QUESTION:
I need to find a control network with sufficient vendor and industry support—a control network for which I can find multiple sources of controllers, motors, drives, sensors, power controllers, HMIs, pneumatic components, and hydraulic components. What’s my best option?
– From January 2007 Control Design
ANSWERS:
Ethernet Is the Answer
We use Ethernet as a machine interconnect network almost exclusively. Ethernet is the most popular PC network, and PCs are becoming more common as industrial control elements and platforms for developing operator interfaces.
There are some specialty applications—multiaxis synchronized motion systems or systems polling a lot of data—that require time-critical data gathering at 20 msec or faster scan rates. In these applications, Ethernet’s lack of determinism can be an issue, but bandwidth advances being made will continue to erase these constraints.
We often configure operator interfaces using Visual Basic (VB), and it’s easy to interact with an Ethernet network using VB software. Other HMI packages for the PC also support Ethernet, so designers’ choices aren’t constrained. We’ve worked with various remote I/O, different drives, and many PLCs. The majority of new devices support Ethernet connectivity.
For example, we recently finished developing an inkjet marking system for a machine that boxes apples. We used VB to develop the operator interface and Ethernet to connect to the inkjet print head. In the old days, proprietary hardware and software would have been used, but the open system approach using Ethernet made the system much easier to design and maintain.
Another benefit of Ethernet is that it allows users to combine standard off-the-shelf components for network hardware, providing a choice of manufacturer and vendor and, ultimately, the best price.
A side note: Ethernet media is standardized, but different manufacturers will support different Ethernet protocols. Users need to be aware of this as they define how hardware is integrated.
Although we think an Ethernet network gives many benefits to control system designers, we’re not advocating plopping a control system onto an existing Ethernet business network. Control networks need to be exclusively for control.
Clay Horste, Engineer, Concept Systems
We Like Modbus
In our experience as an industrial communications software developer and supplier, Modbus and Modbus/TCP are the most prevalent by far at the controller/instrumentation level. Since our inception in 1994, Modbus has been the leader due to the many devices and software that implement the protocol. This broad support is due to several reasons:
- Open, standards-based protocol
- Easy to deploy, scalable, and small footprint
- Media independent
- Available conformance testing
Modbus/TCP has become the No. 1 protocol for industrial Ethernet. We believe this is a result of more devices becoming Ethernet-enabled combined with a very small learning curve when moving from Modbus to Modbus/TCP.
Many devices that implement proprietary protocols also implement Modbus and/or Modbus/TCP, providing compatibility with a huge number of Modbus-enabled software packages, SCADA systems, and devices.
We see growing demand for EtherNet/IP, though not at the rate of Modbus/TCP. While EtherNet/IP comes with a wealth of pre-defined object specifications that handle a broad range of device types and includes mechanisms for bridging and routing, we believe the slower rate of adoption is partly due to the complexity of the multi-layered protocol.
Mark Markarian, Vice President of Engineering, Automated Solutions
Network Must Support Your Machine
The convergence of motion control and I/O networks has become an increasingly important evolutionary step in machine control because the market sees device networks incorporating motion control capabilities and motion control networks incorporating I/O capabilities.
In tandem, the latest generation of technologies and standards has further expanded the network capabilities with:
- Multi-master capabilities that reduce network traffic and improve event handling
- IEEE 1588 standard for time-based synchronization
- Self-healing networking technology for high-availability systems
- Ethernet-compliant networks that use existing, unmodified Ethernet, and reduce the number of specialized networks
- Ethernet-based networks that make modifications to Ethernet standards, and provide some level of compatibility for linking with standard Ethernet-compliant networks.
The challenge for end users and machine builders is to choose the networking technology that provides device interoperability during the lifecycle of the system. The requirements for networking technology should consider the designers’ efforts to incorporate alternative devices in both the motion control subsystem and in ancillary equipment.
The latest generation of motion control networks takes the integration of intelligent devices and I/O subsystems into consideration. These devices might not be motion control elements, but they need to be coordinated with the motion control subsection. It’s important to decide which solution has the greatest potential to meet current and future production needs.
Sal Spada, Research Director, and Himanshu Shah, Senior Analyst, ARC Advisory Group
Pick One of These Five
Engineers love to talk about baud rate and bitwise arbitration. For your typical application, these details really don’t matter. There literally are hundreds of industrial protocols that technically can do the job. Frankly, after 12 years in the business, discussing these technical details bores me to tears. The primary question to ask when choosing a network is simple: How well do the products I plan to use connect to this network? Consider both current and future needs. Here is a checklist:
- The network must connect well to your PLC—the most complex component. Like any product that connects to the network, it makes both a physical (electrical) connection and a logical (software) connection to the network. The PLC’s logical connection can become quite complex. At the very least it contains I/O data, but it also can contain diagnostic data, the ability to automatically reconfigure a replaced device, the ability to download logic, and/or other useful features.
- The network must connect well to other complex devices such as drives, HMIs and motion controllers. These are less important than the PLC, so if you have to make concessions, it would be better to make them here.
- The network must connect well to digital and analog I/O systems from multiple vendors. This is the last critical piece for your average control system. The best control system designs today connect sensors, pneumatics, and hydraulic components through I/O blocks or small, remote I/O racks. A hydraulic valve bank is at the opposite end of the software complexity spectrum from the PLC. In the case of a hydraulic valve bank, it’s best to choose the valve based entirely on how good the valve is, and then connect the valve to the network using a digital output card or a networked station.
For a Rockwell Automation PLC, DeviceNet is your best network choice. You might choose EtherNet/IP in heavy data applications with little I/O, or you might end up with DeviceNet on bottom and EtherNet/IP on top. With Siemens PLCs, your best choices are Profibus-DP, AS-Interface, or Profinet.
With other PLC brands, ask which networks they best support. Some European PLCs best support CANopen. This isn’t a bad choice, but it will limit your choices on drives.
If you use PC-based control, any of the above networks will work well. Modbus TCP/IP might also be a good choice.
None of the other networks meet my three requirements.
Bob Gardner, Senior Product Manager, Networked I/O, Turck
No Perfect Solution
In an ideal world, one motion network would support a wide variety of generic I/O sensors and drives from multiple vendors. This network would support high-performance motion control and diagnostics. A perfect network solution doesn’t exist for every industry, but one motion network has emerged as the ideal plug-and-play solution for high-performance motion applications. In performance controls markets such as the semiconductor, robotics, and electronic assembly industries, SynqNet motion network boasts 225,000 axes shipped.
When engineers assemble a machine, they want a seamless motion network that feels like an Ethernet network with plug-and-play devices and auto-configuration. They don’t want to spend time setting up their network by tweaking network addresses or setting interrupts. SynqNet is the closest solution to a motion-based Ethernet network available on the market today. Connect any SynqNet-compatible drive or I/O device to a SynqNet network and you’re ready to start writing your motion application and spinning motors.
Dean Onishi, Product Marketing Specialist, Danaher Motion
Flavors of Ethernet
In industrial machine control, older and often proprietary networks have the largest selection of compatible devices. If throughput isn’t critical and if higher costs aren’t a concern, then the choice can be to use older networks such as CANopen or DeviceNet for slave devices and Modbus for control-to-control communications.
However, if this is a new machine, your first decision should be to use an Ethernet-based network with its higher transmission rates and lower physical-media costs. Ethernet-based systems are a better way to not only connect to slave devices for control-to-control schemes, but also for connectivity to the IT world.
EtherCat is one of these newer technologies and has the advantage of being truly open. Users of EtherCat enjoy updates to 1,000 distributed I/O as fast as 30 µs, or communication to 100 axes every 100 µs.
In addition to the very-high-performance level, EtherCat allows connection to legacy networks via a low-cost interface, so legacy devices not ready for major updates still can be used and networked.
The EtherCat Technology Group (ETG) is open to any company without fee and gives members extensive inside access to product development with the technology. More than 400 companies have joined the ETG within two years making it the largest Industrial Ethernet organization in the world.
Skip Hansen, I/O Systems Product Manager, Beckhoff Automation
Everyone Needs a Network
The various network organizations compete not as much with one another as with point-to-point wiring. Machine builders and users need to choose a control network over point-to-point wiring. The savings are significant.
Global availability of products and expert support is key for a machine builder. With the largest global installed node base, Profibus is positioned to provide product support, and Profinet adds Industrial Ethernet capabilities. Profibus and Profinet International (PI) has 1,400 members, and there are well over 3,000 different product types available. PI provides 34 competence centers throughout the world to provide local expertise with network questions.
Drives are integrated easily on the same network by using the motion control capabilities of Profibus and Profinet. In additon, safety can be included from the beginning and on the same network using Profisafe, which works seamlessly between Profibus and Profinet.
When very simple devices must be connected, a network such as AS-Interconnect or a system like IO-Link can be integrated into a Profibus/Profinet system, as can networks such as Modbus and DeviceNet. Profinet provides the added benefit of representing the machine as an object or component. This makes it easier to integrate the machine with others to form an integrated production line.
Carl Henning, Deputy Director, Profibus North America
CAN Is Widely Used
CANopen was designed for embedded machine control applications. To simplify system integration, CANopen specifies the application layer and profiles. The communication profile specifies dedicated messages for network management, synchronization, time distribution, and emergency information. The device and application profiles specify generic control devices and dedicated devices for specific machines.
Generic control devices include PLC, input/output module, sensor and closed-loop controller, electrical drive, encoder, and hydraulic vales as well as drives. Under development are profiles for RFID reader, low-voltage gear devices, and pumps.
Application-specific profiles include extruder downstream devices and weaving machine add-on devices. Specific profiles for other machines such as molding, packaging, wood processing, and knitting machines are under development.
The implementation of CANopen is license-free. This also includes the profiles. CANopen source code and CANopen tools are available from different manufacturers. More than 600 companies offer CANopen hardware and software products.
CANopen is standardized in EN 50325-4. The CANopen specifications include protocols for safety-related communication up to SIL 3 compliant to IEC 61508 and network redundancy as well as flying NMT master.
CANopen is suitable for embedded machine control systems as well as open subsystem networks. It’s also used for deeply embedded networking such as a backplane bus in a modular device.
CANopen originally was developed for CAN-based networks. The application layer and profiles have been adopted for other network technologies such as EtherCat, Powerlink, and Varan. This allows easy integration of CANopen networks into these Ethernet-based backbone networks. It’s also possible to integrate high-speed motion control networks into CANopen-based control systems because the profile definitions are the same.
CANopen is a future-proofed network technology not limited to CAN, and CAN is very reasonably priced. In 2006 more than 500 million CAN controller chips were sold worldwide.
The features of the CAN data link layer are unique regarding error detection, robustness, and reliability. The data rate is limited to 1 Mbps at a maximum bus length of 25 m. This maximum length can be increased if the data rate is lowered. In machine control applications, typical data rates are 500 kbps, 250 kbps, or 125 kbps with maximum respective bus lengths of about 100 m, 250 m, and 500 m.
Holger Zeltwanger, Managing Director, CAN in Automation
Combine Two Technologies
There’s no single network that fits all aspects of automation. Profibus and DeviceNet both offer good connections to higher level devices such as complex drives, RFID, and HMI. They’re not good with simple devices like sensors, actuators, or valves. Ethernet-based solutions are growing but still have to catch up.
Customers often tell us that of the 60+ addresses available on DeviceNet, they almost never use more than 20 because performance goes way down. The solution is easy: put all the simple devices on AS-Interface and all the complex devices on DeviceNet. Then get AS-Interface data into DeviceNet using a gateway. This uses up one address, and makes package utilization very good.
Helge Hornis, Intelligent Systems Manager, Pepperl+Fuchs
Follow the Trends
First consider which networks deliver solutions for the specific machine requirements. This is especially true for network cycle time and determinism.
A trend we clearly see is the decentralization of logic and motion control. Centralized racks are replaced by remote I/O very close to the sensors and actuators, thereby simplifying wiring and saving installation cost.
Another trend is the replacement of mechanical line shafts by multiple electronic servo motors, saving cost and increasing machine flexibility.
These changes mean that more nodes need to be supported with faster cycle times and increased timing precision.
When one AC motor drove a mechanical line shaft, cycle times of about 10 ms were sufficient. Now the use of multiple servos on a network requires cycle times in the microsecond range. Typically the position control loop of the servo drive runs at cycle times of 250-400 µsec. Hydraulics and pneumatics are about 10 times slower than servo motion. Logic controllers run update times from 0.5 to 10 msec. HMI update times are typically in the 100 ms range. The timing precision of the network is most stringent for servo motion control, where a jitter larger than 1 µsec can have the network telegram hit or miss the actual position control loop cycle.
Traditional fieldbus networks such as DeviceNet or Profibus don’t offer the network throughput speed to run coordinated motion control on high-speed machiner y. To bridge the technology gap led by the development of Ethernet Powerlink in the late 1990s, modern networks now are based almost exclusively on Ethernet communication.
However, its network latency presents a significant drawback for machine automation. Latency occurs due to collisions that cause a message to be resent after a random time. Latency means that the arrival time of a telegram can’t be guaranteed, but rather is dependent on the network load.
What do the two terms real-time and determinism mean? There are certain analogies between the mail logistics world and the industrial communication world that make it easy to understand the two terms. Real-time means that the recipient knows exactly when a message was sent, which is equivalent to being able to track the delivery of a piece of mail on the Internet. Determinism means that a telegram is guaranteed to arrive at a certain time, which is equivalent to guaranteed next-day delivery. Industrial Ethernet networks use different strategies, based on hardware or software, to ensure deterministic delivery of telegrams.
Software-based solutions such as Ethernet Powerlink offer an advantage compared to hardware-based, ASIC-constrained solutions because any Ethernet hardware can be used to realize a device node.
With a software-based network solution, Gigabit Ethernet can be realized by swapping the Ethernet hardware and keeping the software stack in place.
Another important criteria is the experience a vendor has with a network. Make sure when vendors talk about deployment in the field that the quantities quoted cover deterministic, real-time communication nodes, not the legacy networks or slower networks with the same name.
Among the deterministic, real-time networks, Ethernet Powerlink has deployed close to 200,000 nodes on more than 10,000 machines produced by more than 150 machine builders worldwide.
In the end, the number of devices available with each network technology will determine the success of a specific network. For now, Ethernet Powerlink and EtherCat are the two deterministic, real-time networks with the most devices available.
For the machine builder, selection of one device profile per bus system helps to keep down the number of solutions a device manufacturer needs to develop, and prevents confusion.
For the device manufacturer, adding additional interfaces to a drive, encoder, I/O, sensor means additional cost and time. ProfiNet and EtherNet/IP CIP Motion are late to the market with deterministic, real-time solutions, so only a small number of devices are available.
Other important criteria are:
- Availability of a safety protocol.
- Possibility for deterministic controller-to-controller communication following OMAC PackConnect guidelines.
- Options for infrastructure layout such as star, line and ring.
- Direct, peer-to-peer communication whereby a message is directly broadcast without detouring to a centralized station.
Markus Sandhoefner, Ethernet Powerlink Standardization Group
May's Problem Are Wireless Sensors Ready for Me? We need wireless sensors for vibration monitoring, temperature and presence sensing, and other machine monitoring and control applications. The sensors need to be inexpensive, reliable, and easily connected to our PLC and PC-based control systems. Do wireless sensors that meet our requirements exist, or are we asking too much too soon? Send us your comments, suggestions, or solutions for this problem. We’ll include it in the May 2007 issue and post them on ControlDesign.com. Send visuals, too—a sketch is fine. E-mail us at [email protected]. Please include your company, location and title in the response. Have a problem you’d like to pose to the readers? Send it along, too. |
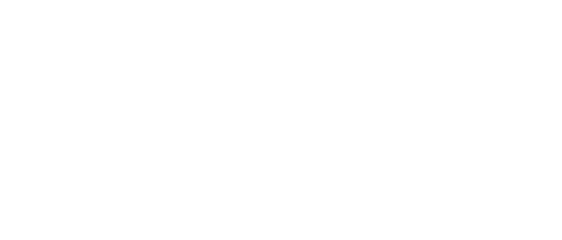
Leaders relevant to this article: