In 2006, Mark Lamendola was a freelance writer and frequent contributor to Control Design with many years of experience working in and writing about industrial automation issues.
In Ethernet networks, the three main hardware components besides cable and connectors are hubs, routers, and switches. How and why you select and implement each of them will determine the functionality, reliability, security, and flexibility of your industrial network. Let's look at these devices, starting with the simplest of the three.
SEE ALSO: Routers and Switches Continue Directing Industrial Network Traffic
Hubs in the Network Universe
A hub acts much like those three-way plugs you might use in your home's electrical outlets. Hubs simply connect one pathway to another. This capability can actually complicate things, reports the engineering staff at FLG Networking Services in Overland Park, Kan. FLG provides network design and security services to industries that include polymer processing, paper goods, and printing. "When you put multiple devices on a cable without some kind of traffic control, you get collisions," says Fred Granville, FLG's principal. "Hubs assume every device is on the same IP subnet." In short, a hub doesn't differentiate between the data paths it's connecting; it just connects them.
"We generally don't recommend hubs, but they still have a place," advises Dan Parker, project applications engineer at Curry Controls in Lakeland, Fla. "For fieldbuses, the hub provides an essential function for impedance matching and multiple connections. And, where a customer requires a simple data connection, we use simple, low-cost hubs to provide it." Curry provides design, engineering, integration, installation, and service for industrial and municipal process control and radio telemetry systems.
So, hubs are useful when you don't need to differentiate between the data paths you're connecting, and just want low speed and no processing in that connection. "We develop our own control systems and use Ethernet in special ways that are internal to our system, so we use hubs to monitor traffic," adds Ernesto Colon, vice president of Turbine Diagnostic Services in Odessa, Fla, a field service company servicing power-generation equipment, manufacturing turbine, and balance-of-plant (BOP) controls for various industries. "We also use hubs due to cost and lower latencies."
In short, because hubs have limited capabilities, the heavy lifting in networking is left to the routers and switches.
An industrial communications network can be as complex and multi-layered as the production machine system itself, in this case, a paper-making system.
Source: Contemporary Controls
Routers Provide Direction
Granville explains that routers are critical for networking. "A router provides a connection from one IP subnet to another, allowing you to talk between IP networks and subnets," he says "Routers interconnect local area networks (LANs) and virtual LAN (VLAN) segments in a switched environment. However, a router doesn't propagate broadcasts. Switches do."
Routers also solve some otherwise intractable security problems. "One customer wanted a webcam, but didn't want to open its network to an outside connection," says R. Andrew Bowman, PE, vice president for engineering at SiteSecure in Sanford, Fla. "We plugged a router into their network. The router became the device with the IP address." SiteSecure provides security and safety solutions, including design, installation and startup.
Parker also has seen many misapplications of routers. "Usually, these result from the great divide between the plant-floor, industrial types and the information technology types," he explains. "The IT folks want every device on the network to be DNS-enabled, so they have control over the device. The plant-floor folks want every device to have a fixed address, so it can be communicated with simply and easily on a regular, repeatable basis, as with, for example, PLC-to-PLC communications."
Parker believes the problem goes beyond turf battles. "Routers often operate as DNS servers," he continues. "In the typical scenario, the plant goes into operation and everything is fine until there's a power failure. Then, as the power-up order changes, each device is re-assigned an address. This drives the control system crazy, and production time is lost while it's all sorted out."
The heat-sink capability inside this managed switch allows it to perform reliably in high-temperature environments.
Source: GarretCom
Switches Make it happen
While routers connect networks together, switches actually run the network. This is when expertise-driven functions such as product selection, system design and installation can quickly become complicated (Figure 1).
So, the switch is the real workhorse of industrial networks, as Granville hinted, but it needs to be industrial grade. "Industrial switches have several advantages over their commercial counterparts," says Roger McFall, control systems project manager at A&E Engineering in Greer, S.C., which provides automation and information services from design through integration. "Compact size with DIN-rail mounting is one advantage. Low port density is another because many plant applications have a small number of Ethernet devices per panel, but have many panels."
Steve Byars, also a control systems project manager with A&E, adds, "The ruggedized, higher temperature, and vibration specifications of industrial switches (Figure 2) are critical in harsh industrial environments."
SEE ALSO: Manage Your Network
All of these networking pros agree that you have to use industrial switches, not consumer-grade ones. The next decision about switches is whether to choose managed or unmanaged.
"If switches, cables, or any other connected devices experience communication failures, a managed switch can alert you," says Wright Sullivan, A&E's vice president. "With an unmanaged switch, you find the problem only after equipment has failed, so you're flying blind."
Granville adds, "As a rule of thumb, I don't recommend using unmanaged switches in an enterprise. An unmanaged switch provides dedicated bandwidth per port, but there's so much more you can and should do with a managed switch. Troubleshooting, for example, is a huge issue.
This panel is equipped with PLCs (right), an access point (top left), and directly below the access point are industrial Ethernet switches with fiberoptic connectivity.
Source: Curry Controls
A&E's Byars agrees. "Most managed switches come with a web browser tool for monitoring your entire network down to the port level," he adds. "For any network larger than a handful of switches, this is a critical tool for troubleshooting."
Parker says many of his customers require managed switches for any Ethernet networking project because they provide efficient delivery of network data packets.
It gets better. "We completed a project for a water company, connecting six RTU cabinets via managed switches," says Mike Nicholas, senior project manager for Emerson Process Management's Bristol division in Watertown, Conn., which supplies and commissions remote automation units for process and other industries. "The switches allowed 10/100 Mbps Ethernet connectivity to all RTU cabinets. Fiberoptic cable extended the connection distance far beyond the 100 m limitation of 10BaseT cable. The self-healing ring switches ensured that bandwidth was maintained for all connections, and provided network reliability with dual, self-healing communication paths."
Managed switches also help avoid the tyranny of numbers that results from setting up separate physical networks for each department, such as IT versus plant systems. "If you're sharing infrastructure with other departments, you need to manage your switches with a virtual network," warns Bowman. "You have to subdivide physical switches into VLANs. It's a matter of assigning specific traffic by function to specific ports, so you have no crosstalk between functions."
With separate networks, the accumulation of multiple device footprints makes it difficult to have a space-efficient installation (Figure 3). Bowman identified two other problems. "Deploying physically separate networks can be very expensive if there isn't sufficient cable to support a second network, and it adds to the infrastructure the IT department must support," he cautions. "Managed switches provide the answer to both of those downsides."
There are more reasons to use managed switches. "Intelligent switching gives you control over the network and control over the device," says David LaBree, CTO of Prime Telecom in Tampa, Fla., which provides network engineering, integration, and maintenance services to municipal and ISP networks. "This speeds up troubleshooting immensely. You can logically go through the troubleshooting process, rather than physically going into the field. A device might seem to be malfunctioning, but the problem could be the communication to the device."
In addition, the push since 9/11 for security enhancements has required Prime's installed network to allow for additional devices such as IP-enabled security cameras, VOIP audio capability, and badge/card reader systems, says Parker. "We can set up a VPN within a managed switch, and allow for segregation of the industrial control equipment and the security systems," he adds.
Bowman says many layers of security come with more sophisticated hardware.
Complete the Thought Process
While correct hardware selection is critical, it's not the end of the story. "There are tradeoffs," points out Bowman. "You have to plan your system. Simply adding things as you go can make implementation more difficult and costly."
Existing standards help with this planning. "By using standards such as Rapid-Spanning, Tree Protocol (RSTP) for fault tolerance, designers can increase network availability and reliability without resorting to proprietary or complicated techniques," says Sullivan.
Fred Granville, principal of FLG Networking Services, identifies seven things users can do only with a managed switch:
1. Provide redundant connections between a pair of switches, and have both carry traffic
2. See into traffic (port errors, volume, type of traffic)
3. Phone home
4. Create virtual local area networks (VLANs)
5. Do VLAN trunking
6. Implement quality of service (QoS)
7. Prioritize traffic
What standards are Byars and Sullivan talking about? "Hubs and switches can carry many types of protocols," says Granville. "They aren't tied to TCP/IP, but that's pretty much the standard protocol today."
Two other often-overlooked standards that can be critical are VLANs and Quality of Service (QoS). "These tools allow you to separate mission-critical control traffic from lower-priority traffic to ensure that critical messages go through," says McFall. "These capabilities are found only in managed switches that support the 802.1p and 802.1q standards."
Of course, you need to connect the devices correctly. "Don't neglect correct cable selection or overlook cable routing," warns Colon. "We even color code the cables by function."
As Ethernet devices proliferate, the plant-floor network becomes an even more mission-critical infrastructure. "Proper use of managed switches, IT standards, and a well-designed network are the keys to reliable manufacturing in the Ethernet era," concludes Sullivan.
Common Mistakes, Uncommon Problems
Another reality is that sometimes users get networking wrong, and misapply redundancy, for example. "One project required redundancy on network switches with fiberoptic capability," Parker says. "The consulting firm provided the fiberoptic backbone design, but called for single, multi-fiber cables to each switch with redundant connectivity provided by using differing pairs of fiber. We recommended improving this by using separate cables and paths, which resulted in half of the redundant backbone being run down the left side of the production line and the other half run down the right side." This turned out to be a smart recommendation.
"Each redundant path had spurs to each item of equipment," adds Parker. "The cost of this enhancement seemed excessive to the end user until a plant incident rendered the right side of the production line cabling unusable. The left side of the line network continued to operate and allowed for a safe, fully automatic shutdown. This functionality can be implemented only with redundant-ring-enabled network switches."
Unfortunately, Colon says, security and reliability often lose out. "Customers hear the pitches about wireless and just start installing equipment," he states. "They don't realize they're opening their networks to hacking and possible sabotage."
Granville couldn't agree more, saying, "Implementing wireless correctly requires extensive expertise."
Bad communication during planning is, perhaps, the biggest mistake. "The IT department and the plant floor must communicate up front," Parker insists. "This precludes a lot of heartache and sorrow during the implementation phase of a project. The IT folks must understand what the plant floor needs and vice-versa."
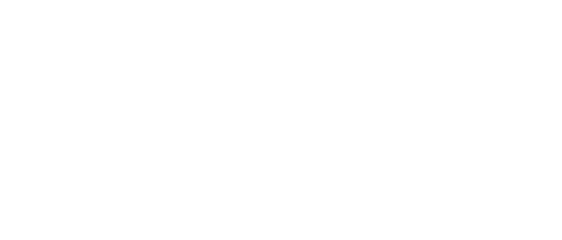
Leaders relevant to this article: