QUESTION:
What Vision System Data Protocol Do We Use?
We've decided to offer an integrated vision system as an option for our packaged goods machinery. It probably will be a multi-camera system leading back to one processor as part of the overall Windows-based control system. We're inexperienced about what data communications protocol to use to balance performance with connectivity needs. The options seem to be Camera Link, FireWire, DeviceNet, Profibus, an Ethernet version, or some vendor/proprietary options. We'd like some opinions on this.
From June 2005 Control Design
ANSWERS:
Choose Camera Link or FireWire
While researching the camera that fits your application, an often overlooked step is figuring out how the camera will connect to a PC or a compact vision system.
Though camera connectivity has come a long way in recent years, it can still be difficult to decide which standard is best for your application and which standard will be around for years to come. While everyone has their favorites, two camera standards have emerged as the clear leaders: Camera Link and IEEE 1394 (FireWire).
In general, you’ll find that Camera Link addresses the higher data throughput applications, such as continuous web inspection or high-speed cosmetic inspection, and that IEEE 1394 addresses lower-cost, lower-bandwidth applications, such as checking for part presence and product identification.
Camera Link, with bandwidths to 680 MB/sec, ensures that you’ll be able to acquire all the images you need, no matter how fast the objects speed past. While Camera Link is pervasive and fast, it does require an image-acquisition board for the PC. The latest Camera Link image-acquisition boards are based on PCI Express, which eliminates the PCI bus bottleneck of 132 MB/sec. Some boards can acquire images from two Camera Link cameras at once, but most of the time, you’ll need a plug-in board for each camera.
For your application, you state that you may need more than one camera. A popular solution to this is to use IEEE 1394. With FireWire, you can connect multiple cameras to one low-cost, consumer-grade FireWire interface device, which means you don’t need to buy a special image-acquisition plug-in board. With that said, you do have to consider a few things with FireWire, the first of which is bandwidth. With IEEE 1394.a, you’re limited to 50 MB/sec, which is shared by all the connected cameras. Usually this means that beyond three VGA cameras running in parallel, you’ll run into data throughput issues. Another consideration is triggering and synchronization. Consumer-grade IEEE 1394 interface devices don’t have built-in digital I/O, so you have to wire a trigger directly to the camera. Sometimes this means developing custom circuitry or buying additional hardware for the PC. There are a few products on the market that combine digital I/O with an IEEE 1394 interface device, such as our PCI-8254R.
Looking to the future, Camera Link will be around for years to come. As for FireWire, the 50 MB/sec bandwidth limitation is about to disappear with the adoption of IEEE 1394.b, which doubles the available bandwidth to 100 MB/sec. Companies such as Sony, Prosilica, and Point Grey have released cameras for IEEE 1394.b and more are soon to follow.
Kyle Voosen, Vision Product Engineer, National Instruments, Austin, Texas
An Ethernet Plug
The primary objective for building Ethernet communication capabilities into some of our vision sensors is to support quality control traceability through connectivity. This can simplify data tracking from high precision inspection, giving customers with the ability to continuously improve their processes.
Remote access and operation across Ethernet is an important consideration for integrating quality inspection into an entire automation scheme. With increased demand for quality traceability, our customers use Ethernet-ready vision systems to take full advantage of Ethernet’s communication flexibility. A dedicated communications processor ensures the inspection process never is slowed or interrupted during remote data access. The supporting software simplifies remote parameter changes for setup and production changeover, and offers advanced monitoring and data-logging capabilities. By using the Ethernet capabilities that these vision controllers offer, one can view and display real-time images from the vision sensor on a personal computer monitor or HMI. A user can also simultaneously view these images from several controllers connected to the same network.
In addition to external storage through an Ethernet communications backbone, these systems also accommodate on-board storage. Local storage of at least 200 images right in the controller allows attachment of images to quality control reports. They also can be used in production optimization, based on checks of measurement accuracy over samples taken at different time intervals. Images can be off-loaded to the local server at any time.
Ethernet-ready systems make vision data more useful in any environment where quality control and traceability is important. These systems combine Ethernet’s broad communication capabilities with PC-based support software for unparalleled access to vision data and reporting tools. Used together, they form a powerful combination to help manage quality control, production traceability and process diagnostics, from any location, remotely or from the factory floor, by allowing data access any time, anywhere. Important processes can be monitored and controlled from one or multiple points with live monitoring. Critical processes that require high speed, high-resolution inspections can be monitored simultaneously to assure consistency across several production lines.
Vision software supports remote operations, simplifying and centralizing program management by downloading setup functions for single or multiple production lines across the network. Remote setup and monitoring of operations provide quick change over between products or programs. Vision sensor measurements can be started and stopped, and scene data settings can be specified from a remote computer. The data stored in the controller can be transferred to any designated storage location, whether local or remote, and also at any time. Users can analyze data without slowing the inspection operation or the production line. With high-speed Ethernet 100BaseTX communications, even large volume image files can be transferred rapidly.
Ethernet capability allows a larger field of functionality that a standalone system can’t provide. In many applications where vision is used, it is most often integrated with some sort of HMI, PLC controller, or other sensing devices. By having a common Ethernet backbone, we can ensure that these systems are compatible and able to communicate seamlessly with each other as a total packaged solution.
Robert Lee, Product Marketing, Omron Electronics, Schaumburg, Ill.
January’s Question:
We Have PID Troubles
We build turnkey PLC-based batching and blending systems for the wet chemical producing industry, and as customer requirements become more demanding, we're finding it increasingly harder to control some loops with basic PID. We are aware of advanced options such as fuzzy logic and adaptive control, but mostly in the context of much larger operations. Does anyone have some experience to share?
Send us your comments, suggestions, or solutions for this problem. We’ll include them in the January 2006 issue and post them at ControlDesign.com. Send visuals, too—a sketch is fine. E-mail us at [email protected] or mail to The Answer to Your Problems, CONTROL DESIGN, 555 W. Pierce Rd., Suite 301, Itasca, IL 60143. You can also fax to 630/467-1124. Please include your company, location and title in the response. Have a problem you’d like to pose to the readers? Send it along too. |
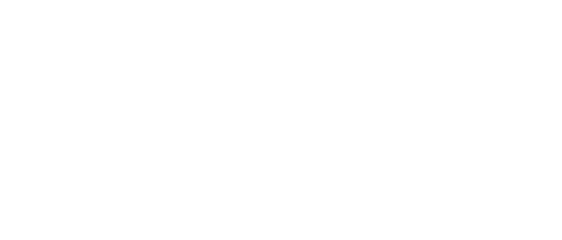
Leaders relevant to this article: