By Mike Bacidore, managing editor
Pneumatic technology has had a successful role in lumber-processing machinery for years. But, just like other motion alternatives, there’s always a need to make pneumatic components perform better.
Manufacturers of equipment used in harsh sawmill environments traditionally used pneumatic cylinders made of steel. Designers considered steel to be the only material capable of tolerating the debris, temperature fluctuations, vibration, and shock generated in tough applications such as trim-saw lines.
Sawmill equipment manufacturer USNR, headquartered in Woodland, Wash., is one machine builder that recently sought improved pneumatic cylinder performance alternatives for its new Accu-Trim trim-saw machine.
Serious Cutting
The Accu-Trim planermill trim saw has 11 14-in.-diameter saws on 1-ft centers, which are used to trim planed boards to length prior to sorting. The machine processes 4-6-in. wide boards that are 2-4 in. thick and 6-10 ft long. Boards are fed into lugs just before the trim saw, and they pass laterally via chain conveyor through the machine. The saws are independently actuated in a quick down-and-up motion to trim the boards to specified lengths as they pass through the trimmer. The extension and retraction of each saw is driven by 80-mm bore pneumatic cylinders (Figure 1). The cylinders are controlled by a master PLC, and require 80 psi air to complete the down-and-up stroke.
Air-Powered Trimming
Figure 1: The infeed side of the open trimmer shows how the extension and retraction of each saw is driven by pneumatic cylinders operating at 80 psi and controlled by a master PLC.
Photograph courtesy of USNR
The PLC also monitors and controls the complete trimmer/sorter system for the planer mill. Rather than use position sensors in this tough environment, the saws are actuated up and down based on timing the system’s encoder counts.
The PLC code is written by USNR PLC programmers, and is customized for each mill application.
Need for Speed
“To meet increasing customer demands for speed, we needed saw-actuation cylinders that could extend 90 mm in 50 msec, and retract in 80 msec,” says Tommy Green, USNR’s chief engineer for lumber handling equipment. “Faster cylinder-actuation speeds mean an increase in the number of boards processed per minute. The trim saw rate had been 140-160 boards per minute, but our goal was 200 boards per minute—a significant production increase.”
Green adds that, in the worst case, the saw has to cycle down, cut the board, then cycle up for the next board. This all has to be done in about 300 msec.
USNR’s engineers researched using aluminum pneumatic cylinders coupled with a concept known as ideal cushioning. They discovered a real potential for cost and performance gains.
“We initially had doubts about the durability and performance of aluminum cylinders in such a harsh, demanding environment,” says Green (Figure 3). “Our concern was how the cylinders would withstand a bad block cut, which can send a chunk of wood spinning out of control, and really batter the trimmer. We also were skeptical whether the aluminum cylinders could perform at the speeds desired without quick deterioration from the impact shock in each cylinder.”
Cutting in Line
Figure 2: The trimmer is about 8 ft wide, 20 ft across, and 8 ft. tall with multiple 14-in. diameter saws.
Photograph courtesy of USNR
Test Results Don’t Lie
USNR tested components from several different suppliers to determine what type of pneumatic cylinder was best suited to meet Accu-Trim’s speed and durability requirements. “We built a test stand in our shop to cycle the saw ladder just as it would happen in the trimmer,” says Green. “We ultimately chose a Bosch Rexroth ISO/VDMA 523 ‘ideally cushioned’ aluminum cylinder because it performed best. The heavy-duty aluminum, wall thickness, and forged housing of the cylinder held up well during testing. The cushioning method successfully dampened the shock, and prevented the rod ends of the cylinders from breaking. All of these benefits, including an overall weight reduction afforded by the aluminum, were remarkable given the unprecedented speed we demanded of the cylinder.” Green adds the superior cushioning in these new aluminum cylinders allows faster motion with less force, as well as faster and more-efficient stroke cycles.
After seeing how 523 dampens shock in an aluminum cylinder, and ultimately enabled Accu-Trim to cut 200 boards/min at 40-60 msec/stroke, USNR specified these components for its Accu-Trim Trimmer high-speed trim saws.
“We saw that aluminum cylinders enable faster cycle rates and greater productivity at a lower overall component cost,” summarizes Green. “The speed and productivity benefits from aluminum’s lighter weight, combined with eliminating end-of-stroke bounce, coupled with the lower cost of aluminum compared to steel, make aluminum cylinders increasingly competitive for us.”
Good for Awhile
As their costs decrease, electronic linear motors can be an alternative for pneumatic cylinders, though Green sees no compelling need to change yet. “I think electric linear motors will have a place in some sawmill applications,” he says. “We’re looking at using them in several places to take the place of hydraulic linear-positioning cylinders, but I don’t think we’ll consider using them for the trimmer saw actuators in the near future.”
Lousy Working Conditions
Figure 3: USNR initially had doubts about the durability and performance of aluminum cylinders within such a harsh, demanding environment.
Photograph courtesy of USNR
Further, says Bosch Rexroth’s Mark Christopher, his company has a newer device for measuring cylinder speed, and controlling its signal valves. “We’ve always been able to measure speed, but controlling the signal valve is relatively new,” he says. “Monitoring both the actuators and the signal valves is important because no two machines are the same. Even machines with multiple ‘identical’ devices have some degree of variance in their operating characteristics. This is caused by different line lengths between the signal valves and the actuators, different friction loads caused by inconsistent assembly methods, different tolerances on mechanical bearings, and so forth.”
An example of this in a sawmill, says Christopher, is on a sorter line. “A sorter can have as many as 70 bins, each holding a particular type and size of dimensioned lumber,” he says. “These bins are fed by overhead chains operated by one or two air valves and cylinders. The inconsistent behavior of these devices required users to program several hundred milliseconds of lag time to ensure that the cylinders could open and close a bin to accept only the appropriate piece of lumber.” This lag time means the delivery chains run slower than the rest of the saw mill, creating a bottleneck in the system.
“Knowing the exact cycle time for each bin, users program the PLCs for each bin’s limitations, eliminate this programming lag, and speed up the chain to keep up with the rest of the mill,” says Christopher.
The Cushioning Concept
The concept of “ideal cushioning” for pneumatic cylinders aimed to reduce cycle time, reduce noise and vibration, and increase cylinder life, says Bosch Rexroth’s Mark Christopher. Cushioning is particularly important for the short process cycles and high kinetic-energy levels that often occur in sawmills. Bounce essentially equates to a system settling time.
Ideal cushioning means there is no end-of-stroke bounce of the piston in the cylinder. The direction of travel of the piston is the same throughout the entire cushioning sequence, and its velocity is exactly zero when it reaches the end of its travel. Some form of cushioning normally is required to reduce the rate of cylinder travel before the piston strikes the end cover. Reducing the piston velocity at the end of its travel lowers the stresses on the cylinder while reducing vibration in the overall structure. In addition, the sound of end cover contact is negligible and the total cycle time is minimized.
“In this application the end point accuracy doesn’t have to be as high as other applications,” says USNR’s Tommy Green. “Taking the shock out of the system makes the components last longer and be capable of higher speeds.”
The cushioning is first adjusted by checking the piston velocity and ensuring that it corresponds to a specified standard depending on the system. Typically, flow control valves located in the connection ports of the cylinder allow for proper adjustment of inlet flow with a screwdriver. The outlet pressure is adjusted by altering the area of the exhaust port with the adjustment screw. The cylinders incorporate a magnetic piston to trigger end of stroke sensors. Used in conjunction with a chronograph, users adjust cylinder speed to any desired setpoint.
“By knowing how to control a high-speed mass moving at a consistent speed and reducing the off-cushion lag and bounce, we could reprogram the machine controls to reduce the usual program lags and there by tighten the entire operation to increase board count,” says Christopher.
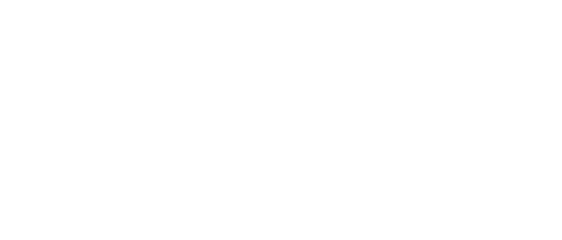
Leaders relevant to this article: