We measure a few process variables on our plastics processing machines including temperature and pressure. We use these variables for both real-time control and for monitoring. What are the challenges and benefits of upgrading these instruments from 4-20 mA to smart instruments with digital communications? Is there a benefit I can promote to customers? Is support another learning curve for us?
—from August ‘07 CONTROL DESIGN
Answers
Weigh the Costs
Smart transmitters will give you transmitter diagnostics, the ability to read additional variables, and the ability to reconfigure the transmitter remotely. Also, smart transmitters usually offer high-end performance.
Additional benefits of Profibus and Foundation fieldbus installations include less wiring, better management of instrument resources, direct digital communication which eliminates digital-to-analog conversion and its error contribution, and reduced maintenance cost. HART also can offer some of these benefits.
The main challenges are the learning curve for installation and configuration of Profibus or Foundation fieldbus networks and higher instrument costs. However, after gaining installation experience, your savings in wiring, installation, and maintenance should outweigh the increased instrument and learning curve cost.
MATT MOREN, director, sales support
Moore Industries, www.miinet.com
The Slope of the Learning Curve
In recent years we’ve seen a huge growth in industrial communications and smart devices. Although many factors influence this growth, two things remain common: Smart devices save time and money. When implemented correctly, smart devices typically will save the user time and money, and increase efficiency because they can remotely diagnose problems in real-time.
The downside to upgrading to smart instruments is bearing the brunt of the initial cost. This upgrade cost is dissolved quickly once the benefits are observed. These benefits include online local/remote diagnostics, online status, and multiple variable readings with one transmitter. In this application, a single multi-variable transmitter could provide both pressure and temperature readings.
As with anything new, there’s going to be a learning curve. The slope of the curve will vary greatly depending on what steps the selected vendor takes to make the product easy to use and depending on the end user’s openness to using something new.
CHRIS HINES, level III support engineer
ProSoft Technology
Put Down the Screwdriver
Upgrading instruments from 4-20 mA to smart instruments with digital communications allows users to track important production variables like temperature and pressure and potentially save the time that is wasted when equipment fails.
Prior to the advent of digital communications and capable smart instruments, transmitter calibration required an operator to manually tweak 0 and span with a screwdriver. When a new transmitter was installed, it had to be calibrated to match the specifications of the transmitter before it. There were no diagnostics available, so failures such as blown transmitters were a surprise.
Today, smart protocols such as the HART protocol facilitate the encryption of a message packet into the 4-20 mA signal wire. These messages include status and control, setting the 0 and span, and digital signals. All of these capabilities can yield substantial time savings.
Status and control messages offer diagnostics from the control room for remote transmitters. These smart diagnostics capabilities allow scaling the 0 and span from the control room, so personnel no longer need to go into the field for instrument calibration. Additionally, with digital and analog signal values, it is possible to directly compare 4-20 mA signals to digital messages, enhancing diagnostics capabilities.
Of course, the main benefit relates to economy of motion because increased productivity and efficiency create the potential for additional profitability.
Currently, the main challenge facing smart instrument implementations is ensuring all instruments have the same communications specs. For example, employing HART means that all instruments would need to be rated at 4-20 mA and include HART communication capability.
Economy of motion is vital to machine builders because this directly impacts the bottom line. Given the advances in automation technology, it’s time to put down the screwdriver and get smart by integrating smart instruments into process control machinery.
MARK DECRAMER, product manager
Wago
Tap the Intelligence
There certainly is value in having smart instruments. The key to success is to include a system that takes advantage of the added intelligence. Over the long term, the advantage will be in asset management. The smart way to connect and access smart instruments is with a fieldbus. This is the summary we use in our one-day training classes on Profibus and ProfiNet on the benefits of a fieldbus.
Engineering and Documentation
-
Easier configuration
-
Easier to use and up-to-date documentation
Hardware
-
Less Hardware: I/O, terminal blocks, enclosures, barriers, wire
Installation
-
Easier, quicker, and less time-consuming
Commissioning
-
Faster
Maintenance/Operations
-
Improved availability and reduced down time
-
Improved asset management
Manufacturing Flexibility
-
Changes are implemented rapidly
There is a learning curve for any new application. The good news is that training is widely available to make the curve shorter. For example, we offer certified network engineer training for both Profibus and ProfiNet.
Carl Henning, deputy director
PTO
Upside, Downside
Changing from an analog to digital sensor can have both advantages and disadvantages.
Advantages include electrical noise immunity. Unlike analog sensors, digital sensors typically do not have problems associated with EMI, which could lead to erratic or false readings.
High resolution is another advantage. We find that digital position sensors from firms such as Balluff and MTS offer excellent performance, increased resolution, and high speed. These sensors are suitable for closed-loop control and real-time data logging.
Disadvantages include communication methods that are somewhat slow as compared to 4-20 mA sensors. Slow sensor response might not be a problem as most digital pressure sensors are used for monitoring and not for real-time control.
Dennis Meckler, marketing manager
Plastics group Bosch Rexroth – Hydraulics
Continuous Diagnostics
Upgrades to digital technology offer operations and maintenance advantages for your customers. Intelligent digital transmitters run continuous diagnostics that provide predictive status information about the health of the plastics processing and the transmitters themselves. This continuous status information enables users to switch from preventative/scheduled to predictive maintenance, avoiding unnecessary costs and interruptions.
Further, the diagnostics provide early warning capability that enables maintenance departments to tend to issues before they become serious, avoiding surprises and resulting in improved process up time.
Wireless digital transmitters offer an excellent choice for reliable and continuous delivery of all digital information from plastics processing machines. Wireless overcomes many of the challenges of existing wired practices. Installation is low-cost, easy, and fast. Installation costs are reduced up to 90% with wireless as compared with wired installation.
Wireless field networks are self-organizing mesh technology, providing message reliability greater than 99% and allowing installation where it’s best for the measurement—not where it’s best for wireless transmission. Site surveys are not needed; the meshes are smart and simply reroute as needed to complete paths for communications to the gateway and human interface devices.
As for support, effective wireless solutions should not present challenges or require more labor for installation or operation than wired installations. Customers should be able to use or improve upon existing business practices. Required operator rounds are eliminated, personnel improve safety by staying out of the field, and time is freed up for more valuable process oversight and action. Wireless technology furthers simplicity because radio and antenna expertise are unnecessary and because units install and start up easily out of the box.
Bob Karschnia, vice president of technology,
Rosemount division of Emerson Process Management
January's Problem
We need to measure motor speen in our dry food packagung machines in order to close the loop for more precise control. We have narrowed our choices to either an encoder or a resolver, but we are having touble deciding which is best. What are the advantages and drawbacks of each technology?
Send us your comments, suggestions, or solutions for this problems. We’ll include it in the Jan. ’08 issue, and post it on ControlDesign.com. Send visuals if you’d like—a sketch is fine. E-mail us at [email protected]. Please include your company, location and title in the response.
HAVE A PROBLEM YOU’D LIKE TO POSE to the readers? Send it along, too.
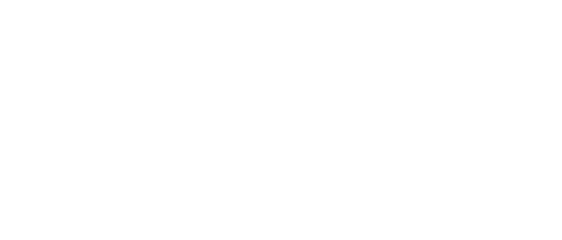
Leaders relevant to this article: