There’s an insistent drumbeat in Motion Control Nation that says the demise of electromechanical components, including the family of ball screws and lead screws is on a fast track. The well-touted advantages of direct drive motors for all but a few high-torque applications seem compelling.
As with many technology predictions, the talk of the demise of ball screws and lead screws for linear motion translation often neglects to factor in applications for which the approach is highly beneficial.
For example, ball screws continue to find favor with Westweigh Systems in Johannesburg, South Africa. The company worked with Tectra Automation to develop a fully automatic weighing and packaging machine for powder mills. It can fill and package up to 12 bags/minute, weighing 10–12.5 kg.
The solution rests on a highly automated system in conjunction with reliable performance from mechanical components. Linear guides and ball screw drives are directly attached to the servo motors and provide a sealed unit that minimizes the ingress of dirt. “Despite it being fully automated, we can offer it at a third of the cost of an imported unit,” says Bill Binckes, Westweigh sales engineer.
Noise Abatement
Meeting performance expectations isn’t always just about speed and accuracy. The designers of drug sample analysis machines at PerkinElmer Life Sciences, Waltham, Mass., will tell you that noise is a serious consideration in component selection. The company offers a broad range of automated systems for liquid handling and sample preparation for small academic laboratories and large labs engaged in clinical, biotech and drug discovery research.
Their noise problems came from the ball screws that play an integral part in the motion schemes of various machines that analyze customer drug samples. The ball screw was a 5/8-in.-diameter screw, a popular item produced in very high volumes. This is the same type of screw used in many automobile steering wheel systems. While the performance of the ball screw was fine, the noise it created was a nuisance.
Ball of Noise
Figure 1: The noise problems in PerkinElmer’s robotic liquid handling system, which came from ball screws that were an integral part in the motion, were eliminated by a switch to lead screws.
Photo by PerkinElmer Life Sciences
Fed up with the noise, as well as some of the maintenance and service issues necessitated by the ball screws—they constantly needed lubrication—PerkinElmer replaced the ball screws in several machines, specifically MiniTrak (Figure 1), a compact liquid handling model, and PlateTrak, a robotic liquid handling system designed for high-throughput screening and other drug discovery and biomolecular protocols.
Steve Schaefers, one of the manufacturing/production engineers involved with the machine designs, says his company did a thorough search for vendors to solve its noise problems. Investigating myriad competitive alternatives, they discovered that Kerk Motion Products was best-suited to their needs.
“We evaluated numerous prototypes and based our decision on results,” says Schaefers. PerkinElmer used Kerk’s B-series, non-ball lead screws with modified nuts constructed of acetal material with stainless steel screws coated with a proprietary TFE that Kerk claims increases lubricity and extends normal nut life by more than 300%.
“In a ball screw, noise emanates from the ball return tube,” says Andy Boyer, Kerk sales engineer. “The balls come out of the nut and go into the return tube. Basically, the balls move to the start of the circuit and then go back into the nut, and that process actually is very noisy.”
Boyer says it surprises a lot of people that a non-ball lead screw, which is a friction system, is quieter than a ball screw. “Most people think a ball screw is going to be really quiet and last forever,” he says. “While ball screws can be efficient in performance, they are markedly noisier than non-ball lead screws and require far more maintenance.”
Technical issues also arose because the Kerk nut design was a bit different, reports Boyer. “Our screws are constructed from a high-quality stainless steel, which is different than the ball screws previously used. Plus, for them to be properly mounted on their equipment, we had to modify the nut design.”
The B-series general-purpose assembly is designed for applications not requiring anti-backlash and wear compensation. “It provides effective power transmission at minimum cost,and features extended life,” says Boyer.
PerkinElmer machines have several different assembly sizes. Some machines, expandable with additional modules depending on customer requirements, might have as many as 28 lead screws.
“The machines run noticeably quieter than our old configuration,” says Schaefers. “Plus, the self-lubricating lead screws greatly improved our old lubrication issues. Lubrication and routine service maintenance problems have been reduced or eliminated.”
The machine assembly also was simplified, as were installation and adjustment procedures. “The changes have been a major contributor in reducing time and labor required during assembly, reducing inventory, increasing throughput, and most importantly, achieving our goal of satisfying the needs of our customers,” he adds.
Selection Decisions
Then, there’s the question of whether to buy a linear motion subsystem or do it yourself. “Machine builders who build their own linear stages frequently spend a great deal of time and money purchasing, assembling, programming and troubleshooting multiple components from different suppliers,” says Mike Woelfel, linear motion product marketing manager at Rockwell Automation. “The situation becomes more complicated when direct-drive, linear-motor technology is applied since mechanical and electrical integration require additional considerations for linear feedback devices and forces due to magnetic attraction.”
Rockwell has a new line of linear stages available in both ball screw and direct drive motor versions, so machine designers can choose a linear stage design based entirely on desired performance and not worry about internal technology. Using Rockwell Software’s RSLogix programming software and A-B Motion Analyzer servo system selection and optimization software, Woelfel says OEMs can specify load and motion profile parameters to select the appropriate linear stage.
Dazzling Performance
Clarity, carat, color and cut (4C) are commonly accepted as the determining factors for identifying a superior diamond. The 4C information, however, doesn’t separate a superior diamond from a diamond of inferior appearance. What makes a diamond eye-catching is the way it plays with light.
GemEx Systems, Mequon, Wis., applies digital optics technology to the worldwide diamond industry with its diamond analyzing equipment. “Even so-called ‘ideal-cut’ diamonds don’t guarantee great light performance,” explains Kurt Schoeckert, GemEx co-founder.
See the Light
Figure 2: The accuracy of measurements in the BrillianceScope relies heavily on the precise movement of the lead screw-driven rail to execute a repeatability of ± 5%.
Photo by Gemex
Schoeckert, a mechanical engineer, along with other GemEx engineers, created the BrillianceScope Analyzer, an imaging spectrophotometer that measures the ability of a diamond to refract and focus light (Figure 2).
Using complex optic technology, the device measures three types of light returned through its crown: white light, colored light and scintillation. Superior performance in any of these light categories yields a beautiful diamond.
The scope measures the diamond in a controlled environment consisting of multiple lighting angles. The gem is placed within a 3-in. integrated sphere with a 1-in. hole in which the diamond is firmly positioned. After measurements are made at an initial light angle, the ring light is repositioned at five different pre-set areas, each one a fixed amount closer to the diamond to create a slightly different angle of light. This movement is achieved via a motion system consisting of a stepper motor attached to a rail on which the ring light is situated.
Measurement accuracy relies heavily on precise rail movement. The smallest inaccuracy in the motion of the arm affects the angle of the light and, as a result, the analysis of the diamond. Repeatability is essential. “We have to be very accurate about where the rail stops,” explains Schoeckert. “Because of its comparative scale, the diamond has to reside in exactly the same five spots every single time we run an analysis. Without this precision, the device’s accuracy would be called into question.”
A lead screw is integral in each of the five movements the ring light executes to a repeatability of ± 5% to ensure the validity of the test results.
If at First …
In order to create the necessary movement, Schoeckert designed his own linear system—an assembly constructed from a U-shaped piece of sheet metal, a 3/16-in.-diameter drive screw and a power nut with two bearings on the end. Unfortunately, this first iteration did not perform up to GemEx standards.
“It wasn’t very robust, and we also had other problems such as backlash,” recalls Schoeckert. While researching suppliers, Schoeckert noticed that Kerk specialized in small drive systems. “Short of completely redesigning a custom drive, we found nothing else that looked like it would work in our application,” he says.
Table
After the table loads on new window click on image once to maximize its size
GemEx eventually used a Kerk ScrewRail assembly consisting of a drive screw with a concentric rail, a combination nut and bushing, and a support positioned on the end. On the ScrewRail end support, threaded mounting holes were provided, after which GemEx simply ran the ScrewRail through a base.
GemEx says the ScrewRail saved space, eliminated the device’s existing offset rail, and provided smoother, repeatable motion.
GemEx used that assembly for a few years before working with Kerk on a redesign. It experienced some issues where the ring light cantilevered off of the ScrewRail. The drive nut/bushing would rock on the screw as a result of some extra clearance in the system. A new RGS slide—with an extrusion that prevented rocking—enhanced the stability and accuracy.
“The redesign did a better job of resisting the rocking motion,” says Jim Bostwick, Kerk application sales engineer. “It created the increased rigidity and reduction in torsional play that GemEx needed to ensure that the light that shines through the stone stays absolutely still.”
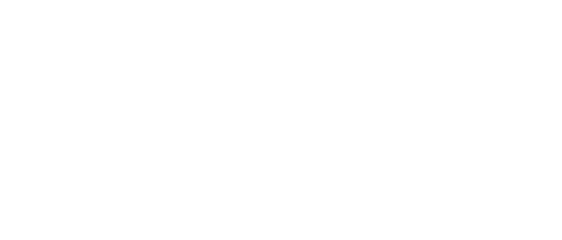
Leaders relevant to this article: