They would select automation components that featured the best performance, that were easy to implement, and that were simple to support.
If left to their own devices, those machine builderās customers would demand each machine builder totally conform to their own regional and corporate standards. They would demand the same price, delivery, performance, and support for their custom regional automation system as promised for the machine builderās standard worldwide automation system.
In the real world, machine builders and their customers must compromise. The result often is a machine automation system that, while not ideal for either, is acceptable to both.
Deciding how much customization is right for each regional market is a balancing act that has to take into account the advantages and disadvantages of standardization versus customization.
One Size Fits All?
There are obvious benefits resulting from standardizing on one global automation platform throughout an entire machine line. āThe advantages of one design are cost savings through efficiency during the manufacturing process and intimate familiarity with the product by all employees within the company,ā says Ron Karpinski, electrical designer with Marchant Schmidt, Fond Du Lac, Wis. Marchant Schmidt provides equipment and services for the food and dairy industries.
Megtec Systems, DePere, Wis., supplies splicers, dryers, and oxidizers for web offset printing, web coating, packaging, paper, tissue, and other industrial markets. āMachine builders face high costs to train staff and provide software for automation systems,ā observes Rick Lehman, electrical engineering leader at Megtec. āThere is a great savings when only one system needs support and management of upgrades and version changes. Volume discounts based on worldwide purchasing agreements also can be negotiated. Spare part stock is reduced greatly, and the staff engineers only have to be trained on a single system.ā
Another machine builder seconds Lehmanās opinions. āStandardization always is more economical,ā claims Rodrigo Sanchez, vice president and director of North and Central America for Masipack (www.masipack.com). Masipak manufactures machines for vertical and horizontal packing in the food and the home, health, and beauty industries. āReduced inventories, standardized methods and documentation, and a more efficient maintenance program can be better achieved with a single automation platform.ā
Volker Klocke, project manager for software and HMI systems at GL&V USA (www.glv.com) in Lenox, Mass., sees another advantage of worldwide standardization. GL&V manufactures paper machine winders. āChoosing a single standard automation system lets a machine builder realize the unique benefits of the chosen hardware,ā relates Klocke. āImprovements are easy to implementāthey can be tested directly on the target.ā
Standard Worldwide
Advantages
|
Disadvantages
|
Using one automation system lets machine builders focus on development and performance, believes Graham Harris, president of Beckhoff Automation. āThe perceived advantages of multiple systems based on regional demands are short-lived,ā he says. āThe customer gets a machine it thinks will be well-supported by the local automation supplier, but the local supplier doesnāt have an in-depth understanding of the machine. Service from the machine builder also is problematic because its service people usually are less familiar with the special regional machine.ā
Consider this, says Harris, āWould Toyota have succeeded in the U.S. if it had put a GM transmission in its U.S. market cars because local dealers, garages, and mechanics were more familiar with GM transmissions?ā
Does One Size Fit None?
All well and good, but from a customerās perspective and often from the machine builderās outlook, standardization can result in a one-size-fits-none outcome.
āSome customers will not accept an automation system they have not used,ā says Pneumatic Scaleās Christman. āSome automation components might not be supported in all geographical regions worldwide, and the standard design might be too costly in some countries.ā
Automation engineers usually are not directly responsible for revenue, but they understand that rigid standards can limit sales. āStandardization can limit your market-share potential to those willing to accept your standard design, and pose possible difficulties in areas where your standard components are difficult to locate, and create resistance from your customers to things very different from what they are used to,ā observes Marchant Schmidtās Karpinski.
Klocke of GL&V also is concerned about customer acceptance and local support. āOther issues to consider are multi-language support, imperial and metric measurement systems, local expertise and support, and certifications such as CE/TUV/ISO,ā he cautions.
Megtecās Lehman also looks at drawbacks from the machine builderās point of view. āStandardizing increases risk if the chosen vendor cannot meet our demands,ā he says. āSuppliers also might be less inclined to provide competitive pricing and additional support if they know we are single sourcing.ā
Customization a Better Fit?
Customization provides a better answer to customer needs, but at what cost?
āBecause no one automation system truly is supported globally, having multiple systems enables a company to have support in each geographical region,ā says Lehman. āBeing able to support multiple automation systems enables machine builders to garner a wider variety of customers.ā
Karpinski adds, āMultiple designs broaden your client base by including regional preferences and standards, expanding the knowledge and experience of your employees, and possibly exploring new components and techniques that could carry over to other designs or products.ā
Customization can be required for compliance with hazardous area regulations. āU.S. standards (ANSI/ISA 60079-X), Canadian standards (CAN/CSA E60079-X), and European standards (EN 60079-X) all are based on IEC 60079-X with national differences,ā says Paris Stavrianidis, general manager of FM Approvals at the FM Global Group. āA common product for all those markets isnāt a reality because of differences in installation practices. Many U.S. and Canadian installations still use the traditional two-division area classification system instead of the IEC-based three zones, making IEC products unacceptable.ā
Donāt Go Custom Crazy
A little customization is good, but too much of a good thing might not be. āGlobal customization requires more time and most likely more employees,ā opines Christman of Pneumatic Scale. āPlus, the cost of development and support increases because systems are non-standard.ā
Custom Regional
Advantages
|
Disadvantages
|
Not only is staffing more expensive, it can be hard to find the right people. āCustomizing for local markets makes it hard to find properly trained staff for the work in the particular locale,ā concludes Lehman. āThere also is a much higher cost to maintain spare parts and keep up on software and hardware upgrades. The cost of training a staff on multiple automation systems is extremely high and outweighs most advantages of using multiple systems.ā
Compromise Required
Machine builders want global standardization and their customers want regional customization, so compromise is necessary. āFeatures required by customers in one region might be insignificant to users in another area, so there is a balance to be struck,ā says Andrew McCauley, vice president of marketing at Danaher Motion. āDrives and controls tend to have more regional differences than motors. Drive and control component size, shape, connector type, connector location, wire terminations, and voltage requirements all can have a significant impact.ā
What works well in the U.S. might be unsuitable for overseas. āSafety requirements will drive different needs for safety functionality and cost in different regions,ā explains McCauley. āLow-labor-cost regions often prefer a machine with less capital content, even if more workers will be needed to operate the machine.ā
If customers want customization, why not let them drive it? āThe ideal automation system would meet all applicable regional standards and permit configuration,ā observes Mark Kenyon, product marketing manager for ABB Low Voltage Drives. āThe OEM would build one global product to 95% completion and then configure the remaining 5% to regional differences and customer preferences.ā
Customizing the network instead of the controller and the I/O is another likely compromise. āElectrical substructure such as the I/O systems can accommodate regional communication networks such as EtherNet/IP, Profibus, or CC-Link just by changing a network interface module without replacing the controller and the I/O hardware. This lets the machine builder provide a regional control system without extensive redesign,ā says Beckhoffās Harris.
Itās difficult to produce an off-the-shelf design that meets all standards and is universally accepted, observes Craig Torrance, services sales manager for Pilz Automation Safety. āBut significant advantages can be gained by thinking about machine automation system design as a modular-platform-based process,ā he says. āA machine builder should have a suite of possibilities to offer the customer. Each platform should be of a proven design and not completely reengineered for each customer. The machine builder can take each module of the automation system such as motion, safety, control, and visualization and have two or three different platforms for each.ā
The ultimate goal, concludes Torrance, should be modular automation components and platforms with a common overall design, flow, and feel.
Machine Builder Sticks to Its Standards
Remmele Engineering designs and builds custom automated manufacturing systems. āOur machines generally are one-of-a-kinds built to meet unique manufacturing requirements for new products with worldwide markets,ā says Tom Olin, control engineering supervisor for the Automation division of Remmele. āOur largest market is life sciences and our customer base includes the top 100 worldwide product manufacturers.ā Olin says the typical price tag of a Remmele-supplied system can run $1-15 million with the automation component of the engineering and purchased hardware totaling about 20% of the value.
Its machines are customized for each application, but Remmele sticks with a standardized approach. āWe find no advantage in multiple automation system designs,ā says Olin. āCustomers pay a hefty premium if they require a different manufacturerās control system. At present, 90-95% of our customers accept our Rockwell Automation solution.ā
Remmeleās reasons for choosing a single automation system:
- The hardware and software offerings can meet the requirements of 99% of our applications.Ā
- The hardware and software offerings are the preference of at least 70% of our customerās worldwide.Ā
- Even though each machine is unique in nature, large portions of the hardware design and numerous standard software modules can be leveraged from project to project.Ā
- The ControlLogix platform with integrated motion control programming integrates well with the complexity of our systems.Ā
- The family of operator interfaces meets a majority of our requirements, including those for 21 CRF Part 11, data collection, and interface to SCADA systems.Ā
- The controller and HMI families of products integrate very efficiently and effectively with machine vision, robotics, various types of lasers, various types of welding equipment, and other special types of automation support equipment.Ā
- Technical support is superior. We tend to be among the first OEMs to try new products or use existing product to the bare limits of their specifications. Between vendor and distributor, we have support from two dozen technical resources available to us 24/7 as needed.
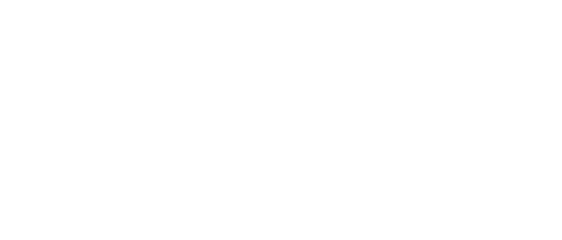
Leaders relevant to this article: