Its ironic that sometimes even high-flying software needs some help from meat-and-potatoes industrial networking hardware. Its doubly ironic if that hardware is wireless.
This was the case for Cornucopia Tool & Plastics of Paso Robles, Calif., which uses a variety of injection molding machines to produce a wide line of plastic products and injection machine molds. The company partnered with Integrated Quality Management Systems (IQMS) of Paso Robles, a developer of enterprise resource planning (ERP) software, and wireless hardware developer Crossbow Technology in San Jose, Calif., to beta test a wireless data handling system.
When reconfiguration or relocation of machines is required frequently due to product demand, any associated disconnection and reconnectionof the ERP systemsometimes involving rewiringcan be daunting. This wireless system eased the problems associated with machine relocation.
The IQMS system Cornucopia uses evaluates signals every time its assigned work-center completes a cycle, and helps to route resulting products to the next center or to an inventory management system. The software also tracks raw material use, labor, and overhead costs.
The data stream from the work-center reports whether its running, and the bill of materials shows whether that machine should be running. This allows users to track their application up and downstream, and enables them to potentially run leaner.
IMQS has developed enterprise resource planning software since 1989 for manufacturing users, especially for plastic injection molding and die-cast metal applications. The company added a real-time production monitoring module in 1993, and its EnterpriseIQ (EIQ) system has been hooking simple sensors up to machines since 1997.
The beta test involved plugging a wireless board into an sister board with a sensor.
Instead of going over the usual wires, data now travels at 2.4 GHz over an IEEE 802.15.4 Zigbee physical layer. This network is arranged in a automatic-routing, self-healing mesh configuration, which allows its data packets to hop to the closest hub (See Figure 2 below).
FIGURE 2: RUNNING ONBOARDThese routing parameters usually are built into the wireless systems software (See Figure 3 below).
FIGURE 3: WIRELESS SOFTWARE LEVELSOur stress testing showed the network can handle signals every 0.6 seconds. When the distance to the gateway becomes too long, we can just add another wireless mote, says Randy Flamm, IQMS president. When were dealing with real-time signals, some latency gets added when a signal goes into the Oracle database. In a wired environment, a real-time, PC-based server watches these signals. So, it required us to do some development to eliminate this latency in our new wireless environment.
As with most wireless networks, maximum distance between transmitters and their gateway can vary widely depending on how crowded a location is with heavy machinery, electrical interference, and/or other obstacles. The boards in this solution operate with a maximum distance around 100-250 ft. before another node is needed, according to Joerg Bertholdt, Crossbows marketing vice president.
Early on, we saw that our board also needed some additional filtering because it was picking up some interference at 60 MHz on some of the 10 V components, adds Bertholdt. We took more queries from the database, and again compared the wired and wireless performances to locate the problem. The hardware indicated that we needed to supply better earth grounding to solve the problem at 60 MHz.
Evaluating Wireless
After building their wireless boards, IQMS, Crossbow and Cornucopia began the beta tests. The price tag for IQMS and Crossbows experiment also wasnt too burdensome for Cornucopia. It cost $300-500 per machine to outfit them with wireless boards, plus another $60-100 overall for 1,000 ft. of cabling arranged in a star topology. Flamm reports that a similar hardwired solution would have $700-900.
Cornucopia had our ERP system and hardwiring installed, and agreed to run our wireless solution in parallel, says Flamm. This gave us a unique opportunity to verify how our wireless signals compared to our hardwired signals.
Despite concerns that wireless might have more potential faults than hardwiring, the test found wireless wasnt more sensitive. Wireless data packets informed the system if signals were delivered successfully after machine cycles, and used the machines process controls to report if parts produced were of good quality. The developers even hooked up 1970s-80s vintage machines with relays and solenoids, and secured 12 and 24 VDC signals, again reporting when the devices completed their cycles. This allowed the systems PLC to confirm when products were being made. PLC interfaces to our board also say if parts are good based on robot inspections, adds Flamm.
Unexpected Applications
Besides improving its quality efforts, wireless could potentially help IQMS expand its applications into more sophisticated production monitoring and process control, as well as ERP related to orders and inventory, according to Flamm. IQMS uses Oracle exclusively for its database server.
We previously stayed out of these areas, but our customers are spread out over plants, and our ERP systems works on one centralized database, says Flamm. The database now allows us to see production data up to the second, and lets users tell their customers when shipments are most likely to occur anywhere in the U.S. or worldwide. They can also set database scans, for example, and show on plant-floor monitors if their machines are running lean (green), slow (yellow), or stopped (red).
Some machines monitored by the software also are being run by operators. Providing immediate operational information feedback from a wireless network also can help them adjust production more quickly in response to orders, reduce scrap, and keep inventories lower. Most importantly, this data can help prevent non-monitored production overruns, and the costs of making unneeded parts.
Similarly, keeping better track of machine cycles via wireless can improve maintenance scheduling for molds and tools attached to particular machines. The one board on each machine is able to serve all three types of devices.
At this point, were still just marking cycles and monitoring for quality. Were not doing control yet. In the future, were going to learn how to send temperature and pressure data via wireless, too, says Flamm. Weve been working with wireless for about one year, and its scary how fast its grown. We started at one plant, and then had orders to install three more this past July. So now our wireless solution is on about 100 machines in four different plant.
Our solution allows us to hook up any type of cyclic process. Were also going into metal-stamping machines, and this will allow us to generate a signal for every stroke. This isnt just process data. This really is a business solution.
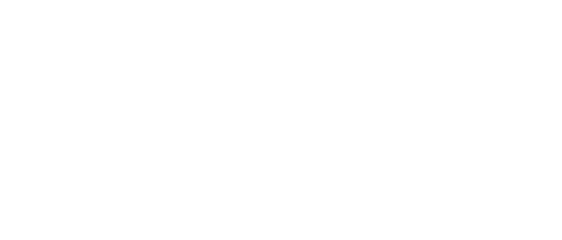
Leaders relevant to this article: