of customer willingness to consider alternative automation suppliers as symptomatic of how those customers have to deal with diminishing levels of experience and expertise on their own factory floors. “They want machine builders to guarantee performance and reliability these days,” he says. “They’re becoming less likely to have real concerns about how you get it done.”
As with most industrial machine builders, Eagle has mixed feeling about changing suppliers. “Our experience with Rockwell Automation was both good and bad,” Short says. “Let’s face it, the automotive industry is dominated with A-B controls. But with all the new technology that B&R offered, we figured a change was a good idea.”
One of the most critical process parameters is part-length accuracy, says Short. “On every die head the part length is a function of the machine’s ability to use encoder information to accurately track a position on the material as it moves through the system,” he adds. “Our design mandated that the machine cut parts to length with a precision tolerance of no less than 0.04 in. running at a line speed of 50 ft./min.” The influenced the choice of the Powerlink-centric decentralized control scheme.
Above All, Meet Expectations
“Our new machine now combines six different tools into a single operating set up that automatically moves the required tool into place when called upon to do so via the controller,” says Short. “The tools are changed using a combination of different servo mechanisms ‘In-line and On-The-Fly’ without interrupting the flow of the upstream extruded material.”
Additionally, the panel PC is the main CPU and uses a single processor to perform logic control, visualization and motion control tasks. This, says Short, provides the customer additional value since additional processors and the communication between them is eliminated. The onboard standard Ethernet port provides connectivity to a line host and enables remote diagnosis of the system.
“The servo solution also provided a size benefit over any other competitor,” says Short. “Because of the unique design of the drives, Majority Controls was able to fit all 22 servo drives within the specified two-door enclosure along with the entire control system and supporting electrical components.” The B&R ACOPOS solution allowed the servo controllers to be mounted side by side with no air-gap spacing.
“The drives are stackable in the cabinet and with the motion controller built into the drive, we eliminate the need for the PLCs,” says Short. “It was an important factor in reducing the size of a pretty big controls cabinet.”
The remote panel functionality in the programming environment was used to link a 4x20 character display on each of the four stations to the main CPU in a very short application development time. “The remote panel enables the operator to set up machine parameters in close proximity to the processing, saving time and facilitating the precise preparation of a new job, simultaneous to the ongoing production of parts in the other stations,” adds Short.
The main CPU and the remote panel both access one single transparent variable database. Changes from any one of the panels or the main control panel result in an immediate change of the display on all of the other stations.
Throughout the project, safety and security were overriding factors in the software design, because the machine’s primary function is cutting and punching. Light curtains and other safety devices specified by Eagle Manufacturing, when tripped, instantly shut down the operation of the machine. The software allows for a quick restart once the safety violation has been remedied.
The combined benefits of Ethernet Powerlink and decentralized motion control let Eagle Manufacturing create a machine that delivers what the company believes to be unprecedented process accuracy, despite the large number of geared axes in one system.
“Customers want machine builders to guarantee performance and reliability these days. They’re becoming less likely to have real concerns about how you get it done.” |
Eagle cut 10% off the previously budgeted cost of the more traditional automation system consisting of an HMI Panel, PLC, and motion controller. The new machine design enables the automotive end user to produce higher quality parts and simultaneously cut operating cost by reducing waste, set-up, and down time, while increasing the overall flexibility of the production line.
“With automotive customers, performance feedback in any granularity is hard to come by,” says Short. “But, it seems we met this customer’s demands for a configuration that delivered 99% efficiency, based on its internal criteria.”
Cycle Time Considerations
CURRENT, VELOCITY, and position control loops in servo applications are closed at different cycle times. A typical cycle time for a current control loop is 50-100 µs. It’s 150-200 µs for the velocity control loop, and 300-500 µs for the position control loop.
For systems in which the control loops are closed inside a centralized motion controller, the communication needs to be fast enough to supply sufficient bandwidth to transfer setpoints and feedback values back and forth. “As a consequence, compared to a completely decentralized system at the same performance, the centralized system needs to transfer information up to four times faster,” argues Marcus Sandhoefner, B&R Automation sales manager. “This becomes increasingly challenging for digital communication systems such as SERCOS, ProfiBus, and DeviceNet, which provide a more reliable and more economical interface, but communicate in the multiple millisecond cycle range. The Eaglematic application requires a synchronized position update time of 400 µs, 10 times faster than the cycle time of the above mentioned networks. Additionally, for greater numbers of axes connected to the motion controller, there is increased traffic on the network, since every axis communicates the same amount of information to the motion controller and receives the set points in return.”
The control system met the tolerance requirement by sending the encoder signal to one drive, from which the signal was transmitted to the other drives over Powerlink. Each drive calculates its own slave position from the master in real time, following a signal from the upstream caterpillar drive. Both the drive position-control loop and Powerlink cycle are synchronized to provide jitter-free operation. As a result, the system produced a cycle time of 800 µsec on a position update of every 0.008 in. of fed material at a throughput of 50 ft./min., ensuring previously unreached process accuracy even with the number of total axes.
“By splitting up the coordinating task of a centralized motion controller into small, fast, decentralized tasks in the drive, the motion control system’s performance improves due to reduced network and CPU load,” says Eagle Manufacturing president Brent Short. Instead of having to communicate a new speed control set point to every drive and a feedback value from each drive in the Eaglematic machine every 100 µs, the network only needs to broadcast a master position once every 400 µs, adds Sandhoefner. “A broadcast can be received simultaneously by all nodes on the network, so that the maximum number of axes inside a machine no longer depends on the CPU performance and the communication bandwidth of the centralized motion controller,” he says. “This is determined only by the maximum allowed number of nodes and the bandwidth of a network. Today’s available time and cost efficient drive processors provide ample processing power to handle all control loops and additional decentralized motion controller functionalities inside the drive.”
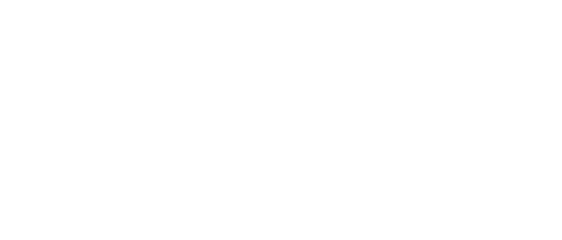
Leaders relevant to this article: