THE INTERNET is on the plant-floor. Web-based technology is now a common tool in many industries, particularly where centralized machine control or process functionality is important. Embedded web browsers are successful in many distributed processes, communicating with centralized monitoring and data evaluation centers. Data streams coming from multiple web-enabled points simultaneously allow operators, on or off-site maintenance, production supervisors, and other connected individuals to observe whats happening at any time.
Data latency isnt an issue in most processes, so delays in delivering information in real-time usually arent a problem. Trending critical events on a polling basis is adequate for most processes. Keeping processes operating within defined high and low limits allows centralized supervisory control to be more effective than scattered, localized control and monitoring stations.
Where genuine real-time information is needed, software layers have been developed to capture data in a defined determinism to provide faster reactive capability.
For instance, as raw materials are converted to discrete product, the need for more real-time information becomes essential. If production processes are disrupted, the raw material feeding that process might keep coming. In a float glass plant, for example, if any of the cutting, separating, stacking and/or packing equipment breaks down, theres no choice but to break glass. Fortunately, glass can be recycled, but many other raw materials converted to off-spec products cant be recycled effectively.
Functional Differences
Many machines still operate as fixed automation devices that produce one part or product continually, and are controlled by PLCs. While they excel at providing mission-critical, real-time control, most PLCs arent configured to deliver mission-critical control data at specific times, that is, without adding costly communication modules and a layer of communications software.
On the other hand, many machine control schemes use PC-based control with a real-time operating system and IEC-compliant soft-PLC technology to deliver data because most communication ports (Ethernet, USB, etc.) are built into the industrial PC platform. Adding an Ethernet port to an industrial PC is trivial compared to the sticker shock of adding an Ethernet module to a proprietary PLC platform.
Openness in most PLCs comes at a high price, says David Cole, president of Cole Controls, Ft. Wayne, Ind., a controls integrator for several different machine builders. Either you spend extra money on a PLC CPU card that has a built-in Ethernet card, or you buy a plug-in Ethernet card suitable for data collection.
In contrast, Nick Siliciano, mechanical engineer for Package Machinery, Co., West Springfield, Mass., reports that regardless of the cost and multiple layers of intelligence in his companys machines, his preferred method is to integrate web-based control. We use a common PLC platform with an Ethernet module, then provide a separate HMI platform that includes software for establishing Internet protocol (IP) addresses for each machine, he states.
Similarly, Syscon International (SI), South Bend, Ind., provides manufacturing execution (MES) and monitoring systems for both retrofit and new machine applications. SIs technology monitors and processes mission-critical operating data from injection molding, blow molding, thermoforming, metal forming and other processing machines. Syscon uses a slightly different and more streamlined approach, explains Rick Goldstein, Syscons corporate VP. Syscons PlantStar is a totally web-based technology, says Goldstein. Our strategy is to embed a browser at each machine, deliver that information to our own Linux-based Apache server, then work through the customers IT system by Virtual Private Network (VPN) to deliver the information in virtual real-time. Each intelligent I/O station has embedded pages that provide Down Reasons, Job History, Reject Reasons and other important information. (See Figure 1 below)
FIGURE 1: PROCESS INFO BROWSABILITY
So Lets Browse
The machine environment (See Figure 2 below) suggests theres relatively easy access to machine data with web-based technology. The client might exist at the MES level or at the enterprise level, often, but not always, in the same plant. In many applications, these clients include pages that are delivered by a server somewhere in the enterprise, either locally or from afar. These pages are delivered and stored on the clients. Often using Java applets, page sophistication is determined by the type and amount of information required and the machines complexity.
There can be relatively easy access to machine data with web-based technology. The client might exist at the MES level or at the enterprise level, often, but not always, within the same plant. In many applications, clients include pages that are delivered by a server somewhere in the enterprise, either within the same plant or afar.
Our primary use for a web interface is to provide an economical means for remote control of our packaged chillers, says Joe Huber, R&D manager for packaged chillers at Ketema LP, Grand Prairie, Texas. In most installations, our equipment is installed in a remote area of the factory or in outdoor locations, where its inconvenient for the equipment operators to obtain readings and change set-points. Most of our customers have an Ethernet network in their plants, and have PCs with web browsers attached to that network. Using the web capabilities of the NX controller allows our customers to quickly interface with our chillers, without needing expensive OPC servers, protocol translators, or installing a serial network to connect the chiller to a monitoring computer.
In addition, Horner Automation Products Group, an Indianapolis-based, global manufacturer of HMI and machine control products for machine builders, provides Ketema LP with its web-enabled operator control station (OCS). Many of our machine builder OEMs are using our integrated web-server capabilities to provide machine maintenance services to their customers, says Chuck Ridgeway, Horners OCS product manager.
Ridgeway believes Horners machine builder OEMs are uniquely qualified to make the right recommendations for proper predictive maintenance and parameter updating based on real-world conditions. The integral HTTP and FTP web services in our OCS, all-in-one control platform (HMI, PLC, networking hub, and I/O access) enable machine builders to accomplish remote monitoring and maintenance.
Basically, we need to keep in mind that web-enabled data gathering is one thing. Doing control over the web is quite another.
From our experience, its best to leave the actual machine control to the PLC or intelligent motion controller, advises Marty Huff, director of computing solutions at MSI Tec, Centennial, Colo. A web browser is a great way to monitor, stop and start processes, and call routines from a device. The top advantage is that every computer already has a web browser. There is no client software to load or client licenses to track. MSI Tec is an automation integrator for machine automation technologies, and specializes in implementing web-based technology as part of a machine control strategy.
For example, Alcoa Packaging Machinery (APM), Englewood, Colo., builds a can decorator machine with print heads that sometimes lose alignment (See Figure 3 below). Sensors detect when a print-head comes out of alignment. Then, using embedded web-based technology, alarms are generated using a web-tablet format to deliver this information via wireless Wi-Fi to an operator, explains Huff. Providing real-time monitoring on the machine saves a significant number of misprinted cans.
Alcoa Packaging Machinery builds a can decorator machine with print heads that sometimes lose alignment. Sensors detect when a print head comes out of alignment, then, using embedded web-based technology, alarms are generated using a web-tablet format to deliver this information via wireless Wi-Fi to an operator. Source: MSI Tec
As an M2M integrator of RTP software to major machine builders such as Mori Seiki, Haas, Daewoo, Fadal, and Van Dorn, B2D Solutions, Cleveland, argues that embedded browsers provide competitive advantage for machine builders. It provides a collaborative platform for others, but only as part of a much broader strategy for generating value, says Bill DeCamp, chief technical officer. B2d Solutions has installed web-based technology on different machines including many CNC-based machine tools from those listed above. On most installations, the emphasis is on remote diagnostics and centralized HMI capabilities.
Get Real-Time Data, Too
B2d Solutions strategy employs a MES-level software platform to monitor real-time information on legacy machines in plants and new machines by tying existing machine mounted devices to information centers via its field-installed Intelligent Device Module. For machine builders, B2d solutions implements its Embedded Device Module that is fully integrated with each machine mounted device to be monitored.
For real-time, mission-critical information gathering, Syscon Intl. installed a system at Keneka-Texas, in Jackson, Mich., through a proprietary machine builder from Japan. Keneka-Texas manufactures automobile doors out of a polypropylene slug.
Its essential to precisely monitor the weight of the slug, then all molding variables throughout the mold cycle, to assure that the door produced meets rigid structural [actually crash test] standards, says Sycons Goldstein. During the process, a bar code is embedded in the final molded product. We record that code and all associated process variables, and then deliver the information to an installed Apache server via the web technology. At this collection point, the information is accessible to Keneka-Texas at any time. If process parameters measured are over prescribed limits, the part is rejected.
The Security Issue
Web browsers let user and machine builder get access to a machine buried someplace in a remotely located plant with a gateway infrastructure in place to deliver the required information to an enterprise-level server. But how does a machine builder get through the firewall to do diagnostic troubleshooting?
Weve found it necessary to work with IT departments instead of against them, says Huff. With the current trend to extend IT systems to the factory floor, MSI Tec believes its easier for IT departments to embrace machine-control-embedded web browsers. Browser-based technology is actually easier for IT departments to implement because theres no client software to install or track," adds Huff. Security can be somewhat of an issue if the application is accessed across the companys local area network (LAN), and even more of an issue if that LAN is accessible through the Internet. MSI Tec recommends isolating the existing LAN by using a different subnet, or a separate network hardware connection media.
Machine builders connect into the plant via their Intranet or through VPN, says Hughes. However, many plants allow read-only access. Others use multiple layers of security including firewalls and multiple passwords processing, especially for real-time information."
When Not to Browse?
USING A web browser is hardly a universally accepted concept. In some machine builder segments, its still seen as unnecessary.
Warren Witten, engineering manager for the Pittsburgh, Pa.-based Exonic Systems Division of BW Rogers Co., an integrator and builder of custom special machines provides immediate access to downstream automated machines. However, Exonic doesnt provide web-based technology to access those machines, says Witten. We transfer the knowledge to maintain and support these machines through extensive training programs during machine acceptance. That, coupled with the appropriate spare parts at the installation site, allows the plants to take care of themselves. Perhaps its old school, but it works in the glass industry. Our customers are not asking for web-based technology, so we see no need to push into this strategy.
Similarly, Samtec, New Albany, Ind., an electronic assembly manufacturer that builds most of its production machines in-house, professes a similar philosophy. At present we see no need to connect any machine to the Internet, says Steve Kaake, electrical engineer. We use similar controls in most machines, and people here know how to troubleshoot and maintain them.
Likewise, two winding machine builders, Windamatic, Huntertown, Ind., and Alliance Winding, Ft. Wayne, Ind., indicate no real urgency to employ web-based technology on their machine controls just yet. However, Kevin Leech, Alliances control manager, says his company is considering the possibility of including web-based technology on some of our machines in the future.
Bill DeCamp of B2d knows it doesnt apply everywhere. Our experience has been that embedded browsers arent always reliable for industrial controls, he says. They have limited capacity, and when the web server fails on a Windows CE platform, for example, it affects other parts of the operating system. We try to limit browsing to the device thats only for troubleshooting and maintenance purposes.
MSI Tecs Huff says there often is some latency when accessing a device across a network, depending on the network configuration and traffic, but insists thats not a total deal killer. Several steps can be taken to decrease latency, including providing higher bandwidth networks, using managed switches, and isolating the device from the companies LANs, he adds.
About the Author |
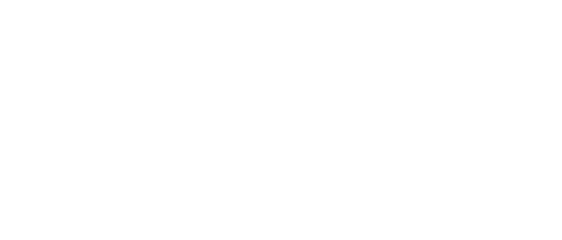
Leaders relevant to this article: