THE FUTURE just isnt what it used to be, and current events are to blame. Despite the recent U.S. economic recovery, theres plenty of news certain to screw up the near future for many people. These events include GM and Fords numerous upcoming plant closings, Mercks layoffs, ongoing outsourcing to China and India, accelerating retirement rates and lost expertise, ongoing technological shifts, expanding job descriptions, and many other galloping and/or lurching forces.
Still, because the future remains always unknown, we can pour our fears into it, and use pessimism to justify reactionary laziness dressed in conservative clothing. Or, we can use the best information we have about whats happening now, do what we know we should doing anyway, make the most informed decisions we can, and prepare to capitalize on our correct guesses and minimize the damage from our incorrect ones. (Please insert your favorite make your own luck cliché here.)
Making an educated guess more educated and less of a guess requires using what you know, and finding out what you dont know. Fortunately, you dont have to wait for the future to arrive to do this. In fact, if you do prepare well, the future and its inhabitants will have to worry about you rather than the usual reverse.
Packaging Machinery Shipments, 2004-2007 (in millions of $)
|
2004 |
2005 |
2006 |
2007 |
% increase per year |
U.S. |
5,240 |
5,690 |
5,700 |
5,980 |
3.8 |
Canada |
421 |
446 |
446 |
472 |
3.9 |
Packaging Machinery Manufacturers Institutes (PMMI) 11th annual Shipments and Outlook Study states growth will be fueled by growing U.S. and Canadian economies, increased capital spending on equipment, and expanding capacity utilization. Source: PMMI
Builders Perspective
So far, 2006 seems like its looking up, and well likely see stable to increased performance, says Steve Bergholt, chief electrical/electronic engineer at 80-year-old Triangle Packaging in Chicago. "Some industries are hurting and some arent. Its just a matter of keeping up to date with the times and new technologies. If we dont, then we could have problems keeping up production and surviving. We build packaging equipment for the machine industry, so we have to offer equipment that makes our users more efficient, and helps them achieve the production levels they need, whether it happens with improved data acquisition, better control, or via some other new capabilities.
Besides designing our machines to take advantage of any new technologies, we also try to educate our customers about what they need to be doing. Sometimes everyone is a little behind the times, and needs to be dragged into the future kicking and screaming. However, once people are educated and learn what they can really do, then theyre very accepting.
To help users try new technologies and learn their value, Bergholt adds that Triangle often gives machines to its clients, and promises not to charge them until they accept it. We say, You didnt ask for this, but its what you need, and its close to what you want, adds Bergholt. Most of the time they eventually do accept the new equipment, so its a very good investment for us.
Despite accelerating competition from and outsourcing to the Asia-Pacific regions, increasing energy and transportation costs will help North American manufacturers continue to stay competitive., says Chris Choi, CTO for machine operations at Husky Injection Molding Systems in Bolton, Ontario, Canada. We think 2006 is going to be a good year for machine builders because business has been relatively slow for awhile, and many manufacturers are looking to renovate their equipment and productivity, adds Choi. We think Husky also is going to have a good year because most of our major customers have already scheduled renewals for new equipment. We also supply PET plastic-making machines to bottlers, and that industry is growing too.
Another trend in coming years is that machine builders are being asked to improve on the energy efficiency of their machines. Most builders in Europe are doing this because electricity costs eight cents per kilowatt hour, while North America still relies on low-cost oil that isnt going to be there soon.
Choi adds that North America and Europe also must raise the bar on educating its worker and keep investing in R&D because the recent economic setback and recovery are cyclical. He recently passed away, but Peter Druckers idea of the need for knowledge workers is more important than ever now, adds Choi. The developed world needs to transform itself from a manufacturing-centric model to a knowledge-centric one, focus on intellectual property and innovations, and learn to cooperate with low-cost labor providers.
Paul Brancaleone, engineering manager for software and control at Battenfeld Gloucester in Gloucester, Mass., reports that driving down costs will continue to be his firms most critical challenge in 2006. The firm makes plastics processing equipment for film extrusion. Its hard, but it is possible, he says. Weve seen a lot of assembly move to China, so were also sourcing some pieces of equipment there. This can help, but it also requires us to educate our staff better, mostly because we have to make our equipment documentation more precise to go to China. Documentation in the U.S. didnt need to be as precise because experienced operators could make up the difference.
Brancaleone adds that Battenfeld already is seeing signs that it will pick up more orders in 2006. We just acquired a startup printing company, so well be able to produce more complete products for our customers, he says. Now, we can provide a more complete package, which helps us bargain better. Were also producing more flexible machines that can make a wider variety of products. For example, production lines that used to make either trash bags or films can now be configured to do both.
Biggest Hurdles, Threats for Machine OEMs (in the next three years)
Hurdles That Can Be Changed
- Understanding what customers value -- 25%
- Poor communication/weak selling process -- 8%
- Company unable to respond -- 6%
- Allocating enough marketing resources -- 4%
- Slow to redesign -- 2%
Threats That Are Out of OEMs Control
- Strong domestic competition -- 26%
- Talent shortage -- 17%
- Strong local competition -- 13%
- Weak local economy -- 10%
- Availability of capital -- 10%
- Weak national economy -- 7%
- Declining customer base -- 6%
- Rapid technology changes -- 5%
- Material availability -- 4%
- Cost of technology -- 3%
Machine OEMs report their top two external competitive threats will come from local, rather than global, competition, and a shortage of skilled staff. Source: FiveTwelve Group
Associations Overview
Besides developing more flexible products, the many machine builders reportedly are being more cautious in how they respond to this latest U.S. economic recovery, according to the Pat McGibben, strategic information and research vice president with the Association for Manufacturing Technology. Going into 2006, capacity utilization still is on the rise in most AMT members industries says McGibben. In most economic upturns going back to the 1950s, manufacturers let capacity utilization climb to 80-85%, and then company buy until it declines to 70-75% again, which causes a dip after a recoverys first 11-12 months. However, this most recent upturn in 2004-05 has been different because the manufacturers never let capacity utilization get really high. There just wasnt a big push to start the usual double-digit increases in orders.
McGibben explains this caution might stem from manufacturers memories of 2003, which he says was one of the worst years ever for new orders. It was followed by a 30% jump in orders in 2004, though total revenues were less than expected, and then a percentage increase in the teens in 2005. So, were expecting members to be up against the same forces in 2006, which we think result in another orders increase the teens, he says. It wont be bad, but it wont be exciting. Buyers are making purchases incrementally, and they arent stocking up too much on capital investments like they did n the 1990s.
Fortunately, this cautious economy and a slightly weak dollar apparently are diverting some manufacturing back to North America, especially into Mexico and Canada, and likely into the U.S. soon as well. McGibben says this trend is fueled by increased adoption of several new technologies, increased shipping efficiency, skyrocketing energy prices and recent supply-chain advantages. In short, the Pacific Ocean often is still too danged big.
McGibben adds that North Americas competitiveness also is based on the fact that, over the past 25 years, many machines have become two or three times more productive and efficient, even though they can still be bought for essentially the same price. In addition, many machines are far more flexible now, and one piece of equipment can handle several different jobs, such as grinding, prismatic cutting and turning on a line of symmetry.
Were expecting demand and output to keep growing in the double digits, and then capacity will fill-in behind, says McGibben. As a result, AMT expects capital spending on manufacturing technology to increase 10-13% over 2005.
Similarly, Ben Miyares, industry relations vice president at the Packaging Machinery Manufacturers Institute, reports that PMMIs members saw demand for packaging equipment grow 7% in 2005, but expects slower, steadier growth of approximately 4% in 2006. A weak dollar and North Americas longer-lasting packaging will be two main contributors to the trend, he says. Were at the point where much of the large amount of machinery bought in the 1980s needs to be replaced, and so the economic advantages of replacing it is becoming more apparent, adds Miyares. This is helped by the fact that the average productivity of packaging equipment increased 4% per year for the past 25 years.
Proximity and Photoelectric Sensor Shipments (in millions of $)
|
2004 |
2005 |
2006 |
2007 |
% increase per year |
Capacitive |
15.0 |
15.7 |
16.4 |
17.3 |
4.9 |
Inductive |
275.9 |
286.3 |
297.3 |
309.4 |
3.9 |
Magnetic |
25.4 |
26.1 |
26.8 |
27.5 |
2.7 |
Magnetic actuated |
30.4 |
31.7 |
33.1 |
34.7 |
4.5 |
Photoelectric |
201.0 |
212.9 |
225.9 |
240.0 |
6.1 |
Photointerrupter |
52.3 |
54.8 |
57.5 |
60.4 |
4.9 |
Ultrasonic |
17.2 |
17.9 |
18.5 |
19.2 |
3.7 |
Total |
617.2 |
645.4 |
675.5 |
708.5 |
4.7 |
Photoelectronic sensors are expected to be the fastest growing segment during 2004-2007. Source: VDC
Analysts Assistance
Jim Taylor, group manager for industrial automation at Venture Development Corp., says the 2006 outlook is mixed, and VDC is observing a lot of moves offshore from the U.S., as well as greenfield development overseas, by companies seeking lower manufacturing costs, and that related control and components work is following them. These problems are accompanied by an ongoing engineering skills shortage in manufacturing, which increasingly is relying on system integrators and OEM suppliers for design, new applications development and maintenance.
The GM and Ford plant closings, Mercks layoffs, and other events dont bode well for U.S. manufacturing, but the nations economy is still growing, and we see some more growth in the oil, gas and petrochemical industries, says Taylor. So, if youre not going offshore, then you have to continue to find ways to cut costs, and deliver value to the customer. This means service and support become even more crucial factors, and must include everything from thoroughly educating staff to having a well-designed and useful web site.
Taylor adds that many control product suppliers also are seeking to provide the broadest possible hardware and software product lines. This is necessary so they can offer more complete solutions and one-stop shopping to their customers. The most exciting areas involve the wired and wireless networking capabilities that now are being tied to many machines and processes, adds Taylor. Ethernet especially is coming on very strong, making the biggest share gains, and is becoming almost a de facto standard.
Worldwide Machine Safeguarding Shipments (in millions of $)
- 2004 -- 1,050
- 2005 -- 1,120
- 2006 -- 1,240
- 2007 -- 1,310
- 2008 -- 1,440
- 2009 -- 1,570
ARC Advisory Group reports that the supply side in the safeguarding solutions field is reorienting to serve machine builders and other users. Source: ARC
Other technological advances include the continuing emergence of safety systems in discrete applications and their integration in machines where they hadnt been used to such an extent before, according to Sal Spada, research director at ARC Advisory Group. He adds that servo-controlled welding is another likely growth area because it reduces the costs associated with traditional pneumatic-controlled welding, and delivers better thickness and torque control.
Perimeter guarding and light curtains are becoming almost passé as manufacturers want their operators to work more within the envelope of their machines, Spada explains. To achieve this safely, safety systems are being integrated into control systems. Were seeing advanced safety systems being integrated with robotics and complex machining centers, which have multiple access gates, but can function safely while operating. A lot of this is happening in Europe, where manufacturers are using electronic subsystems to program servos and other devices.
Spada adds that Europe already allows controlled e-stop functions in machines, which provides a competitive advantage. However, he says the U.S.-based National Fire Protection Assn. and OSHA are expected to approve similar rules soon . Machine builders should focus on being able to operate in a safe-but-still-powered mode because it can reduce the cost of employing safety systems, says Spada. Machine builders might also want to consider shifting from using highly electromechanical hardware to more software-controlled subsystems and automation. To remain competitive, theyll also have to incorporate software design processes in their organizations, so they can more efficiently design and place machines, and deliver more customized designs for target applications.
Builders also need to look at software reusability and object-oriented design, adds Spada. This is because theyve already addressed the 40% of a machines development that involves mechanical design and the 10-15% cost of electrical layout, but they havent addressed the 25-30% of development related to software, he states. They just need to look for solutions and control platforms that are easy to integrate.
Because software is beginning to permeate every area of machine design, Spada says software management issues are becoming more important for machine builders. Simply having a manufacturers different product-line divisions talk to each other can help them reuse code where appropriate.
Though the big corporate events grab headlines, we believe theres going to be a ramp up and greater use of automation in North America to help companies keep pace with less-costly labor from other regions, says Spada. In fact, there are a lot of products that cant be built without automation now, and thats only going to increase as automaton tasks get smaller and tolerances get tighter. As a result, the U.S. is going to retain many value-added applications, and rely on automation and intelligence tied to it business goals.
In fact, McGibben adds, BMW, Hyundai, Toyota, Daimler Chrysler and Honda are adding to their manufacturing capacity in North America, and so employment in the auto industry should actually increase in the near future. Also, he reports that Chrysler, Hyundai and Mitsubishi are opening six plants worldwide as part of their joint engine-making program, and that two of these plants will be in the U.S.
The auto industry is spinning off requirements for more complete systems to first, second and third-tier suppliers, which is a challenge, but it also means that one or two suppliers no longer have all their business locked up, adds McGibben. This means that all the marbles are on the floor, and theyre just waiting for someone willing to pick them up.
U.S. Packaging Machinery Shipments and Forecasts (in millions of $ for selected machinery categories in 2004 and projected in 2007)
Machinery Category |
2004 Shipments |
2007 Forecast Value |
Projected Annual Growth Rate (%) |
Premade bag hanging, opening, weighing, filling and closing/sealing |
134 |
150 |
3.8 |
Bottling line machinery |
304 |
335 |
3.3 |
Capping, overcapping, lidding and sealing |
157 |
174 |
3.5 |
Cartoning and multipacking; and associated leaflet/coupon placing |
194 |
211 |
2.8 |
Case and tray forming, packing, unpacking, closing and sealing |
359 |
393 |
3.1 |
Coding, dating, printing, marking, stamping and imprinting |
528 |
658 |
7.6 |
Converting machinery (selected categories) |
152* |
174* |
4.6* |
Conveying, feeding, orienting; placing and related machinery |
1,123 |
1,228 |
3.0 |
Filling machinery -- dry products |
161 |
177 |
3.2 |
Filling machinery -- liquid products |
232 |
251 |
2.7 |
Form/fill/seal machinery -- bag/pouch |
220 |
250 |
4.4 |
Inspecting; detecting and checkweighing |
250 |
270 |
2.6 |
Labeling machinery |
366 |
437 |
6.1 |
Palletizing, depalletizing and pallet utilizing |
410 |
458 |
3.8 |
Shrink film and heat sealing |
165 |
186 |
4.1 |
Skin and blister packaging |
24 |
27 |
4.7 |
Wrapping machinery |
205 |
224 |
3.0 |
All other packaging machinery |
512 |
553 |
2.6 |
Total |
5,344 |
5,982 |
3.8 |
*Converting machinery is not included in the packaing machinery total.
AC Drives, CNC Systems, Motion Control,
PLC Markets Growing
FIVE RECENT research studies by ARC Advisory Group are projecting growth in the low and high-power AC drive, CNC systems, general motion control, and PLC markets:
- The worldwide low-power AC drive market is expected to grow at an 8.6% compound annual growth rate (CAGR) from just over $5 billion in 2004 to approximately $7.5 billion in 2009, according to ARCs Low-Power AC Drive Worldwide Outlook. The availability of inexpensive, reliable, miniature electronic components have resulted in low-cost, compact AC drives, according to the report.
- The global high-power AC drive market is expected to grow at a 5.7% CAGR from just over $2.5 billion in 2002 to approximately $3.3 billion in 2007. ARCs High-Power AC Drives Worldwide Outlook adds the need to reduce mounting energy costs is the most important driver of the high-power AC drives market.
- The worldwide CNC market is expected to grow at a 3% CAGR from $3.3 billion in 2002 to $3.9 billion in 2007, states ARCs CNC Worldwide Outlook. The study says declining new machinery sales will abate as demand for new capabilities boosts growth in the CNC-based machinery market. Also, an increasing buildup of manufacturing capabilities in Asia will spur demand for production-oriented machinery in the automotive and heavy machinery sectors.
- North Americas general motion control (GMC) market is rebounding, and will experience a healthy 6.2% CAGR from close to $900 million n 2003 to close to $1.2 billion in 2008 over the next five years, states ARCs General Motion Control Outlook for North America, Market Analysis & Forecast Through 2008. New automation standards for interfaces, programming languages, physical connections and protocols are helping to lower the cost of related equipment.
- The global market for programmable logic controllers (PLC) reportedly is surging due to implementation in fast-growing regions and expanding applications areas outside of manufacturing. Despite declining prices, the PLC market is projected to grow at a 4.6% CAGR from more than $6 billion in 2003 to more than $7.5 billion in 2008, says ARCs Programmable Logic Controller Worldwide Outlook.
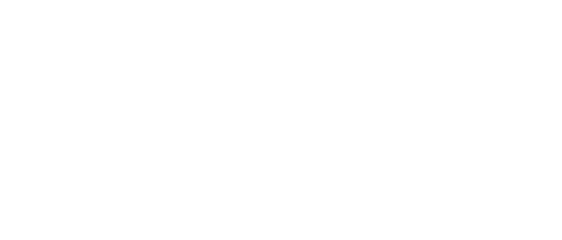
Leaders relevant to this article: