Light pulses travel over glass fibers using a principle known as total internal reflection. Because light travels in a straight line and cabling often is bent, the light bounces or is reflected off the fiber's mirrored walls or cladding. This means the light signal is not absorbed outside the glass fibers and can travel with little degradation.
The signal begins at the network's transmitter, which can accept electronic pulses from copper wire and translate it to equivalently coded light pulses.
Regardless of the transmitter used, a fiberoptic cable is subject to signal losses, primarily through light scattering or dispersion. The faster the light fluctuates and the longer the distance traveled, the greater the risk of dispersion. Light strengtheners, called repeaters or optical regenerators, often are necessary to refresh the signal in certain applications.
Durability Counts
Under harsh conditions, the ruggedness and durability of previous-generation fiberoptic cables had come into question. Typical loose-tube or "indoor" tight-buffered cables work for most straightforward, non-critical applications. However, factories might need the performance advantages of higher-quality, abuse-resistant, tight-buffered, fiberoptic cables. With improved bend, crush, impact and chemical resistance — across a broad thermal operating range — ruggedized, tight-buffered cables can speed installation, reduce attenuation loss, and maximize up-time.
"I was involved in one of the first wastewater treatment plants that ever used fiberoptic cable," recalls Charlie Motz, senior engineer with system integrator Control Instruments (C2i), Smyrna, Ga. "But we don't bother with loose-tube stuff anymore. Now we use ruggedized, tight-buffered cable because it's quicker to install, is more reliable and provides greater value in the long run."
Low Cost, High Risk
Almost as old as glass fiber itself, loose-tube fiberoptic cable still is used in commercial and industrial enterprise applications and for many long-haul backbones — often because of its relatively low cost. "But in a demanding plant environment, the temporary cost differentials vanish in the specter of interrupted output caused by data loss or cable failure," says Bob Booze, vice president of sales operations and marketing at Optical Cable. "The cost of cabling represents a small fraction of a communication system when factoring in network equipment, cable connectivity hardware, and installation and testing. A 10-20% price premium for ruggedized, tight-buffered cable amounts to only a few percentage points increase."
Installation Hazards
Unlike some long haul-applications where the cable basically is dropped into the ground and covered with dirt with minimum connectorization, placement of fiber in a factory requires many bends, pulls and connections. Here, loose-tube designs can fail quickly. For the most part, if major cable stress or damage occurs during the installation process, the contractor presumably knows about it right away, and will quickly fix or replace the damaged link.
More insidious, though, is microbend or residual stress that can occur during or after installation. Often too small to notice initially, the cumulative stresses on cable during rough handling can return to haunt a plant with higher loss transmissions, missing data, and broken fibers. At worst, a complete shutdown in the communications link can occur.
Also, instrumentation and controls engineers increasingly need 10-Gbps transmission for some links in the factory, which can require the latest 50-µm, multi-mode, OM-3 fiber and, in some cases, single-mode fiber. However, these fibers are much more bend-sensitive than previous generation 62.5-µm fibers, requiring cable quality that goes well beyond minimum standards.
In-Service Abuse
"Once installed in a factory, the integrity of cable runs remains anything but static as harsh environments and even gravity can play havoc," says Booze. "If anything, today's 10-Gigabit communication links increasingly spotlight the fragility of all but the most sturdy fiberoptic cables. Even after installation, any kind of stress, whether minor mechanical loads or temperature extremes, can result in microbends or other fiber stress that in turn might lead to increased cable loss and transmission errors, or even eventual fiber failure and breakage."
For instance, explains Booze, heavy cables lying on top of the high-speed link in a cable-tray can cause cumulative trauma to the glass fibers. In addtion, even within vertical runs, cable can be subjected to added stress because gravity causes axial migration that can slowly weakens the fiber. This can go on until a good installation degrades to the point where the link no longer functions properly.
"Consider the fact that 1-Gigabit lengths that are limited to about 300 m, and OM3 10-Gigabit lengths that often are used to extend 1 Gigabit links beyond 1,000 m, have less than 43 dB of total allowable channel insertion loss — per the IEEE 802.3 Ethernet specification — and it becomes obvious that even the slightest increase in attenuation can sabotage the communication link," says Booze.
Motz adds, "I've been using Optical Cable's cable for about 15 years, and we've had zero failures. We had one instance where a guy in a backhoe accidentally dug up some buried cable. He brought it completely out of the ground before he noticed it." Despite his company's concerns, Motz says the cable wasn't broken and continued to work well.
"Keep in mind that our installations are far from ‘primo' because of the nature of the waterworks industry," continues Motz. "There's submergence, abusive chemicals and sewage spills. Yet, after the cable has been installed, we've never had a failure because of degradation or anything like that."
Relative to Copper
When it comes to costs, fiberoptic cable generally is assumed to be much more expensive than copper cabling.
Cable, terminations or networking electronics for a fiberoptic system costs more, although as copper gets faster, it becomes more expensive, almost as much as fiber, says John MacChesney, fellow, Bell Laboratories in Murray Hill, N.J. "While fiberoptic optic cable has become cheaper in recent years, an equivalent length of copper cable costs less per foot but is not equivalent in capacity," he says. "Fiberoptic cable connectors and the equipment needed to install them are still more expensive than copper counterparts."
The reasons for deploying fiberoptic rather than copper are simple: phone companies use fiberoptic networks because it has thousands of times the bandwidth of copper wire, and can carry signals hundreds of times further before needing a repeater. CATV companies use fiberoptic networks because they provide greater reliability and the opportunity to offer new services, like phone service and Internet connections.
Industrial Networks
In an industrial environment, electromagnetic interference (EMI) often is a big problem. Motors, relays, welders and other industrial equipment generate tremendous amounts of EMI that can interfere with signals transmitting along copper cables, especially unshielded cable. In order to run copper cable in an industrial environment, it's often necessary to use conduit to provide adequate shielding. With fiberoptic cable, there's complete immunity to EMI. However, since it's generally strung through the plant relatively unprotected, the cable type must be rugged enough for the installation.
Fiberoptic cable can be installed easily from point to point, passing right next to major sources of EMI with no effect. Conversion from copper networks is easy with the various media converters mentioned earlier. Even with the cost of the media converters, the fiberoptic network will be less than copper run in conduit.
AMR, the parent of American Airlines, has converted its aircraft maintenance facility from a cost center to a profit center by providing maintenance for other commercial and freight airline fleets. The facility had to develop a data system to measure time, track materials, reduce energy consumption, and enable accurate and timely billing.
The facility encompasses 15 buildings spread over hundreds of acres, and includes a hodgepodge of control equipment using various networking schemes including ArcNet, serial, and Ethernet (Figure 1).
This created unique challenges, which included providing connectivity over long distances and at many locations and interfacing with multiple types of controls.
GarrettCom in Fremont, Calif., and system integrator Z Technologies Industrial Automation in Fort Worth, Tex., installed managed switches, which support Ethernet bandwidth from 10 Mbps to 1 Gbps. Ultimately, 100 Mbps was selected as the backbone for the facility. The mix of modular ports in the GarrettCom switches allowed them to connect to the various controls, and transmit via fiberoptic cable to the network server, which made them well-suited for the application.
The layout of the facility's cabling, which originally was a loop, was converted to a fiberoptic ring by Z Technologies. GarrettCom's standards-based, S-Ring technology, a redundant management software package for ring topologies, provides automatic fault recovery, maintaining communications even if a cable is cut or a system component fails.
Don Cryer, Z Technologies' president, says, "We needed robust switches for the job. This deployment required more than two miles of fiber cabling, connecting several sectors of the facility, including the utility plant, fuel farm, and hangar. Unlike a simple deployment between office buildings, AMR's facility required Ethernet switches that could withstand the elements. We'd worked with GarrettCom before, and we knew they could do the job."
The Ethernet, fiber-ring topology used among AMR's multiple buildings saved a huge amount on maintenance, says Frank Madren, GarrettCom's president. "And our switch redundancy capabilities supported the facility's up-time requirements," he adds.
GWS Tube Forming Solutions (GWS) in Bothwell, Ontario, builds PC-based CNC, hydraulic, and servo-controlled tube-forming machines. The PCs that GWS uses are connected via SERCOS and IP Link, using fiberoptic networking from Beckhoff. "Fiberoptic cabling is a great fit for our machines because it's highly immune to electrical noise interference issues that can plague other fieldbus cabling," says Cliff Bailey, electrical engineering manager at GWS.
"One of the major trends in machine automation right now is pushing ever-higher speed in control processing and networking with less hardware," says Graham Harris, Beckhoff's president. "With faster processors and more bandwidth in the I/O network, machine builders will be able to increase throughput, combine multiple functions in one machine, eliminate auxiliary controllers, and use one network for all device connectivity."
Ruggedized, tight-buffered, fiberoptic cable derives much of its reliability and performance advantages from its basic design. As opposed to loose-tube designs, which only have one thin coating surrounding each optical fiber, ruggedized tight-buffered fibers have two. In loose-tube cable designs, the fiber coating is 62-µm thick. In addition to a primary fiber coating, each tight-buffered fiber has a secondary buffer that can bring the total thickness to 387 µm, which is more than six times the primary coating alone.
For exceptionally demanding applications, some cable manufacturers customize the cable with additional jacketing and strengthening of each fiber subunit prior to final cable jacketing (i.e., breakout cables), further enhancing the design's ability to exhibit low loss in the face of extreme operating temperature ranges and extraordinary mechanical stress.
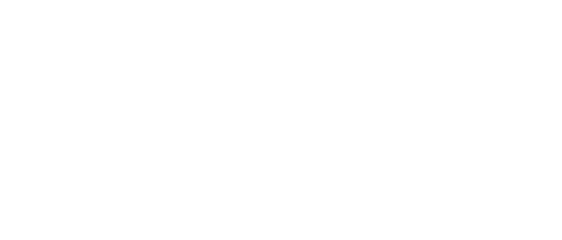
Leaders relevant to this article: