MANY ENGINEERS believe that water, in all its various forms, is the most insidious force in nature.
Sure, it’s tasty and essential for life. Yes, we’re three-quarters water ourselves. Some, yawn, astronomers think liquid H2O might be the most precious substance in the universe because of the relatively tiny temperature window it needs to exist.
However, this is small comfort to anyone who’s ever had to mop up a flooded basement, keep moisture out of delicate instruments, or clean up an inundated neighborhood or city. Whether pulled down by gravity or condensing out of the air, water literally gets in everywhere.
Ironically, though they make their living cleaning up wastewater or supporting those that do, several engineers in upstate New York this summer had far more cause than they expected to sympathize with folks in New Orleans and along the Gulf Coast. That’s because these municipal, electrical, and construction professionals had to cope with and recover from a devastating, late-June flood at their wastewater plant. And, as if this wasn’t enough, these engineers had to deal with the extra tragic twist that they were within five weeks of finishing a major retrofit of their plant.
Renovation Innovation
About two years ago, the Binghamton-Johnson City Joint Sewage Treatment Plant in Vestal, N.Y., started a $55-60 million retrofit project to improve its capability and capacity for treating wastewater. The plant also needed to comply with U.S. Environmental Protection Agency and New York State Department of Environmental Conservation regulations, according to Art Van Gelder, project manager for C&S Engineers, Syracuse, N.Y., which is the project’s design, build, and construction management firm.
The original plant had six primary settling tanks, four secondary settling tanks, three thickeners, three digesters, a belt filter press, a composting facility, and equipment for grit handling and other tasks.
However, because its 18.5-acre site is hemmed in by neighbors, a road, and two rivers, the plant’s construction and electrical engineers had to find a way to increase its capacity without increasing its footprint. The designers eventually settled on plans to implement an innovative biological aerated filter (BAF) system. Though this technology is gaining popularity in Europe, where riverfront space also is scarce, Van Gelder says there are less than a half dozen of these installations in the U.S. The Binghamton-Johnson City plant eventually bought its BAF system from Norway-based IDI Systems.
The initial reconfiguration involved converting the plant’s four secondary settling tanks into primary settling tanks, which typically have slower flow rates. New tanks added to the facility included eight carbonaceous filters, eight nitrification filters, and four de-nitrification filters, as well as backwash pumps, a second inflow pump station, and fine-screen rooms.
To monitor and manage all of the plant’s new equipment and systems, C&S and Matco Electric, Vestal, N.Y., networked pneumatic control valves on the plant’s 21 motors with Foundation fieldbus (FF) and DeviceNet protocols via Turck’s molded cables, connectors and cordsets. These motors average 200-300 hp, but include a few 450-hp units.
Installing twisted-pair Foundation fieldbus and DeviceNet terminated with molded cordsets reduced the amount of hardwiring used at the wastewater treatment plant. These waterproof cables and connectors survived a late-June flood without needing the deconstruction, drying, and rebuilding that a regular wire-in-conduit job would have required.
The new network also controls the plant’s level, flow, and pressure transmitters, as well as its analyzers and level switches. This twisted-pair networking topography, enabled by FF and DeviceNet, reduced the plant’s hardwiring by thousands of feet (See Figure 1). The plant previously relied on a point-to-point architecture that filled its existing cable trays. When it’s installed, FF’s cable usually contains one pair of wires for data, and one drain wire. DeviceNet cable usually has five total wires, including one pair for data, one pair for power, and one drain wire or shielded conductor.
Dan Dvorsky, Matco’s general foreman, says DeviceNet generally is used to control valves and pumps, while FF monitors the flow and level transmitters. The supplier provided custom-length cables and ends for a total of 200 valves on 20 tanks.
These improvements and the BAF system are designed to increase the plant’s capacity from 18.5 mgd average flow, with a peak of 23-25 mgd, up to 60 mgd. It was IDI’s developers that advised the plant to adopt FF and DeviceNet.
Flood and Recovery
Because water treatment plants are situated near channels that can accept their effluent, the Binghamton-Johnson City facility is located at the confluence of the Susquehanna and Chenango rivers, which both feed the greater Delaware watershed (See Figure 2 below). “All of the surrounding communities are higher than the plant,” says Van Gelder.
The Binghamton-Johnson City Joint Sewage Treatment Plant is located next to (and occasionaly in) the confluence of the Susquehanna and Chenango rivers.
Because its location is necessarily hazardous, the plant was in a vulnerable position when extremely heavy rains and resulting floodwaters arrived over a three-day period beginning on June 28. Most of the facility and its new construction ended up under about 8 ft of water. The rivers reportedly reached 4-5 ft above their estimated 100-year flood level. This is the level that water treatment plants are usually designed to withstand.
New construction damaged or otherwise affected by the flood is estimated at $10.3 million, which is what it would reportedly cost to get the plant back to its pre-renovation state. Total damage to the plant was reportedly $15-25 million.
In fact, this was the fourth flood that has occurred during the two-year renovation project. The first two didn’t affect the plant or the project, but the third in the spring of 2005 reached the 100-year level and delayed the renovation by about five weeks.
The treatment plant has continued to treat sewage from its customers, even while its staff carries out flood-related repairs. However, it’s still not known how many more months it will take to completely repair the plant, or when its new capacity will come online.
Cordsets Eclipsing Conduit
When a catastrophe like a flood happens, people often find that few of their usual, sophisticated tools have survived. One of the very few bright spots for the plant’s staff and consulting engineers is that Turck’s over-molded, IP-67-rated cordsets used in the renovation and the BAF system survived the flood pretty much unscathed. This meant that the plant’s staff didn’t have to clean and rebuild these network components.
“A lot of the new installation was underwater,” says Dvorsky. “However, our new cables and cordsets were waterproof enough that they survived. We didn’t even have to clean and dry them out like we did with all of our other electrical conduit.”
Van Gelder adds, “If we’d had regular electrical conduit instead of these molded cordsets, then we would’ve had to take it all apart, clean out the water and silt, and rebuild them.” Also, the fact that the plant converted from point-to-point hardwiring to twisted-pair FF and DeviceNet meant that there were far fewer networking paths, cable runs, and other equipment to clean out.
Another advantage of using pre-made molded cordsets is that they’re becoming less expensive for users than buying and assembling separate components. When originally called in on the Binghamton-Johnson City project, Turck reviewed several connector and I/O concepts to determine which would be most efficient.
“The original plan was to buy the big traditional spools of wire ands lots of field-wireable connectors, but we first compared the cost of this typical wire to molded cordsets,” says Kim Anderson, Turck’s business development manager. “What we found was that a 5-m piece of cable and two field-wireable connectors was $90.30 and would have a good rating, but still have the possibility for leaks. However, a pre-made, over-molded, 5-m cordset would only cost $79.50 and is entirely sealed against possible leaks.
So, traditional wisdom that custom-made cabling is more expensive than assembling cables on your own appears to be wrong in some cases. Anderson attributes this to several factors. “Cable molding machines are being improved and working faster these days, so they can make a greater volume of cable for less cost,” he says. “This retrofit converted pipe and wires to an open-wiring configuration, but was still able to maintain that same level of safety.”
Because they had experience with water getting into their conduit before, Anderson adds that Binghamton-Johnson City’s engineers and contractors initially were looking for alternatives to pipe and wire, but were concerned about the customized cables coming up too short or too long. However, the varied lengths and standardized connectors of the cordsets actually make them more flexible than traditional wiring. “This allows users to pull devices such as valves or transmitters out of service much more easily, and work on them at the more-comfortable workbench level,” says Anderson. Also, if users ever want to add on to their cordset-based network, they can simply extend with more connectorized cables.
“When mistakes occur, we also have a job box that allows users to make cables available at different lengths,” adds Anderson. “This makes contractors and end users a lot less worried.” Reducing worry is always good, but it’s especially helpful when a natural disaster comes along.
“When the flood happened, and so many of the devices and cables were underwater, the contractors called Turck because they thought they’d have to pull apart, clean, and dry the cordsets like they had to do with conduit,” says Anderson. “However, our over-molded cordsets were fine. They didn’t have to do anything, and so they could go on to other repairs.”
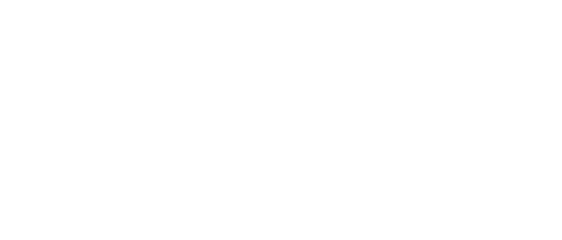
Leaders relevant to this article: