By Chuck Reed, Weiler Engineering
For machine builders, a decision to make control and automation component changes to their production machines has great significance. These OEMs have to consider the machine’s operating parameters for a wide spectrum of customer performance requirements, as well as the machine’s integration with many equipment options.
Weiler Engineering, an Elgin, Ill.-based global provider of aseptic, blow/fill/seal machines for pharmaceutical and healthcare applications, confronted serious PLC compatibility issues when its original controls supplier changed its product line.
One for All
Figure 1: Weiler’s blow/fill/seal technology integrates blow molding, sterile filling and hermetic sealing in one continuous operation to produce aseptically manufactured products.
Photo by Weiler Engineering
Demanding Customers
“The ability of our customers to provide these sterile liquid products, which must meet corporate, scientific, regulatory and end-user requirements, can be quite demanding,” explains Bob Mazur, manager of electrical engineering for Weiler. “These challenges are met by specific container and closure designs available with Weiler’s systems, which are designed to manufacture containers ranging 0.2–1,000 ml at rates up to 15,000 units per hour, depending on container configuration.”
Weiler’s Asep-Tech equipment extrudes a tubular, plastic shape called a parison into a mold containing from five to 60 chambers. When the parison reaches the proper length, the mold closes and the parison is cut. The bottom of the parison is pinched closed, and the top is held in place. The mold then is conveyed to a position under the blowing and filling nozzle.
The blow/fill nozzle is lowered into the parison to form a seal with the neck of the mold. The container then is formed by blowing sterile, filtered, compressed air into the parison, expanding it against the walls of the integrally cooled mold cavity. Next, the sterile air is vented from the container, and the sterile product is metered into the container through the fill nozzle, which then retracts. Separate sealing molds then close to form the top and hermetically seal the container.
Step Changes
Figure 2: The series of steps involved to form, fill and seal the container is completed in successive steps in and at the mold.
Photo by Weiler Engineering
Customer Concerns
Upgrading components in manufacturing process equipment is something plant engineers take seriously, too. The newly modified machine must operate flawlessly to fulfill the requirements of the facility and must integrate smoothly with other equipment in the plant. However, too often engineers end up finding less actual capability from the new components because of compatibility issues with their control systems.
One example of this happened to us a few years ago when Barber-Coleman’s Maco 8000 controller, which we used for a long time on our machines, became obsolete, says Mazur. The company’s new, second-generation PLC was installed, but we had issues with it. The problems mostly involved internal communications in its own two-CPU setup and the touchscreen they supplied.
We eventually chose the Siemens 300 series CPU family. “The Simatic S7-300 is a modular PLC platform with integral I/O, integrated technological functions, and integrated communications interfaces for efficient processing speeds for short machine cycle times,” says Michael Cizmar, account manager, Siemens. “The modules are DIN-rail mountable, and the backplane bus is integrated into the modules, so the bus connectors simply can be plugged in. With the varied range of modules for the PLC, centralized expansions and simple distributed structures can be configured.”
Along with a Siemens engineer, we developed a well-documented and well-structured software program.
The reaction among Weiler’s customers was very positive. Training and orientation for the new software was no problem either. Mazur points out that the machines run about 50 hrs/week for eight to 10 weeks before we ship them to our customers’ plants. “Ninety-nine percent of the time, the customer never needs to get into the program,” says Mazur. “Our machines have to run 24 hours a day until a batch of product is gone, and that could be four days altogether.” He adds that users typically do a three-hour steam cleaning, connect a new tank of raw material, and again run it for four days. For added support, Weiler installs a modem and Siemens TS adapter for a phone connection.
The Next Iteration
Now, several years later, we decided to build an all-electric machine, but this time use a different manufacturer’s drives and motors. The machine involved an 11 servo-axis design, and we wound up with a communications and information nightmare. “This time Siemens backed us up with an engineer who worked in plastics applications, knew drives and communications with third-party controllers, and stayed with us during the debug time we needed. He also helped us develop a well-documented and well-structured software program that did the communications necessary to run our machine. He understood what needed to be done to eliminate third-party device issues when the drive controllers where not 100% Profibus-certified. The system also has the interface flexibility to work with Siemens products or third-party products that are Profibus-registered. We just connect the wires and control them.
“It took us about nine weeks from the start of drive communication programming to a finished working program,” recalls Mazur. “We had to keep going back to the drives supplier to make changes in their firmware in order to handle the commands and communications acknowledgements.”
Here again, customer reaction was positive. “The field support was quite easy because most of our customers are outside of the U.S.,” recalls Mazur. “They wanted a change, and when we chose Siemens, they actually were pleased. We put enough diagnostics into the program and kept a very similar-looking appearance to the screens, so our techs and the customer have had little trouble running the machines.”
Diagnostics
The new PLC functionality lets us make changes online from Chicago on a machine in India. The system also provides a flexibility that allows our customers to see what’s happening in the machine. “From a programming code method standpoint, for which we use ladder and structured text, there are advantages gained because our customers can see the code and they can troubleshoot it, but we can lock up function calls such as any code calculations that we don’t want them to change,” adds Mazur. “We also use Siemens-written subroutines built in Structural Constraint Language (SCL).” SCL lets designers formalize and confirm the program’s alignment with the intended design.
The new system is more advanced when it comes to using Ethernet or Profibus to alert our client’s plant maintenance that there’s a problem with the machine. “All the I/O cards and the drops are capable of self-diagnostics,” explains Mazur. “If anything should go wrong—shorts or a bad connection on a card—it will indicate on the card that it has a problem, and internally set alarm bits that are trapped to a diagnostic screen on the machine. It immediately gives the maintenance people at our customer’s site a very fast way of finding the problem prox or card.”
Our machines went from about 15 touchscreens that were used for basic operations to 75-80 screens now. We still have the 15 or so screens that most of our customers are familiar with. But now it has much more behind that, including all the screens used for troubleshooting and diagnostics, such as seeing every input and output turning on or off, and getting more than 200 alarm messages that pop up when they happen and are stored on the alarm log screen.
Click here to read Automation Means Cleaner Manufacturing. This article is an OEM Spotlight on Weiler Engineering and talks about how the machines it builds for the pharmaceutical industry are affected by regulations.
Also, read Do You Pay Too Much for Components. This article addresses how to choose between industrial and commercial components and suggests what to do when you need to replace components that are obsolete.
Is the risk of component compatibility a big issue for you when you consider changing suppliers or are faced with replacing an obsolete product in your system? You’ll find folks who share your position on this issue and maybe some who disagree at ControlDesign.com/obsolescence.
Chuck Reed is director of sales for Weiler Engineering, based in Elgin, Ill. Learn more about the company at weilerengineering.com.
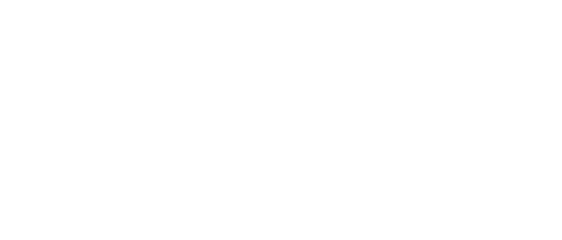
Leaders relevant to this article: