- Cameras, usually color CCD devices similar to those in camcorders
- Frame grabbers, which digitize analog images and interface with bus structures
- PCs
- Software and fast data transfer
- Controls
Imaging functions may be further broken down into image acquisition, image processing, and feature extraction.
Machine vision performs four tasks very well: guidance, inspection, gauging, and identification, suiting them for packaging. However, with the right programming, vision systems can also pick out fill errors, detect smudges on ampoules, inspect lyophilization cakes for contaminants, and accept or reject solid materials based on average particle size. Some biotech companies have even used cameras to monitor froth and turbidity during fermentations.
But process applications lie at the fringes of Zuech’s definition because of the required human intervention. Besides, traditional measurements (temperature, pH, extent of reaction) are relatively straightforward and require no new thinking. With drug-makers just getting comfortable with conventional real-time process analytics, machine vision for process monitoring is probably a long way off, at least in North America.
For example, Japanese drug makers have embraced machine vision inspection of solid dosage forms, where their peers in the U.S. have not. Vision systems excel at for inspecting pills and tablets for defects, engravings, and overall integrity. About a half-dozen companies sell inspection equipment for this type of application to Japanese markets, but Nello Zuech says vendors can barely give their equipment away to U.S. pharmaceutical manufacturers.
Seidenader Markt (Schwaben, Germany) offers a barrier-enclosed inspection system with a throughput of 2,500 tablets per minute. The company also develops machine vision systems for ampoules, prefilled syringes, and infusion bottles plus ampoule cleaning/drying machines and capsule polishers. The InspectoRx tablet/capsule inspection system from American SensoRx (Glen Rock, N.J.) accepts or rejects solid doses based on integrity, color, shape, and presence of foreign object contamination. Other solid dose inspection vendors include Driam USA (Spartanburg, S.C.), AC Compacting (North Brunswick, N.J.), and Japan’s Kanebo. A few blister-pack equipment vendors, most notably Bosch and Uhlmann, integrate inspection systems on their machinery.
Eyes-in-a-Box
Machine vision can be deployed out of the box, built into a process, or custom-installed. Off-the-shelf apps like identification code recognition perform one task very well and do not require customization. “They’re about as close to a standard application as you can get,” notes Justin Testa, senior vice president for Identification Products at Cognex (Natick, Mass.).
Although high-end implementations tend to be custom-built, with unique lighting, integration, and object presentation, vision companies have been striving to develop more general-purpose products. “One goal is to make these deployments simpler and cheaper so users can be up and running quickly,” says Testa. Another is to provide products with the capability of vision systems and the ease of use of barcode readers.
Cognex, which sells sensors, components, and vision systems to several industries, offers In-Sight technology, which reads and verifies RSS (Reduced Space Symbology) codes on pharmaceutical packages for product identification and traceability. RSS codes, whose compactness allows them to go where no barcode has gone before, can uniquely identify unit doses, even individual tablets.
Most companies enter the machine vision application business as component vendors, picking up the required integration skills later on. Others, like IC-Vision, enter from the software side. Today the company bundles its code with custom, integrated, turnkey vision systems. IC-Vision differentiates itself on its high speed (inspecting up to 3,600 parts per minute) and with its software, which marketing development director Luis Cruz says requires little or no programming.
IC-Vision offers two systems based on a self-learning “neuro-based” image analyzing algorithm. The flagship Eye-Q system inspects caps, closures, bottles, tubes, and print quality, detecting malformations, flash (extraneous plastic at joints), missing liner, contamination, outer or inner missing cap, line defects (missing, half-moon, deep cut, folded, half-seated, off-center), defects in tamper-evident bands and printing defects. Since Eye-Q’s processing algorithm memorizes the flawless product rather than likely flaws, it recognizes all product flaws that yield visual differences with the reference group, resulting in more accurate defect recognition and reduced changeover and production downtime.
IC-Vision's Inspector system, which also uses a self-learning algorithm, memorizes up to 13 million features on a part in relation to other features. Inspector extracts these characteristics related to size, color, position, and other criteria and uses them to calculate simple decision-making criteria.
Although they’re smart enough to catch tiny perforations in blisterpaks or unnoticeable skew in labels or cartons, IC-Vision’s imaging systems cannot verify the integrity of
printed materials beyond their physical orientation.
“We can detect if the label has been cut improperly, if the print is the right color, and if all the print is present, but we can’t detect if the printer switched an ‘I’ with an ‘l,” Cruz explains. “We don’t do OCR and actually we don’t do absolute measurement, even though we detect differences much smaller than one millimeter.”
To Cruz, the most difficult aspects of creating a functioning vision system are mechanical handling and presentation of products to the camera. Issues such as what type of guide rail to use, product stability as it passes by the camera, lighting, and how it’s all put together spell the difference between success and failure. “Vision systems are only as good as their installation,” Cruz says. “Components may be great by themselves, but you’ll get mediocre results if the people installing them don’t know enough about the product and operation.”
The Eyes Have It
The greatest difficulty in implementing machine vision is defining appropriate inspection criteria. Particularly in a regulated industry like pharmaceuticals, where everything is validated, QA groups must be in alignment with what the vision system determines is acceptable or unacceptable product.
“When switching over from manual inspection to machine vision everyone must agree, and then understand, what’s satisfactory from the vision standpoint,” says Dan Freed, Business Development Manager at Xyntek (Yardley, Pa.). “Figuring out the inspection criteria is the starting point of any machine vision project,” Freed remarks. “Then comes the art of determining if you can get what you need from an image standpoint.”
Machine vision implementations are almost never as straightforward as they appear. “Some applications appear to be simple, but when you get onsite you discover that they’re difficult or impossible,” Freed observes. He notes a recent biotech project involving hundreds of roller bottles, which Xyntek was asked to monitor for cell culture health. “We didn’t think we’d be able to image color and turbidity, which can be indicators of dead cells or contaminated cultures. But we came up with an incredible lighting scheme that gave us what we needed without resorting to software tricks.”
Optical character verification (OCV), a classic machine vision application, involves matching printed symbols on a label (e.g. date, lot code) or manufacturing packaging with a standard image. OCV differs from optical character recognition (OCR) in that the machine is not reading the print but instead verifying that everything is there, in the right place, as it would for a part.
“An OCR system has no idea what it’s reading, whereas with OCV, you already know what you’re looking at,” says Dan Freed of Xyntek, which offers a turnkey, configurable OCV system it calls MVX-OCV. Like other machine vision implementations, MVX-OCV needs to be trained using, in this case, a standard alphanumeric set or library. Xyntek’s other packaging products include MVX-Blister (for tablet color, integrity, presence), MVX-PQI (labels/printing), MVX-TFI (tablets on slat filling machines), MVX-2D, and MVX-CPI.
Xyntek also serves drug discovery and laboratory automation markets through its MVX-PAS for grading biological samples by color, area, density, and height. Another biotech-oriented product, MVX-CCA, inspects and grades cell cultures based on visual properties like color, cell clumping, and light transmittance. MVX-CCA, which was the basis of Xyntek’s cell culture product, consists of a high-resolution color CCD camera, lighting, machine vision processor, and application software.
Although most machine vision vendors specialize in a narrow application area--for example, packaging or print imaging--Xyntek tackles most applications that come its way, even process monitoring. According to Freed, sensor or component vendors have an easier time specializing, whereas value-added engineering firms recognize that even within inspection classifications every application is different.
“What one manufacturer considers a quality defect may not be an issue for anyone else,” he observes. "Vision systems are only as good as their installation... Components may be great by themselves, but you’ll get mediocre results if the people installing them don’t know enough about the product and operation."
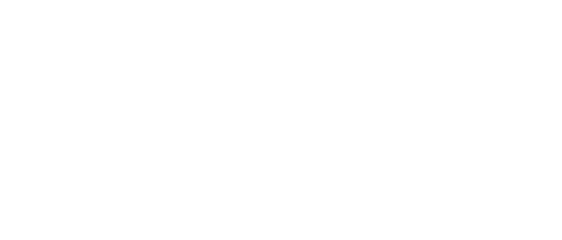
Leaders relevant to this article: