By Joe Morrissey, Conflex
The Renaissance period spanning from the 14th to 17th centuries was a period of rebirth—cultural enlightenment and learning—in western Europe. These days, the term is applied to everything from government to education, and most certainly to technology.
Our company, Conflex, a builder of shrink-wrapping machines, has undergone what many of us refer to as a renaissance. In 2005, Conflex began its own rebirth by substantially redesigning each machine in the product line and continued redesigning machines through the end of 2007. The company’s Modular CW and ServoFlex lines have undergone a complete mechanical and electrical redesign (Figure 1).
Conflex wrapping machines are tailored to the food, consumer goods, electronic media and printing industries, among others. Typical applications for our machines include wrapping for frozen foods, bulk packaging for club stores, CD and DVD packaging and the packaging of household products and toys.
Extreme Makeover
Figure 1: The ServoFlex line had a complete mechanical and electrical redesign and now performs better, is more flexible to program and can teach operators how to use the machine with automated instruction.
Photo by Conflex
Most of our builds are standard machines for the particular industry, but we also develop custom infeeds that connect to our machines to offer customers different ways to feed their product into our machines.
Coordinated Motion
The ServoFlex wrappers use a DC motor to drive the infeed portion of the machine and all three servo motors follow the speed of this motor. The film feed and vacuum belt are run off a servo. Servo motion is well-suited for exact bag sizing—particularly for print registered applications. The discharge belt is driven by a servo that runs either faster, slower or the same speed as this vacuum belt so the individual packages can either bunch or pull away from each other. The last servo moves the seal head back and forth in a flying saw fashion. The seal head matches the speed of the discharge belt and then places the seal in an exact location by sensing the gaps between packages.
With our company motto—“Flexible people make flexible systems” —in mind, we sought a controls system that could deliver true application flexibility to customers in these diverse industries. Over the past five or so years, our customers had been asking our industry’s machine builders for increased flexibility, faster changeovers and easier operation, troubleshooting and remote connectivity capability.
“All of Conflex’s customers demand user-friendly machines with intuitive interfaces,” adds Mark Lorenz, Conflex electrical applications engineer. “New technology is a critical factor for us. Tough competitors in our field also are promoting the latest and greatest technologies, but ease-of-use also is a must-have.”
Choose Action, Not Buzz
When servo technology started generating a high level of industry buzz in the early 2000s, Conflex was one of the first companies to successfully incorporate it in shrink-wrapping machines. Today, as open, PC-based control and industrial Ethernet technologies make a similar commotion in our industry, Conflex is at the forefront to actually do something with it.
In particular, the ServoFlex film seal wrapper has been through dramatic changes since its previous incarnation. “The old ServoFlex design used numerous intelligent drives that handled the automation and motion control aspects of the machine,” says Lorenz. “The required programming time for multiple drive controllers really irritated us. This was a three-servo system, and each axis had a controller that had to be individually programmed.” The drives weren’t equipped for Ethernet connectivity either, which hampered needed networking requirements.
Adding or removing I/O further complicated the problem. “If even a single I/O point failed in the intelligent drive system, we’d have to replace entire boards,” adds Lorenz. “It also was very expensive to replace the drives themselves whenever we had a failure. It became apparent that to be flexible and better manage our controls, we needed a new solution.”
Eleventh-Hour Transformation
In late 2005, we had made what we thought was our final decision on a new platform from a major automation and controls vendor. “It was an acceptable motion controller with PLC functionality but didn’t have all the programming and design flexibility we hoped for,” recalls Lorenz. “We just accepted that we had to put more time and effort into the design than was ideal.”
We planned to order our controllers the following Monday. Don Seicther, Beckhoff Automation’s Wisconsin regional sales manager, called us the Friday before and explained how the Beckhoff product line might be able to help us.
We learned about Beckhoff’s DIN-rail-mounted embedded PC and IEC 61131-3-compliant automation and motion control software. “The solution turned out to be exactly what we were looking for and allowed us to create our ideal electrical controls system,” says Lorenz. “We were impressed enough that we decided to make a major course change at the last possible minute. With the perfect technological match with the openness and flexibility we wanted, the Beckhoff system costs much less than the other vendor’s system.”
We considered using standard PC components, but we didn’t consider them industrial enough, and we would have had to use several suppliers to get all the needed components.
From January 2006 onward, Conflex designed and built the revamped ServoFlex machines using the CX1020 embedded PC with 1 GHz Celeron M ULV processor and TwinCat motion control software as the main control platform (Figure 2).
“With this hardware/software combination, we handle all PLC functions and motion control on a single device,” says Lorenz. “The new ServoFlex horizontal form, fill and seal wrapper is a four-axis system—one master axis with three slave axes. It delivers continuous motion at up to 100 ft of film per minute with an advanced, reciprocating, hot-knife seal system.”
We found several of the programming libraries in TwinCat particularly helpful. “The Flying Saw code library saved us time and effort by providing pre-written software functions to achieve a great deal of our motion programming,” says Lorenz. “On the ServoFlex, a vacuum conveyor holds the wrapper film and leads it to the sealing area that features a reciprocating motion. We have to hit a very specific mark on the film, so the Flying Saw program handles the sealing motion of the knife moving back and forth on the machine. A pneumatic cylinder closes a sealing jaw while the cut is made. Built-in libraries for PID temperature control for the machine’s film heaters and superimposed move for print registration functions are huge time savers in our area of packaging.”
Simpler Means Sophisticated
Figure 2: Conflex uses embedded PCs with TwinCat handling all PLC functions and motion control on a single device.
Photo by Conflex
Any controller we use must provide very fast control of the film-cutting knife to exactly match the speed of the incoming wrapper film. EtherCat helped ramp up our control speed on the ServoFlex machines. “In addition to performance, we had to choose a fieldbus that will be supported well into the future and won’t go obsolete in a few years,” adds Lorenz. “Conflex customers also enjoy remote diagnostic capabilities for troubleshooting via standard Ethernet connectivity with the EtherCat-equipped machines.”
The ServoFlex uses some EtherCat I/O terminals to develop built-in special latching functions for hardware interrupt. The latch input is significant since it synchronizes the machine cutting and sealing operations to the printed film. This allows for a very professional-looking finished product for the end user. “The EL5101 EtherCat Terminal is an interface for the direct connection of incremental encoders with differential/RS485 inputs,” says Seicther. “A 16-bit counter with a quadrature decoder and a 16-bit latch for the zero pulse can be read, set or enabled. Incremental encoders with alarm outputs can be connected at the interface’s status input.” Interval measurement with a resolution of 500 ns is possible, he says:
“We have the best solution available compared with our previous I/O board challenge,” says Lorenz. “We only buy the points we need and can replace as needed, one I/O card at a time. The simple, direct I/O connection to the embedded PC made this decision that much easier.”
The main objectives of the Conflex machinery renaissance were to build a better performing machine and to make it more flexible and easier for manufacturers to operate.
Watch and Learn
Figure 3: The HMI software is unlike virtually any other in the industry with onboard instructional videos to train machine operators.
Photo by Conflex
To emphasize the learning aspect of a renaissance, the ServoFlex HMI includes detailed instructional programs that literally can teach users how to operate them (Figure 3). Operators can view demonstration videos detailing machine setup, film threading, troubleshooting and other how-to videos. These videos are very helpful when companies have to deal with high operator turnover. Troubleshooting guides, electrical schematics and machine part drawings can be viewed, as well. “We run Windows CE on the embedded PCs, and we were able to create a human-machine interface (HMI) that is unlike any other in the industry,” claims Lorenz. “It’s something that couldn’t be done easily using conventional controls platforms.”
An added bonus of these embedded PCs is that all the software resides on a CompactFlash (CF) card, so changes can be made very easily in the field if needed. “Since the HMI software is also running on the CF card, customers can find a replacement display very easily without reloading any software if a backlight fails on our integrated monitors,” says Lorenz.
The Microsoft Dilemma?
Some machine builders are concerned about whether using PC-based controls ties you to companies such as Microsoft, and whether additional overheads in new operating systems could even overwhelm the processors. They wonder if a migration could be forced when the OS no longer is supported, and that could happen much earlier than they want.
With this Beckhoff system, we might be tied to a Microsoft OS, but the OS provides the advantage of direct access to databases, raw TCP/IP functionality and direct access to PLCs from HMI implementations, to name a few elements. A traditional rack-mount PLC would require an expensive add-on card or an additional PC to run software to support these elements. When adding these other pieces to a rack- mount PLC you are, in our judgment, not only adding more points of failure to the system, but adding unnecessary cost.
We’ve heard that operating-system overhead is a valid concern when running a “user level” application on top of any OS. On Windows XP Pro and XP Embedded based systems TwinCat doesn’t modify the OS—it provides a kernel-level, real-time package that can run I/O and PLC functions deterministically to 50 µs. With WinCE-based systems, Beckhoff tells us that TwinCat takes advantage of the inherent real-time nature of that OS and can run I/O and PLC tasks down to 100 µs. This means you can run everything from high-speed I/O tasks to standard PLC logic to complicated motion control.
Renaissance on Repeat
With the majority of the Conflex redesigns complete, we now offer smaller machine footprints, more competitive system costs, greater flexibility and faster machine delivery. “Before 2006, Conflex machines had four separate control devices, each with bits and pieces of code for the machine spread throughout,” reminds Lorenz. “Now we have one device on our machines that contains all of our programming. This is a much more streamlined approach.”
TwinCat proved to be a highly flexible environment for Conflex machine programming. “We can use a standard set of programs for three different models of machines that vary depending on the application,” says Lorenz. “We choose the appropriate program to match our customer’s application when the system boots up. In a few hours we can make immediate modular design changes that previously would take up to several weeks of cumbersome work.”
To make sure that changes took a minimal amount of time while learning a new system, Conflex took full advantage of the engineering support available to them. “Beckhoff support always is available to assist with our questions and we all learned quite a bit together as engineers in our technical discussions,” says Lorenz. “Our machines now are better suited to integrate more seamlessly into lines with machines from a variety of manufacturers and extract data from the entire line. The Ethernet capability is a huge benefit for our customers and helps us deliver the most flexible machines possible.”
The controls replacement cost on Conflex machines has been highly optimized. “The old drive system with integrated intelligence cost about triple what we’re paying for a Beckhoff system that does more work.
With the kind of success we experienced on the ServoFlex line, we’ve incorporated this approach into our AdvantEdge series of servo-driven, side-seal wrappers, and will be expanding the solution into other machine lines to fully apply our enhanced PC-based control expertise.
Down the road we expect this HMI and connectivity approach to lead us into providing value-adds such as machines that would monitor parts due for replacement and send an order back to us when it’s time. The replacement part could be sent to the customer for a just-in-time delivery. In our judgment, the sky’s the limit when it comes to what a Windows-based system can provide.
Joe Morrissey is product manager for Germantown, Wis.-based Conflex. Learn more about Conflex at conflex.com.
Conflex had confidence in its migration to a PC-based control scheme. What would your strategy be if some of your customers were uneasy about leaving well-understood legacy controls behind? Look for comments—add your own—on this issue at ControlDesign.com/renaissance.
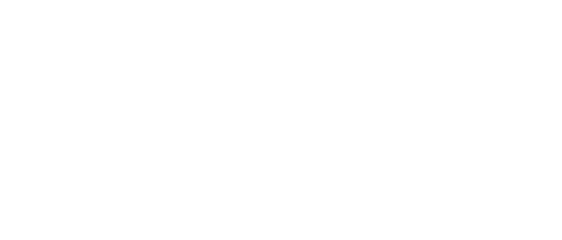
Leaders relevant to this article: