There are machines that make the same parts/assemblies continuously—fixed automation machines—and flexile machines that make multiple parts/assemblies. The former lend themselves more readily to the same type of control system, even as the machine advances through generational changes, as long as the supplier supports it.
One example of that 2005 control strategy was machine builder JVH Engineering, Grandville, Mich. JVH has installed A-B PLC5s on its injection-molding machines for more than 18 years. So, even though its machine design changes could justify more modern controllers at less cost, PL5s still are offered to customers whose maintenance capabilities still are at the PLC5 level.
Using 20-year-old controls would be a novel practice for many machine builders, but if it assists customers on long-term machine upkeep, it clearly is a valid strategy for sustaining fixed automation machines, regardless of design changes over the years. Having the same or similar controls lets factories move more quickly from a reactive to a preventive maintenance mode.
Be Flexible
Moving forward, machine builders must be aware of how users sustain machine operation, regardless of personnel change influences. In many specifications for new, flexible machines, a predictive maintenance program is a requirement.
To meet lean standards, particularly in the installed base, machine builders respond with simpler, more easily maintainable equipment with embedded controllers. This gantry robot for end-of-the-line case packing and palletizing has an integrated control system, power supply, four servo-motors, and control computer in the machine itself.
A primary driver behind the movement to predictive maintenance processes is the growing implementation of lean manufacturing principles to optimize plant asset utilization—a move considered vital to compete globally. Interestingly, a recent study by Aberdeen Group shows more than 80% of those surveyed consider asset maintenance extremely important or very important to their facility’s success.
Are integrated controls and mechatronics a solution to long-term machine sustainability? Mechatronics supplier Precise Automation, Los Altos, Calif., thinks so. “We offer a series of robots that incorporate controls inside the robot,” says Brian Carlisle, Precise’s president. “The only wires coming out of the robot are an Ethernet cable and AC power. These robots feature lifetime lubrication and lifetime servo drives. All harnessing, including air lines, are contained inside the robot and designed for a minimum of 20 million flex cycles. With no external controller, the robots can be uncrated and running in minutes.”
Precise Automation also offers a series of multi-axis motion controllers with integrated drives small enough to be embedded inside a machine, eliminating the separate controller cabinet and associated cables. The reduction in wires greatly reduces the chances of bad connections, noise problems in extended cables, and damage to cables from environmental factors.
Remote diagnostics, support and upgrades through an integrated web server are included in these embedded controllers. Machine performance data can be logged, time-stamped, and uploaded to remote sites via an Ethernet link. Machine programs can be uploaded and downloaded over the web. This gives machine builders access to their equipment anywhere in the world, easing the burden of sustaining machines over an extended time.
An example of this forward-thinking design is found at machine builder CAMotion, Atlanta. CAMotion supplies gantry robots and control systems for high-speed industrial automation applications such as end-of-the-line solutions in case packing and palletizing.
CAMotion incorporated Precise Automation’s integrated controller solution for a custom depalletizing machine (Figure 1). The integrated, four-axis controller package fits nicely into the design, providing a smaller machine with simplified controls. “We selected the integrated controller because of cost, but more importantly, because it’s lightweight, small, and easy to replace,” says Steve Dickerson, CAMotion’s CTO. “For this depalletizing application, we embedded the entire control system, power supply, four servo-motors, and control computer into the machine. The control equipment moves with the gantry, so size and weight are very important. We even used wireless communications to eliminate any tether on the 100-ft-plus long machine.” For gantry maintenance considerations, Dickerson says the integrated controller is relatively easy to replace. “If something should fail, or get damaged, we would merely replace the entire unit, since it’s easily replaced and costs very little.”
Sustaining Machines With Legacy Controls
Mark Lewis, service and support manager, Beckhoff Automation, boasts that, “Beckhoff has an unfair advantage over many other control vendors in the obsolescence game. If you replace a hardware PLC with a newer model, new software often is required for the migration path. This consumes excessive budget and engineering resources, since much of the machine builder’s code will have to be redone. Since we use a PC-based platform with standard IEC 61131-3 software and standard Intel hardware, we’re not required to have such a resolute and inflexible migration path.”
Radiator Specialty achieved up to 20% production increases from its cappers with scalable, open PC controls. The company reduced controls costs on the capper machine by more than $5,000 by controlling an entire line with one PC, rather than multiple PLCs for each machine or line component.
To assure long-term maintenance, Beckhoff provides direct input into new installations to ensure maintainability of the equipment. As long as machine builders stay within the software’s IEC-61131 framework, their machines should upgrade easily, and be more maintainable for their end-users. “After upgrades and maintenance, the software will perform the same way it had in the past with minimal required changes,” adds Lewis. “Users who purchased a license and registration key can quickly download the latest unrestricted version of our TwinCat software from the Beckhoff website at no charge. A 30-day trial of the latest version also is available free of charge.”
To obtain the benefits available in new software versions, Radiator Specialty, Charlotte, N.C., maker of Gunk-brand car-care products, migrated from one version of TwinCat to another in 2006 to upgrade its capper machines. “With our upgrades and line integration, we achieved production increases from our machines ranging from 10-20%,” says Shawn Lahart, Radiator’s electrical technician. “We probably could have increased our production to a meaningful level with traditional PLCs, but equipment and installation cost, as well as extra programming time, would have eaten into the bottom line (Figure 2). Using scalable, open PC controls, we reduced controls costs on our capper machine by more than $5,000. Much of this was enabled by the ability to control an entire line with one PC, rather than controlling each machine or line component with multiple PLCs.”
How Integrators Do It
IBM has used a head bond machine for tape drive production for more than 15 years. It has 10 machines in production facilities in the U.S. and Singapore. The machine design consists of x, y, and theta stages controlled by step-motor drives and a Compumotor PC-based controller board. The cost to develop and build a new machine exceeded $75,000. The best choice was to upgrade the controls.
IBM told Western Technology Marketing (WTM), an automation solution center in Morgan Hill, Calif., that it wanted a solution with some very-rigid design requirements to retain all system functionality, create no changes for the system operator, minimize downtime, and be a cost-effective upgrade.
WTM engineers chose to stay with the unit’s existing Advantech PC. “However, there were extensive software changes needed to upgrade the communication drivers for the new Parker controller,” says Norm Williams, WTM’s president “In addition, a new operating system had to be installed, making the upgrade more complex.” Besides the software changes, WTM had to replace the existing interconnect module, power supply and cabling with a new Ethernet-based, standalone controller, and ancillary components (Figure 3).
To ensure success across all 10 machines, WTM provided step-by-step upgrade training, allowing IBM manufacturing engineers in Singapore to complete the installation in the field.
The cost to develop and build a new bond machine exceeded $75,000, so the engineers stayed with the existing PC, made extensive software changes, upgraded the communication drivers, and replaced the existing interconnect module, power supply and cabling with a new, Ethernet-based standalone controller and ancillary components.
After completing the initial engineering phase, WTM installed the first system in two weeks. The total downtime for follow-on upgrades was two to three days. With very minimal downtime, IBM was back into production at a fraction of the original estimated cost.
The EU’s Approach
Sicme Motori S.p.A., Torino, Italy, builds rotating machines for industries such as power generation and lift systems. In Europe, Sicme maintains installed machines through a network of service centers. “Our network of service centers keeps our machines operating 24/7 for our customers,” states Ugo Bello, Sicme’s sales director. “Such a level of service is essential for mission-critical applications like power stations.”
Andrea Dolfi, Sicme’s service manager, says it analyzes actual application conditions, and does machine simulation to develop specifications that ensure successful installations. Considerations include materials used, ventilation needs, and overall electrical characteristics of each machine. Once installed, says Dolfi, each machine is tested again and registered for a preventive maintenance program.
“The first rule of Sicme Motori’s service program is not to take the place of the customer’s service personnel, but to cooperate with them through training,” continues Dolfi. “This includes operators and maintenance personnel. Preventive and daily maintenance procedures are defined based on the installation environment and machine duty-cycle. Establishing maintenance procedures early will prevent emergency repairs, and will lead to predictive maintenance that not only is non-intrusive in the normal operation, but also enables the user to know motor status and to determine exactly when to stop the machine according to production needs. Precision decision-making depends on available technological tools and on training given to specialists who make the analysis.”
Sicme usually recommends all critical machine parameters be analyzed every 1,000 hours for high-duty-cycle machines, and every 2,000 hours for lower-duty-cycle machines.
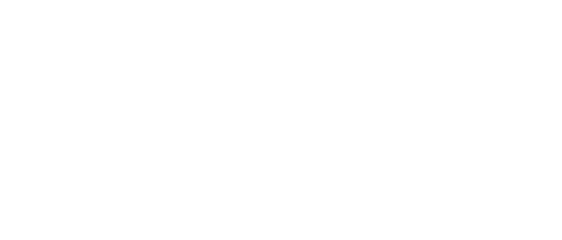
Leaders relevant to this article: