Automation is but a narrow niche in the wide world of commerce, so there always will be a shortage of young job candidates with formal automation training. The best our industry can hope for is a sufficient number of two-year technical and four-year engineering graduates. Machine builders, system integrators and vendors have to take it from there.
To increase the supply of technical graduates, some machine builders start young and help introduce kids to math and science at the elementary school level. “We sponsor three elementary-school-level robotics teams as part of the nationally recognized FIRST Lego League robotics program,” says Ed Diehl, principal at system integrator Concept Systems in Albany, Ore.
Many elementary schools have Lego clubs and classes that help introduce students to basic engineering concepts in a fun environment.
The next steps are high school and then a two-year technical degree or a four-year engineering degree. This is where co-op programs come in, and it’s also where companies can provide material assistance in the form of hardware, software and direct funding.
Big Men and Women on Campus
Machine builders find co-op programs valuable if used correctly. “It’s difficult for us to find automation engineers with experience, so we use co-op and intern programs,” relates Chris Cote, manager of R&D electrical engineering at Goss International Americas in Durham/Dover, N.H. Goss is a global business that manufactures commercial and newspaper printing presses, as well as post-press finishing equipment. “Co-op programs are good, but only if the company is committed to making employment offers to these individuals when they graduate,” cautions Cote. “Otherwise, you’re spending time and engineering hours to train someone to be productive in another company.”
Remmele Engineering in St. Paul, Minn., designs and builds custom automated manufacturing systems for a diversified group of industries and has a well-developed co-op program. “Sophomore or junior-level EE candidates join one of our engineering teams full-time for eight months and receive hands-on control engineering training,” explains Tom Olin, control engineering supervisor of the automation division at Remmele. “Most students return for an additional three-month term between their junior and senior years. By completing the program, these students gain a full year of practical experience over and above what their peers possess.”
Remmele gets three bonuses from the program. “First, by the end of the third or fourth month, most co-op students have enough proficiency that a portion of their time can be charged to projects,” states Olin. “Second, most co-op candidates are self-starters by nature, and these types of individuals fare best in our engineering environment. Finally, we’re a small company by corporate standards, and recruiting for candidates against big companies at major engineering universities across the Midwest can be an onerous task. Our co-op-recruiting network in many cases introduces us to the best candidates before the big companies know they exist.”
Good Tools, good training
Figure 1: This hydraulics laboratory at Spokane Community College incorporates a Delta Computer Systems motion controller and related programming software.
Photo by Delta Computer Systems
Besides employment opportunities, suppliers also work with schools by donating money and equipment. “We encourage the development of relevant professional training in the industry by providing motion control hardware to the labs at Spokane Community College in Washington (Figure 1), Purdue University and the Milwaukee School of Engineering,” says Steve Nylund, CEO of Delta Computer Systems.
Delta, as part of a National Fluid Power Association initiative, is a founding sponsor of an Engineering Research Center grant for fluid power innovation provided by the National Science Foundation. “These organizations promise to champion better fluid power education, which will ultimately provide the industry with more skilled automation professionals,” says Nylund.
OEMs and SIs Like OJT
The next step is to transform students into productive employees. “We pair new hires with experienced engineers, so they can learn our company processes, get up to speed on our design standards and pick up good work habits,” explains Cote of Goss. “We try to get new employees involved in a project quickly to determine their capabilities. We like to get them into the field to get a feel for the scale of our equipment and to understand the operating environment.” Goss has its own in-house training center and sends employees to vendors’ training courses as needed.
Concept Systems also finds on-the-job training to be effective. “On-the-job training has proven to be most effective in teaching technical skills,” says Diehl. “To jumpstart this learning process, we’re updating our in-house training program to include a mock project that new engineering hires will go through to get a feel for all aspects of a real project.”
It seems many machine builders and system integrators use OJT extensively. “Experienced peers lead teams that include younger engineers, who learn to follow project methodologies to design and test systems in ways that have been proven to result in success,” relates Dick Ciammaichella, director of control systems integration at RoviSys. Another system integrator uses OJT as its primary teaching tool. “Our main training method for young engineers is to have them work with experienced staff both in the office and in the field,” says Doug Rhodes, manager of the electrical power and automation group at Dayton & Knight in North Vancouver, B.C., Canada.
Suppliers’ Structured Training
While smaller firms like machine builders and system integrators use some standardized training, they mostly rely on OJT. Their relatively small size lets them personalize training via OJT, and they find this highly effective.
Bigger firms such as industry suppliers also use OJT, but they rely more on formalized and structured training programs to standardize training for relatively large numbers of new hires. This often includes a formal mentoring program.
Stick with me, KID
Figure 2: Motion control supplier Galil’s mentoring program pairs senior application engineers with new hires. After two weeks of basic training, a new application engineer listens in on technical calls with his mentor.
Photo by Galil
Safety supplier Pilz Automation Safety has a training program that addresses both new and existing employees. “We use a managed program to identify automation and safety competencies required to perform the job,” says Craig Torrance, U.S and Canada national sales manager for Pilz. “All engineers and consultants are assessed yearly and benchmarked against the competence profile for their job. Gaps in competence are considered development opportunities, and this is where training fits in. Our professionals get an individual training program based on their gaps.” Torrance says Pilz uses a combination of internal training modules delivered by its own people and external courses.
Another supplier invests 12 months in training its new hires. “Before sending new engineers into the field, they complete a year-long program that gives them the tools and experience necessary to properly size and specify products,” says Dean Moody, division training manager for Parker Hannifin.
One of the most structured and formalized of the supplier training programs is conducted by Rockwell Automation. College graduates attend Rockwell’s six-month Engineer in Transition program. “Following the first 15 weeks of classroom training, the students deploy to their eventual field assignment location for one week to familiarize themselves with the location, housing situation and co-workers,” explains Joe Allie, business manager of field support for Rockwell. “After the field assignment, the engineers return to Rockwell’s competency center in Mayfield Heights, Ohio, for nine to 11 weeks of advanced training in one of several critical technological areas such as motion, drives, process, software and safety.” Upon completion of the advanced training, they’re deployed full-time to the field.
The other focused new hire class is for technician resources with two-year degrees, explains Allie. “Their curriculum is similar to the engineers, but with condensed scope and time frame,” he says. “The core element of the class is eight weeks with the advanced curriculum dependent on the local requirements of the technician’s eventual field assignment.”
How Industry Trains New Hire Automation Professionals |
|
Key to Success |
|
While experienced engineers stress the value of real-world immersion, they don’t forget the technology theory that has to be in place for success. “It’s very necessary to combine hands-on training with theory,” says Tom Cappel, SEW Eurodrive’s corporate training manager. “It’s also important to explain how and why the automation processes have changed with the advance of technology. Discussing the advantages and disadvantages of various design parameters is vital for a well-rounded understanding of the automation industry.”
That’s seconded by John Klauser, principal electrical engineer at Speedline Technologies in Franklin, Mass. Speedline makes automation machines for the PCB assembly industry including stencil printers, dispensers and ovens. “We primarily train our automation professionals on-the-job, although seminars and trade shows are encouraged,” observes Klauser. “Prior to hiring, I would prefer new employees be well-grounded in the basics of science and engineering. We can add automation skills such as control techniques and code compliance.”
Keys to Success
The key success factors are common to machine builders, system integrators and suppliers alike. “Young engineers need to work on a variety of platforms and not get stuck working on the same systems on 90% of projects,” observes Ciammaichella of RoviSys. “We find that well-rounded engineers pick up new systems quickly.”
Goss also has its keys to success. “It’s critical to recruit people with the right skill sets and a personality fit,” says Cote. “These people must be assigned to the right projects initially, so they can begin to use our internal business processes and design standards immediately.”
Motion control supplier Galil works hard to hire people with a good level of intelligence and basic engineering knowledge combined with a curiosity and interest in solving problems. “As I mentioned, assigning a mentor and having a step-by-step training program is crucial for the basics, but the real key is to put them right in the thick of things, and have new hires exposed to customer problems right away,” explains Wade. “The new hire gains more experience and confidence with each problem he or she solves.”
Delta’s Nylund argues that his company culture promotes new learning. “Employees are encouraged to try or risk new things,” he says. “When we look to hire new people, we search for prospective employees who enjoy learning and like to share ideas.”
An apprentice program and mentoring are used to bring new employees into the fold at Phoenix Contact. “Our apprentice program brings newly graduated students into our work force as full-time employees,” says Marrero. “During the first year they work in every department from the manufacturing plant to field sales. Once they complete the training portion of the program, they obtain a position within the company based on company need and employee preference.”
Because automation is a narrow niche in the wide world of commerce, will there always be a shortage of young job candidates with formal automation training? Is the best the industry can hope for a sufficient number of two-year technical and four-year engineering graduates? What must machine builders, system integrators and vendors do to turn these graduates into productive employees? Join the discussion at ControlDesign.com/autopro
Machine builders and system integrators train their people at their own expenses for their own benefit. Suppliers do the same, and they also train existing and prospective customers for a fee.
Non-profit industry organizations incorporate training of automation industry professionals as part of their missions. For PTO, the North American arm of Profibus and ProfiNet, this mission includes promotion of Profibus standards and professional certification.
“We offer learning opportunities for automation professionals that range from one-hour webinars to one-day overview classes to full-week training sessions,” reports Carl Henning, deputy director of PTO.
The webinars and one-day classes are free. The one-week classes cost, but they lead to certification as either Profibus- or ProfiNet-certified network engineers for those who pass the theoretical and practical exams. “The exams are standardized worldwide by Profibus and ProfiNet International, so certified engineers are prepared uniformly worldwide,” explains Henning.
In addition to webinars, the web provides a convenient way for PTO to make white papers and application stories available to controls engineers.
“Our biggest challenge is letting potential trainees know about the classes and webinars,” points out Henning.
“Our second big challenge is convincing potential attendees that the free one-day training events really are training and not self-promotion.”
Online Learning Has Its Limits
The Internet was supposed to take education and indeed the entire field of training by storm. Many thought that the only factors holding online learning back were high-speed Internet connections, the right training materials and inertia.
But now that online learning is being used extensively in our industry, limitations are becoming apparent. “The element required to make a change is practice of the desired behavior,” observes Gordon Kilgore, president of system integrator CQS Innovation.
“Computer-based training programs are good for new technologies if they provide exercises to demonstrate how things work, but we find that coaching students through real-life examples of the task helps to reinforce information presented online,” adds Kilgore.
Phoenix Contact uses online modules, but they find that traditional classroom instruction and outside services are also needed to properly train their automation professionals. “Our online modules cover basic content and prepare employees for more in-depth instruction,” explains Jeff Frekot, strategic initiatives manager at Phoenix Contact. “Traditional classroom instruction includes lecture and hands-on lab exercises that provide a deeper level of understanding of products and applications. We also use outside services when more detailed or application-specific training is required.”
The Web does have its purposes, particularly for frequent updates to areas already covered via other training methods. “We make virtual updates available to employees via the Web,” says Joe Allie, business manager, field support, Rockwell Automation. “We find that virtual learning is difficult for in-depth product knowledge, but updates lend themselves nicely to this media.”
Industry practitioners who use the Web for training daily find that online is great for introductory training and for updates, but not so good for in-depth instruction.
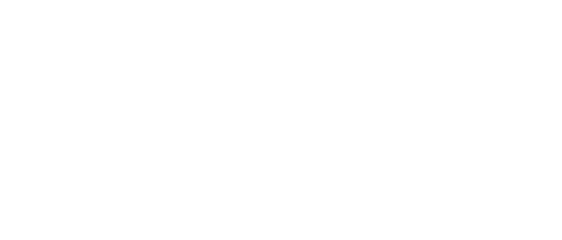
Leaders relevant to this article: